The Rise of Industrial Automotive Adhesives
The Rise of Industrial Automotive Adhesives
The automotive industry has long been at the forefront of innovation, and the role of adhesives in this sector has been steadily growing over the past two decades. As the industry has evolved, driven by global megatrends and consumer demands, adhesive manufacturers have risen to the challenge, developing increasingly sophisticated solutions to meet the changing needs of automotive production.
Evolving Adhesive Technologies
In the years that followed, adhesive manufacturers rose to the occasion, driving a remarkable transformation in their products’ capabilities and applications. As the automotive industry continued to evolve, adhesives became increasingly integral to manufacturing, enabling new design possibilities and streamlining assembly techniques.
One of the most significant advancements was the rise of pressure-sensitive adhesive (PSA) tapes and films. These fast-applying adhesives found their way into various automotive applications, from self-healing protective films to double-sided foam seals and breathable label polymers.
The versatility and performance of these PSA solutions allowed them to gradually replace traditional mechanical fasteners, such as spot welding, screws, bolts, and rivets. Adhesive manufacturers also made strides in addressing the challenge of bonding dissimilar substrates. Developing specialized formulations and surface preparation techniques could create adhesives capable of reliably joining a wide range of materials, from metals and plastics to composites and engineered alloys.
Driving Efficiency and Innovation
As the automotive industry prioritized efficiency and productivity, adhesives emerged as a critical enabler. By streamlining assembly processes, improving structural integrity, and facilitating the use of lightweight materials, adhesives played a pivotal role in enhancing overall manufacturing efficiency.
Adhesive manufacturers responded to this demand by continuously innovating their products. They introduced adhesives with faster curing times, allowing for quicker assembly and reduced downtime. They also developed adhesives capable of withstanding extreme temperatures, harsh environmental conditions, and the unique stresses encountered in modern vehicle designs.
Furthermore, adhesive manufacturers began integrating advanced technologies into their products, such as sensor-enabled “smart” adhesives that monitor performance and enable proactive maintenance. The emergence of 3D printing also opened up new possibilities for customizing and fabricating adhesive structures tailored to specific automotive applications.
Sustainability and the Future
As the automotive industry prioritizes sustainability, adhesive manufacturers have also shifted their focus toward developing eco-friendly solutions. The rise of bio-based adhesives derived from renewable sources promises a more environmentally conscious alternative to traditional formulations.
Looking ahead, the future of automotive adhesive technology is poised for even more groundbreaking advancements. Continued research and development in intelligent adhesives, 3D printing, and sustainable chemistries will shape the next chapter of the automotive industry’s evolution. Adhesive manufacturers, once seen as silent partners in the automotive supply chain, have emerged as key drivers of innovation, efficiency, and sustainability.
As the industry continues to evolve, these industrial adhesive specialists will remain indispensable, helping to propel the automotive sector toward a future of safer, more efficient, and environmentally responsible vehicles.
What Are The Different Types Of Industrial Automotive Adhesives?
Based on the search results, the main types of industrial automotive adhesives include:
- Surface Protective Films: These adhesive-backed polyethylene sheets protect automotive surfaces during transportation and assembly.
- High Bondage Tapes: Very High-Bondage (VHB) acrylic foam tapes create powerful bonds for mounting parts and making connections, such as attaching vehicle badges or connecting mirror components.
- Automotive Gaskets and Sealing Adhesives: These adhesives create airtight seals around electronic components and visual elements like screens and consoles, preventing debris from getting underneath.
- Anaerobic Adhesives include thread lockers, thread sealants, retaining compounds, and gasket sealants used in various automotive assembly and sealing applications.
- Pressure-sensitive adhesives (PSAs): PSA tapes and films are used in a wide range of automotive applications, from protective films to foam seals, gradually replacing traditional mechanical fasteners.
- Hot Melt Adhesives include APAO and EVA-based hot melt adhesives for bonding automotive components like body panels, interior trim, and upholstery.
- Structural Adhesives: Liquid and tape structural adhesives, such as epoxy and acrylic formulations, bond primary automotive structures, replace welds and mechanical fasteners, and enable multi-material bonding.
The search results indicate that automotive adhesives must meet stringent requirements for strength, flexibility, chemical resistance, and temperature tolerance to perform effectively in the demanding automotive environment.
How Have Industrial Automotive Adhesives Evolved?
Industrial automotive adhesives have evolved significantly over time, driven by technological advancements, changing consumer demands, and the need for more efficient and sustainable manufacturing processes. Here’s a summary of their evolution:
Early Developments (Early 20th Century)
- Initially, adhesives were used primarily for bonding rubber shock mounts to metal parts in the automotive industry.
- By the 1920s, thermoplastic adhesives were developed, marking the beginning of a new era in adhesive technology.
Mid-20th Century
- The 1950s and 1960s saw the introduction of pressure-sensitive adhesives (PSAs), which revolutionized the industry by offering fast-applying, easy-to-use solutions for various applications.
- PSAs were initially used for temporary bonding but have since evolved to include self-healing protective films, double-sided foam seals, and breathable label polymers, among other applications.
Late 20th Century
- The 1990s and early 2000s witnessed a shift towards more advanced adhesive formulations, such as those designed for bonding dissimilar materials like urethane to aluminum or PVC to stainless steel.
- Environmental concerns, including volatile organic compounds (VOCs), recycling needs, and product life-cycle responsibility, began gaining significant market attention.
21st Century
- The early 2000s focused on developing adhesives that could effectively bond to low-surface-energy (LSE) substrates, which are common in modern vehicles.
- The use of adhesives accelerated, with a Center for Automotive Research white paper predicting that adhesives would soon overtake traditional joining processes like spot welding, screws, and rivets as the most significant percentage of bonds in a vehicle.
- By the mid-2010s, adhesives had become a critical component in the automotive industry, driving the development of safer, more efficient, and environmentally friendly cars.
Current Trends and Future Directions
- Today, industrial automotive adhesives continue to evolve, driven by global megatrends such as the need for lightweight and fuel-efficient vehicles, the rise of electric cars, and the increasing importance of sustainability.
- Manufacturers focus on developing adhesives that can withstand extreme temperatures, harsh environmental conditions, and the unique stresses of modern vehicle designs.
- The industry is also exploring new technologies like cure-on-demand and de-bond-on-demand, which offer enhanced performance and flexibility in various applications.
- As the industry continues to advance, industrial automotive adhesives are expected to play a pivotal role in shaping the future of vehicle manufacturing, enabling the development of safer, more efficient, and aesthetically pleasing vehicles.
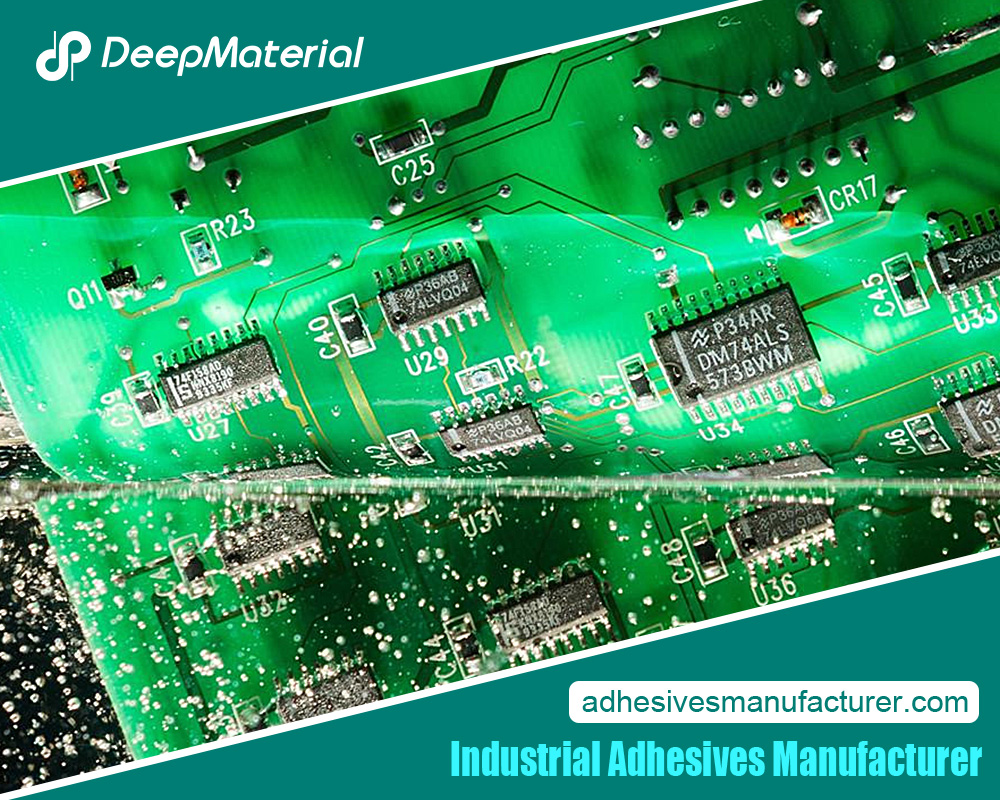
Conclusion: The Indispensable Role of Industrial Automotive Adhesives
The evolution of industrial automotive adhesives has been a remarkable journey, marked by continuous innovation and a relentless pursuit of solutions to meet the industry’s ever-changing demands. From the early days of rubber shock mounts to the sophisticated adhesive technologies of today, these unsung heroes of the manufacturing process have played a pivotal role in shaping the automotive landscape.
As the industry has evolved, driven by global megatrends and consumer preferences, adhesive manufacturers have risen to the challenge, developing increasingly sophisticated solutions to address the growing complexity of vehicle design and production.
The rise of pressure-sensitive adhesives, the ability to bond dissimilar materials, and the integration of advanced technologies have all contributed to adhesives’ indispensable role in the modern automotive ecosystem. The future of industrial automotive adhesives is poised for even more groundbreaking advancements. Continued research and development in intelligent adhesives, 3D printing, and sustainable chemistries will shape the next chapter of the industry’s evolution.
As the automotive sector continues to prioritize efficiency, innovation, and environmental responsibility, adhesive manufacturers will remain at the forefront, driving progress and enabling the creation of safer, more efficient, and aesthetically pleasing vehicles. In the ever-evolving world of automotive manufacturing, industrial adhesives have emerged as the unsung heroes, quietly yet profoundly shaping the industry’s trajectory. As the industry continues to push the boundaries of what’s possible, these adhesive specialists will remain indispensable, ensuring that the vehicles of tomorrow are not only technologically advanced but also environmentally conscious and built to last.
For more about the rise of industrial automotive adhesives, you can pay a visit to Deepmaterial at https://www.adhesivesmanufacturer.com/ for more info.