Surface Mount Adhesive
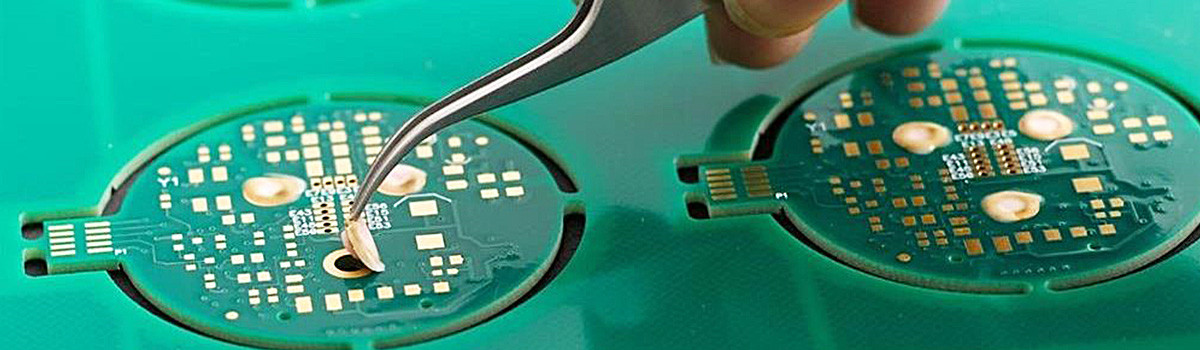
In the fast-paced realm of electronics manufacturing, achieving flawless connections and robust bonds is paramount. Surface mount adhesive, a groundbreaking innovation in electronic assembly, has transformed the way electronic components are affixed to circuit boards. By providing accurate, reliable, and efficient bonding solutions, surface mount adhesives have become a cornerstone of modern electronics production. This comprehensive exploration delves into the world of surface mount adhesives, uncovering their mechanisms, applications, advantages, and their integral role in shaping the electronics landscape.
Unveiling Surface Mount Adhesives
Surface Mount Adhesives (SMAs) play a pivotal role in the electronics manufacturing industry, facilitating the assembly of printed circuit boards (PCBs) and electronic components onto them. These adhesives have gained significant traction due to their ability to enhance manufacturing efficiency and provide robust mechanical and electrical connections. Here are some critical insights into the world of Surface Mount Adhesives:
- Versatile Application:SMAs find applications in various industries, including consumer electronics, automotive, aerospace, and telecommunications. People use them to attach components like resistors, capacitors, and integrated circuits onto PCBs.
- Types of Surface Mount Adhesives:There are two main types of SMAs: epoxy-based and acrylic-based. Epoxy-based adhesives offer excellent bonding strength and chemical resistance, making them suitable for demanding applications. Acrylic-based adhesives, on the other hand, provide flexibility and better thermal cycling performance.
- Dispensing Methods:SMAs can be applied using different dispensing methods, such as stencil printing, jetting, and screen printing. Each method has advantages and is chosen based on factors like adhesive viscosity, component size, and production volume.
- Curing Process:These adhesives typically undergo a curing process to achieve their full strength. You can accomplish curing through heat (thermal curing) or by exposing it to ultraviolet (UV) light (UV curing). Thermal curing is time-consuming, while UV curing offers rapid curing times and reduces energy consumption.
- Advantages:SMAs offer several benefits, including improved shock and vibration resistance, thermal conductivity, and electrical insulation. They also help reduce electronic devices’ size and enhance their performance.
- Challenges:Despite their benefits, using SMAs presents challenges such as achieving precise dispensing, managing curing times, and ensuring compatibility with different component materials. Manufacturers need to optimize these processes for consistent and reliable results.
- Environmental Considerations:With a growing emphasis on sustainability, eco-friendly formulations of SMAs are gaining prominence. Manufacturers are exploring options to reduce the environmental impact of these adhesives through recyclable and biodegradable materials.
Key Components and Formulation
The formulation of various products, whether in consumer goods, pharmaceuticals, or industrial materials, relies on a precise combination of critical components to achieve desired properties and functionalities. This intricate process involves carefully considering several factors to create products that meet specific requirements. Here are some essential insights into the key components and formulation process:
- Component Selection:The choice of components is pivotal and depends on the product’s intended purpose. For instance, cosmetic manufacturers carefully select ingredients like moisturizers, emollients, and active compounds to achieve desired skincare effects. In the food industry, professionals choose flavorings, preservatives, and nutritional additives to enhance taste, shelf life, and nutritional value.
- Synergistic Effects:Formulators need to consider how different components interact. People often seek synergistic effects, where features work together to enhance each other’s properties. In the pharmaceutical field, combining multiple active ingredients can improve therapeutic results.
- Balancing Properties:The formulation process requires a delicate balance of various properties, such as stability, viscosity, solubility, and shelf life. To achieve the desired balance, professionals often test different ratios and combinations of components to optimize the final product’s performance.
- Chemical Compatibility:Compatibility between components is crucial to avoid unwanted reactions leading to degradation or altered properties. For example, lubricants and additives must be chemically compatible in the automotive industry to ensure optimal engine performance.
- Manufacturability:Formulations must be conducive to the manufacturing process. Components should be easily mixed, blended, or processed into the desired product form, whether a tablet, cream, liquid, or powder.
- Regulatory Compliance:Formulators must adhere to regulations and safety standards specific to the industry. In pharmaceutical industries, thorough testing and documentation are necessary to guarantee product effectiveness and patient safety.
- Innovation and Customization:The formulation process is also a space for innovation and customization. As consumer preferences evolve, formulators adapt by incorporating novel components or modifying existing ones to create products that meet emerging demands.
- Quality Control:We implement rigorous quality control measures throughout the formulation process. Testing the raw materials, intermediate products, and final formulation is part of this process, ensuring consistency, stability, and compliance with specifications.
- Environmental Considerations:Environmental concerns have influenced the formulation process in recent years. Companies are integrating sustainable and eco-friendly components to reduce the ecological footprint of products.
Types of Surface Mount Adhesives
Surface Mount Adhesives (SMAs) come in various formulations, each tailored to specific manufacturing needs and performance requirements. These adhesive types are crucial in attaching electronic components to printed circuit boards (PCBs) efficiently and securely. Understanding the different kinds of SMAs is essential for optimizing assembly processes and achieving reliable connections. Here are the key types of Surface Mount Adhesives:
- Epoxy-Based Adhesives:Epoxy-based SMAs are known for their exceptional bonding strength and chemical resistance. Typical applications that demand robust connections, such as automotive electronics and aerospace systems, often use them. These adhesives offer excellent thermal and mechanical stability, making them ideal for components subjected to harsh environmental conditions.
- Acrylic-Based Adhesives:Acrylic-based SMAs provide flexibility and improved thermal cycling performance. They are suitable for applications where vibration and temperature fluctuations are significant factors. Preferably, people use acrylic adhesives to attach components that may undergo mechanical stress, as these adhesives maintain their adhesive properties over a wide temperature range.
- Silicone-Based Adhesives:Silicone-based SMAs offer excellent electrical insulation properties and high-temperature resistance. Such applications as LED lighting and power electronics, which require crucial heat dissipation, frequently use them. Silicone adhesives provide reliable adhesion while minimizing the risk of damaging sensitive components due to their soft and compliant nature.
- UV-Curable Adhesives:UV-curable SMAs provide rapid curing times and energy efficiency. These adhesives solidify when exposed to ultraviolet light, reducing assembly time and energy consumption. In high-volume production settings and applications where precise control of curing times is essential, people commonly use them.
- Thermal Conductive Adhesives:Experts formulate these specialized SMAs to improve heat transfer between components and the PCB. They are handy for devices that generate significant heat, such as microprocessors and power amplifiers. Thermal conductive adhesives help dissipate heat efficiently, preventing thermal damage and extending the lifespan of electronic devices.
- Low-Temperature Curing Adhesives:For applications involving heat-sensitive components, low-temperature curing SMAs are employed. These adhesives solidify at lower temperatures, reducing the risk of thermal damage to delicate parts during assembly.
- Flexible and Conductive Adhesives:Flexible and conductive SMAs combine adhesive properties with electrical conductivity. They find use in applications like flexible circuits and wearable electronics, where the adhesive attaches components and serves as an electrical connection.
Role in Electronics Manufacturing
Surface Mount Adhesives (SMAs) play a pivotal role in the intricate process of electronics manufacturing, contributing to the efficient assembly of printed circuit boards (PCBs) and the reliable attachment of electronic components. These adhesives are vital components that enable the creation of advanced devices and systems that power our modern world. Here are the key ways in which SMAs contribute to electronics manufacturing:
- Precise Component Placement:SMAs facilitate the accurate placement of electronic components on PCBs. By securely adhering elements in their designated positions, these adhesives ensure that connections are consistent and aligned, minimizing the risk of misalignment or short circuits.
- Enhanced Bonding:One of the primary functions of SMAs is to provide robust and reliable bonding between components and PCBs. This bonding is essential to ensure electrical connectivity and mechanical stability, even in demanding applications subject to vibrations, temperature changes, and other stressors.
- Miniaturization:There is a constant drive for smaller and more compact devices in the electronics industry. SMAs support this trend by enabling the attachment of tiny components with precision, allowing manufacturers to create increasingly miniaturized products without sacrificing performance.
- Improved Thermal Management:Certain SMAs, such as thermal conductive adhesives, contribute to effective thermal management within electronic devices. These adhesives help dissipate heat generated by components, preventing overheating and maintaining optimal device performance.
- High-Volume Production:In high-volume manufacturing environments, efficiency is paramount. SMAs that offer rapid curing, such as UV-curable adhesives, streamline the assembly process by reducing curing times and increasing production throughput.
- Diverse Applications:SMAs find applications in various industries, from consumer electronics to automotive, aerospace, medical devices, and telecommunications. Their versatility allows them to accommodate the specific requirements of each sector, contributing to the creation of diverse electronic products.
- Reduced Mechanical Stress: The flexibility and elasticity of certain SMAs, like acrylic-based adhesives, help absorb mechanical stress and prevent damage caused by movements, vibrations, and thermal expansions. This feature is precious in applications where durability is crucial.
- Environmental Considerations:As sustainability becomes a priority, eco-friendly formulations of SMAs are emerging. Manufacturers are exploring ways to reduce the environmental impact of electronics manufacturing by incorporating biodegradable and recyclable adhesive materials.
- Reliability and Longevity: The proper selection of SMAs and their correct application lead to long-lasting and reliable electronic devices. These adhesives ensure that components remain securely attached throughout the product’s lifecycle, minimizing the risk of malfunctions or failures.
Precise Component Placement
Precise Component Placement is a critical aspect of various industries, including electronics manufacturing, mechanical assembly, and construction. This process involves meticulously arranging individual parts, components, or elements in an organized manner to ensure optimal functionality, structural integrity, and efficient manufacturing. The precise component placement must be recognized, as it directly influences product performance, reliability, and aesthetics. Several key points highlight the significance of this practice:
- Quality and Performance:Accurate component placement is essential for maintaining the overall quality and performance of the final product. In electronics manufacturing, for instance, incorrect placement of microchips or connectors can lead to signal interference, reduced circuit efficiency, or even complete device failure. Similarly, improperly placed components in mechanical systems can result in reduced functionality or compromised structural integrity.
- Manufacturing Efficiency:Efficient component placement streamlines the assembly process, reducing the time and resources required for production. Arranging components logically can speed up assembly lines and minimize errors and rework. It is essential in industries that require high-volume production.
- Space Optimization:Precise component placement allows for optimal space utilization. In electronics design, for example, arranging components in a compact and organized manner helps minimize the size of the final product, making it more suitable for compact devices such as smartphones, wearables, and IoT devices.
- Heat Dissipation and Airflow:Effective component placement plays a role in heat dissipation and airflow management. In electronic devices, proper arrangement can facilitate the dissipation of heat generated during operation, preventing overheating and extending the lifespan of components.
- Aesthetic Considerations:Beyond functionality, component placement also affects the visual appeal of the end product. Well-organized and neatly placed components contribute to a polished and professional appearance, crucial in industries where aesthetics matter, such as consumer electronics.
- Testing and Maintenance:Carefully placed components simplify testing and maintenance procedures. Accessible and properly spaced elements allow easier troubleshooting, repair, and replacement, reducing downtime and associated costs.
- Reliability and Longevity:Precise placement contributes to a product’s overall reliability and longevity. Components situated correctly are less prone to wear and tear, vibration-induced damage, or unintended interactions with neighboring elements.
Eliminating Soldering Challenges
Eliminating soldering challenges is crucial in industries that rely on soldering processes for electronic assembly, metalwork, and various fabrication tasks. Soldering, the process of joining two metal components using molten filler material, presents several challenges impacting product quality, reliability, and efficiency. Addressing these challenges is essential for achieving consistent and high-quality soldered joints. Key points highlighting the importance of eliminating soldering difficulties include:
- Quality Assurance:Overcoming soldering challenges directly impacts the quality of soldered joints. Poor soldering can lead to weak connections, incomplete joints, or even electrical shorts, compromising the overall functionality of electronic circuits or mechanical assemblies.
- Reliability and Durability:Properly soldered joints are essential for products’ long-term reliability and durability. In applications like automotive electronics or aerospace components, where temperature fluctuations and vibrations are common, unreliable solder joints can result in frequent failures.
- Thermal Management:Efficient heat dissipation is crucial in many soldering processes. Ensuring proper soldering techniques and materials selection can prevent heat-related issues like overheating, which can damage components or affect overall performance.
- Miniaturization:With the trend towards smaller and more compact devices, soldering challenges have become more pronounced. As components and solder pads shrink, precise soldering techniques are required to avoid bridging, tombstoning, or insufficient solder fill.
- Automation and Efficiency:Eliminating soldering challenges often involves embracing automation. Automated soldering systems can enhance precision, consistency, and efficiency, reducing the risk of human errors and increasing production throughput.
- Materials Compatibility:Different materials require specific soldering techniques and materials. Overcoming challenges related to material compatibility ensures that solder joints adhere correctly and maintain their integrity over time.
- Environmental Considerations:Traditional soldering methods can involve lead-based solder, which raises environmental concerns. Transitioning to lead-free soldering processes helps meet environmental regulations and ensures safer products.
- Training and Skill Development:Properly trained personnel are essential to overcoming soldering challenges. Providing training and skill development opportunities ensures that technicians and operators are well-equipped to handle complex soldering tasks effectively.
- Process Control and Monitoring:Implementing robust process control and monitoring mechanisms can help identify and address soldering challenges in real time. This proactive approach minimizes defects and reduces the need for rework.
- Cost Efficiency:Efficient soldering processes translate to cost savings. Minimizing defects and rework reduces material waste, labor costs, and the risk of recalls, ultimately contributing to improved bottom-line results.
Compatibility with SMD Components
Ensuring compatibility with Surface Mount Device (SMD) components is paramount when designing electronic circuits or PCB layouts. SMD components have revolutionized the electronics industry with compact size, improved performance, and automated assembly capabilities. To ensure seamless compatibility with SMD components, you must consider several key factors:
1.Footprint Design:The footprint, or land pattern, of an SMD component on the PCB, plays a pivotal role in compatibility. It is crucial to precisely match the component’s recommended footprint dimensions and pad layouts specified in its datasheet. Deviations from these specifications could lead to soldering issues, misalignment during assembly, or compromised electrical connections.
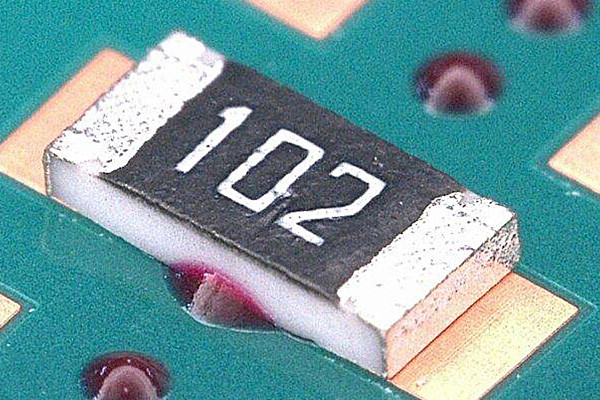
2.Pad Design and Placement:Proper pad design and placement are critical for soldering reliability. The pads’ shape, size, and spacing must accommodate the specific SMD package type (e.g., SOIC, QFN, 0201 resistors) to ensure optimal solder joint formation during reflow soldering. The pads’ orientation and alignment must also align with automated pick-and-place machines’ capabilities.
3.Solder Stencil Design:SMD components are typically soldered using a solder paste stencil during assembly. The stencil design, which includes openings corresponding to the component pads, should be precisely aligned with the pad layout. It’s essential to have adequate aperture sizes in the stencil to ensure the right amount of solder paste application and prevent solder bridges or insufficient soldering.
4.Thermal Considerations:SMD components can generate heat during operation. Proper thermal management is necessary to prevent overheating, which could degrade performance or lead to premature component failure. Adequate spacing between components, appropriate copper traces for heat dissipation, and the selection of suitable soldering materials contribute to effective thermal management.
5.Component Handling and Placement:SMD components are delicate and susceptible to electrostatic discharge (ESD) damage. You must take proper ESD precautions during component handling, storage, and assembly to prevent potential damage. Calibrate automated pick-and-place machines to ensure precise component placement, thus minimizing the risk of misalignment or damage.
6.Design for Manufacturability (DFM):Considering manufacturability early in the design process can enhance compatibility with SMD components. Collaborating with manufacturers and assembly houses can provide insights into their capabilities and constraints, guiding design choices that optimize the assembly process and reduce production costs.
7.Testing and Inspection:After assembly, thorough testing and inspection are essential to verify the compatibility of SMD components. Automated optical inspection (AOI) and X-ray inspection can detect soldering defects, misalignment, or other issues affecting the circuit’s functionality or reliability.
Thermal Conductivity Considerations
Thermal conductivity considerations are pivotal in various fields, influencing diverse systems and materials’ design, efficiency, and functionality. One must understand how heat transfers through different mediums to optimize energy usage, prevent overheating, and promote thermal management. Key points to consider in thermal conductivity include:
- Definition and Importance:Thermal conductivity refers to a material’s ability to conduct heat. It’s a fundamental property that impacts heat transfer in applications ranging from electronics cooling to building insulation. Materials with high thermal conductivity efficiently dissipate heat, while those with low thermal conductivity act as insulators, retaining heat.
- Factors Affecting Thermal Conductivity:Several factors influence thermal conductivity. Crystal structure, density, and atomic arrangement impact a material’s ability to transmit heat. Additionally, temperature and impurities can alter thermal conductivity. For instance, metals generally have higher thermal conductivity due to their close-packed atomic structure, while gases exhibit lower conductivity due to the more significant gaps between molecules.
- Anisotropy:Some materials exhibit anisotropic thermal conductivity, meaning their heat transfer properties vary with direction. This phenomenon is common in crystals and layered fabrics. For instance, graphite conducts heat better along its layers than perpendicular to them. When designing materials for specific applications, one must consider anisotropy.
- Applications in Engineering:Thermal conductivity considerations are crucial in engineering designs. In electronics, efficient heat dissipation prevents devices from overheating, extending their lifespan and enhancing performance. Similarly, in the automotive and aerospace industries, understanding thermal conductivity aids in developing materials that withstand extreme temperatures while ensuring safety and reliability.
- Insulation Materials:Materials with low thermal conductivity are essential for insulation. They are used in buildings to minimize heat loss during winter and prevent excessive heat gain in summer. Examples include fiberglass, foam, and aerogels. Selecting the suitable insulating material involves balancing factors like thermal resistance, cost, and environmental impact.
- Thermal Interface Materials (TIMs):Individuals use TIMs to enhance heat transfer between two surfaces, such as a microprocessor and a heat sink. These materials fill microscopic irregularities between characters, reducing thermal resistance. Greases, pads, and phase-change materials are common TIMs with distinct thermal conductivity properties.
- Nanotechnology Impact:Advances in nanotechnology have introduced new materials with remarkable thermal properties. Carbon nanotubes and graphene exhibit exceptionally high thermal conductivity, making them promising candidates for efficient heat dissipation applications.
High-Speed and High-Volume Assembly
High-speed and high-volume assembly processes represent a crucial frontier in modern manufacturing, streamlining production lines and enhancing efficiency across various industries. These advanced assembly techniques stand out for their rapid pace and ability to handle large quantities of components or products precisely. Key features and considerations include:
- Automation at Scale:High-speed and high-volume assembly rely heavily on automation for consistent and rapid production. Automated systems, such as robotic arms and conveyor belts, facilitate the seamless movement of components through different stages of assembly.
- Precision Engineering:Maintaining accuracy and precision at high speeds is a significant challenge. Innovative technologies like computer vision systems and advanced sensors ensure each component is correctly positioned and assembled with minimal error.
- Customization Potential:Despite the focus on speed and volume, modern assembly processes are becoming more adaptable to customization. Flexible manufacturing systems can swiftly switch between different product configurations, catering to varying customer demands without sacrificing efficiency.
- Lean Principles:Incorporating lean manufacturing principles into high-speed, high-volume assembly enhances resource utilization and waste reduction. By minimizing downtime, optimizing workflows, and reducing unnecessary steps, these processes remain efficient even during intense production runs.
- Material Handling Solutions:Efficient material handling is critical to high-volume assembly. Implementing strategies such as just-in-time delivery and automated material replenishment ensures a continuous flow of components to the assembly line, preventing bottlenecks.
- Quality Control Integration:Maintaining quality standards is imperative. Integrating quality control measures within the assembly process, including real-time inspections, testing, and data analysis, ensures early identification of defects and prevents downstream issues.
- Training and Maintenance:Skilled technicians must set up, operate, and maintain high-speed assembly systems. Comprehensive training programs and ongoing maintenance schedules are essential to ensure consistent and reliable operation.
- Advanced Robotics:Robotics technology has revolutionized high-speed assembly, enabling precise and swift manipulation of components. Collaborative robots, or cobots, work alongside human operators, enhancing efficiency and flexibility.
- Optimized Workflow Design:Designing an efficient workflow is crucial. Conducting thorough time and motion studies helps identify opportunities for optimizing and rearranging assembly stations, reducing unnecessary movements and delays.
- Scalability: Designers create high-speed and high-volume assembly processes with scalability in mind. As production demands increase, companies can expand these systems by adding more stations, robots, and resources, ensuring a smooth transition to higher production levels.
Dispensing Techniques and Equipment
Dispensing techniques and equipment play a pivotal role in diverse industries, enabling precise and controlled application of liquids, adhesives, coatings, and other materials. These technologies have evolved significantly, offering enhanced accuracy, efficiency, and customization. Key aspects of dispensing techniques and the equipment involved include:
Overview of Dispensing Techniques
Dispensing techniques encompass a range of methods for accurately depositing liquids and materials onto surfaces. These techniques cater to various viscosities, materials, and application requirements. Some standard methods include:
- Jetting:High-velocity liquid streams suitable for high-speed, high-volume applications.
- Needle Dispensing:Controlled release through a fine needle, ideal for intricate patterns.
- Syringe Dispensing: Precise delivery using a syringe-based system, suitable for small-scale applications.
- Time-Pressure Dispensing:Consistent dispensing by controlling material pressure and time duration.
- Positive Displacement:Accurate dispensing of materials with varying viscosities using a piston or screw mechanism.
Advanced Equipment and Technologies
Modern dispensing equipment integrates advanced technologies to optimize accuracy and efficiency. Key features include:
- Precision Valves:Automated valves with microprocessor control for precise flow control and drop sizes.
- Augmented Reality (AR) Guidance: AR systems overlay digital information on the operator’s view, aiding accurate material placement.
- Automated Robotic Systems:Robotic arms equipped with dispensing tools for complex patterns and hard-to-reach areas.
- Progressive Cavity Pumps:Ideal for high-viscosity materials, providing continuous flow and consistent dispensing.
- Multi-Component Dispensing: Simultaneous dispensing of multiple materials, enabling quick and accurate mixing in situ.
Industry Applications
Dispensing techniques find application across diverse industries, contributing to product quality and production efficiency:
- Electronics Manufacturing: Precise application of adhesives, solder pastes, and encapsulants onto circuit boards.
- Automotive Industry: Sealing, bonding, and gaskets in assembly processes, ensuring durability and safety.
- Medical Device Production:Accurate dispensing of biomaterials for implantable devices and drug delivery systems.
- Packaging:Controlled application of adhesives for sealing, labeling, and packaging integrity.
- Aerospace: Coating application for corrosion protection, thermal management, and aerodynamics.
Customization and Flexibility
Dispensing equipment’s adaptability is crucial in meeting diverse production demands:
- Programmable Settings:Equipment can be programmed for specific patterns, volumes, and speeds, accommodating various product designs.
- Quick Changeovers: Tool-free changeovers and adjustments enable rapid shifts between dispensing tasks.
- Material Compatibility: Versatility to handle a wide range of materials, from low-viscosity liquids to high-viscosity pastes.
Quality Assurance and Optimization
Dispensing equipment incorporates features to ensure consistent quality and operational efficiency:
- Vision Systems: Integrated cameras for real-time monitoring and alignment verification.
- Closed-Loop Feedback: Sensors provide feedback to the system, maintaining precise control over material deposition.
- Process Monitoring: Data analytics enable process optimization through material usage and performance insights.
Non-Conductive vs. Conductive Adhesives
Regarding adhesive selection, the distinction between non-conductive and conductive adhesives holds significant implications for various industries. Each type of adhesive serves a distinct purpose based on its electrical conductivity properties, making it crucial to understand their differences for optimal application and performance.
Non-Conductive Adhesives
- Insulation Function:Formulators create non-conductive adhesives to prevent the flow of electrical current between bonded components, effectively insulating them from each other. This property is significant in electronics to prevent short circuits and interference.
- Dielectric Strength:These adhesives exhibit high dielectric strength, allowing them to resist voltage without experiencing an electrical breakdown. This characteristic is essential for maintaining insulation integrity in applications involving sensitive electronics.
- Typical Applications:Non-conductive adhesives find use in bonding components such as touchscreens, sensors, and other electronics where electrical insulation is essential.
- Thermal Conductivity:Generally, non-conductive adhesives have lower thermal conductivity, which can be beneficial when heat dissipation is not a primary concern.
Conductive Adhesives
- Electrical Conductivity:Formulators create conductive adhesives to facilitate the flow of electrical current, enabling electrical connections between bonded components without traditional soldering or welding.
- Low Resistance:These adhesives exhibit low electrical resistance, ensuring efficient current flow and reliable electrical connections.
- Typical Applications:Conductive adhesives are widely used in flexible electronics, printed circuit boards (PCBs), RFID tags, and electronic packaging, offering an alternative to soldering in delicate or heat-sensitive situations.
- Thermal Conductivity:Some conductive adhesives also feature respectable thermal conductivity, aiding heat dissipation in electronic assemblies and enhancing system reliability.
- Balancing Act:Conductive adhesives’ electrical and thermal properties require careful balancing. While electrical conductivity is essential, high thermal conductivity might lead to uneven heat distribution.
Choosing the Right Adhesive
- Application Criteria: The choice between non-conductive and conductive adhesives hinges on application-specific requirements. Factors such as electrical conductivity, insulation needs, thermal management, and environmental conditions guide the decision.
- Material Compatibility:Compatibility between the adhesive and bonded materials is crucial for establishing a solid and durable bond. The adhesive’s mechanical properties, curing process, and chemical resistance must also align with the application’s demands.
- Design Flexibility:Adhesive selection can influence design and manufacturing processes. One should consider aspects like ease of application, curing methods, and the potential for rework or repair.
- Thorough Testing:Rigorous testing and validation ensure that the chosen adhesive meets performance standards. Electrical, mechanical, and thermal tests verify the adhesive’s suitability for the intended application.
Temperature and Environmental Resilience
In material performance, the concepts of temperature and environmental resilience hold paramount importance, particularly in aerospace, automotive, and electronics. The ability of materials to withstand extreme temperatures and challenging environmental conditions can determine the success and longevity of various products.
Temperature Resilience
1.High-Temperature Stability:Materials with temperature resilience can maintain their structural integrity and functionality even under elevated temperatures. This property is vital for components in engines, furnaces, and other high-heat environments.

2.Low-Temperature Flexibility:On the other end of the spectrum, materials must remain flexible and functional in icy conditions. Materials used in aerospace applications must withstand extreme temperatures during re-entry and in outer space.
3.Thermal Expansion:The ability of materials to handle thermal expansion and contraction without warping or cracking is essential in preventing mechanical failures caused by temperature fluctuations.
Environmental Resilience
- Moisture and Humidity:Resilience to moisture and humidity is critical to prevent degradation, corrosion, and mold growth. Materials used in outdoor applications or contact with water must resist water absorption and maintain structural integrity.
- Chemical Resistance:In environments with chemical exposure, materials must resist degradation, swelling, or loss of mechanical properties. It is especially crucial in fields like chemical processing and manufacturing.
- UV and Radiation Resistance:Materials used in outdoor applications or near radiation sources must withstand the damaging effects of UV radiation and ionizing radiation, which can cause degradation and discoloration.
Challenges and Solutions
- Material Selection:Engineers must carefully choose materials based on their intended operating environment. Professionals often select polymers, ceramics, composites, and specialized coatings for their temperature and environmental resilience properties.
- Testing and Validation:Rigorous testing is essential to ensure that materials meet the required temperature and environmental performance standards. We use accelerated aging tests, thermal cycling tests, and exposure to extreme conditions to assess resilience.
- Innovations:Advances in material science continually push the boundaries of temperature and environmental resilience. Nanotechnology, advanced coatings, and novel material formulations enhance performance in challenging conditions.
Real-World Applications
- Aerospace:Spacecraft components must withstand space’s vacuum, extreme temperature variations, and radiation exposure.
- Automotive:Engine components must endure high temperatures, while underbody parts face exposure to moisture, road salt, and chemicals.
- Electronics:Electronic devices must function reliably across various temperatures and resist the effects of moisture and humidity.
- Infrastructure:Materials used in bridges, buildings, and pipelines must withstand temperature changes and environmental factors to ensure long-term structural integrity.
Miniaturization and Microelectronics
The relentless march of technology has brought about remarkable achievements in various fields, and one of the most profound among them is miniaturization and microelectronics. This phenomenon is characterized by shrinking electronic components and devices to incredibly tiny sizes, leading to many revolutionary applications across industries.
The Driving Force
This transformation’s heart is the constant pursuit of greater efficiency, performance, and functionality. Miniaturization allows for the creation of devices that are not only more compact but also more powerful than their larger counterparts. Advancements in materials, manufacturing techniques, and design principles have allowed this to become a reality.
Key Benefits and Implications
Miniaturization and microelectronics have had far-reaching implications for various sectors:
- Consumer Electronics:The rise of smartphones, tablets, and wearables exemplifies how miniaturization has enabled devices to become pocket-sized while offering enhanced computing capabilities and connectivity.
- Medical Devices:Implantable medical devices, such as pacemakers and insulin pumps, have become more comfortable and convenient for patients due to their miniaturized nature. Additionally, miniature sensors enable real-time monitoring and data collection, revolutionizing healthcare.
- Aerospace and Defense:The aerospace industry benefits from lighter and more efficient electronics, which improves fuel efficiency and aircraft performance. In defense applications, miniaturized components enable advanced surveillance and communication systems development.
- Manufacturing and Automation:Microelectronics are crucial in precision manufacturing and automation, enabling robots and machines to perform intricate tasks accurately. The outcome of this has been an increase in productivity and better quality in various industries.
- IoT (Internet of Things): The proliferation of IoT devices, ranging from smart thermostats to industrial sensors, is mainly due to miniaturized electronics. These devices can collect and transmit data, leading to more intelligent decision-making and efficient systems.
Challenges and Future Prospects
While miniaturization offers numerous benefits, it also presents challenges:
- Heat Dissipation:Packing more components into smaller spaces can lead to increased heat generation, requiring innovative cooling solutions.
- Manufacturing Precision:Miniaturized components demand high levels of manufacturing precision, increasing production complexity.
- Reliability:Smaller components might be more susceptible to environmental factors and wear, potentially impacting device reliability.
Sustainability in Electronics Bonding
Electronics bonding, a crucial process in manufacturing electronic devices, involves joining components using various techniques. In recent years, the electronics industry has witnessed a growing emphasis on sustainability due to environmental concerns and the depletion of resources. This focus has extended to electronic bonding methods, driving the development of more eco-friendly and efficient bonding practices.
Challenges and Environmental Impact
- Traditional Bonding Techniques:Conventional bonding techniques often involve using hazardous chemicals, high energy consumption, and generating substantial electronic waste, contributing to environmental pollution.
- Resource Depletion:The materials used in bonding, such as adhesives and substrates, can contribute to resource depletion and generate significant carbon emissions during manufacturing.
- E-Waste Concerns:Inefficient bonding processes can lead to the premature failure of devices, resulting in higher rates of electronic waste generation. E-waste contains toxic elements that pose environmental and health risks.
Sustainable Bonding Approaches
- Lead-Free Soldering:Lead-free soldering has gained prominence due to eliminating toxic lead content. It reduces the harmful impact on workers’ health and the environment.
- Low-Temperature Bonding:Developing bonding techniques that require lower temperatures reduces energy consumption and minimizes thermal stress on components, prolonging their lifespan.
- Recyclable Materials:Using recyclable and biodegradable materials in bonding, such as eco-friendly adhesives and substrates, reduces the environmental footprint of electronic devices.
- Energy-Efficient Processes:Innovative technologies like plasma and laser bonding offer energy-efficient alternatives to traditional methods, lowering greenhouse gas emissions.
Advantages of Sustainable Electronics Bonding
- Reduced Environmental Footprint:Embracing sustainable bonding practices helps minimize hazardous waste, conserving natural resources and reducing pollution.
- Extended Device Lifespan:Sustainable bonding methods enhance the reliability and longevity of electronic devices, reducing the need for frequent replacements and conserving resources in the long run.
- Regulatory Compliance:Adhering to sustainable bonding standards ensures compliance with evolving environmental regulations, avoiding potential legal and financial penalties.
- Positive Brand Image:Electronics manufacturers adopting sustainable bonding showcase their commitment to environmental stewardship, appealing to eco-conscious consumers and investors.
Adhesive Inspection and Quality Control
Adhesive bonding plays a critical role in various industries, ensuring the integrity and performance of assembled products. To maintain high-quality standards and prevent defects, adhesive inspection, and quality control processes are essential. These processes involve thorough assessment, testing, and verification of adhesive application to ensure proper bonding and adherence.
Importance of Adhesive Quality Control
- Product Reliability:Properly bonded adhesives are vital for the structural integrity, reliability, and longevity of assembled products, from electronics to automotive components.
- Safety:In aerospace and medical devices industries, inadequate adhesive bonding can compromise security, making stringent quality control indispensable.
- Cost Efficiency:Early detection of adhesive defects through quality control minimizes production downtime and reduces the costs associated with rework or product recalls.
Adhesive Inspection Techniques
- Visual Inspection:The most straightforward inspection involves visually assessing the adhesive application, looking for issues like uneven coverage, voids, or foreign particles.
- Ultrasonic Testing:This non-destructive technique uses high-frequency sound waves to detect internal flaws, such as delamination or incomplete bonding.
- Shear and Peel Tests:These mechanical tests measure the adhesive’s strength and bonding properties, evaluating its performance under stress.
- X-ray and CT Scans:These techniques provide a cross-sectional view of adhesive bonds, revealing hidden defects or inconsistencies.
Quality Control Protocols
- Sampling Plans:Establishing statistically significant sampling plans helps ensure representative testing across production batches.
- Standardization:Adhering to industry standards and specifications for adhesive application and testing maintains consistency and quality.
- Process Monitoring: Continuous monitoring of adhesive application parameters during production helps identify deviations early on.
- Root Cause Analysis:When we identify defects, we thoroughly analyze the underlying causes and guide corrective actions.
Advantages of Effective Adhesive Inspection
- Consistency:Quality control ensures uniform adhesive application, reducing bond strength and performance variations.
- Early Defect Detection:Detecting defects in early production stages prevents downstream issues, reducing wastage and rework.
- Enhanced Product Performance:Reliable adhesion achieved through stringent inspection contributes to product durability and overall performance.
- Customer Satisfaction:High-quality products from practical adhesive inspection enhance customer trust and satisfaction.
Collaboration with Design Engineers
Effective collaboration between software developers and design engineers is pivotal in creating successful, user-friendly products. This partnership blends developers’ technical expertise with designers’ creative insights, ensuring that products are functional, visually appealing, and intuitive. By fostering a cohesive working relationship, both teams can leverage their unique skills to streamline product development and achieve optimal results. Here’s a closer look at how collaboration between software developers and design engineers contributes to successful outcomes:
Shared Vision and Understanding
- Establishing a shared vision helps align developers and design engineers on the project’s goals, target audience, and core features.
- Regular communication and brainstorming sessions promote a better understanding of each other’s perspectives and constraints.
Efficient Problem Solving
- Design engineers bring a user-centered approach, identifying potential pain points and proposing creative solutions that developers can implement seamlessly.
- Developers contribute technical insights, suggesting feasible methods to bring design concepts to life within the constraints of the chosen technology stack.
Iterative Design and Development
- Collaborative iterations enable rapid prototyping, refining the user interface/experience (UI/UX) and the underlying codebase.
- Feedback loops between developers and design engineers allow continuous improvement throughout the development lifecycle.
Seamless Integration of Functionality and Aesthetics
- Design engineers ensure that user interface elements are visually appealing and intuitively functional, enhancing the overall user experience.
- Developers work closely to integrate these design elements into the software architecture, ensuring that the final product meets aesthetic and functional requirements.
Optimized User Experience
- Collaboration among team members leads to the developing of user-centric products, ultimately enhancing user satisfaction and engagement.
- Usability testing and user feedback collection benefit from both teams’ insights, leading to refined products that address user needs effectively.
Addressing Technical Constraints
- Developers offer insights into technical feasibility and potential limitations during the design phase, preventing unrealistic design ideas.
- Close collaboration facilitates finding creative solutions to technical challenges while maintaining design integrity.
Timely Delivery and Quality
- Collaboration prevents bottlenecks by anticipating potential roadblocks and addressing them collectively, contributing to timely project delivery.
The combined efforts of design engineers and developers lead to a high-quality end product that aligns with design aspirations and technical requirements.
Industry Standards and Regulations
In various sectors, adhering to industry standards and regulations is paramount to ensure product and service safety, quality, and reliability. These standards provide a framework that guides organizations in maintaining consistency, interoperability, and compliance with legal requirements. A thorough understanding and integration of industry standards and regulations have several key implications for businesses:
Quality Assurance and Reliability
- Industry standards outline best practices and quality benchmarks, contributing to creating products and services that meet or exceed customer expectations.
- Adherence to these standards enhances reliability, reducing the likelihood of defects and improving overall product performance.
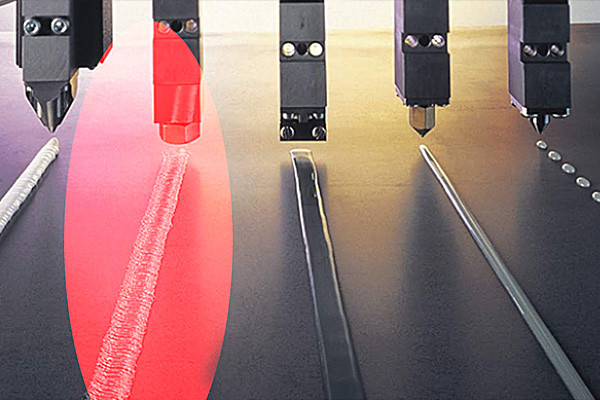
Interoperability and Compatibility
- Standards promote interoperability by ensuring that products and systems can work seamlessly together, fostering an environment of integration and compatibility.
- Incorporating new technologies and partnering with other organizations becomes effortless with this feature.
Risk Mitigation and Safety
- Compliance with regulations minimizes risks associated with safety, health, and the environment, safeguarding consumers and employees.
- Organizations that often prioritize safety build stronger reputations and gain consumer trust.
Global Market Access
- Many international markets require adherence to specific standards, and compliance can simplify market entry and expansion into new regions.
- Conforming to globally recognized standards can streamline regulatory approvals and reduce entry barriers.
Innovation and Efficiency
- While regulations set minimum requirements, they can also drive innovation as companies strive to differentiate themselves while staying compliant.
- Innovation can lead to more efficient processes, reduced costs, and improved customer experiences.
Legal Compliance and Liability
- Non-compliance with industry regulations can result in legal consequences, fines, or even product recalls, impacting a company’s finances and reputation.
- Demonstrating adherence to standards can serve as a defense against legal actions.
Customer Trust and Reputation
- Complying with industry standards and regulations enhances a company’s credibility and reputation, demonstrating a commitment to quality and responsibility.
- Trustworthy organizations are more likely to retain existing customers and attract new ones.
Continuous Improvement
- Regularly reviewing and updating standards and regulations ensures businesses stay current with evolving technologies, practices, and customer expectations.
- This process encourages a culture of continuous improvement and adaptability.
Advancements in Adhesive Technologies
Recent years have witnessed remarkable advancements in adhesive technologies, revolutionizing manufacturing and healthcare industries. These innovations have significantly improved adhesive materials’ bonding strength, versatility, and durability, offering numerous benefits across various applications.
Nanotechnology Enhancements
- Nanoadhesives infused with nanoparticles exhibit enhanced bonding properties and improved resistance to environmental factors.
- Nanotechnology enables precise control over adhesive properties, making them suitable for diverse substrates and challenging conditions.
Smart and Self-Healing Adhesives
- Innovative adhesives respond to external stimuli like temperature, light, or pH, allowing for controlled adhesion and detachment.
- Self-healing adhesives can recover their integrity after damage, extending product lifespans and reducing maintenance needs.
Biodegradable and Sustainable Adhesives
- Adhesive formulations derived from natural sources, like plant-based polymers and proteins, are environmentally friendly and biodegradable.
- These sustainable options address concerns about waste and pollution, aligning with eco-conscious consumer demands.
High-Performance Bonding in Extreme Environments
- Adhesive technologies offer robust performance in extreme temperatures, high humidity, and corrosive environments.
- These advancements are crucial in aerospace, automotive, and industrial applications where reliability under harsh conditions is paramount.
Enhanced Medical Adhesives
- Medical-grade adhesives are designed for biocompatibility, enabling non-invasive wound closure and improved surgical procedures.
- Flexible and biodegradable medical adhesives contribute to faster healing and reduced scarring.
Multi-Material Bonding Solutions
- Adhesives can now bond various dissimilar materials, reducing the need for traditional mechanical fasteners and expanding design possibilities.
- This versatility improves structural integrity and aesthetics in industries such as electronics and construction.
Adhesives for Electronics Miniaturization
- Miniaturization in electronics requires adhesive solutions that offer strong bonding and efficient heat dissipation.
- Adhesive technologies cater to delicate electronic components, enabling slim designs without compromising performance.
Advanced Application Techniques
- Adhesive application methods, such as 3D printing and sprayable adhesives, provide precision and consistency in bonding.
- These techniques streamline production processes and allow for intricate designs.
Aerospace and Defense Innovations
- Aerospace manufacturers benefit from lightweight adhesives that maintain structural integrity, reducing weight and enhancing fuel efficiency.
- Advanced adhesive solutions also contribute to stealth technology in defense applications.
Reduced Environmental Impact
- Low-VOC (Volatile Organic Compound) adhesives and solvent-free formulations minimize harmful emissions during application.
- These environmentally conscious solutions align with regulations and sustainability goals.
Challenges and Mitigation Strategies
In today’s dynamic world, various challenges arise across different sectors, from technology to healthcare. Implementing effective mitigation strategies is essential for progress and growth. This article delves into some common challenges and their corresponding mitigation strategies.
Technological Disruptions: Embracing Change for Competitive Advantage
The rapid pace of technological advancements often poses challenges to businesses and industries. To stay ahead, companies must embrace innovation and adapt their operations. Regular training and upskilling of employees, fostering a culture of innovation, and collaborating with tech experts can enable businesses to not only navigate technological disruptions but also leverage them for a competitive edge.
Data Security and Privacy: Safeguarding Information in a Digital Age
With the increasing reliance on digital platforms, ensuring data security and privacy has become paramount. Frequent cyberattacks and data breaches can have severe consequences. Organizations must invest in robust cybersecurity measures, conduct regular audits, and educate employees about best practices. Encryption, multi-factor authentication, and continuous monitoring effectively protect sensitive information.
Environmental Sustainability: Balancing Growth and Conservation
As environmental concerns escalate, industries face the challenge of achieving growth while minimizing their ecological footprint. Implementing sustainable practices, such as reducing carbon emissions, optimizing resource usage, and adopting circular economy models, can help mitigate these challenges. Collaboration with environmental experts and integrating sustainability into corporate strategies is essential for long-term success.
Fostering Innovation through Varied Perspectives
Creating an inclusive and diverse work environment remains a challenge across sectors. A lack of representation can limit creativity and innovation. Mitigating this challenge requires proactive efforts, including unbiased hiring practices, diversity training, and fostering a culture of respect. Encouraging open dialogue and embracing diverse perspectives can lead to enriched problem-solving and more effective decision-making.
Global Health Crises: Strengthening Healthcare Infrastructure for Resilience
The ongoing COVID-19 pandemic highlighted the vulnerabilities of healthcare systems worldwide. Preparedness for health crises requires robust healthcare infrastructure, investment in medical research, and effective crisis management protocols. Collaborative efforts between governments, healthcare organizations, and international bodies are essential to ensure timely responses and mitigate the impact of future health emergencies.
Future Outlook for Surface Mount Adhesives
Surface Mount Adhesives (SMAs) play a crucial role in the electronics manufacturing industry, facilitating the assembly of components onto circuit boards. As technology advances, SMAs are evolving to meet new demands. Let’s explore the future outlook for SMAs, including emerging trends and innovations.
Enhanced Conductivity and Performance
- The demand for high-performance electronics drives the need for SMAs with improved conductivity.
- Researchers are developing innovative formulations to ensure reliable connections in high-frequency applications.
- Nanotechnology-infused adhesives promise better electrical and thermal conductivity.
Miniaturization and High-Density Packaging
- The trend towards smaller, more compact devices necessitates SMAs that can adhere to tiny components in densely packed areas.
- Researchers are researching nano adhesives to provide strong bonds without compromising on space.
Compatibility with Diverse Substrates
- The electronics industry employs a wide range of materials. Future SMAs must adhere well to various substrates, including traditional ones and novel materials like flexible and organic ones.
- Researchers are exploring cross-compatible adhesives to reduce production complexities.
Environmentally Friendly Formulations
- As sustainability gains prominence, there’s a push for eco-friendly SMAs that reduce environmental impact.
- Bio-based adhesives and those with reduced volatile organic compounds (VOCs) are gaining attention.
Advanced Dispensing Techniques
- Automation and robotics are becoming more prevalent in electronics assembly.
- SMAs designed for precise and automated dispensing are increasing, improving production efficiency.
Thermal Management Solutions
- With electronics becoming more powerful, effective heat dissipation is vital.
- Researchers are developing SMAs with improved thermal conductivity to prevent overheating.
IoT and Wearables Compatibility
- The Internet of Things (IoT) and wearable technology markets are expanding rapidly.
- SMAs are adapting to cater to the specific needs of these sectors, such as flexibility and durability.
Industry 4.0 Integration
- Industry 4.0 emphasizes interconnected and intelligent manufacturing processes.
- Researchers are exploring innovative adhesives with embedded sensors for quality control and real-time monitoring.
Adapting to Harsh Environments
- Companies are increasingly deploying electronics in challenging environments.
- SMAs that can withstand extreme temperatures, moisture, and vibrations are crucial for sectors like aerospace and automotive.
Collaboration and Research
- The future of SMAs relies on collaboration between adhesive manufacturers, electronics companies, and research institutions.
- Ongoing research will drive innovation and address emerging challenges.
Surface mount adhesive has emerged as a game-changer in the electronics manufacturing landscape, streamlining processes, enhancing reliability, and enabling the creation of ever-smaller and more intricate electronic devices. Its ability to offer precision bonding, thermal management, and a higher degree of design flexibility has made it indispensable for industries racing to keep pace with technological innovation. As electronics continue to evolve, surface mount adhesives will remain at the forefront of enabling groundbreaking products, bridging the gap between functionality and miniaturization. With ongoing advancements in adhesive formulation and application techniques, the role of surface mount adhesive in shaping the future of electronics assembly is undeniably pivotal.