Two Component Epoxy Adhesive
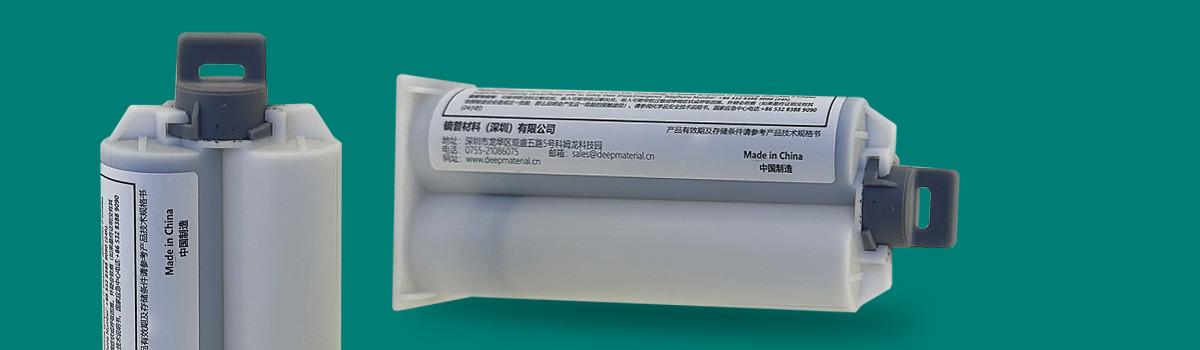
In the realm of adhesive technology, two component epoxy adhesives have carved a niche for themselves by offering a dynamic solution that combines the strength and versatility of epoxy with the precision of a controlled mixing process. These adhesives, which comprise a resin and a hardener, come to life when the components of resin and hardener mix. This mixing triggers a chemical reaction that results in a robust bond. This two-step process ensures optimal adhesion and allows for customization of properties such as cure time and flexibility. This comprehensive exploration delves into the realm of two component epoxy adhesives, uncovering their mechanisms, applications, benefits, and their pivotal role in versatile bonding solutions across industries.
Understanding Two Component Epoxy Adhesives
Two component epoxy adhesives represent a sophisticated bonding solution that combines the remarkable properties of epoxy resin and hardener to create robust and versatile adhesion. Comprising two distinct components that remain inert until mixed, these adhesives leverage a controlled chemical reaction to achieve optimal bonding. This dynamic interaction ensures a strong and durable bond and allows for customizing adhesive properties to suit specific application requirements. Key points to comprehend about two component epoxy adhesives include:
Dual Component System: Two component epoxy adhesives consist of a resin component and a separate hardener component, which are kept isolated until the point of use. This separation prevents premature curing and preserves the adhesive’s shelf life.
Chemical Reaction: The bonding begins upon mixing the resin and hardener. Initiating a chemical reaction forms strong covalent bonds between the adhesive and the substrates being bonded.
Customizable Properties: The mixing ratio of resin and hardener can be adjusted to control various adhesive properties such as curing time, flexibility, strength, and thermal resistance. This flexibility allows for tailored adhesion solutions to meet specific application demands.
Enhanced Performance: The chemical reaction between the components creates a bond that is typically stronger and more durable than single-component adhesives. This quality makes two component epoxy adhesives perfect for applications that demand exceptional structural integrity.
Versatility: These adhesives find utility in various industries, from electronics and automotive to aerospace and construction. Their ability to provide reliable bonds in multiple environments and substrates underscores their versatility.
Surface Preparation: Proper surface preparation is crucial to ensure successful bonding. Surfaces should be clean, dry, and contaminant-free to facilitate optimal adhesion.
Application Techniques: Commonly, users dispense two component epoxy adhesives using mixing nozzles, syringes, or dispensing equipment. Proper application techniques ensure uniform mixing and consistent bonding.
Curing Process: After application, the adhesive undergoes a curing process, transforming from a liquid to a solid state. Adjusting the resin-to-hardener ratio allows for control over the curing time.
Curing Conditions: Curing can occur at ambient or under elevated temperatures, depending on the adhesive formulation and application requirements.
Advantages of Dual Component Formulation
Using dual-component formulations in various industries offers a range of advantages that enhance performance, versatility, and customization in adhesive applications. This innovative approach involves combining two distinct components, often a resin and a hardener, at the moment of use to initiate a chemical reaction that drives bonding. The benefits of dual component formulations include:
Optimal Adhesion: The chemical reaction between the components results in a bond typically more vital and more durable than that achieved by single-component adhesives, ensuring reliable and long-lasting connections.
Customizable Properties: The ability to adjust the mixing ratio of components enables precise control over adhesive properties such as curing time, flexibility, strength, and thermal resistance. This tailoring allows for adhesive solutions that meet specific application requirements.
Controlled Curing: By fine-tuning the adhesive’s resin-to-hardener ratio, you can adjust the curing time to match the application’s requirements, whether you need rapid bonding or extended working time.
Flexibility in Use: Dual component formulations cater to various applications across diverse industries, including electronics, construction, automotive, aerospace, and more, demonstrating their adaptability to multiple substrates and environments.
Reduced Waste: Unlike one-component adhesives that can cure prematurely once opened, dual-component formulations remain inert until mixed. This approach eliminates waste caused by unused bonds going to waste due to limited working time.
Long Shelf Life: The components of dual-component adhesives can be stored separately for extended periods, preserving their efficacy and ensuring a longer shelf life than pre-mixed adhesives.
Consistent Performance: Mixing the components before application guarantees consistent adhesive properties, resulting in reliable performance and predictable outcomes.
Higher Temperature Resistance: The chemical reaction in dual component formulations often leads to adhesive bonds that exhibit superior resistance to high temperatures, making them suitable for applications that require thermal stability.
Enhanced Structural Integrity: The inherent strength of the chemical bonds formed by the reaction contributes to the structural integrity of bonded components, especially in demanding environments.
Versatile Application Methods: Dual component formulations can be applied using various techniques, including manual mixing, dual cartridge dispensing, and automated systems, accommodating different production scales and processes.
Mechanisms of Epoxy Adhesion
Their exceptional bonding properties and versatility make epoxy adhesives widely used in various industries. The adhesion of epoxy resins to different substrates involves intricate mechanisms influenced by a combination of chemical, physical, and interfacial factors. Understanding these mechanisms is crucial for optimizing adhesive performance and developing advanced bonding solutions. Several vital tools contribute to the adhesive strength of epoxy resins:
- Chemical Bonding:Epoxy adhesion often relies on chemical bonding, specifically covalent bonding, between the epoxy resin and the substrate. Epoxy resins contain reactive epoxy groups that can react with functional groups on the substrate surface, such as hydroxyl, amino, or carboxyl groups. These chemical reactions form strong and durable bonds, enhancing adhesion.
- Surface Preparation:Effective surface preparation is essential for promoting epoxy adhesion. Substrates must be clean, free from contaminants, and suitably roughened to create a larger surface area for adhesive contact. Techniques like sanding, degreasing, and etching are commonly employed to enhance mechanical interlocking and adhesion.
- Wetting and Spreading:Epoxy adhesives exhibit excellent wetting characteristics, allowing them to spread across the substrate surface and intimately contact irregularities. This wetting ability ensures that the sealant fully covers the substrate and minimizes voids or air pockets that could weaken the bond.
- Mechanical Interlocking:The automatic interlocking mechanism involves epoxy penetration into surface microstructures, such as pores, roughness, or grooves. As the epoxy cures, it solidifies within these microfeatures, creating a physical connection that enhances adhesion by resisting shear forces.
- Diffusion and Intermingling:Epoxy molecules can diffuse into the substrate to some extent, leading to the intermingling of the adhesive and substrate molecules at the interface. This diffusion increases the intermolecular interactions and creates a gradual transition zone, improving the overall bond strength.
- Curing and Crosslinking:Epoxy adhesives require a curing process, during which the epoxy resin undergoes crosslinking. Crosslinking involves the formation of strong covalent bonds between epoxy molecules, leading to the transformation of the initially liquid adhesive into a solid, rigid material. This curing process contributes to developing cohesive strength within the bond itself.
Resin and Hardener: Components of Bonding
In adhesives and bonding agents, few components are as pivotal as resin and hardener. When combined in the right proportions, these two substances create a potent bond widely used across industries for joining materials, from simple crafts to complex industrial applications. Here’s a closer look at these essential components and how they work together:
Resin: Resin is a dense, often transparent, or slightly colored substance that is the primary adhesive in the bonding process. It is typically derived from organic compounds and can be modified to suit various applications. Resins form strong bonds with materials such as wood, plastic, glass, and metals. They have a low molecular weight and can flow and wet surfaces effectively. This characteristic allows the resin to penetrate the pores and imperfections of substrates, creating a secure connection. Manufacturers can tailor resins to possess specific properties, such as flexibility, heat resistance, or transparency, which makes them versatile for different uses.
Hardener: The hardener is the catalyst that initiates the chemical reaction between the resin molecules. When combined with the resin, it triggers a process called curing or polymerization. Hardener molecules create cross-linking bonds between the resin molecules, transforming the initially liquid or semi-liquid mixture into a solid, durable adhesive. The hardening process is often irreversible and irreversible, resulting in a material that exhibits high mechanical strength and dimensional stability. Depending on the specific formulation, hardeners can impact the bonded material’s curing time, temperature sensitivity, and final properties.
The synergy between resin and hardener is crucial for achieving successful bonds. Correctly measuring and mixing these components in proportions is vital to ensure the adhesive’s integrity and strength. Additionally, when choosing resin and hardener types for a specific application, you should align them with factors like the materials being bonded, environmental conditions, and desired properties of the final product.
Structural Bonding with Two Component Epoxies
Two-component epoxies have revolutionized the realm of structural bonding, offering a versatile and robust solution for joining materials across a wide range of industries. These epoxies, which comprise a resin and a hardener, create bonds that are incredibly strong but also durable and resistant to various environmental factors. Here’s an exploration of the key features and advantages of using two-component epoxies for structural bonding:
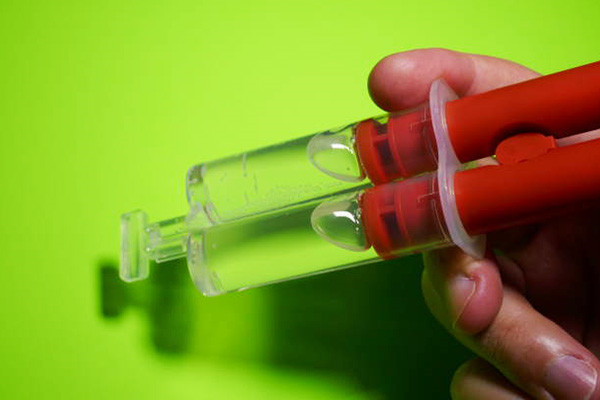
- Superior Strength:Two component epoxy adhesives are renowned for their exceptional bonding strength. Mixing the resin and hardener in the prescribed ratio initiates a chemical reaction that forms cross-linked polymer chains. This results in bonds that can withstand significant loads and stresses, making them ideal for applications where structural integrity is crucial.
- Versatile Substrate Compatibility:Two component epoxies exhibit remarkable adhesion to various substrates, whether made of metal, plastic, wood, ceramic, or composite materials. Their ability to bond dissimilar materials expands their utility across diverse industries, from construction and automotive to electronics and aerospace.
- Durability and Resistance:Once cured, two component epoxy bonds are highly resistant to environmental factors such as temperature fluctuations, moisture, chemicals, and UV exposure. This durability ensures the longevity of the bonded structure, reducing the need for frequent maintenance or replacements.
- Gap-Filling Capability:Two component epoxies possess excellent gap-filling properties due to their low viscosity before curing. This characteristic enables these adhesives to effectively fill voids and imperfections in mating surfaces, ensuring a uniform and secure bond, even on uneven surfaces.
- Design Flexibility:The versatility of two component epoxy adhesives extends to their application methods. They can be applied using injection molding, brush coating, or dispensing techniques, allowing for customization based on the specific bonding requirements and production processes.
- Temperature and Chemical Resistance:Two component epoxies can endure extreme temperatures, ranging from sub-zero to high-heat environments, without compromising their adhesive properties. They also resist various chemicals, which makes them suitable for applications anticipating exposure to harsh substances.
Controlled Curing and Customization
Two-component epoxy adhesives stand out for their exceptional bonding capabilities and their controlled curing process and customization options, offering engineers and manufacturers greater flexibility in various applications. A precise mixture of resin and hardener initiates a chemical reaction, leading to controlled curing with benefits. Here are the key points highlighting the controlled curing and customization aspects of two-component epoxy adhesives:
Tailored Working Time: The controlled curing process allows for a tailored working time, known as pot life. You can modify this time frame between mixing and complete curing by selecting formulations with varying pot life durations. This versatility is advantageous in scenarios where complex assemblies or intricate bonding processes are involved.
Adaptability to Application: Two-component epoxy adhesives can be customized to fit the specific requirements of an application. Manufacturers can select bonds with varying cure speeds and viscosities, ensuring an optimal fit for tasks ranging from rapid production line bonding to intricate, time-intensive projects.
Room Temperature or Elevated Curing: These adhesives can be designed to cure either at room temperature or with heat application. This adaptability is particularly useful when working with substrates sensitive to temperature changes or aiming for a faster curing process.
Color and Aesthetic Considerations: Two-component epoxy adhesives can formulate in different colors for applications where aesthetics matter. This aspect is particularly relevant for visible bonds, especially in industries like furniture manufacturing, where matching adhesive color to materials is essential for a seamless finish.
Enhanced Bonding Performance: Customization extends beyond the curing process. Engineers can tailor adhesive formulations to achieve specific binding properties, such as flexibility, impact resistance, or high strength. This adaptability ensures that the adhesive is optimized to handle the stresses and requirements of the intended application.
Adhesion to Various Substrates: Two-component epoxy adhesives can be designed to adhere to a wide range of substrates, from metals and plastics to composites and ceramics. This adaptability enables bonding between different materials, enhancing the potential applications of these adhesives.
Heat and Chemical Resistance
Two-component epoxy adhesives have garnered widespread recognition in the world of bonding due to their exceptional heat and chemical resistance properties. These adhesives consist of a resin and a hardener mixed just before application, initiating a chemical reaction resulting in a solid and durable bond. One of the most remarkable features of these adhesives is their ability to withstand extreme temperatures and harsh chemical environments, making them invaluable in various industrial, automotive, aerospace, and electronic applications.
Here are the key aspects highlighting the heat and chemical resistance of two-component epoxy adhesives:
- High-Temperature Endurance:Two-component epoxy adhesives are designed to maintain structural integrity even when exposed to elevated temperatures. They can endure temperatures ranging from sub-zero to well over 200°C (392°F), making them suitable for applications where other adhesive options might degrade or fail.
- Chemical Shielding:These adhesives defend against various chemicals, acids, solvents, and oils. Their chemical resistance is pivotal in environments where exposure to aggressive substances could compromise the integrity of bonded materials. This characteristic extends the lifespan of related components, reducing maintenance and replacement costs.
- Durability in Harsh Environments:Industries such as aerospace and automotive rely on two-component epoxy adhesives to create bonds that last in challenging settings. These adhesives ensure stability in conditions involving constant vibrations, thermal cycling, and exposure to varying moisture levels.
- Corrosion Prevention:The heat and chemical resistance of two-component epoxy adhesives also aid in preventing corrosion. By forming a barrier against moisture and corrosive agents, these adhesives protect the underlying materials from degradation and maintain the structural strength of the bonded joint.
- Versatility:Two-component epoxy adhesives exhibit heat and chemical resistance across various substrates, including metals, plastics, composites, and ceramics. This versatility enables engineers and manufacturers to choose the appropriate adhesive for their specific application, enhancing the overall reliability and performance of the end product.
Electrical Insulation Properties
Two Component Epoxy Adhesives are widely valued for their exceptional electrical insulation properties, making them indispensable in various industries that require reliable bonding solutions while maintaining electrical integrity. These adhesives offer a combination of robust adhesive strength and effective electrical insulation, addressing the unique needs of electronic devices and components.
Dielectric Strength: One of the primary advantages of Two Component Epoxy Adhesives is their high dielectric strength, allowing them to withstand significant electrical fields without breaking down. This property is critical for preventing electrical leakage and short circuits, especially in closely packed components.
Surface Insulation: These adhesives create a reliable insulating layer on surfaces, preventing direct contact between conductive elements and reducing the risk of unintended electrical pathways. This feature is essential in complex circuitry where precise insulation is crucial.
Protection Against Moisture and Contaminants: In electronic applications, exposure to moisture and contaminants can compromise electrical performance. Two Component Epoxy Adhesives form a protective barrier that shields components from these elements, ensuring consistent and reliable electrical insulation over time.
Thermal Stability: Many electronic devices generate heat during operation. Two Component Epoxy Adhesives that offer thermal stability maintain their electrical insulation properties even at elevated temperatures, preventing insulation breakdown in demanding conditions.
Flexibility in Formulations: The versatility of Two Component Epoxy Adhesives allows for tailored formulations to match specific electrical insulation requirements. This flexibility permits engineers to select adhesives that align precisely with the needs of their devices.
Substrate Compatibility: These adhesives provide strong adhesion to various substrates commonly used in electronics, enabling consistent electrical insulation across diverse components and materials.
However, a few considerations are essential:
Curing and Mixing Precision: Achieving optimal electrical insulation properties requires accurately mixing the adhesive’s two components and adherence to recommended curing conditions. Deviations can lead to compromised insulation performance.
Testing and Validation: In critical electronic applications, thorough testing and validation are necessary to ensure that the selected adhesive meets required electrical insulation standards and maintains reliability over time.
Temperature and Environmental Factors: While Two Component Epoxy Adhesives offer excellent electrical insulation, verifying their performance across the range of temperatures and environmental conditions they might encounter is essential.
Electronics and Component Assembly
Two Component Epoxy Adhesives have emerged as essential materials in electronics and component assembly, addressing these industries’ intricate bonding needs and performance requirements. These adhesives offer a versatile solution for creating strong, durable, and reliable bonds in various electronic devices and components.
Miniaturization Support: The electronics industry continuously strives for smaller, more compact devices. Two Component Epoxy Adhesives enable precision bonding in tight spaces, securing delicate components and ensuring optimal functionality in miniature electronics.
Thermal Conductivity: Some formulations of Two Component Epoxy Adhesives exhibit high thermal conductivity in applications like semiconductors, where heat dissipation is critical. This property helps transfer heat away from sensitive components, preventing overheating and enhancing overall performance.
Electrical Insulation: These adhesives often possess excellent electrical insulation properties, crucial for preventing short circuits and ensuring proper signal transmission in electronic devices and circuits.
Adhesion to Various Substrates: Electronics involves various materials, from metals to plastics. Two Component Epoxy Adhesives offer strong adhesion to diverse substrates, providing a reliable bond regardless of the materials. We are in the process of joining.
Chemical and Environmental Protection: Components in electronics are vulnerable to moisture, chemicals, and environmental factors. Two Component Epoxy Adhesives act as a protective barrier, guarding against corrosion and ensuring the longevity of components in various conditions.
Customizable Formulations: Different electronic applications have unique bonding requirements. Two Component Epoxy Adhesives can be formulated with specific properties, such as curing time, flexibility, and bond strength, to cater to the particular needs of each application.
However, specific considerations are essential:
Precision Mixing: Achieving the desired properties necessitates accurately mixing the two components in the proper ratios. Inaccurate mixing can lead to variations in adhesive performance.
Curing Conditions: Adhering to recommended curing conditions, including temperature and humidity, is vital for achieving optimal bond strength and performance.
Pot Life Management: After mixing, two Component Epoxy Adhesives have a limited pot life. Proper application within the pot life timeframe is crucial to prevent premature curing and wastage.
Automotive and Aerospace Applications
Two Component Epoxy Adhesives have become indispensable in both automotive and aerospace applications, where the need for strong and durable bonding solutions aligns with the demands of these industries. These adhesives offer a versatile solution for achieving robust bonds in diverse and challenging environments, enhancing components’ structural integrity and performance.
Structural Bonding: Two Component Epoxy Adhesives are favored for their exceptional bonding strength, making them essential for joining critical components in automotive and aerospace structures. They distribute stress evenly across bonded surfaces, contributing to load-bearing capacity and overall structural stability.
Vibration and Impact Resistance: Components Undergo vibrations and impacts in both industries. Two Component Epoxy Adhesives provide a cushioning effect that helps absorb shocks, reducing the risk of damage and fatigue, vital in applications like aircraft interiors and vehicle assemblies.
Weight Reduction: Aerospace and automotive sectors prioritize weight reduction for improved fuel efficiency and performance. These adhesives allow for the substitution of heavy mechanical fasteners, leading to significant weight savings without compromising bond integrity.
Chemical and Environmental Protection: Two Component Epoxy Adhesives are a barrier against moisture, chemicals, and environmental factors that could degrade materials. This protective layer ensures the longevity of components exposed to diverse conditions such as corrosive chemicals or changing weather.
Temperature Resistance: Both industries encounter extreme temperature fluctuations. Two Component Epoxy Adhesives offer reliable performance across a wide temperature range, from the extreme cold of aerospace applications to the high temperatures under automotive hoods.
Customizable Formulations: These adhesives can be tailored to specific requirements, allowing for the optimization of properties like cure time, flexibility, and adhesion strength. This flexibility ensures compatibility with the unique needs of each industry.
However, specific considerations apply:
Precise Mixing: Proper mixing of the two components is crucial for achieving optimal bonding properties. Deviations from recommended mixing ratios can affect the strength and performance of the adhesive.
Pot Life: Two Component Epoxy Adhesives have a limited pot life after mixing, requiring efficient application to avoid wastage and compromised bonds due to premature curing.
Curing Conditions: Achieving thorough curing requires adherence to recommended conditions, including temperature and humidity. Deviations can lead to incomplete curing and compromised bond strength.
Medical Device Bonding
The convergence of Automotive and Aerospace Applications with the field of Medical Device Bonding highlights the remarkable versatility of adhesive technologies across diverse industries. Advanced adhesives play a pivotal role in structural integrity, weight reduction, and enhancing aerodynamics in the realm of Automotive and Aerospace Applications. In aerospace, bonding technologies facilitate the assembly of composite materials, ensuring the robustness of components subjected to extreme conditions. Similarly, in the automotive sector, adhesives are used to join dissimilar materials, contributing to improved fuel efficiency and crash performance. The integration of adhesive solutions in these sectors underscores the significance of innovation in achieving unparalleled performance and safety.
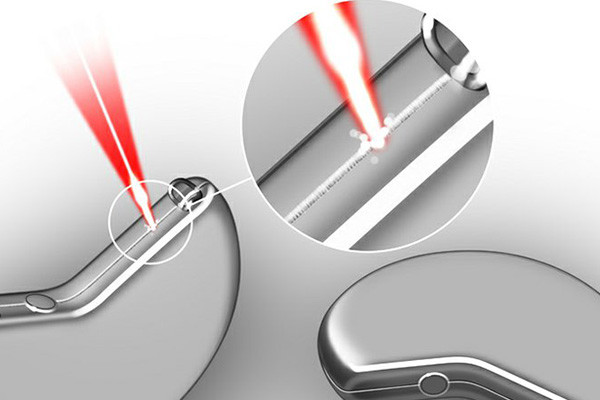
Transitioning to Medical Device Bonding, adhesive technologies demonstrate their importance in the healthcare landscape. Medical devices demand precision, biocompatibility, and durability, making adhesives invaluable. Bonding techniques assemble intricate medical devices like catheters, pacemakers, and wound care products. We carefully tailor adhesive properties to ensure secure attachment, patient comfort, and the prevention of infections. Moreover, adhesives enable the development of wearable medical devices, such as continuous glucose monitors and remote patient monitoring patches, which adhere seamlessly to the skin while delivering critical healthcare insights.
Key points encompassing the integration of adhesive technologies in Automotive and Aerospace Applications, as well as Medical Device Bonding, include:
Material Versatility: Adhesives offer the advantage of bonding different materials, promoting design flexibility, and allowing the use of lightweight and specialized components in both aerospace and automotive manufacturing. In medical devices, adhesives facilitate the joining of delicate materials without compromising patient safety.
Structural Integrity: Adhesive bonds distribute stress more evenly than traditional mechanical fasteners, enhancing the structural integrity of components in vehicles and aircraft and in medical devices designed for durability and longevity.
Reduced Weight and Improved Efficiency: In the automotive and aerospace sectors, adhesives contribute to weight reduction, leading to improved fuel efficiency and better performance. Similarly, lightweight sealants are crucial for minimizing device weight without compromising functionality in medical devices.
Biocompatibility: Medical Device Bonding necessitates adhesives that are biocompatible and safe for use within the human body. These adhesives must securely adhere while posing no harm to patients.
Precision Assembly: In all three fields, precise assembly is essential. Adhesives offer the advantage of uniform distribution, enabling seamless bonding of intricate components.
Construction and Infrastructure Use
The symbiotic relationship between adhesive technologies and the realm of Construction and Infrastructure Use underscores the transformative impact of these materials in shaping our built environment. Adhesives play a multifaceted role in modern construction, offering solutions that range from improving structural integrity and durability to enhancing energy efficiency and design aesthetics. Critical points in the integration of adhesive technologies in construction and infrastructure include:
Structural Bonding: Adhesives have revolutionized how construction connects structural components. They offer a strong, even bond that distributes stress more effectively than traditional mechanical fasteners, increasing load-bearing capacity and resilience against seismic forces. Applications range from bonding large glass panels in skyscrapers to joining pre-fabricated concrete elements.
Energy Efficiency: Adhesive technologies contribute to enhancing energy efficiency in buildings. Insulation materials, such as panels and foams, are securely attached using adhesives, minimizing thermal bridging and improving overall energy performance. It is essential to prioritize sustainable building designs that effectively reduce heating and cooling demands.
Facade Enhancement: Adhesives enable the creation of stunning and innovative building facades. Modern architecture often features complex geometries and materials like glass, metal, and composites, seamlessly integrated using advanced bonding techniques. This results in aesthetically pleasing exteriors that push the boundaries of design.
Quick and Precise Installation: Adhesives offer rapid curing times, allowing for efficient installation of construction elements. Having this ability is especially useful for projects that have strict deadlines. Additionally, using adhesives reduces the need for heavy equipment and noisy construction processes, contributing to a more sustainable and less disruptive construction environment.
Durability and Longevity: Adhesive technologies enhance the longevity of construction materials by providing a protective barrier against environmental factors like moisture, corrosion, and UV radiation. It is essential to ensure the longevity of buildings and infrastructure by taking necessary measures.
Specialized Applications: Adhesives cater to technical construction needs. For instance, in assembling composite materials in bridges, adhesives provide high-strength bonds that can withstand dynamic loads and harsh weather conditions. In tunnels, sealants secure fire-resistant panels that enhance safety.
Green Building Practices: Adhesive technologies align with green building practices by minimizing material waste and reducing the need for resource-intensive construction methods. Low-VOC (volatile organic compounds) adhesives contribute to better indoor air quality.
Dispensing Techniques and Mixing Ratios
In adhesive applications, achieving accurate and consistent results hinges on two critical factors: dispensing techniques and mixing ratios. These components work in tandem to ensure that adhesives are applied effectively, yielding reliable bonds and optimal product quality.
Dispensing Techniques: From Manual to Robotic
Various dispensing techniques cater to different needs and levels of precision:
- Manual Dispensing:In situations requiring intricate control, manual dispensing remains invaluable. Operators use hand-operated tools to place adhesives, making them suitable for small-scale applications.
- Pneumatic and Mechanical Dispensing:These systems, which employ air pressure or mechanical mechanisms, are ideal for larger production volumes. They ensure consistent adhesive flow rates, reducing variability and operator fatigue.
- Robotic Dispensing:Robotic systems offer unmatched precision for complex applications. Programming robots to apply adhesive with micron-level accuracy is optimal for high-volume production and intricate designs.
Mixing Ratios: Balancing Components for Optimal Performance
Mixing ratios are crucial, particularly in two-part adhesive applications, where improper ratios can lead to incomplete curing and weak bonds. Two common approaches include:
- Weight Ratio:We achieve accurate ratios by measuring adhesive components by weight. This approach is well-suited for production settings, with digital scales and automated systems ensuring precision.
- Volume Ratio:Volume-based mixing is standard, though differences in component viscosity can pose challenges. Thorough mixing compensates for viscosity variations, ensuring proper curing.
- Metering Systems:For large-scale applications, metering systems offer meticulous control. These automated setups accurately measure components, minimizing waste and promoting consistency.
Harmony in Practice: Achieving Consistency
Dispensing techniques and mixing ratios intersect to deliver adhesive excellence. The appropriate method and ratio depend on adhesive properties, application requirements, and production scale. Be it delicate medical devices, intricate aerospace components, or massive construction projects, the harmony of precise dispensing and accurate mixing guarantees the final adhesive product’s integrity, reliability, and performance.
Quality Control and Testing Standards
In adhesive applications, maintaining quality control and adhering to rigorous testing standards are paramount to ensuring optimal performance, reliability, and safety. As adhesive technologies evolve across industries, stringent quality control measures and standardized testing procedures are pivotal in verifying adhesive properties and performance.
Critical aspects of Quality Control and Testing Standards in the realm of adhesive applications include:
- Raw Material Verification:The journey to adhesive excellence begins with thoroughly examining raw materials. Adhesive manufacturers and end-users rely on quality suppliers, conducting rigorous checks to ensure the consistency and integrity of incoming materials. This verification process prevents variations that could compromise the adhesive’s final performance.
- Batch-to-Batch Consistency:Manufacturers monitor and control batch-to-batch consistency by implementing strict quality control protocols. Analytical techniques, such as spectroscopy and chromatography, help ensure that adhesive formulations remain within specified parameters, reducing the risk of unexpected variations.
- Adhesion and Bond Strength Testing:Adhesive performance hinges on creating solid bonds. Adhesion tests assess how well an adhesive attaches to specific substrates, while bond strength tests evaluate the durability of the adhesive-substrate connection. These tests simulate real-world conditions, ensuring the adhesive can withstand various stresses.
- Environmental and Aging Tests:Adhesives often encounter challenging environmental conditions. Accelerated aging tests subject adhesives to extreme temperatures, humidity, and UV exposure, providing insights into long-term durability. These tests are crucial for applications exposed to harsh environments.
- Viscosity and Rheological Analysis:Adhesive viscosity affects dispensing, while rheological properties impact flow behavior. Consistent thickness ensures uniform application, while rheological analysis aids in optimizing adhesive performance under different conditions.
- Adhesive Cure and Setting Time:Determining optimal cure and setting times is vital for production efficiency. Accurate measurement of these times helps establish appropriate process timelines and ensures that the adhesive achieves the desired properties upon curing.
- Industry-Specific Standards:Different industries have distinct adhesive requirements. Organizations like ASTM, ISO, and NIST establish industry-specific standards for adhesive testing. Complying with these standards ensures that adhesives meet established performance benchmarks.
- Non-Destructive Testing:Advanced techniques like ultrasonic testing and thermography allow for non-destructive evaluation of adhesive bonds. These methods provide insights into bond integrity without compromising the tested components.
Curing and Reaction Mechanisms
The curing process and the underlying reaction mechanisms within adhesives are the core determinants of adhesive performance, durability, and functionality. Understanding these intricate processes and employing appropriate techniques are vital to ensuring optimal bond strength and reliability in diverse applications.
Key aspects of Curing and Reaction Mechanisms in adhesive applications include:
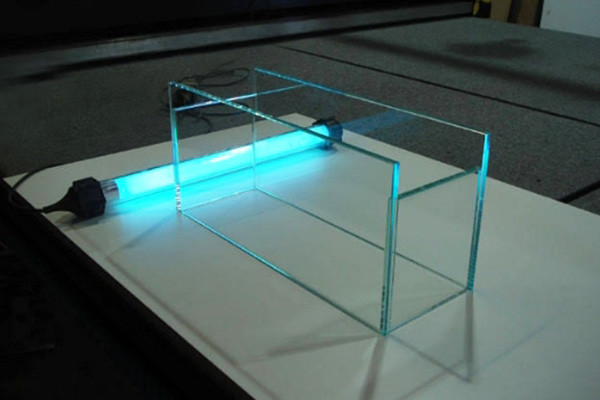
Chemical Crosslinking: Many adhesives rely on chemical reactions to achieve curing. In two-part adhesives, the resin and hardener undergo crosslinking, forming a network that solidifies the adhesive. This chemical transformation grants adhesives their inherent strength and durability.
Curing Agents and Catalysts: Curing agents and catalysts initiate and accelerate crosslinking. Their careful selection and proportion influence curing time and bond performance. Matching the curing agent with the adhesive composition is critical for achieving consistent and reliable results.
Temperature and Humidity: Environmental factors play a pivotal role in curing. Temperature and humidity levels impact curing rates and influence adhesive properties. Properly controlling these conditions ensures that adhesives cure predictably and uniformly.
UV and Light Curing: In applications demanding rapid curing, UV and light-curing adhesives offer a solution. These adhesives solidify upon exposure to specific wavelengths of Light. This swift curing method enhances efficiency in manufacturing processes.
Thermal Curing: Thermal curing involves applying heat to facilitate the crosslinking process. Different formulations and substrates require specific temperature profiles to achieve desired bond strength and durability.
Hybrid Curing Methods: Some adhesives employ mixed techniques, combining chemical reactions with physical processes. These methods leverage the benefits of multiple curing mechanisms, achieving a balance between speed and strength.
In-Depth Monitoring: To ensure consistent results, real-time monitoring of curing is crucial. Techniques such as thermosetting and infrared analysis provide insights into the progression of chemical reactions, enabling adjustments if needed.
Post-Curing Effects: Post-curing processes, like elevated temperature exposure after initial curing, can further enhance adhesive properties. This additional step improves bond strength, chemical resistance, and overall performance.
Reaction Kinetics: Understanding the kinetics of curing reactions is vital for optimizing adhesive application processes. Reaction kinetics provide insights into how curing progresses, guiding decisions on curing times and temperature profiles.
Environmental Considerations and Sustainability
In an era of growing environmental consciousness, the adhesive industry embraces a paradigm shift toward ecological considerations and sustainability. Adhesives, integral to many applications, are now scrutinized for their environmental impact. Addressing this concern entails a comprehensive approach encompassing raw material selection, production processes, application methods, and end-of-life considerations.
Key aspects of Environmental Considerations and Sustainability in the adhesive industry include:
- Eco-Friendly Formulations:Adhesive manufacturers are increasingly developing formulations with reduced environmental impact. One way to reduce air pollution is by minimizing the release of volatile organic compounds (VOCs). Water-based and solvent-free adhesives are becoming prevalent alternatives, improving indoor air quality and reducing harmful emissions.
- Bio-Based Materials:Bio-based materials derived from renewable resources offer a sustainable alternative to traditional petroleum-based ingredients. These materials reduce reliance on fossil fuels and have a smaller carbon footprint.
- Recyclability and Disassembly:Adhesive bonds can complicate the recycling process of assembled materials. Designing adhesives that allow for easy disassembly and material separation enhances recyclability. It is essential to reduce waste and encourage a circular economy.
- Energy-Efficient Manufacturing:Manufacturers are focusing on energy-efficient production processes. Optimizing energy consumption reduces operational costs and lessens the industry’s overall environmental impact.
- Reduced Packaging Waste:Sustainable adhesive solutions extend to packaging. Efforts to minimize packaging waste through eco-friendly materials and efficient designs contribute to environmental stewardship.
- Life Cycle Assessments:Employing life cycle assessments (LCAs) helps quantify an adhesive’s total environmental impact, from raw material extraction to end-of-life disposal. LCAs guide decisions toward more sustainable adhesive choices.
- Regulatory Compliance:Adhesive manufacturers adhere to environmental regulations and standards to ensure products are safe for users and the environment. Compliance with guidelines such as REACH and RoHS provides responsible chemical use and waste management.
- End-of-Life Considerations:Designing adhesives with end-of-life in mind is critical. Adhesives that facilitate easy separation of bonded materials at the end of their useful life support recycling efforts and reduce waste.
- Longevity and Durability:Durable adhesive bonds contribute to longer-lasting products, reducing the need for frequent replacements and conserving resources.
Challenges in Mixing and Application
Mixing and application are pivotal stages in adhesive, yet they often present intricate challenges that require careful consideration and expertise. Achieving consistent and reliable adhesive bonds requires addressing these challenges to ensure optimal performance across various industries and applications.
Key challenges in the Mixing and Application of adhesives include:
Viscosity Variations: Adhesives come in diverse formulations with varying viscosities. Achieving consistent viscosity across different batches can be challenging, impacting application uniformity and adhesive performance.
Substrate Compatibility: Different substrates demand tailored adhesive formulations. Ensuring compatibility between the adhesive and substrates, especially when dealing with dissimilar materials, is crucial for long-lasting bonds.
Pot Life Limitations: Adhesives often have limited pot life, during which they remain workable. Managing this window becomes challenging, particularly in larger applications or complex assemblies.
Homogeneous Mixing: In two-part adhesives, achieving complete and homogeneous mixing of components is essential for uniform curing and optimal performance. Inadequate mixing can lead to weak bonds and inconsistencies.
Rapid Curing: While fast curing is advantageous for efficiency, it can pose challenges in large applications or complex geometries. Ensuring that adhesive cures before application can be demanding.
Adhesive Placement Precision: Achieving precision in adhesive placement, especially in intricate designs or tight spaces, requires advanced dispensing techniques and robotic systems.
Surface Preparation: Proper surface preparation is critical for adhesive bonding. Challenges arise when dealing with surfaces contaminated by oils, dirt, or oxidation, impacting adhesive adhesion.
Application Temperature: Adhesives can behave differently under varying temperatures. Ensuring consistent application temperature is essential for achieving desired adhesive properties.
Adhesive Migration: Some adhesives, especially those with low viscosity, can migrate within substrates after application. Weakening bonds can harm long-term performance.
Health and Safety: Adhesives may contain volatile solvents or chemicals that pose health and safety risks to workers. Proper ventilation, protective equipment, and safe handling practices are essential to mitigate these challenges.
Quality Control During Application: Monitoring adhesive application in real-time to ensure uniformity and accuracy is challenging, particularly in high-speed production environments.
Future Trends in Epoxy Adhesive Technology
Epoxy adhesive technology is poised to undergo transformative advancements that redefine its role across industries. As demands for higher performance, sustainability, and efficiency rise, future trends in epoxy adhesive technology are poised to shape the landscape of adhesive applications in diverse sectors.
Green Formulations and Bio-Based Epoxy Resins:
In response to growing environmental concerns, the future of epoxy adhesives lies in developing eco-friendly formulations. The utilization of bio-based epoxy resins derived from renewable sources is gaining traction. These resins reduce the reliance on fossil fuels and offer comparable or improved performance, making them a sustainable alternative.
Nanotechnology Integration:
Nanotechnology is poised to revolutionize epoxy adhesive properties. Incorporating nanoparticles can enhance epoxy adhesives’ mechanical strength, thermal conductivity, and electrical properties. This advancement holds significant promise for industries seeking high-performance materials for electronics and aerospace applications.
Innovative and Self-Healing Epoxy Adhesives:
The future will witness the rise of intelligent epoxy adhesives with self-healing capabilities. Incorporating microcapsules containing adhesive agents within the epoxy matrix enables autonomous repair of microcracks and damage. This innovation can extend the lifespan of bonded materials and reduce maintenance efforts.
Enhanced Toughness and Durability:
Future epoxy formulations will focus on achieving excellent toughness and durability. By engineering epoxy structures at the molecular level, adhesive manufacturers aim to enhance impact resistance and fatigue performance. This trend is particularly significant in industries like automotive and aerospace, where materials undergo rigorous conditions.
Customization for Additive Manufacturing:
With the rapid growth of additive manufacturing, epoxy adhesives tailored for 3D printing applications will become crucial. These specialized adhesives allow solid bonding between printed layers, creating intricate and durable structures.
Digitalization and Simulation Techniques:
The integration of digitalization and simulation techniques will streamline adhesive development. Predictive modeling and simulations can aid in designing epoxy formulations with specific properties, accelerating the research and development process.
Biomedical Applications:
Epoxy adhesives are poised to play a significant role in biomedical applications, such as medical device assembly and tissue bonding. We will engineer biocompatible epoxy formulations to meet the stringent requirements of these applications while ensuring patient safety
Innovative Applications of Dual Component Epoxies
Dual component epoxies, renowned for their exceptional bonding properties, are finding innovative applications that push the boundaries of technology and industry. These versatile adhesives, composed of a resin and a hardener that react upon mixing, have evolved beyond traditional uses to tackle new challenges and enable groundbreaking solutions.

Advanced Electronics Assembly:
Dual component epoxies are revolutionizing electronics assembly. As electronics become smaller and more complex, these adhesives offer precise bonding that ensures optimal thermal and electrical conductivity. They facilitate the creation of miniaturized components and enable the assembly of delicate devices like wearables, sensors, and medical implants.
Structural Reinforcement in Automotive and Aerospace:
In the automotive and aerospace industries, dual-component epoxies contribute to lightweight structural reinforcement. They bond composite materials, joining components with high strength and durability. This innovation improves vehicle fuel efficiency and enhances aircraft performance, ensuring safety and longevity.
3D Printing and Additive Manufacturing:
We are tailoring dual-component epoxy resins for additive manufacturing processes like stereolithography. These resins allow for precise layer-by-layer curing, resulting in complex and accurate 3D-printed structures. This application is transforming industries from rapid prototyping to customized medical implants.
Energy Efficiency and Renewable Energy:
Dual-component epoxies are instrumental in renewable energy applications. They are used to bond solar panels, ensuring longevity and stability in harsh environmental conditions. Additionally, they play a role in manufacturing energy-efficient appliances by securely joining components and enhancing thermal insulation.
Biomedical and Healthcare Devices:
In healthcare, dual-component epoxies contribute to assembling medical devices and implants. Biocompatible formulations ensure safe and reliable bonds in devices ranging from pacemakers to prosthetics. These adhesives adhere to strict regulatory requirements and contribute to advancements in patient care.
Benefits of Customizable Bonding Properties
Customizing bonding properties in adhesives offers a spectrum of benefits catering to diverse industries and applications. This tailored approach empowers manufacturers, engineers, and researchers to fine-tune adhesive formulations according to specific requirements, optimizing performance, durability, and efficiency.
Enhanced Adhesion Strength: Customizable bonding properties allow for the optimization of adhesion strength to match the bonded substrates. By ensuring robust bonds that can withstand stressors and environmental conditions, we can contribute to creating longer-lasting products.
Optimized Cure Speed: Industries often demand adhesive formulations that cure rapidly for increased production speed or slowly for intricate assembly processes. Customizable cure speed enables efficient workflows and precision.
Flexibility and Toughness: Some applications require flexibility, while others demand toughness. The ability to tailor adhesive properties enables manufacturers to strike the right balance between these attributes, enhancing product resilience without compromising integrity.
Temperature Resistance: Customization allows adhesives to withstand specific temperature ranges, making them suitable for applications in extreme environments, such as aerospace or automotive.
Chemical Resistance: Certain industries, like the chemical or pharmaceutical sectors, require highly resistant adhesives to specific chemicals. Customization ensures that adhesive bonds remain intact when exposed to corrosive substances.
Controlled Viscosity: Customizable viscosity is essential for precise application. Formulators can create low-density adhesives for easy dispensing into tight spaces or high-density for vertical applications, ensuring uniform coverage.
Tailored Flexibility: Adhesives can be customized to offer the desired level of flexibility. This is important for applications where materials like electronics expand and contract due to temperature changes.
Reduced Waste: Customizable adhesive properties minimize waste by optimizing adhesive usage for each application, leading to cost savings and sustainability.
Compatibility with Substrates: Different substrates require adhesives with specific properties to ensure proper bonding. Customization ensures compatibility, preventing adhesive failure due to substrate mismatch.
Product Differentiation: Customizable adhesives allow manufacturers to differentiate their products by offering tailored solutions that meet customer needs.
Two Component Epoxy Adhesives testify to the power of precision and chemical reaction in bonding technology. Their role in providing robust, customizable, and reliable bonds is pivotal in industries that demand versatile adhesion solutions. As technology advances and initiatives seek innovative ways to achieve optimal bonding, two Component Epoxy Adhesives will remain a cornerstone in driving innovation and efficiency. Ongoing research and improvements are positioning these adhesives to shape the future of adhesive technology further, contributing to the creation of products that seamlessly integrate customized bonding properties into a wide array of applications.