Two-Component Epoxy Adhesive: Properties, Applications, and Benefits
Two-component epoxy adhesives have become integral in modern industries, offering unmatched versatility, strength, and durability. Unlike single-component adhesives, two-component epoxies consist of a resin and a hardener mixed before application. This unique system provides greater control over curing and ensures robust bonds across various materials, including metals, plastics, ceramics, and composites. This article explores the characteristics, advantages, limitations, and applications of two-component epoxy adhesives in various industries.
What is a Two-Component Epoxy Adhesive?
Two-component epoxy adhesives are created by combining a resin (often based on bisphenol A or F) with a curing agent or hardener, typically an amine, anhydride, or polyamide. These two components undergo a chemical reaction upon mixing, transforming the liquid adhesive into a solid, durable bond. This curing process, known as polymerization, makes two-component epoxies highly versatile and allows for various modifications based on specific requirements.
The curing process begins when the two components are mixed, but the cure rate can be controlled by adjusting the formulation or environmental factors like temperature. Some adhesives may cure within minutes, while others may take hours or days. This flexibility makes two-component epoxies useful for quick repairs and longer, more complex assemblies.
Properties of Two-Component Epoxy Adhesives
Two-component epoxy adhesives offer several unique properties that make them suitable for demanding applications across various industries. Here are some key attributes:
High Bond Strength
Two-component epoxies provide exceptional bonding strength, often exceeding that of the bonding substrates. This makes them ideal for structural applications requiring durability and load-bearing capabilities.
Chemical Resistance
Epoxy adhesives are highly resistant to chemicals, including acids, solvents, and oils. This property makes them well-suited for use in harsh environments, such as automotive and industrial applications where exposure to chemicals is daily.
Thermal Stability
These adhesives can withstand a broad temperature range, typically between -50°C to 120°C, with some formulations able to withstand even higher temperatures. This stability is essential for applications where temperature fluctuations occur frequently.
Electrical Insulation
Epoxies are excellent electrical insulators, making them suitable for electronic applications. They are often used to encapsulate and protect electronic components from moisture, dust, and other contaminants.
Water Resistance
Two-component epoxies are moisture-resistant and can maintain their bonding strength even in humid or wet conditions, vital for outdoor applications or underwater repairs.
Customization
Two-component epoxies can be tailored for different properties, such as flexibility and application, depending on the application’s needs. This flexibility makes them popular in custom-engineered solutions.
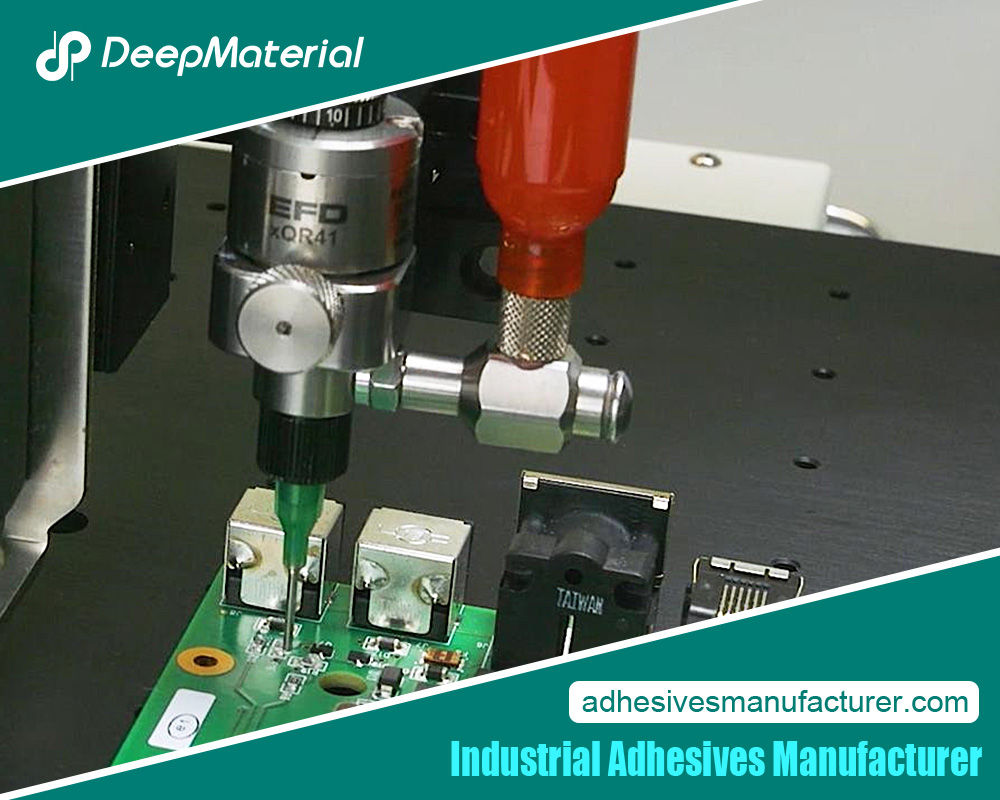
Advantages of Using Two-Component Epoxy Adhesives
The popularity of two-component epoxies is due to their many advantages, which set them apart from other types of adhesives:
Versatile Bonding Capabilities
Two-component epoxies are compatible with various materials, including metals, ceramics, plastics, glass, and composites. This broad compatibility allows manufacturers to use one adhesive for multiple substrates.
Precision and Consistency
The mixing ratio of resin and hardener can be precisely controlled, ensuring consistency in performance. Automated mixing systems also contribute to precision in large-scale industrial applications.
Long Shelf Life
Since the resin and hardener are stored separately, two-component epoxy adhesives typically have a long shelf life. Once mixed, they have a limited working time, but their shelf life in unmixed form is often months or even years, depending on storage conditions.
Tailored Curing Time
The curing time can be adjusted by selecting different hardeners or modifying the formulation, providing flexibility based on application needs. This adjustability allows for fast-setting epoxies for rapid repairs or slower-curing options for more controlled assembly.
Environmental Resistance
In addition to being resistant to chemicals and moisture, two-component epoxies can withstand UV exposure and extreme temperatures, making them ideal for outdoor and high-stress applications.
Limitations of Two-Component Epoxy Adhesives
Despite their many advantages, two-component epoxy adhesives also have certain limitations:
Limited Flexibility
After curing, most epoxies are rigid, making them unsuitable for applications requiring flexibility or bonding substrates with different expansion coefficients. However, some modified formulations offer enhanced flexibility.
Preparation Requirements
Proper surface preparation is essential to achieve the best bond strength. This often involves cleaning, abrading, or priming the surface, which can reduce application time and labor costs.
Handling and Mixing
Mixing the resin and hardener requires precision to ensure a consistent cure. Automated systems are often used in industrial settings to provide the correct ratio, but manual mixing can introduce errors in small-scale or DIY applications.
Limited Pot Life
Once mixed, two-component epoxies have a limited pot life (working time) before they begin to cure. This can restrict their use in applications that require prolonged open times or in hot environments where the curing rate accelerates.
Applications of Two-Component Epoxy Adhesives
Due to their versatility and strength, two-component epoxies are used in various industries, from automotive and aerospace to electronics and construction.
Automotive Industry
Epoxies and bonding components such as metal, plastic, and composites are used extensively in automotive applications. They are used for structural bonding in car frames, sealing and bonding of engine components, and even composite body parts due to their high strength and resistance to oil, fuel, and chemicals.
Aerospace Industry
In aerospace, two-component epoxies play a critical role due to their lightweight properties and strong adhesion to metals and composites. They are used in bonding panels, honeycomb structures, and even fuselage manufacturing, where the adhesive’s ability to withstand high temperatures and pressure is crucial.
Electronics and Electrical Industry
Two-component epoxies are widely used in electronics for potting and encapsulating sensitive components, protecting them from moisture, dust, and physical damage. Their electrical insulating properties make them ideal for transformers, motors, circuit boards, and connectors.
Construction and Infrastructure
Epoxy adhesives are popular in construction for structural bonding, concrete repairs, and anchoring. They bond materials such as concrete, stone, metal, and glass. Sometimes, epoxies repair cracked concrete in bridges, roads, and buildings.
Marine Applications
Due to their excellent resistance to water and chemicals, two-component epoxies are suitable for marine environments. They are commonly used in shipbuilding and maintenance, bonding metals, fiberglass, and wood while withstanding exposure to saltwater and harsh weather conditions.
Medical Device Manufacturing
Due to their biocompatibility and reliability, two-component epoxies are often used in medical device assembly. They bond plastic, metal, and glass components in devices like catheters, needles, and surgical instruments, where strength and stability are critical.
Choosing the Right Two-Component Epoxy Adhesive
Selecting a suitable two-component epoxy adhesive requires careful consideration of the application’s specific needs. Here are some factors to consider:
Substrate Compatibility
Not all epoxy adhesives bond well with every substrate. Consider whether the adhesive is compatible with the materials involved, and check the manufacturer’s recommendations for different substrates.
Curing Time
Applications requiring rapid assembly may benefit from fast-curing epoxies, while those requiring precision may need a slower curing option. Consider environmental factors, such as temperature, which can affect curing speed.
Viscosity and Application Method
Low-viscosity epoxies are ideal for filling gaps and cracks, while higher-viscosity formulations may be better for vertical applications or those needing a thicker bond line. The application method, such as spraying, brushing, or automated dispensing, will also influence the adhesive’s viscosity requirements.
Mechanical Properties
If the application requires load-bearing strength, choose a high-strength epoxy. Select a modified epoxy with rubber or silicone additives for applications requiring some flexibility.
Environmental Resistance
If the adhesive will be exposed to extreme temperatures, chemicals, or UV light, look for epoxies designed for those conditions. Marine-grade epoxies, for example, provide excellent resistance to water and salt.

Conclusion
Two-component epoxy adhesives offer remarkable versatility, strength, and durability, making them a staple in industries requiring reliable, long-lasting bonds. Their adaptability to different curing times, resistance to harsh environments, and ability to bond dissimilar materials have cemented their place in automotive, aerospace, electronics, and other sectors.
While they require careful handling, mixing, and surface preparation, the advantages of two-component epoxy adhesives significantly outweigh these challenges, particularly in applications where a high-performance bond is essential. By understanding the properties and potential applications, industries can choose which two-component epoxy adhesives best meet their needs. As technology and formulations evolve, two-component epoxy adhesives will continue to provide innovative bonding solutions for an ever-growing range of applications.
For more about two-component epoxy adhesive: properties, applications, and benefits, you can pay a visit to Deepmaterial at https://www.adhesivesmanufacturer.com/ for more info.