Structural Bonding Adhesive
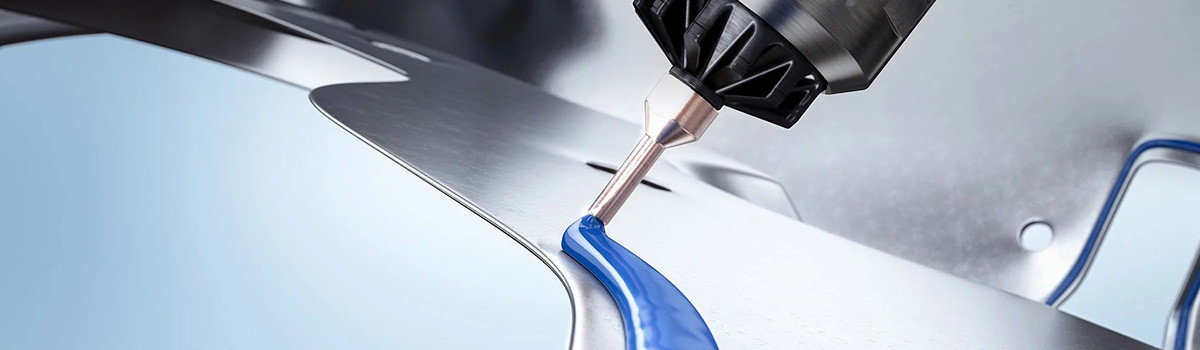
Structural bonding adhesive has emerged as a paramount element in modern engineering and manufacturing in creating robust and reliable connections. Unlike traditional mechanical fasteners that rely on physical interlocking, structural bonding adhesive forms a cohesive bond between materials, distributing stress evenly across surfaces. This adhesive innovation is pivotal in various industries, including aerospace, automotive, construction, and electronics, where the demand for lightweight yet durable solutions is ever-present.
The critical attribute of structural bonding adhesive is its ability to create connections that are not only strong but also stress-resistant. This adhesive promotes enhanced durability and longevity in assembled components by evenly distributing loads and eliminating stress concentration points. Moreover, its flexible nature accommodates various material combinations, allowing for bonding dissimilar substrates that might be challenging with conventional methods. This adaptability opens up new possibilities for innovative designs and improved industry performance.
Beyond its mechanical advantages, structural bonding adhesive offers aesthetic benefits as well. The absence of visible fasteners lends a sleek and streamlined appearance to products, making it particularly valuable in industries where design and aesthetics are crucial, such as consumer electronics and automotive manufacturing. As technology advances and materials diversify, structural bonding adhesive continues to evolve, playing a pivotal role in shaping the future of engineering by enabling secure, efficient, and visually appealing connections in various applications.
What is Structural Bonding Adhesive?
Structural bonding adhesive is an adhesive or glue specifically designed to create strong and durable bonds between various materials, typically used in construction, manufacturing, and engineering applications. Unlike standard adhesives that might be used for simple tasks like sticking paper together, structural bonding adhesives are engineered to provide high strength and long-lasting connections between different substrates, such as metals, plastics, composites, glass, and more.
Structural bonding adhesives offer several advantages over traditional mechanical fastening methods, such as welding, riveting, or bolting:
Uniform Stress Distribution: Adhesives distribute stress evenly across the bonded surfaces, reducing the likelihood of localized stress concentrations that can lead to material failure.
Weight Reduction: Adhesives can eliminate the need for heavy fasteners, leading to weight savings in applications like the aerospace and automotive industries.
Improved Aesthetics: Adhesives can create seamless, clean, and aesthetically pleasing bonds, particularly in applications where appearance matters.
Corrosion Prevention: Adhesives can prevent galvanic corrosion that might occur when dissimilar metals are fastened together.
Vibration Damping: Adhesives can absorb vibrations and reduce noise levels, making them suitable for applications where vibration control is essential.
Flexibility: Adhesives can allow flexibility and movement between joined materials and benefit applications subject to thermal expansion, contraction, or other dynamic forces.
Different types of structural bonding adhesives are available, including epoxy adhesives, polyurethane adhesives, acrylic adhesives, and more. The choice of adhesive depends on factors such as the bonded materials, the intended application, the required strength, temperature resistance, and environmental conditions.
It’s important to note that proper surface preparation, adhesive selection, and application techniques are crucial for achieving reliable and long-lasting bonds with structural bonding adhesives. In critical applications, thorough testing and validation of the adhesive’s performance under different conditions are typically conducted to ensure safety and reliability.
When Was Structural Bonding Adhesive First Developed?
Structural bonding adhesives have been in development and use for several decades. The exact date of the first development can take time to pinpoint due to the gradual evolution of adhesive technologies over time.
One of the earliest significant developments in structural bonding adhesives was the introduction of epoxy adhesives in the mid-20th century. Epoxy adhesives gained prominence due to their excellent bonding properties, durability, and resistance to various environmental factors. These adhesives were used in the aerospace, automotive, and construction industries.
In the 1950s and 1960s, aerospace and aviation industries began exploring adhesives for joining structural components. Aircraft manufacturers started using adhesives to bond metal and composite parts, reducing the need for traditional mechanical fasteners like rivets. This marked a significant step in adopting structural bonding adhesives for critical applications.
Since then, the development of structural bonding adhesives has continued, with ongoing improvements in formulations, performance characteristics, and applications across various industries. As a result, structural adhesives have become an integral part of modern manufacturing, allowing for lighter and more efficient designs while maintaining strong and durable bonds.
Where is Structural Bonding Adhesive Commonly Used?
Structural bonding adhesives have been in development and use for several decades. The exact date of the first development can take time to pinpoint due to the gradual evolution of adhesive technologies over time.
One of the earliest significant developments in structural bonding adhesives was the introduction of epoxy adhesives in the mid-20th century. Epoxy adhesives gained prominence due to their excellent bonding properties, durability, and resistance to various environmental factors. These adhesives were used in the aerospace, automotive, and construction industries.
In the 1950s and 1960s, aerospace and aviation industries began exploring adhesives for joining structural components. Aircraft manufacturers started using adhesives to bond metal and composite parts, reducing the need for traditional mechanical fasteners like rivets. This marked a significant step in adopting structural bonding adhesives for critical applications.
Since then, the development of structural bonding adhesives has continued, with ongoing improvements in formulations, performance characteristics, and applications across various industries. As a result, structural adhesives have become an integral part of modern manufacturing, allowing for lighter and more efficient designs while maintaining strong and durable bonds.
How Does Structural Bonding Adhesive Differ from Traditional Fasteners?
Structural bonding adhesives and traditional fasteners are two different methods for joining materials in various applications. They each have advantages and disadvantages based on the specific requirements of a project. Here’s a breakdown of the critical differences between structural bonding adhesives and traditional fasteners:
- Joining Mechanism:
- Structural Bonding Adhesives:These adhesives are designed to create a robust molecular bond between the surfaces of the joined materials. They use chemical reactions to form this bond, creating a cohesive and continuous connection.
- Traditional Fasteners:Fasteners, such as screws, bolts, nuts, and rivets, physically interlock materials by penetrating and securing them together. The connection is mechanical and relies on friction and the mechanical properties of the fastener.
- Distribution of Stress:
- Structural Bonding Adhesives:Adhesively bonded joints distribute stress evenly across the bonded area. This can lead to more uniform load distribution and potentially higher load-bearing capacity than fasteners’ localized stress concentrations.
- Traditional Fasteners:Fasteners create stress concentrations around the points where they are located. This can lead to weaknesses at those points and require careful design consideration to prevent failure under load.
- Weight and Aesthetics:
- Structural Bonding Adhesives:Adhesives can produce a lighter overall weight since they often don’t require bulky fasteners. They can also provide a cleaner and more streamlined appearance as they are not visible on the exterior surface.
- Traditional Fasteners:Fasteners can add weight due to the physical presence of the hardware. They can also create visible holes or protrusions on the surface, affecting aesthetics.
- Materials Compatibility:
- Structural Bonding Adhesives:Adhesives can bond a wide range of materials, including dissimilar materials, such as metals, to plastics, and create a seal against environmental factors like moisture, chemicals, and gases.
- Traditional Fasteners:Fasteners are often limited by the types of materials they can effectively join, and they might need to be more suitable for joining dissimilar materials. Additionally, fastener holes can compromise the integrity of a sealed enclosure.
- Vibration Damping and Noise Reduction:
- Structural Bonding Adhesives:Adhesively bonded joints can provide better vibration damping and noise reduction due to the flexible nature of the adhesive bond.
- Traditional Fasteners:Fasteners may transmit vibrations and contribute to noise due to their rigid connection.
- Installation and Labor:
- Structural Bonding Adhesives:Applying adhesives might require specific equipment, proper surface preparation, and curing time. However, they can streamline the assembly process by eliminating the need for drilling, aligning, and tightening fasteners.
- Traditional Fasteners:Fasteners often require more manual labor for drilling, aligning, and tightening, but they can offer quicker immediate assembly.
Ultimately, the choice between structural bonding adhesives and traditional fasteners depends on factors such as the materials being joined, load requirements, environmental conditions, production processes, and the desired overall performance of the assembled components. Both methods have advantages and disadvantages, and engineers and designers should carefully evaluate the specific needs of their projects before making a decision.
What Types of Materials Can Structural Bonding Adhesive Bond Effectively?
Structural bonding adhesives are designed to provide robust and durable bonds between various materials, often used in industrial applications where traditional mechanical fastening methods might not be feasible or desirable. These adhesives are engineered to offer excellent adhesion and cohesion properties, allowing them to bond to a wide range of materials effectively. Some of the materials that structural bonding adhesives can bond effectively include:
- Metals: Structural bonding adhesives can bond different metals, including steel, aluminum, stainless steel, copper, and more. They are commonly used in the automotive, aerospace, and construction industries.
- Composites: Adhesives can bond composite materials like carbon fiber-reinforced polymers (CFRP) and glass fiber-reinforced polymers (GFRP). These materials are often found in aerospace, sports equipment, and automotive components.
- Plastics: Structural adhesives can bond with various plastics, including ABS, polycarbonate, polyethylene, and polypropylene. They are used in applications ranging from electronics to automotive components.
- Wood: Adhesives can bond timber and wood-based materials, making them suitable for woodworking, furniture production, and construction.
- Ceramics: Structural bonding adhesives can bond ceramic materials, such as porcelain, ceramic tiles, and ceramic components used in electronics.
- Glass: These adhesives can bond glass to glass or glass to other materials, useful in applications like glass furniture, architectural glass assemblies, and electronics.
- Rubber and Elastomers: Adhesives can bond rubber and elastomeric materials, which is essential in industries like automotive manufacturing, where rubber components must be securely attached.
- Concrete and Masonry: Structural bonding adhesives are sometimes used in construction to bond concrete and masonry materials, offering an alternative to traditional methods like bolts or screws.
- Fabrics and Textiles: Adhesives can bond materials and textiles, enabling the production of clothing, bags, and various textile-based products.
It’s important to note that the effectiveness of a structural bonding adhesive depends on factors such as the specific adhesive formulation, surface preparation, environmental conditions (temperature, humidity, etc.), and the specific materials being bonded. Proper surface preparation and adhesive selection are crucial to achieving robust and reliable bonds. It’s advisable to consult adhesive manufacturers’ guidelines and conduct thorough testing before using any adhesive for critical applications.
When Does Cure Time Play a Role in Structural Bonding Applications?
Cure time is crucial in structural bonding applications that involve joining materials using adhesives, resins, or other bonding agents. The cure time refers to the duration required for the bonding material to solidify and develop its intended mechanical properties fully. Here are some scenarios where cure time is essential in structural bonding applications:
- Load-Bearing Capacity: The bonded joint is often subjected to mechanical loads and stresses in structural bonding. The adhesive or bonding agent needs sufficient cure time for maximum strength and load-bearing capacity. Applying loads or stresses before fully cured bonding material can lead to premature failure or reduced structural integrity.
- Durability and Longevity: Adequate curing is essential to ensure the long-term durability and stability of the bonded joint. An adequately cured bond can resist environmental factors such as temperature fluctuations, moisture, and chemical exposure without degrading over time. Prematurely assembled or used structures may experience degradation due to incomplete curing.
- Dimensional Stability: Some bonding materials undergo a degree of shrinkage during curing. Waiting for the material to cure fully helps prevent dimensional changes that could affect the alignment or fit of the bonded parts. Curing also reduces the risk of stress concentrations from differential shrinkage.
- Chemical Compatibility: Certain bonding agents may require a specific cure time to react with the substrate materials fully. In cases where the bonding material chemically interacts with the substrates, more curing time might lead to complete chemical reactions, resulting in solid bonds or compromised adhesion.
- Temperature and Environmental Conditions: Cure time can be influenced by temperature and humidity. Manufacturers often specify recommended curing conditions to ensure optimal bond development. Deviating from these conditions can prolong or accelerate cure time, potentially affecting bond strength and performance.
- Assembly and Handling Time: For complex structures or assemblies, having a defined cure time provides a window for aligning and positioning parts before the bonding material sets. This is especially important when working with materials with a short open time (when the adhesive remains workable after mixing or application).
- Quality Control and Testing: When manufacturing products that require consistent bond quality, it’s essential to adhere to recommended cure times. Quality control procedures often involve testing bonded samples to ensure they meet specified strength and performance criteria, which can be directly related to the cure time.
Following the manufacturer’s guidelines for the specific bonding material is essential. Cure times can vary widely depending on the type of adhesive, substrate materials, environmental conditions, and desired properties of the bond. Failure to adhere to recommended cure times can compromise the bonded components’ structural integrity and performance.
Where Might Structural Bonding Adhesive Replace Rivets and Bolts?
Structural bonding adhesives have gained popularity in various industries as a viable alternative to traditional methods like rivets and bolts for joining materials. The decision to use structural bonding adhesives over rivets and bolts depends on the specific application and requirements. Here are some areas where structural bonding adhesives might replace rivets and bolts:
1.Aerospace and Aviation: Adhesives can reduce weight and increase fuel efficiency by eliminating the need for fasteners. They also distribute loads more evenly, reducing stress concentrations.
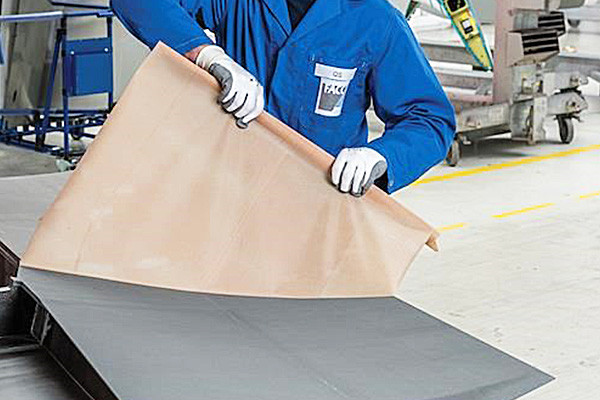
2.Automotive: Adhesives can be used in vehicle assembly to reduce weight, improve aerodynamics, and increase structural integrity. They also dampen vibrations and reduce noise.
3.Marine: Adhesives can help seal and join parts in marine environments, where corrosion from saltwater exposure can concern traditional fasteners.
4.Construction: In modern buildings, adhesives can bond materials like glass, metal, and composites, providing a more aesthetically pleasing and seamless appearance.
5.Electronics: Adhesives can replace mechanical fasteners in electronics assembly, improving thermal conductivity, shock resistance, and vibration damping.
6.Medical Devices: Adhesives can bond medical device components, ensuring they are securely joined while minimizing the risk of contamination from holes or gaps left by fasteners.
7.Renewable Energy: Adhesives assemble wind turbine blades and solar panels, providing strong bonds that withstand the stresses experienced in these applications.
8.Consumer Electronics: Thin and lightweight devices benefit from adhesives, providing a clean and seamless appearance while helping with thermal management.
9.Sporting Goods: Adhesives can manufacture high-performance sporting goods, such as carbon fiber bicycles, skis, and snowboards.
10.Rail and Transportation: Adhesives can provide high-strength, lightweight bonding solutions for railcar assembly, reducing the overall weight and improving fuel efficiency.
11.Military and Defense: Adhesives are used in defense applications where reducing the visibility of joints and increasing structural integrity are crucial.
12.General Manufacturing: Adhesives offer versatility in various manufacturing processes, enabling dissimilar materials to bond and reduce the need for holes and fasteners.
However, it’s important to note that the suitability of structural bonding adhesives depends on factors such as material compatibility, load-bearing requirements, environmental conditions, and the necessary bonding strength. While bonds offer numerous advantages, there are limitations, such as cure time, potential degradation over time, and challenges in disassembly or repair.
Each application requires careful consideration of these factors to determine whether structural bonding adhesives can effectively replace traditional methods like rivets and bolts. Following industry standards and guidelines for proper adhesive selection, preparation, and application is essential to ensure optimal results.
How Do Manufacturers Ensure Consistent Quality in Structural Bonding?
Manufacturers ensure consistent quality in structural bonding through rigorous processes, material selection, testing, and quality control measures. Structural bonding involves joining materials using adhesives, and maintaining uniformity and strength in these bonds is crucial to ensure the safety and reliability of the final products. Here’s how manufacturers achieve consistent quality in structural bonding:
- Material Selection: Manufacturers choose adhesives that are specifically designed for structural applications. These adhesives are formulated to provide high bond strength, durability, and resistance to various environmental factors such as temperature, humidity, and chemicals.
- Process Standardization: Manufacturers develop standardized bonding processes that outline the steps, procedures, and parameters for applying adhesives. These processes are carefully documented and followed to ensure consistency across production batches.
- Surface Preparation: Proper surface preparation is essential for achieving solid bonds. Manufacturers meticulously clean and treat the characters to be bonded to remove contaminants, oils, and oxides. This prepares the surfaces to maximize adhesive contact and bonding strength.
- Adhesive Application: Adhesives follow precise guidelines, such as recommended temperature, pressure, and curing time. Manufacturers may use automated equipment or manual techniques depending on the application and scale of production.
- Curing Conditions: Adhesives often require a curing process to achieve full strength. Manufacturers carefully control curing conditions, including temperature, humidity, and time, to ensure consistent bonding across different batches.
- Testing and Quality Control: Rigorous testing procedures are conducted to validate the strength and reliability of the bonded structures. These tests may include tension, compression, shear, and impact tests to assess the bond’s performance under various conditions. Manufacturers establish acceptance criteria based on industry standards or their internal benchmarks.
- In-Process Inspections: Manufacturers perform regular inspections to identify deviations or issues throughout the bonding process. This helps catch and correct problems early in the production cycle, reducing the likelihood of defects reaching the final product.
- Statistical Process Control (SPC): Manufacturers may use statistical techniques to monitor and control the quality of the bonding process. SPC involves collecting data from various stages of production, analyzing trends, and making adjustments as needed to maintain consistent quality.
- Employee Training: Proper training for operators and technicians is crucial to ensure the bonding process is carried out correctly. Employees should know the techniques, equipment, and safety measures to achieve optimal results.
- Documentation and Traceability: Each production batch is documented, including details about materials, process parameters, and testing results. This documentation provides traceability and allows manufacturers to investigate any quality issues.
- Feedback and Continuous Improvement: Manufacturers collect feedback from testing, inspections, and real-world performance to identify areas for improvement. This continuous improvement approach helps refine processes and maintain or enhance the quality of structural bonding over time.
By combining these measures, manufacturers can consistently produce high-quality products with robust and reliable structural bonds.
What Safety Precautions Are Necessary When Working with Structural Bonding Adhesive?
Working with structural bonding adhesives requires careful attention to safety precautions to ensure workers’ well-being and the bonded structures’ quality. Here are some essential safety precautions to follow:
- Personal Protective Equipment (PPE):
- Eye Protection:Wear safety goggles or a face shield to protect your eyes from potential splashes or fumes.
- Hand Protection:Wear chemical-resistant gloves to prevent direct contact with the adhesive.
- Respiratory Protection:Depending on the adhesive’s fumes and vapors, wear a respirator with appropriate cartridges to prevent inhalation of harmful chemicals.
- Ventilation:
- Work in a well-ventilated area or use local exhaust ventilation to remove fumes and maintain a safe working environment.
- Skin Protection:
- Wear long sleeves, pants, and closed-toe shoes to prevent skin contact with the adhesive.
- If the adhesive comes into contact with your skin, wash the affected area immediately with soap and water.
- Surface Preparation:
- Ensure that the surfaces to be bonded are clean, dry, and free from contaminants like oil, grease, dust, or rust. Proper surface preparation is crucial for the adhesive to create a strong bond.
- Read and Follow the Instructions:
- Carefully read and follow the manufacturer’s instructions and safety data sheet (SDS) for the adhesive. This includes information about the application, curing time, and safety precautions.
- Storage:
- Store adhesives in a cool, dry, well-ventilated area, away from heat sources, flames, and direct sunlight.
- Mixing and Application:
- If the adhesive requires mixing, follow the recommended ratios and procedures precisely.
- Apply the adhesive following the manufacturer’s guidelines, using appropriate tools.
- Emergency Preparedness:
- Have access to emergency eyewash stations, safety showers, and a first aid kit in case of accidental exposure.
- Fire Safety:
- Since some adhesives are flammable, avoid working near open flames, sparks, or ignition sources.
- Keep fire extinguishing equipment readily available in case of emergencies.
- Waste Disposal:
- Dispose of adhesive containers, mixing tools, and waste materials according to local regulations and guidelines.
- Training:
- Ensure that anyone working with structural bonding adhesives is adequately trained in safely handling and applying the products.
- Avoiding Contamination:
- Prevent cross-contamination of adhesives and ensure that mixing tools are clean and free from any residues from previous applications.
Remember that different adhesives may have specific safety requirements based on their chemical composition and intended applications. Always refer to the product’s SDS and follow the manufacturer’s recommendations for safe usage. Consult a knowledgeable supervisor or safety professional if you need clarification on any aspect of working with structural bonding adhesives.
When Did Structural Bonding Adhesive Gain Traction in the Aerospace Industry?
Structural bonding adhesives began to gain traction in the aerospace industry in the mid-20th century, primarily during the 1950s and 1960s. Developing and adopting these adhesives marked a significant advancement in aircraft manufacturing and design.
One of the notable events that contributed to the acceptance of structural bonding adhesives was the introduction of high-strength epoxy resins. These resins provided a reliable and efficient way to bond various materials, including metals and composite materials, with excellent durability and mechanical properties. The development of epoxy-based adhesives made it possible to join aircraft components in ways that were not feasible with traditional mechanical fasteners alone.
The aerospace industry’s interest in structural bonding adhesives grew as aircraft design evolved to incorporate lightweight materials and more complex shapes. Adhesives offered several advantages over conventional methods, including reduced weight, improved aerodynamics, and minimized stress concentrations, ultimately contributing to better fuel efficiency and overall performance.
One of the milestone moments in using structural bonding adhesives in aerospace was during the production of the Boeing 787 Dreamliner, which first flew in 2009. The Dreamliner featured more composite materials than previous aircraft models, and adhesives played a crucial role in bonding these lightweight materials. This highlighted the industry’s increasing reliance on adhesives for structural integrity.
Since then, the aerospace industry has continued exploring and refining structural bonding adhesives for various applications, including assembling aircraft components, attaching interior fittings, and even replacing traditional rivets and fasteners.
It’s worth noting that the timeline may vary depending on the specific type of adhesive, manufacturer, and aerospace company. Still, the broader trend of adopting structural bonding adhesives significantly influenced the industry from the mid-20th century onward.
Where Can Structural Bonding Adhesive Provide Enhanced Vibration Damping?
Structural bonding adhesives can provide enhanced vibration damping in various applications across different industries. Here are some common areas where structural bonding adhesives are used to provide vibration damping:
- Automotive Industry: Structural bonding adhesives are extensively used in the automotive industry to join different components, such as body panels, chassis parts, and interior elements. By creating a strong bond between these components, adhesives can help absorb and dampen vibrations, reducing noise and improving overall vehicle comfort.
- Aerospace Industry: Structural bonding adhesives are used to join lightweight materials and components in aerospace applications. They help dampen vibrations in aircraft structures, reducing vibration propagation through the aircraft’s body and features. This contributes to passenger comfort and ensures the structural integrity of the plane.
- Railway Industry: Like the automotive industry, structural bonding adhesives are used in the railway sector to bond and join various parts of train carriages and locomotives. By dampening vibrations, sealants can help reduce noise levels within the train and improve the overall ride quality for passengers.
- Electronics and Electronics Packaging: In electronics manufacturing, adhesive bonding is used to assemble and secure device components. Adhesives can help dampen vibrations that might be generated by moving parts or vibrations transmitted through the environment, improving electronic device performance and reliability.
- Construction Industry: Structural bonding adhesives can be used to bond various building materials together in the construction of buildings and structures. This can help reduce the transmission of vibrations caused by traffic, machinery, and external forces, resulting in a quieter and more comfortable indoor environment.
- Marine Applications: In marine environments, structural bonding adhesives join hulls, decks, and other components in boats and ships. These adhesives help dampen the vibrations caused by water turbulence and engine operation, contributing to a smoother ride and increased structural integrity.
- Renewable Energy: Structural bonding adhesives are used in the renewable energy sector, particularly in wind turbine manufacturing. They help bond components of turbine blades and tower structures, reducing vibrations caused by wind forces and mechanical operations.
- Industrial Machinery: Many industrial machines and equipment generate vibrations during operation. Structural bonding adhesives can be applied to join parts of these machines, reducing vibrations and minimizing noise levels in the surrounding environment.
- Medical Equipment: Structural bonding adhesives can be used to assemble medical devices and equipment in the medical field. These adhesives help dampen vibrations and reduce noise in sensitive medical equipment, contributing to better patient experiences.
Overall, structural bonding adhesives are crucial in enhancing vibration damping in various applications, contributing to improved performance, comfort, and longevity of multiple products and systems. The benefits and applications can vary based on the adhesive’s properties, the bonded materials, and the related assembly’s intended use.
How Does Structural Bonding Contribute to Design Flexibility in Products?
Structural bonding plays a significant role in enhancing design flexibility in various products. It involves using adhesive materials to join components rather than traditional mechanical fasteners like screws, bolts, or rivets. This bonding technique offers several benefits that contribute to design flexibility:
1.Versatile Material Compatibility:Structural bonding allows for bonding dissimilar materials that might be difficult to connect using traditional methods. This opens up opportunities for combining materials with complementary properties to achieve desired performance characteristics, weight savings, or aesthetic appeal.
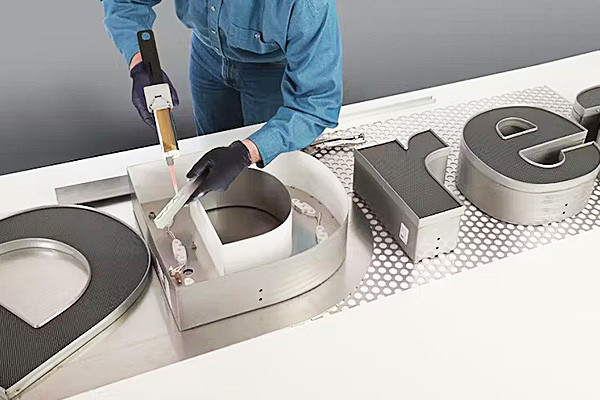
2.Reduced Weight:Adhesives are often lighter than mechanical fasteners, distributing loads evenly across the bonded surfaces. This can lead to weight reduction in products, which is especially crucial in aerospace, automotive, and consumer electronics industries.
3.Enhanced Aesthetics:Without the need for visible fasteners, structural bonding can result in a cleaner and more streamlined appearance, contributing to the overall aesthetic appeal of the product.
4.Stress Distribution:Adhesives distribute stresses more uniformly across the bonded area than localized stress concentrations at fastener points. This can improve the overall strength and durability of the product, especially under dynamic or cyclic loading conditions.
5.Improved Sealing and Water Resistance:Adhesives can create a continuous bond line that seals joints and prevents the ingress of moisture, dust, or other contaminants. This is particularly important for products intended for outdoor or harsh environments.
6.Vibration Damping:Adhesives can absorb and dampen vibrations, reducing product noise and vibration levels. This is especially valuable in applications where noise reduction is essential, such as the automotive and aerospace industries.
7.Complex Geometries:Adhesives can bond irregular and complex shapes more effectively than traditional fasteners. This allows designers to create innovative and intricate product designs that might not be feasible using conventional joining methods.
8.Improved Load Distribution:Adhesives can provide a larger contact area between bonded surfaces, leading to improved load distribution. This is particularly advantageous in products subjected to varying or fluctuating loads.
9.Stress Concentration Avoidance:Unlike mechanical fasteners, adhesives do not create stress concentration points that could weaken the material. This is especially relevant for materials prone to cracking or other forms of stress-related failure.
10.Reduced Assembly Time and Costs:Structural bonding can lead to quicker and simpler assembly processes since there’s no need for drilling holes, inserting fasteners, or aligning components precisely. This can result in reduced labor costs and increased production efficiency.
11.Increased Design Freedom:The absence of visible fasteners can give designers more creative freedom to develop unique and aesthetically pleasing products without being restricted by the placement and visibility of traditional pins.
Overall, structural bonding offers a range of benefits that enhance the design flexibility of products across various industries. It enables designers to think beyond the limitations of mechanical fasteners and explore innovative solutions for achieving improved performance, aesthetics, and functionality.
What Role Does Surface Preparation Play in Achieving Strong Bonds?
Surface preparation is crucial in achieving solid bonds in various applications, such as adhesive bonding, painting, coating, welding, and more. The quality and effectiveness of the bond between two materials often depend on how well the surfaces are prepared before joining or applying any coating. Here are some reasons why surface preparation is essential for achieving strong bonds:
- Cleanliness: Surfaces must be free from dirt, dust, oils, greases, and contaminants to ensure proper bonding. Even small amounts of pollutants can create barriers that prevent adhesives, coatings, or other bonding agents from directly contacting the substrate, leading to weak bonds.
- Adhesion: For adhesive bonding, the strength of the bond depends on the molecular interaction between the adhesive and the substrate. Proper surface preparation helps create a solid interlocking molecular connection between the two, enhancing adhesion.
- Coating Uniformity: In painting and coating applications, surface irregularities can lead to uneven coating thickness and reduced protection against corrosion or environmental factors. Adequately prepared surfaces provide a uniform substrate for coatings to adhere to, ensuring consistent security and appearance.
- Roughness: Creating controlled surface roughness through techniques like sanding, grit blasting, or etching increases the surface area available for bonding. This enhanced surface area allows bonding agents to interlock and create stronger bonds mechanically.
- Removal of Oxides and Scale: In welding, surfaces might have oxides, rust, or mill scale that hinder the fusion process. Proper surface preparation, which may involve cleaning, grinding, or pickling, removes these impurities, enabling the weld metal to bond effectively with the base metal.
- Microscopic Interlocking: Microscopic surface features, like pores, grooves, and irregularities, can interlock with bonding agents, enhancing the overall strength of the bond. These features are more effective when surfaces are adequately prepared.
- Surface Activation: Some materials require surface activation to make them more receptive to bonding agents. Techniques like plasma treatment or chemical activation can modify the surface properties and promote better adhesion.
- Durability: A well-prepared surface enhances the durability of the bond or coating by minimizing the potential for premature failure due to factors like peeling, delamination, or cracking.
- Corrosion Prevention: Properly prepared surfaces are less prone to corrosion since contaminants that could initiate corrosion processes are removed, ensuring a sound and lasting bond.
- Compatibility: In cases where materials with different properties are being bonded, surface preparation can help bridge the compatibility gap by creating an interface that enhances the bond between dissimilar materials.
Overall, surface preparation sets the foundation for achieving solid and durable bonds in various applications. It improves the intimate contact between the bonding agents and substrates, minimizes potential weak points, and ensures the reliability and longevity of the bonded system. Different bonding methods and materials might require specific surface preparation techniques, so following recommended procedures for each application is important.
When Is Structural Bonding Adhesive a More Economical Choice?
Surface preparation is crucial in achieving solid bonds in various applications, such as adhesive bonding, painting, coating, welding, and more. The quality and effectiveness of the bond between two materials often depend on how well the surfaces are prepared before joining or applying any coating. Here are some reasons why surface preparation is essential for achieving strong bonds:
- Cleanliness: Surfaces must be free from dirt, dust, oils, greases, and contaminants to ensure proper bonding. Even small amounts of pollutants can create barriers that prevent adhesives, coatings, or other bonding agents from directly contacting the substrate, leading to weak bonds.
- Adhesion: For adhesive bonding, the strength of the bond depends on the molecular interaction between the adhesive and the substrate. Proper surface preparation helps create a solid interlocking molecular connection between the two, enhancing adhesion.
- Coating Uniformity: In painting and coating applications, surface irregularities can lead to uneven coating thickness and reduced protection against corrosion or environmental factors. Adequately prepared surfaces provide a uniform substrate for coatings to adhere to, ensuring consistent security and appearance.
- Roughness: Creating controlled surface roughness through techniques like sanding, grit blasting, or etching increases the surface area available for bonding. This enhanced surface area allows bonding agents to interlock and create stronger bonds mechanically.
- Removal of Oxides and Scale: In welding, surfaces might have oxides, rust, or mill scale that hinder the fusion process. Proper surface preparation, which may involve cleaning, grinding, or pickling, removes these impurities, enabling the weld metal to bond effectively with the base metal.
- Microscopic Interlocking: Microscopic surface features, like pores, grooves, and irregularities, can interlock with bonding agents, enhancing the overall strength of the bond. These features are more effective when surfaces are adequately prepared.
- Surface Activation: Some materials require surface activation to make them more receptive to bonding agents. Techniques like plasma treatment or chemical activation can modify the surface properties and promote better adhesion.
- Durability: A well-prepared surface enhances the durability of the bond or coating by minimizing the potential for premature failure due to factors like peeling, delamination, or cracking.
- Corrosion Prevention: Properly prepared surfaces are less prone to corrosion since contaminants that could initiate corrosion processes are removed, ensuring a sound and lasting bond.
- Compatibility: In cases where materials with different properties are being bonded, surface preparation can help bridge the compatibility gap by creating an interface that enhances the bond between dissimilar materials.
Overall, surface preparation sets the foundation for achieving solid and durable bonds in various applications. It improves the intimate contact between the bonding agents and substrates, minimizes potential weak points, and ensures the reliability and longevity of the bonded system. Different bonding methods and materials might require specific surface preparation techniques, so following recommended procedures for each application is essential.
Where Might Harsh Environmental Conditions Impact the Performance of Adhesive Bonds?
Harsh environmental conditions can have a significant impact on the performance of adhesive bonds. Adhesive bonds are widely used in various industries to join materials, and their performance can be compromised when exposed to certain environmental factors. Here are some examples of harsh environmental conditions that can impact adhesive bonds:
- Temperature Extremes: Adhesive bonds can weaken or fail when exposed to extreme temperatures, either high or low. High temperatures can cause adhesives to soften, lose strength, and potentially melt, while low temperatures can make adhesives brittle, reducing their flexibility and strength.
- Moisture and Humidity: Moisture and humidity can lead to the degradation of adhesive bonds, especially for adhesives not designed to be water-resistant. Water can weaken the adhesive or cause the bonded surfaces to deteriorate, leading to reduced adhesion.
- UV Radiation: Ultraviolet (UV) radiation from sunlight can degrade the properties of many adhesives, leading to reduced bond strength and potential failure. UV radiation can break down the molecular structure of adhesives and weaken the bonds over time.
- Chemical Exposure: Adhesive bonds can be affected by exposure to various chemicals, solvents, and corrosive substances. Chemical interactions can lead to adhesive degradation, weakening of bonds, and loss of adhesion strength.
- Vibration and Mechanical Stress: Harsh mechanical conditions, such as constant vibration or repetitive loading, can cause adhesive bonds to fatigue and eventually fail. Vibrations can weaken the bond interface and lead to disbanding.
- Abrasion and Wear: Adhesive bonds in areas prone to abrasion and wear, such as moving parts, can experience deterioration due to friction and mechanical stress. The constant rubbing or scraping of bonded surfaces can lead to adhesive failure.
- Saltwater Exposure: Adhesive bonds exposed to saltwater environments can experience corrosion and degradation, mainly if the adhesive is not designed to withstand the corrosive effects of saltwater.
- Pressure Changes: Rapid changes in pressure, such as those experienced at high altitudes or in vacuum environments, can affect the performance of adhesive bonds. Pressure changes can lead to bubbling or separation of bonded surfaces.
- Biological and Biological Exposure: Adhesive bonds used in applications involving natural materials, such as medical devices or food processing equipment, can be affected by bacteria, enzymes, and other biological factors that might degrade the adhesive.
- Electromagnetic Interference: In specific applications, electromagnetic interference (EMI) or radio frequency interference (RFI) can affect adhesive bonds by inducing electrical currents that might weaken the bond or alter the adhesive’s properties.
To mitigate the impact of these harsh conditions on adhesive bonds, it’s crucial to choose adhesives specifically formulated to withstand the anticipated environmental factors. Conducting thorough testing and considering the intended application environment will help select the suitable adhesive for the job and ensure bonded structures’ durability and reliability.
How Does Research and Development Contribute to Advancements in Structural Bonding Adhesive Technology?
Research and Development (R&D) is crucial in driving structural bonding adhesive technology advancements. Structural bonding adhesives are essential in various industries, including automotive, aerospace, construction, and electronics. Here’s how R&D contributes to the rise of this technology:
- Material Science and Formulation: R&D efforts focus on developing new adhesive formulations with improved properties such as strength, durability, flexibility, and resistance to various environmental factors. Researchers work on designing adhesive materials at the molecular level to achieve specific characteristics, enhancing their performance in different applications.
- Improved Bonding Performance: R&D works optimizing adhesive chemistries to provide more robust and reliable bonds between different materials, such as metals, composites, plastics, and ceramics. This involves understanding the interactions between the adhesive and the bonded surfaces and tailoring adhesive properties accordingly.
- Enhanced Durability: The adhesives used in structural applications must withstand a wide range of conditions, from extreme temperatures to mechanical stresses and corrosive environments. R&D focuses on developing adhesives that exhibit improved durability, long-term stability, and resistance to degradation over time.
- Reduced Cure Times: Traditional adhesive curing processes can take time, limiting the efficiency of manufacturing processes. R&D aims to develop adhesives with faster curing times, enabling quicker production cycles and reducing manufacturing costs.
- Health and Safety: R&D efforts focus on developing safer adhesives with reduced volatile organic compounds (VOCs) and toxic emissions. This addresses both worker safety concerns and environmental regulations.
- Ease of Application: Adhesives must be user-friendly and easily applicable in various manufacturing processes. R&D seeks to develop easy adhesives to dispense, spread, and cure, ensuring consistent results across different manufacturing environments.
- Customization for Specific Applications: Different industries and applications require adhesives with unique properties. R&D works to customize adhesive formulations for specific uses, such as aerospace, automotive, electronics, or medical devices, ensuring optimal performance in each context.
- Adhesive-Substrate Compatibility: Adhesives must bond effectively with a wide variety of substrates. R&D focuses on understanding the interaction between adhesives and substrates to minimize issues such as adhesion failures, delamination, or weak bonds.
- Testing and Validation: R&D involves developing comprehensive testing methodologies to assess the performance of adhesives under various conditions. This includes mechanical testing, environmental exposure, and accelerated aging tests to ensure the adhesive’s reliability over its intended service life.
- Innovation and Breakthroughs: R&D encourages innovative thinking and exploration of new technologies, such as nanotechnology or bio-inspired adhesives, which can lead to revolutionary advancements in adhesive technology.
- Sustainability: With growing environmental concerns, R&D focuses on developing sustainable adhesive solutions, such as bio-based adhesives or recyclable adhesive systems, to reduce the ecological impact of bonding technologies.
In summary, R&D drives structural bonding adhesive technology advancements by continuously pushing the boundaries of material science, chemistry, engineering, and application methods. These advancements lead to more robust, more durable, efficient, and environmentally friendly adhesive solutions that significantly impact various industries and technologies.