Waterproof Adhesive Glue
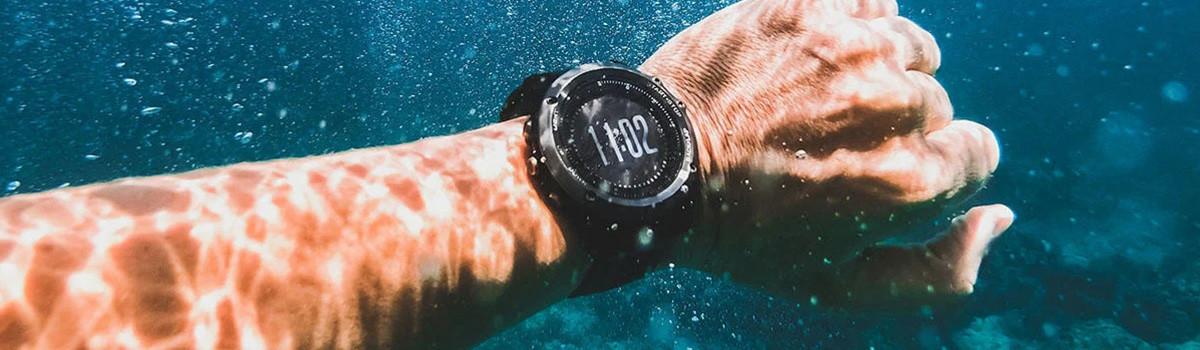
In a world where exposure to moisture can compromise the integrity of materials and structures, waterproof adhesive glue has emerged as a transformative solution. This remarkable innovation goes beyond conventional bonding, offering a versatile and reliable way to create resilient connections that withstand water, humidity, and other environmental challenges. Whether in construction, marine applications, outdoor equipment, or even everyday objects, waterproof adhesive glue provides an effective shield against the corrosive effects of moisture. This comprehensive exploration delves into the realm of waterproof adhesive glue, uncovering its formulations, applications, benefits, and its pivotal role in enhancing the durability and longevity of diverse materials.
Unveiling Waterproof Adhesive Glue
In a world where innovation constantly pushes the boundaries of what is possible, a remarkable breakthrough has emerged in adhesives: Waterproof Adhesive Glue. This revolutionary adhesive promises to redefine how we think about bonding materials together, offering a solution that is strong and impervious to water. This game-changing adhesive opens many possibilities, from construction projects to DIY home repairs.
The Challenge of Traditional Adhesives
Traditional adhesives, while effective in many applications, have their limitations. One of the primary challenges is their susceptibility to water damage. In wet environments or during exposure to rain, ordinary adhesives can weaken, leading to structural failures or material separations. This limitation has hindered the use of adhesives in various industries, including marine, automotive, and construction.
The Science Behind Waterproof Adhesive Glue
What sets Waterproof Adhesive Glue apart is its unique formulation. At its core, the manufacturers designed this adhesive to repel water and maintain its adhesive properties even in the most demanding conditions. It achieves this through a combination of hydrophobic compounds that create a protective barrier around the bonded materials. This innovation ensures that the adhesive remains intact and robust, regardless of exposure to moisture.
Applications in Construction
The construction industry stands to benefit significantly from Waterproof Adhesive Glue. You can use it in various applications, from sealing joints in building envelopes to bonding materials in underwater construction projects. Its ability to maintain its strength in wet conditions reduces the need for costly and time-consuming repairs, making it a game-changer in the construction sector.
DIY Enthusiasts Rejoice
For the avid DIY enthusiast, Waterproof Adhesive Glue is a dream come true. They no longer have to worry about rain causing their outdoor furniture to fall apart or unexpected leaks compromising their home repair projects. This adhesive provides peace of mind, knowing their creations will withstand the test of time and weather.
Challenges of Moisture in Bonding
Moisture, whether in the form of humidity, rain, or water exposure, poses significant challenges to various industry bonding processes. From construction to manufacturing and even everyday DIY projects, people must appreciate the impact of moisture on adhesives. Understanding these challenges is crucial for finding practical solutions and achieving durable, moisture-resistant bonds.
The Impact of Moisture
Moisture can compromise the integrity of adhesive bonds in several ways, making it a formidable adversary for bonding processes:
- Weakening Bond Strength:Moisture can drain the adhesive’s grip on surfaces, causing premature failures and structural instability. This concern is particularly significant in load-bearing applications where strong bonds are essential.
- Reduced Adhesive Effectiveness:Some adhesives use chemical reactions to cure and achieve optimal strength. Moisture can interfere with these reactions, leading to incomplete curing and adhesive failure.
- Debonding and Delamination:Exposure to moisture over time can lead to debonding, where the adhesive separates from the substrate, and delamination, where layers of materials come apart. These issues are prevalent in laminates, composite materials, and coatings.
Moisture-Resistant Adhesives: A Solution
Developments in adhesive technology have yielded moisture-resistant adhesives specially formulated to tackle these challenges. These adhesives offer several advantages:
- Hydrophobic Formulations:Moisture-resistant adhesives often contain hydrophobic compounds that repel water, preventing it from compromising the bond. This property ensures that the adhesive maintains strength, even in wet conditions.
- Long-Term Durability:Designers have created these adhesives to withstand prolonged exposure to moisture, making them suitable for outdoor applications, marine environments, and even underwater bonding.
- Versatility:Various industries can use moisture-resistant adhesives, including aerospace, automotive, construction, and electronics. Their versatility makes them a valuable asset in moisture-prone environments.
- Cost Savings:By reducing the need for frequent repairs and replacements due to moisture-related failures, these adhesives can lead to substantial cost savings in the long run.
Mechanisms of Waterproof Adhesion
Understanding the intricate mechanisms behind waterproof adhesion is essential for appreciating its effectiveness in challenging environments. This advanced adhesive technology employs several active tools to create solid and water-resistant bonds while minimizing passive elements that could compromise performance.
Active Mechanisms
- Hydrophobic Barrier Formation: At the heart of waterproof adhesion lies the creation of a hydrophobic barrier. This active mechanism involves the adhesive’s ability to repel water molecules, preventing them from infiltrating the bond.
- Chemical Crosslinking: Waterproof adhesives often employ chemical reactions as an active mechanism. These reactions form strong covalent bonds between the adhesive and the substrate, enhancing overall adhesion strength.
- Flexible Polymer Matrix: Many waterproof adhesives incorporate a springy polymer matrix. This matrix actively adapts to environmental changes, expanding and contracting with temperature and humidity variations while maintaining a secure bond.
- Surface Tension Reduction: Active surface tension reduction is a crucial mechanism. It ensures the adhesive can spread evenly across the substrate’s surface, enhancing contact and adhesion.
Minimizing Passive Elements
- Water Absorption Resistance: Waterproof adhesives actively minimize water absorption, which can weaken bonds over time. By reducing passive water ingress, they maintain adhesive strength and durability.
- Environmental Sensing and Adaptation: Some advanced waterproof adhesives incorporate active sensors that respond to changes in environmental conditions. The bond can adjust itself to different moisture and temperature levels in a functional manner.
- Continuous Bond Monitoring: Active mechanisms also include continuous bond monitoring. By actively assessing the integrity of the bond, these adhesives can detect any potential weaknesses and take corrective actions.
- Enhanced Surface Wetting: Waterproof adhesives improve surface wetting, ensuring that the adhesive effectively wets the substrate for a more substantial initial bond. This active element is crucial in preventing bond failures.
Types of Waterproof Adhesive Formulations
Waterproof adhesive formulations are as diverse as the applications they serve. Engineers have designed these specialized adhesives to withstand exposure to moisture, offering reliable bonding solutions in a wide range of scenarios. Here, we explore various waterproof adhesive formulations tailored to meet specific needs and challenges.
Silicone-Based Formulations
- Active Resistance to Moisture:Silicone-based waterproof adhesives offer exceptional resistance to moisture, making them ideal for applications exposed to rain, humidity, or immersion.
- Versatile:They bond well to various substrates, including glass, metals, plastics, and ceramics, making them versatile for construction and electronics.
Polyurethane-Based Formulations
- Active Flexibility:Polyurethane adhesives exhibit flexibility even in wet conditions, allowing for expansion and contraction without compromising bond strength.
- Excellent Adhesion:They adhere well to wood, concrete, and various plastics, making them suitable for construction, marine, and automotive applications.
Epoxy-Based Formulations
- High Bond Strength:Epoxy adhesives are renowned for their exceptional bond strength, and waterproof epoxy formulations retain this strength even in the presence of moisture.
- Chemical Resistance:They are resistant to chemicals, which makes them suitable for bonding applications in corrosive environments.
Cyanoacrylate (CA) Formulations
- Fast Curing:CA adhesives cure rapidly, forming solid bonds even in moisture. This property is advantageous for quick repairs and assembly processes.
- Limited Flexibility:While they excel in fast bonding, CA adhesives may need more flexibility than other formulations.
Hybrid Formulations
- Active Adaptability:Hybrid waterproof adhesives combine the strengths of multiple formulations, offering enhanced performance in challenging conditions.
- Versatile Applications:They find use in diverse industries, from aerospace to marine, thanks to their ability to adapt to various substrates and environments.
UV-Cured Formulations
- Active Rapid Curing:UV-cured adhesives quickly harden when exposed to ultraviolet light, forming solid bonds resistant to moisture.
- Electronics and Optical Applications:The electronics and optical industries commonly use them for their precision and moisture-resistant properties.
Marine Grade Waterproof Adhesives
Marine-grade waterproof adhesives are indispensable in the world of maritime and underwater engineering. These robust adhesives play a pivotal role in ensuring the structural integrity of vessels and offshore structures, where exposure to harsh aquatic environments is a constant challenge. Designers have created them to withstand the relentless assault of saltwater, extreme temperatures, and dynamic forces, making them a cornerstone of safety and reliability in marine applications. These adhesives are predominantly epoxy-based, combining exceptional bonding strength with unmatched waterproofing properties. Engineers and naval architects rely on them to bond various materials, from metals and composites to plastics and glass, creating watertight seals that endure for years.
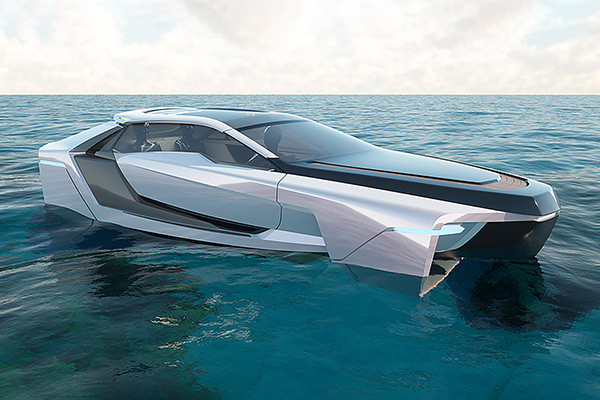
One of the critical advantages of marine-grade waterproof adhesives lies in their versatility and adaptability. Various maritime applications can use them, including repairing cracks in ship hulls, securing critical components on oil rigs, or even assembling marine recreational equipment like kayaks and sailboats. Their robustness extends beyond simple adhesion; they are also resistant to the corrosive effects of saltwater, ensuring that bonded materials remain firmly in place even in the harshest marine conditions. This reliability translates into enhanced safety and cost-efficiency for maritime industries.
In the realm of boat building, these adhesives are a game-changer. Traditional methods involving rivets and welding are prone to corrosion over time, weakening the vessel’s structural integrity. Marine-grade adhesives eliminate this vulnerability by forming a seamless bond impervious to water intrusion. These enhancements improve the boat’s durability and overall performance by reducing weight and eliminating potential leak points. Furthermore, these adhesives are compatible with fiberglass and composite materials commonly used in modern boat construction, ensuring that vessels are strong but also lightweight and fuel-efficient.
Outdoor and Weatherproof Applications
Today’s world places increasing demands on outdoor and weatherproof applications, with these solutions finding widespread use across diverse industries. They are pivotal in meeting the growing need for materials and products capable of withstanding the harshest environmental challenges.
Construction: Building Resilient Structures
The construction industry relies heavily on outdoor and weatherproof applications to fortify structures against the elements. Waterproof membranes, sealants, and coatings reinforce roofs, walls, and foundations, shielding them from water infiltration and related damage. These applications extend buildings’ lifespans and improve energy efficiency by eliminating leaks that can lead to heat loss or gain.
Transportation: Ensuring Smooth Mobility
Outdoor and weatherproof solutions are indispensable in the transportation sector, ensuring the safety and functionality of vehicles and infrastructure. Automotive manufacturers employ weather-resistant coatings to protect crucial components from corrosion, while the aviation industry depends on such materials to safeguard aircraft during prolonged outdoor storage.
Telecommunications: Reliable Connectivity
Outdoor and weatherproof applications are vital in telecommunications, where enclosures, cable connectors, and junction boxes must endure rain, heat, and cold to maintain uninterrupted network connections. Weather-resistant coatings and materials ensure consistent data transmission, even in challenging outdoor environments.
Outdoor Leisure: Enjoying the Great Outdoors
Outdoor and weatherproof applications are essential in outdoor leisure, contributing to the longevity and performance of various products. Weather-resistant paints and coatings safeguard outdoor furniture from corrosion and fading, while specialized fabrics and materials ensure that outdoor gear keeps users dry and comfortable during adverse conditions.
Bonding in High-Humidity Environments
Bonding materials in high-humidity environments can be a challenging endeavor due to the adverse effects of moisture on adhesion. However, with advancements in adhesive technology and meticulous application, it’s possible to achieve robust and reliable bonds even in such conditions.
Challenges of High-Humidity Bonding
- Reduced Bond Strength:High humidity can weaken adhesive bonds, compromising strength and durability.
- Adhesion Failure:Excessive moisture can cause adhesives to fail prematurely, leading to costly repairs and downtime.
- Surface Contamination:Moisture can contaminate surfaces, hindering proper adhesion and substrate preparation.
Strategies for Successful Bonding
- Choose the Right Adhesive:Opt for adhesives specifically designed for high-humidity environments, such as moisture-cured urethanes or epoxy formulations.
- Surface Preparation: Thoroughly clean and dry surfaces before applying adhesive to eliminate contaminants and ensure a strong bond.
- Humidity Control:Consider dehumidification or temperature control in controlled settings to reduce ambient moisture.
- Optimal Application Conditions:Apply adhesives within recommended temperature and humidity ranges for optimal bonding results.
- Proper Curing Time:Allow sufficient time for adhesives to cure, ensuring they achieve their full strength before subjecting them to high-humidity conditions.
Benefits of High-Humidity Bonding
- Versatility:Mastering high-humidity bonding expands the range of applications for adhesive technology, allowing for bonding in previously challenging environments.
- Corrosion Resistance:Some adhesives formulated for high humidity also offer excellent resistance to corrosion, enhancing the durability of bonded materials.
- Cost Savings:By enabling reliable bonding in high-humidity conditions, industries like marine and construction can reduce maintenance costs and extend the lifespan of their structures.
Corrosion Resistance Through Waterproof Glue
Waterproof glue is pivotal in enhancing corrosion resistance, a crucial factor in the durability and longevity of various materials and structures. This type of glue, when applied effectively, creates a robust barrier against moisture, preventing it from infiltrating surfaces and causing corrosion. The active role of waterproof glue in this process lies in its ability to bond materials securely, thus sealing potential entry points for water and corrosive agents. For instance, waterproof glue forms an impenetrable shield when applied to metals, safeguarding them from rust and deterioration even in the harshest environments.
One of the primary advantages of waterproof glue is its versatility in applications. This adhesive contributes significantly to corrosion prevention, whether used in construction, automotive, marine, or even household settings. By using waterproof glue, manufacturers can assemble products with increased resistance to environmental factors, reducing maintenance costs and prolonging the lifespan of the finished goods. The adhesive’s active function is to unite components tightly, eliminating gaps and crevices where moisture can accumulate and start corrosion. This proactive approach to corrosion resistance ensures that structures and products remain reliable and functional for years.
In addition to its preventative capabilities, waterproof glue offers ease of application and compatibility with various materials. This adhesive actively facilitates the bonding process by creating a robust and long-lasting connection between surfaces, making it a valuable tool in industries that require corrosion-resistant solutions. From bonding wooden joints in boat construction to sealing seams in metal roofing, the active role of waterproof glue extends its influence across a broad spectrum of sectors.
Construction and Infrastructure Use
In construction and infrastructure, waterproof glue is a fundamental component for reinforcing structural integrity, ensuring longevity, and mitigating the impact of moisture-related damage. Its active role in fortifying various elements of construction and infrastructure projects is indispensable.
Foundation and Concrete Sealing:
Preventing Water Infiltration
Builders actively employ waterproof glue to seal the foundations of buildings and concrete structures. It forms a waterproof barrier, preventing water infiltration, which can lead to erosion and weakening of the foundation. By actively blocking moisture, waterproof glue prolongs the life of foundations, ensuring their stability over time.
Roofing Systems:
Sealing Vulnerable Joints
Roofing systems are vulnerable to water damage due to their exposed position. Waterproof glue plays an active role in sealing joints, seams, and gaps in roofing materials, effectively preventing leaks and extending the roof’s life. This proactive approach to waterproofing contributes significantly to maintaining the integrity of the entire building.
Exterior Cladding:
Protecting Against the Elements
Exterior cladding materials, such as siding and panels, are susceptible to moisture-related degradation. Waterproof glue actively secures these materials, creating a seamless, weather-resistant surface that shields the structure from rain, snow, and humidity. This proactive protection enhances the building’s aesthetics and durability.
Wooden Structures and Decks:
Preserving Natural Beauty
Wooden structures and decks in construction and infrastructure require special attention to combat moisture-induced rot and decay. Waterproof glue actively bonds wooden components, creating a robust shield against water ingress. This proactive measure ensures that wooden elements maintain natural beauty and structural integrity.
Tunnel Construction:
Resisting Underground Pressure
In tunnel construction, waterproof glue actively reinforces the lining materials. It prevents water from infiltrating through the tunnel walls, reducing the risk of erosion and damage caused by groundwater pressure. This proactive use of waterproof glue ensures the safety and longevity of tunnels.
Electronics and Water-Resistant Bonding
The seamless integration of electronics and water-resistant bonding has ushered in a new era of technological innovation, where our gadgets are no longer confined to dry environments but can thrive in wet, humid, and even underwater conditions. The relentless pursuit of durability and functionality in electronic devices drives this transformative shift. Manufacturers have honed their skills in crafting circuitry that can withstand the harshest of aquatic challenges. One of the fundamental techniques employed in this endeavor is using specialized materials and adhesives designed to create waterproof seals. These seals, known as gaskets, coatings, or encapsulants, protect against water intrusion, safeguarding the delicate components within.
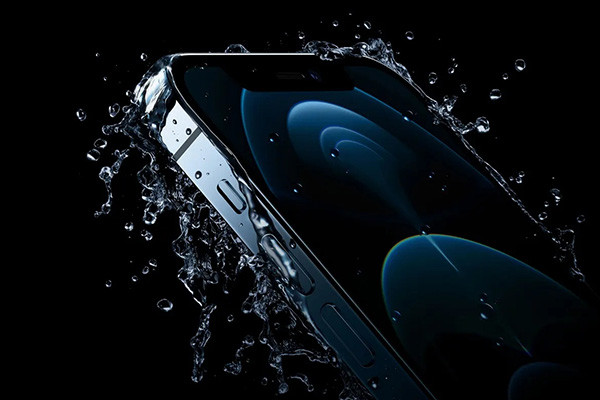
One of the most notable developments in this domain is the advent of nanotechnology. Nanoscale materials and coatings, with their exceptional water-repelling properties, have revolutionized how electronics interact with moisture. Nano-engineered surfaces effectively repel water droplets, akin to the behavior of lotus leaves, rendering them highly hydrophobic. This technology is widely employed in smartphones, smartwatches, and fitness trackers, where users demand functionality and water resistance. These devices now routinely feature an invisible shield of nanocoatings, allowing them to remain operational while submerged in water.
Beyond consumer electronics, water-resistant bonding plays a critical role in various industrial applications. Industries such as marine exploration, oil and gas, and underwater robotics rely on advanced bonding techniques to ensure their equipment can endure the extreme conditions of the deep sea. Specialized adhesives, sealants, and potting compounds enable these machines to function reliably in corrosive saltwater, high pressure, and frigid temperatures.
Moreover, this technology has expanded into medical devices, where waterproofing is essential to protect sensitive electronic components, such as pacemakers and hearing aids, from bodily fluids and environmental factors. It’s not just about making gadgets more robust; it’s about saving lives and enhancing the quality of life for millions.
Automotive Water-Proofing Solutions
In automotive engineering, the demand for robust waterproofing solutions has intensified as vehicles become more technologically advanced. These solutions ensure modern automobiles’ reliability, safety, and longevity as electronic components proliferate throughout vehicle systems.
Advanced Sealing Technologies
- Effective Gaskets:High-performance gaskets made from rubber, silicone, or neoprene create watertight seals around doors, windows, and engine compartments, preventing water intrusion even during heavy rain or car washes.
- Liquid Sealants:Liquid-applied sealants, often used in conjunction with gaskets, provide additional protection against water infiltration. They are beneficial for sealing complex shapes and joints.
Electrical Component Encapsulation
- Potting Compounds:These compounds are applied to encapsulate sensitive electronic components within the vehicle. They form a protective, waterproof barrier, guarding against moisture, dust, and vibration.
- Conformal Coatings:Conformal coatings, when applied as thin layers over printed circuit boards (PCBs), protect against water, chemicals, and temperature extremes while preserving electrical functionality.
Water-Resistant Wiring and Connectors
- Waterproof Connectors:Specially designed connectors with sealed housings and gaskets ensure electrical connections remain intact and functional even when submerged or exposed to water.
- Sealed Wiring Harnesses:Automotive wiring harnesses are increasingly equipped with water-resistant features, such as waterproof connectors and protective sleeves, to prevent electrical issues due to water exposure.
Corrosion-Resistant Materials
- Rust-Proofing:Automotive manufacturers employ various rust-proofing techniques, including galvanization and undercoating, to protect metal components from corrosion caused by exposure to water, salt, and road debris.
- Stainless Steel Components:Using stainless steel in critical components like exhaust systems and fasteners enhances corrosion resistance, ensuring longevity even in wet conditions.
Advanced Sensor Protection
Sensor Sealing: Sensors, critical for modern driver-assistance systems, are often sealed to shield them from moisture and environmental contaminants. These sealed sensors ensure accurate readings for features like adaptive cruise control and lane-keeping assistance.
Testing and Quality Assurance
- Water Ingress Testing:Rigorous testing procedures, including water ingress tests, are conducted during vehicle development to identify and rectify vulnerabilities to water intrusion. These tests simulate real-world conditions to ensure robust protection.
- Quality Control:Stringent quality control measures are implemented throughout manufacturing to detect and rectify any defects or weaknesses in waterproofing solutions.
Medical Devices in Wet Environments
In healthcare, medical devices often encounter wet environments during surgeries, wound care, or underwater procedures. Ensuring the safety and functionality of these devices in such conditions is paramount. One critical component in this endeavor is waterproof adhesive glue, pivotal in maintaining device integrity.
Waterproof Adhesive Glue: A Lifesaver in Wet Environments
The Role of Waterproof Adhesive Glue
Waterproof adhesive glue is a specialized adhesive designed to bond medical devices and materials in wet environments. It is essential for several reasons:
Sealing and Durability
- In wet environments, maintaining a solid seal between device components is vital. Waterproof adhesive glue provides a robust bond, preventing potential leaks or failures.
- Its durability ensures that devices continue functioning as intended, even when exposed to moisture, saline solutions, or bodily fluids.
Infection Control
- Effective infection control is crucial in healthcare settings. Waterproof adhesive glue creates a barrier that prevents pathogens from infiltrating medical devices, reducing the risk of infections.
- It also aids in securing wound dressings or catheters, preventing microbial entry points.
Applications in Healthcare
Wound Closure
Waterproof adhesive glue is commonly used for wound closure, replacing traditional sutures or staples. It provides a watertight seal, reducing the risk of infection and improving patient comfort.
Dental Procedures
Dentists rely on waterproof adhesive glue for dental prosthetics, like crowns and bridges. Its resistance to saliva ensures these prosthetics remain securely in place.
Surgical Instruments
Surgical instruments, such as endoscopes and laparoscopic tools, often require waterproof adhesives to maintain integrity during bodily fluids procedures.
Challenges and Innovations
Challenges
- Ensuring the biocompatibility of adhesive materials is a challenge, as they must not trigger adverse reactions in the body.
- Achieving a balance between solid adhesion and ease of removal is essential, particularly for wound dressings.
Innovations
- Researchers are exploring bio-inspired adhesives, mimicking the properties of natural adhesives like mussel glue, to enhance performance.
- Researchers are harnessing nanotechnology to create adhesives with superior strength and biocompatibility.
DIY and Home Improvement Applications
Having the right tools and materials can make all the difference in DIY and home improvement. Waterproof adhesive glue is a game-changing material that finds many applications, offering exceptional versatility and reliability for various projects around the house.
Versatile and Reliable: The Role of Waterproof Adhesive Glue
An Essential in the DIY Toolkit
Waterproof adhesive glue is an indispensable tool for DIY enthusiasts and home improvement projects because of its versatility and reliability. Here’s why:
Strong Bonds and Durability
- Waterproof adhesive glue forms robust bonds, ensuring that DIY projects remain intact over time.
- It’s precious for outdoor projects, as it can withstand exposure to rain, humidity, and temperature fluctuations.
Waterproofing and Leak Prevention
- When used to seal gaps or joints, this adhesive serves as an effective barrier against water infiltration, preventing leaks in bathrooms, kitchens, and even outdoor structures.
- It’s an excellent choice for fixing leaking pipes or sealing the edges of a bathtub.
Mending and Repair
- Thanks to the adhesive’s strong bonding capabilities, DIYers can repair a wide range of items, from shoes to outdoor furniture.
- It’s ideal for reattaching loose soles or fixing broken garden tools.
Applications in DIY and Home Improvement
Tiling and Flooring
- Waterproof adhesive glue is invaluable in tiling projects, ensuring tiles stay firmly in place, even in damp environments like bathrooms or kitchens.
- It provides a secure bond for flooring installations, reducing the risk of loosening or warping.
Plumbing Repairs
- You can simplify DIY plumbing repairs with waterproof adhesive glue. It effectively seals joints and connections, preventing water leaks.
- You can also use it to repair tiny cracks or holes in pipes.
Outdoor Projects
- They are building or repairing outdoor structures, such as fences, decks, or garden boxes, that benefit from the adhesive’s ability to withstand outdoor conditions.
- It’s ideal for securing wooden boards or sealing gaps in outdoor furniture.
Submersible and Underwater Bonding
One cannot overstate the significance of robust and reliable bonding solutions in underwater applications. Whether it’s for marine construction, repairing submerged structures, or crafting intricate underwater equipment, the choice of adhesive glue plays a pivotal role in ensuring the longevity and efficiency of these projects. Submersible and underwater bonding techniques have evolved significantly, owing much of their success to the innovative strides made in developing waterproof adhesive glues. This paragraph delves into the active voice narrative, exploring how these adhesive wonders transform underwater industries.
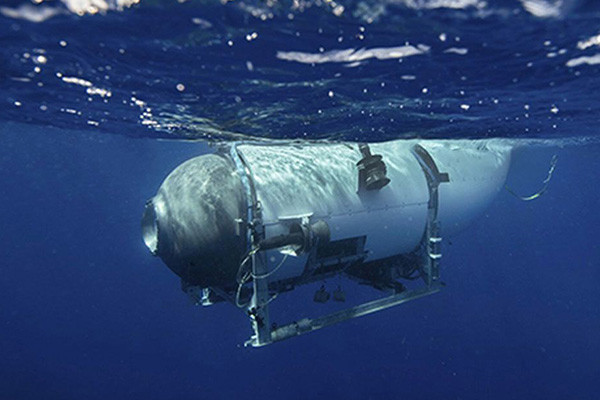
Unparalleled Adhesion in Unforgiving Environments: Engineers have engineered waterproof adhesive glues to thrive in the most hostile underwater environments. They exhibit extraordinary bonding capabilities, adhering to various substrates with tenacity, whether metals, plastics, ceramics, or composites. This adhesive prowess empowers engineers and underwater construction specialists to work confidently, knowing their underwater structures will withstand the harshest conditions.
The Chemistry Behind Success: The science behind these waterproof adhesives is fascinating. Advanced polymer chemistry is the foundation for most of them, ensuring exceptional adhesion and water, salt, and corrosion resistance. When applied, these glues undergo a curing process that solidifies their bond, creating a barrier impervious to the challenges posed by submersion. Such adhesive technologies often incorporate unique formulations, including epoxy, polyurethane, and acrylic-based compositions, each tailored to specific underwater applications.
Versatility Across Industries: The applications of waterproof adhesive glues extend beyond underwater construction. They are indispensable in marine vessel maintenance, where they securely attach hull components, ensuring a watertight seal. In marine biology, scientists employ these adhesives to affix tracking devices to marine animals, collecting valuable data without harming the creatures. The offshore energy sector also relies heavily on these glues to maintain and repair underwater pipelines and infrastructure.
Environmental Friendliness: Many manufacturers formulate waterproof adhesive glues with environmental consciousness. They are free from harmful solvents and emit minimal volatile organic compounds (VOCs). This eco-friendly attribute is essential for underwater projects in sensitive ecosystems, as it helps minimize the impact on aquatic life.
Surface Preparation for Waterproof Bonding
In waterproof bonding, meticulous surface preparation stands as the bedrock upon which the success of adhesive applications hinges. Whether in construction, manufacturing, or marine industries, achieving a robust and lasting bond in wet or submerged environments necessitates a comprehensive approach to surface preparation. Surface preparation for waterproof bonding encompasses a series of essential steps and techniques that clean and prime surfaces and promote the adhesion of waterproof adhesives, ensuring their optimal performance.
Cleaning and Degreasing: The initial step in surface preparation involves thorough cleaning and degreasing. Surfaces must be entirely free of dirt, dust, grease, oils, and other contaminants that could compromise adhesive performance. This cleaning process enhances adhesion and prevents the development of weak points in the bond.
Abrasion and Profiling: To create a microscopically rough surface, abrasion techniques like sanding, blasting, or etching are often employed. This substrate profiling enhances mechanical adhesion by providing more surface area for the adhesive to grip onto. It’s a crucial step, especially for non-porous materials like metals and plastics.
Priming: In many cases, applying a primer after cleaning and profiling is essential. Primers serve as a bridge between the substrate and the adhesive, improving compatibility and promoting chemical adhesion. Formulators design these priming agents to work with specific adhesives and substrates, enhancing bond strength and durability.
Moisture Management: Managing moisture is paramount in waterproof bonding applications. Water can degrade adhesive performance or lead to premature failure. Depending on the conditions, moisture control barriers or moisture-tolerant adhesives may be necessary to ensure a long-lasting bond in wet environments.
Surface Energy and Wetting: Understanding the surface energy of both the substrate and the adhesive is critical. A surface with higher surface energy promotes better wetting and adhesion. Techniques like plasma or corona can modify surface energy to enhance adhesive wetting.
Quality Control: Throughout the surface preparation process, quality control measures, such as adhesion testing and surface cleanliness checks, must be implemented. We perform these checks to ensure we adequately prepare the surface for waterproof bonding and address any issues before applying the adhesive.
Quality Control and Testing Standards
In adhesive technology, the pursuit of excellence is epitomized by stringent Quality Control and Testing Standards, especially in the case of Waterproof Adhesive Glue. The demand for waterproof adhesives has surged across industries, from construction to automotive, as they play a pivotal role in ensuring structural integrity and durability. Consequently, ensuring the reliability of these adhesives is paramount, and this is where Quality Control and Testing Standards come into play.
Quality Control is the cornerstone of any adhesive manufacturing process. It starts by meticulously examining the quality of resins, curing agents, and additives when selecting raw materials. These materials must meet predefined specifications to guarantee the adhesive’s performance. Stringent quality checks continue throughout the production process, including the mixing, coating, and curing stages. State-of-the-art equipment and monitoring systems ensure consistency in adhesive composition, thickness, and healing time.
Testing Standards for Waterproof Adhesive Glue encompass various assessments designed to evaluate the product’s performance. Adhesive bond strength tests determine the adhesive’s ability to withstand multiple stressors, such as tension, compression, or shear forces. Peel tests assess the adhesive’s resistance to delamination, simulating real-world scenarios where bonded surfaces may experience separation forces. Additionally, environmental tests gauge the adhesive’s response to extreme conditions like temperature fluctuations, humidity, and exposure to UV radiation. These tests ensure the bond remains resilient in harsh environments, a vital trait for marine or outdoor construction applications.
Waterproofness is the hallmark of specialized adhesive glue, and testing for this property is meticulous. Submersion tests involve immersing bonded specimens in water for extended periods to determine whether the adhesive can maintain its integrity when exposed to moisture for a prolonged time. Dynamic tests simulate the flexing and movement that materials might undergo in real-world applications, ensuring that the adhesive can maintain its waterproofing capabilities even under stress.
Advancements in Waterproof Adhesive Technology
Waterproof adhesive technology has undergone remarkable advancements in recent years, revolutionizing industries ranging from construction to electronics and even healthcare. These breakthroughs have enabled the creation of products and structures that can withstand the harshest environmental conditions while maintaining their structural integrity. Here, we delve into the key innovations driving this transformation.
One of the most significant advancements in waterproof adhesive technology is the development of nanotechnology-infused adhesives. These adhesives contain nanoparticles that provide enhanced waterproofing properties. These nanoparticles form a tight barrier, preventing water molecules from infiltrating the adhesive bond. This innovation has found applications in everything from underwater construction to waterproof electronics. It ensures that products and structures remain intact, even when exposed to heavy rains, submersion in water, or high humidity.
Furthermore, researchers have made strides in creating adhesives that repel water and self-heal when damaged. Inspired by nature, these adhesives mimic the ability of certain organisms, like some plants and animals, to regenerate or repair themselves. When a crack or break occurs, the adhesive activates its self-healing mechanism, filling the gap with a waterproof sealant. This innovation holds promise for extending the lifespan of structures, reducing maintenance costs, and improving the durability of consumer products.
In medical technology, waterproof adhesives have opened new doors for wearable health devices and medical applications. These adhesives are skin-friendly, waterproof, and biocompatible. They allow for creation of waterproof bandages, sensors, and even implantable medical devices. Patients can now wear monitoring devices while swimming, showering, or even in extreme weather conditions, providing healthcare professionals with more comprehensive and accurate data.
Another breakthrough in waterproof adhesive technology is the development of adhesives that maintain strong adhesion even when submerged in water for extended periods. Traditional bonds tend to weaken and lose their grip when exposed to moisture, but these new formulations maintain their bonding strength in wet environments. These findings have immense implications for industries such as marine engineering, where adhesives are crucial in joining critical components underwater.
Sustainability and Environmental Considerations
In an era where environmental awareness is paramount, the adhesive industry has recognized the need for sustainable and eco-friendly solutions. This trend includes waterproof adhesives, where innovation increasingly focuses on minimizing environmental impact.
Biodegradable Formulations
Waterproof adhesive manufacturers invest heavily in research and development to create biodegradable formulations. These adhesives break down naturally over time, reducing the long-term environmental footprint. By transitioning from traditional, non-biodegradable glues to eco-friendly options, industries can significantly reduce plastic waste in landfills and oceans.
Water-Based Adhesives
Water-based waterproof adhesives have emerged as a sustainable alternative to solvent-based counterparts. These adhesives are composed primarily of water, with minimal volatile organic compounds (VOCs), which harm human health and the environment. Water-based adhesives release fewer emissions and have a lower environmental impact during production and use.
Recycled Materials
A key focus in the sustainability drive is incorporating recycled materials into adhesive formulations. Manufacturers are sourcing post-consumer or post-industrial waste to create adhesives with reduced reliance on virgin resources. This practice not only diverts waste from landfills but conserves valuable raw materials.
Reduced Carbon Footprint
Adhesive manufacturers are increasingly mindful of their production processes, seeking to reduce their carbon footprint. These efforts involve optimizing manufacturing techniques, improving energy efficiency, and utilizing renewable energy sources. These efforts contribute to a lower environmental impact throughout the adhesive product lifecycle.
Extended Product Lifespan
Waterproof adhesives play a pivotal role in enhancing the durability and longevity of various products, from construction materials to consumer electronics. By creating robust adhesive bonds, these products require fewer replacements or repairs over time, ultimately reducing resource consumption and waste generation.
Eco-Friendly Packaging
Sustainability extends beyond the adhesive formulation itself. Manufacturers are reevaluating packaging materials, opting for eco-friendly options such as recyclable or biodegradable packaging. This holistic approach to sustainability reduces the environmental impact of the entire product, from production to disposal.
Regulatory Compliance
Governments and regulatory bodies worldwide impose stricter environmental standards and regulations on adhesives and other chemical products. Adhesive manufacturers adapt to these changes by ensuring their products comply with these regulations, further emphasizing the industry’s commitment to sustainability.
Future Prospects of Waterproof Adhesive Development
The prospects of waterproof adhesive development hold tremendous promise in various industries, from construction to healthcare and consumer electronics. As technology continues to advance and environmental concerns grow, there is a pressing need for innovative adhesive solutions that can withstand water exposure while remaining eco-friendly. In this discussion, we will explore the key factors driving the evolution of waterproof adhesive technologies and their potential applications.
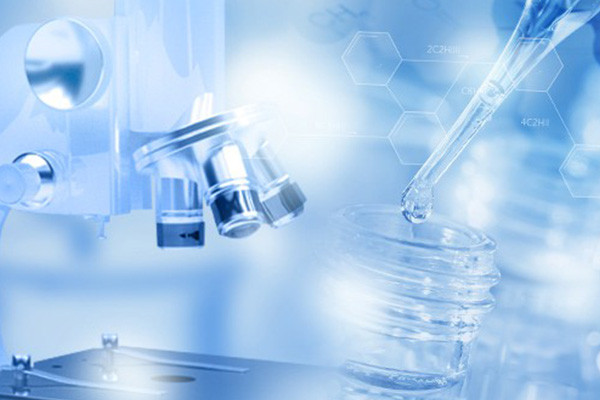
Advanced Materials and Formulations:
Formulating advanced materials is one of the most exciting prospects for waterproof adhesive development. Researchers are actively exploring new polymers and nanomaterials to enhance the adhesive’s water resistance and durability. Innovations in polymer chemistry are paving the way for bonds that can not only repel water but also resist extreme temperatures, chemicals, and UV radiation. These advancements are invaluable in applications such as underwater construction, aerospace, and automotive industries.
Environmental Sustainability:
With a growing focus on sustainability, the future of waterproof adhesives also includes a shift towards eco-friendly formulations. Biodegradable and bio-based adhesives are gaining traction, reducing the environmental impact of these products. Additionally, researchers are exploring the recycling and reusability of waterproof adhesives to minimize waste. This sustainability aspect aligns with global efforts to reduce plastic pollution and promote environmentally responsible practices.
Application in Healthcare:
Waterproof adhesives have significant potential in the healthcare sector. They can use these materials to develop advanced wound dressings and medical devices, which provide a secure and watertight seal while allowing for breathability. These adhesives can enhance patient comfort and reduce the risk of infections, making them invaluable tools in the medical field.
Consumer Electronics and Wearables:
The proliferation of consumer electronics and wearables also opens up exciting prospects for waterproof adhesives. These adhesives can seal the sensitive components of devices, protecting them from water damage. Additionally, in the rapidly growing field of wearable technology, waterproof adhesives are crucial in ensuring that these devices remain functional even in wet conditions, making them ideal for fitness trackers, smartwatches, and more.
Innovative Approaches to Water-Resistant Bonding
Water-resistant bonding is crucial in various industries, from construction to electronics. Innovations in waterproof adhesive technology have become increasingly important as they ensure the longevity and reliability of products and structures in wet or humid environments. This article explores some innovative approaches to water-resistant bonding using waterproof adhesive solutions.
Advancements in Adhesive Chemistry
- Nano-Structured Adhesives:Recent breakthroughs in nanotechnology have led to the development of nano-structured adhesives that exhibit remarkable water resistance. These adhesives contain nanoparticles that create a dense network within the bond, making it impervious to water infiltration.
- Hydrophobic Polymers:Engineers have also been experimenting with hydrophobic polymers, which naturally repel water. When integrated into adhesives, these polymers provide excellent water-resistant properties, making them ideal for outdoor applications.
Application-Specific Adhesives
- Marine Grade Adhesives:Specialized marine-grade adhesives have emerged for industries dealing with marine applications, such as boat building and offshore structures. Manufacturers formulate these adhesives to withstand constant exposure to saltwater and harsh marine conditions.
- Electronics Sealants:Water-resistant adhesives play a critical role in protecting delicate components from moisture damage in the electronics industry. Designers create innovative sealants to form an airtight seal, preventing water intrusion in electronic devices.
Hybrid Adhesive Technologies
- Silicone-Epoxy Hybrids:Hybrid adhesives that combine silicone’s flexibility with epoxy’s strength have gained popularity. These hybrids offer water resistance and robust bonding capabilities, making them versatile for various applications.
- Polyurethane-Acrylic Blends:Another innovative approach is the combination of polyurethane and acrylic adhesives. These blends balance adhesion strength and water resistance, making them suitable for diverse bonding needs.
Advanced Application Methods
- Vacuum Impregnation:Some industries use techniques to draw adhesives into porous materials. This method ensures complete coverage and exceptional water resistance in challenging environments.
- Plasma Activation:Plasma treatment of surfaces before adhesive application enhances adhesion and water resistance. This approach is precious in industries where precise bonding is critical, such as aerospace.
Environmental Considerations
- Sustainability:Innovators are increasingly focusing on environmentally friendly adhesive solutions. Water-based adhesives, for instance, offer good water resistance without the harmful effects of solvent-based alternatives.
- Recyclability:Adhesive manufacturers are exploring recyclable options to reduce waste. Water-resistant adhesives facilitate easy separation from substrates and promote recyclability in various applications.
Waterproof adhesive glue stands as a resilient barrier against the challenges posed by moisture, expanding the possibilities for bonding in environments previously deemed hostile. Its role in enhancing materials’ longevity, structural integrity, and functionality is undeniable. As industries seek solutions that thrive in harsh conditions, waterproof adhesive glue will remain pivotal in driving innovation and efficiency. With ongoing research and advancements, researchers and innovators are positioning these adhesives to shape the future of bonding, creating durable products that can withstand the rigors of moisture-prone environments.