SMT Epoxy Adhesive
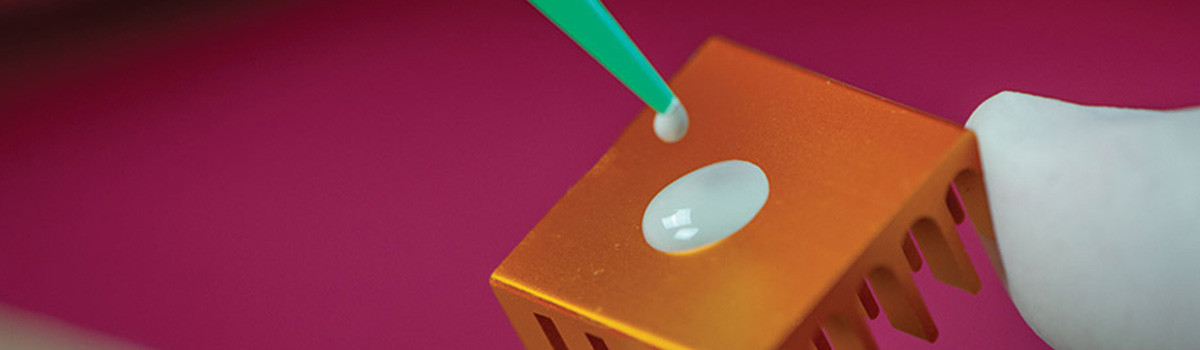
In the realm of electronics manufacturing, the evolution of Surface Mount Technology (SMT) has transformed the landscape of circuit assembly. SMT epoxy adhesives have emerged as a critical solution within this context, revolutionizing the way electronic components are attached to printed circuit boards (PCBs). By providing accurate, reliable, and efficient bonding, SMT epoxy adhesives enhance the mechanical integrity, thermal conductivity, and overall performance of electronic assemblies. This comprehensive exploration delves into the realm of SMT epoxy adhesives, unveiling their mechanisms, applications, advantages, and their integral role in shaping the SMT industry and modern electronics.
Understanding SMT Epoxy Adhesives
Understanding Surface Mount Technology (SMT) epoxy adhesives is crucial in electronics manufacturing, where miniaturization and reliability are paramount. SMT epoxy adhesives are specialized adhesives that attach surface mount components to PCBs, ensuring secure mechanical bonding, electrical conductivity, and protection against environmental factors. These adhesives play a pivotal role in modern electronics assembly processes, contributing to the durability and performance of a wide range of devices.
Key aspects to consider when delving into SMT epoxy adhesives include:
- Application Process:SMT epoxy adhesives are typically dispensed in precise amounts onto designated areas of the PCB using automated dispensing equipment. It is essential to be accurate and precise to avoid using too much adhesive and prevent potential operational problems.
- Dispensing Techniques:There are various dispensing techniques employed in applying SMT epoxy adhesives, such as jet dispensing, needle dispensing, and stencil printing. The choice of technique depends on factors like component size, assembly complexity, and production volume.
- Curing Process:After dispensing, SMT epoxy adhesives undergo a curing process. We use specific temperature profiles to change the adhesive from liquid to solid. We must carefully control the curing process to ensure proper adhesion and minimize thermal stress on components.
- Adhesive Properties:We formulate SMT epoxy adhesives to possess desirable properties, including good adhesion to various substrates, mechanical strength, thermal stability, and resistance to environmental conditions like moisture, chemicals, and temperature fluctuations.
- Component Bonding: SMT epoxy adhesives secure components to the PCB, preventing movement and detachment during operation. This mechanical bonding is essential for small, lightweight components susceptible to vibration or thermal expansion.
- Conductivity Considerations:While most SMT epoxy adhesives insulate, we design some formulations to provide electrical conductivity between components. These adhesives create a conductive path, eliminating the need for additional soldering of specific connections.
- Reliability and Longevity:The correct selection and application of SMT epoxy adhesives contribute to the long-term reliability of electronic devices. Properly bonded components ensure consistent electrical performance and reduce the risk of failures due to mechanical stress or environmental exposure.
Challenges in SMT Assembly
Surface Mount Technology (SMT) assembly has revolutionized electronic manufacturing by enabling the precise placement of components directly onto PCBs. However, this sophisticated assembly technique presents challenges, many of which we can effectively address through SMT epoxy adhesives. Let’s delve into the intricacies of SMT assembly challenges and how epoxy adhesives can provide solutions:
Miniaturization and Component Density
- SMT has led to the miniaturization of components, making precise placement challenging.
- The high component density can lead to issues with heat dissipation and signal interference.
Component Misalignment
- Accurate placement is crucial for proper functionality and soldering.
- Challenges arise due to variations in component size, shape, and tolerances.
Thermal Management
- Modern electronics generate significant heat, impacting component performance and reliability.
- Proper heat dissipation is essential to prevent overheating and ensure longevity.
Mechanical Stress
- During assembly and operation, vibration, shock, and mechanical stress can damage components.
- Components need secure adhesion to withstand these stresses.
Flux Residues and Cleaning
- The use of solder paste and flux can leave residues after assembly.
- Residue removal is critical to prevent electrical shorts and ensure optimal performance.
Adhesion Challenges
- Components with irregular shapes or challenging materials may require special adhesion techniques.
- Ensuring robust and reliable adhesion is essential for long-term functionality.
Environmental and Chemical Exposure
- Harsh environments, chemicals, and moisture often expose electronics.
- Protection against corrosion and degradation is vital for reliability.
High-Speed Signal Integrity
- High-frequency signals are susceptible to interference and degradation.
- Proper placement and securing of components are critical to maintaining signal integrity.
Production Efficiency
- SMT assembly demands precise processes to prevent defects and rework.
- Efficient adhesives can streamline the body, reduce errors, and enhance productivity.
SMT epoxy adhesives offer tailored solutions to these challenges
- Precision Adhesion:Epoxy adhesives provide precise and reliable adhesion for components of varying shapes and materials.
- Thermal Conductivity:Epoxy adhesives with enhanced thermal conductivity help manage heat effectively, preventing overheating.
- Mechanical Stability:These adhesives enhance the mechanical strength of components, protecting them from vibration and shock.
- Flux Residue Compatibility:We often formulate epoxy adhesives to be compatible with flux residues, reducing the necessity for extensive cleaning.
- Environmental Protection:Epoxy adhesives create a protective barrier against environmental factors, enhancing durability.
Mechanisms of Epoxy Adhesion in SMT
Surface Mount Technology (SMT) epoxy adhesives are vital components in electronics assembly, enabling the secure attachment of electronic elements to printed circuit boards (PCBs). The efficacy of these adhesives hinges on the intricate interplay of various mechanisms that combine to ensure robust and lasting connections.
Surface Preparation: Enhancing Cleanliness and Roughness
- Cleaning:Thorough cleaning of surfaces is a fundamental step, eliminating contaminants like oils, dust, and oxides that could compromise adhesion.
- Roughening Techniques:We microscopically roughen surfaces using plasma treatment and sandblasting methods. This process promotes mechanical interlocking and augments the adhesive’s contact area.
Mechanical Interlocking and Conformity
- Viscous Adaptability:The viscosity of epoxy facilitates its accommodation of surface irregularities on both components and PCBs, fostering mechanical interlocking.
- Fillers and Microspheres:Many epoxy formulations incorporate fillers that amplify adhesive contact points, intensifying mechanical interlocking and enhancing adhesion.
Chemical Bonding through Curing
- Chemical Cross-linking:During curing, epoxy molecules polymerize, establishing a network structure that bolsters cohesion and adhesion.
- Curing Initiation:Heat, UV light, or chemical catalysts trigger curing, dictated by the specific epoxy formulation.
- Covalent Bond Formation:The cured epoxy forges potent covalent bonds with the substrate, significantly augmenting adhesive strength.
Customized Epoxy Formulations
- Adhesion-Promoting Additives:Epoxy formulations often incorporate adhesion promoters, fostering chemical interactions with epoxy and substrate surfaces and enhancing mutual affinity.
- Modifiers for Mechanical Properties:We introduce modifiers to fine-tune attributes such as flexibility and thermal resistance, adapting the adhesive to meet diverse mechanical demands.
- Application-Centric Optimization:We precisely tailor epoxy formulations to suit distinct applications, ensuring optimized performance and durability.
The mechanisms driving epoxy adhesion in SMT assemblies encompass a complex blend of preparation, mechanical interlocking, and chemical bonding. These processes synergize to deliver dependable affixation of electronic components to PCBs. Ongoing advancements in formulation techniques and surface treatment methodologies continually refine these mechanisms, propelling the capabilities of adhesive technology and contributing to the evolution of electronics manufacturing.
Types of SMT Epoxy Adhesives
SMT (Surface Mount Technology) epoxy adhesives are crucial in modern electronics manufacturing processes. These adhesives play an essential role by bonding surface mount components to PCBs (Printed Circuit Boards), ensuring reliable connections and mechanical stability within the assembly. Several types of SMT epoxy adhesives are available, each designed to address specific requirements and challenges within the electronics industry.
Electrically Conductive Epoxy Adhesives
- These adhesives contain conductive fillers like silver, nickel, or copper.
- Used to create electrical pathways between components and the PCB.
- Ideal for applications requiring both adhesive bonding and electrical conductivity.
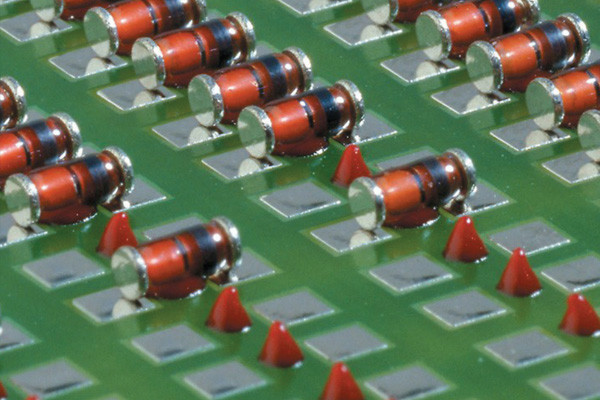
Non-Conductive Epoxy Adhesives
- We design them for bonding components without the risk of electrical short circuits.
- They find common use in applications where electrical isolation is essential.
- Provide strong mechanical bonding without compromising electrical integrity.
Thermal Conductive Epoxy Adhesives
- Its formulation efficiently transfers heat away from sensitive components.
- They find use in applications where heat dissipation is crucial for component performance and longevity.
- Find applications in LED assemblies, power electronics, and high-power RF devices.
Low Outgassing Epoxy Adhesives
- These adhesives release minimal volatile compounds during curing.
- Suitable for aerospace, vacuum, and high-reliability applications where outgassing could affect performance.
- Prevent contamination and maintain the integrity of sensitive environments.
Flexible Epoxy Adhesives
- We engineer it to withstand mechanical stress, vibration, and thermal cycling.
- They find use when components experience movement or varying environmental conditions.
- They commonly find applications in the automotive, aerospace, and consumer electronics industries.
High-Strength Epoxy Adhesives
- Provide exceptional bonding strength and durability.
- Suitable for applications where components may experience significant mechanical stress.
- They find use in critical areas such as automotive under-the-hood electronics.
Fast-Curing Epoxy Adhesives
- They are designed for rapid assembly processes, reducing production cycle times.
- Offer efficient bonding while maintaining required adhesive properties.
- They find common use in high-volume electronics manufacturing.
UV-Curable Epoxy Adhesives
- Cure upon exposure to UV light, enabling precise control over the curing process.
- Ideal for applications where quick curing and accurate placement are crucial.
- They find use in medical devices, optics, and microelectronics.
In electronics manufacturing, selecting the appropriate SMT epoxy adhesive depends on factors such as the desired electrical properties, thermal management needs, mechanical stress requirements, and production efficiency. Manufacturers must carefully assess their specific application demands to choose the most suitable epoxy adhesive type that ensures optimal electronic assemblies’ performance, reliability, and longevity.
Thermal Conductive SMT Epoxy Adhesives
Thermal management is a critical consideration in modern electronics design, as increasing power densities in devices can lead to overheating and reduced performance. Thermal Conductive Surface Mount Technology (SMT) Epoxy Adhesives have emerged as a crucial solution to address this challenge. These adhesives provide strong bonding for electronic components and offer efficient heat dissipation capabilities, making them indispensable in various industries such as automotive, telecommunications, and consumer electronics.
Key Features and Benefits
Thermal Conductive SMT Epoxy Adhesives offer several advantages that make them a preferred choice for electronics manufacturers:
- Heat Dissipation:These adhesives, such as ceramic or metal particles, are formulated with thermally conductive fillers that facilitate efficient heat transfer away from sensitive components.
- High Bond Strength:SMT epoxy adhesives ensure secure and reliable bonding between components and substrates, preventing detachment due to thermal expansion or mechanical stress.
- Electrical Insulation:In addition to heat conduction, these adhesives provide electrical insulation, preventing short circuits and maintaining signal integrity.
- Improved Reliability: By reducing operating temperatures, the adhesives enhance electronic devices’ overall reliability and lifespan.
- Design Flexibility: Their compatibility with automated SMT processes allows for precise application and is conducive to intricate electronic designs.
- Cost-Efficiency:Utilizing thermal conductive SMT epoxy adhesives eliminates the need for additional heat sinks or complex cooling systems, resulting in cost savings during production.
Applications
Thermal Conductive SMT Epoxy Adhesives find applications across a wide range of industries:
- Automotive:In the automotive sector, these adhesives bond power electronics in electric vehicles, control modules, and LED lighting systems while effectively managing heat generated during operation.
- Telecommunications:In the telecommunications industry, where networking equipment often operates in confined spaces, these adhesives ensure reliable bonding and heat dissipation in routers, switches, and base stations.
- Consumer Electronics:In smartphones, laptops, and tablets, these adhesives maintain the performance and longevity of delicate components like CPUs, GPUs, and memory chips.
- Industrial Electronics: In industrial settings, they play a role in power inverters, motor drives, and control panels, preventing downtime caused by overheating.
- Renewable Energy: Thermal conductive adhesives are also utilized in solar inverters and wind turbine control systems, ensuring consistent operation under varying conditions.
Low-Outgassing Epoxy Adhesives for Space Applications
Low-outgassing epoxy adhesives, often referred to as Surface Mount Technology (SMT) epoxy adhesives, have emerged as essential components for space applications due to their unique properties that address the challenges posed by the space environment. These advanced adhesives are crucial in securely bonding sensitive electronic components in spacecraft, satellites, and other aerospace equipment. The key features and benefits of low-outgassing epoxy adhesives for space applications include:
- Minimal Outgassing:One of the primary concerns in space applications is the release of volatile substances from materials, known as outgassing, which can contaminate sensitive instruments and optics. Low-outgassing epoxy adhesives are formulated to have minimal outgassing, reducing the risk of deposition on nearby surfaces and ensuring the longevity and performance of space equipment.
- High Thermal Stability:Extreme temperature variations characterize space environments, ranging from direct sunlight’s intense heat to shadowed areas’ frigid cold. Low-outgassing epoxy adhesives are engineered to exhibit high thermal stability, maintaining their adhesive strength and structural integrity across a wide temperature range.
- Excellent Adhesion:Ensuring secure and reliable bonding of components is essential to prevent malfunctions or damage during the mission. These epoxy adhesives offer excellent adhesion to various substrates, including metals, ceramics, and composites, enhancing the overall structural integrity of the spacecraft.
- Vibration and Shock Resistance:During launch and other mission phases, spacecraft experience intense vibrations and shocks. Low-outgassing epoxy adhesives are designed to absorb and dissipate mechanical stresses, safeguarding delicate electronics and components from potential damage.
- Radiation Resistance:Space is fraught with ionizing radiation, which can degrade materials over time. We engineer SMT epoxy adhesives to withstand the effects of ionizing radiation, preserving their mechanical and adhesive properties throughout the mission’s duration.
- Long-term Reliability:Space missions can extend over several years, and the reliability of materials is paramount. Low-outgassing epoxy adhesives undergo rigorous testing to ensure long-term performance and durability, minimizing the risk of adhesive failure during the mission.
High-Temperature SMT Bonding Solutions
High-temperature Surface Mount Technology (SMT) bonding solutions, often called SMT epoxy adhesives, are innovative materials designed to withstand extreme thermal conditions while maintaining reliable bonds in electronic assembly processes. These advanced adhesives play a crucial role in ensuring the longevity and performance of high-temperature electronic devices. Key features and advantages of these SMT epoxy adhesives include:
- Thermal Stability:We formulate high-temperature SMT bonding solutions to endure elevated temperatures, rendering them suitable for applications where heat stress might cause traditional adhesives to fail. They exhibit impressive thermal stability, ensuring the integrity of the bond even in demanding environments.
- Reliable Bonding:These adhesives offer exceptional adhesion to various substrates commonly found in electronics manufacturing, such as ceramics, metals, and polymers. This reliable bonding capability enhances the overall durability of electronic components.
- Resistance to Harsh Environments:We engineer high-temperature SMT epoxy adhesives to withstand high temperatures, harsh chemicals, moisture, and other environmental factors that can degrade conventional adhesives. This resistance contributes to the extended operational lifespan of electronic devices, even in challenging conditions.
- Thermal Conductivity:Some formulations of these adhesives possess excellent thermal conductivity properties. This feature is particularly advantageous in applications where efficient heat dissipation is essential for maintaining device performance and preventing overheating.
- Reduced Warping and Stress: One of the challenges in high-temperature electronics assembly is the potential for warping and stress due to differential expansion and contraction of materials. SMT epoxy adhesives with low coefficient of thermal expansion (CTE) help minimize these issues, improving overall mechanical stability.
- Process Compatibility:We design high-temperature SMT bonding solutions to integrate into existing assembly processes seamlessly. Automated equipment can dispense them, facilitating efficient production and minimizing the need for process adjustments.
Protection Against Vibration and Mechanical Stress
In electronics manufacturing, the delicate components on printed circuit boards (PCBs) are susceptible to damage from various external factors, with vibration and mechanical stress particularly concerning. Surface Mount Technology (SMT) epoxy adhesives have emerged as a vital solution to ensure the stability and longevity of electronic devices by providing adequate protection against these hazards.
Advantages of SMT Epoxy Adhesives
- Vibration Dampening:SMT epoxy adhesives offer exceptional vibration-dampening properties, absorbing and dissipating mechanical vibrations that could otherwise lead to component dislodgment or solder joint failure.
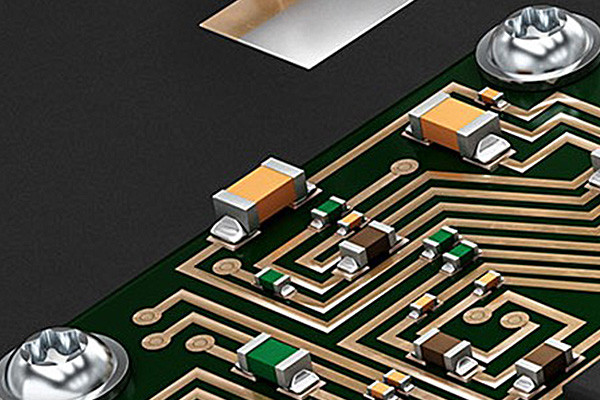
- Enhanced Shock Resistance:These adhesives create a secure bond between components and the PCB, improving shock resistance and minimizing the risk of damage during transportation, handling, or accidental drops.
- Reduced Stress on Solder Joints:By providing an additional support layer, SMT epoxy adhesives alleviate stress on solder joints caused by thermal expansion and contraction, ensuring solder joint integrity over time.
Application and Process
- Dispensing:SMT epoxy adhesives are precisely dispensed onto specific areas of the PCB using automated dispensing equipment, ensuring accurate placement and minimizing waste.
- Component Placement:Delicate components, such as microcontrollers, sensors, and connectors, are positioned onto the adhesive-coated areas, allowing the adhesive to create a strong bond during the curing process.
- Curing:Epoxy adhesives undergo a curing process, during which they harden and develop their robust properties. This method guarantees a reliable and long-lasting connection between the components and the PCB.
Considerations and Compatibility
- Material Compatibility:Manufacturers must choose epoxy adhesives compatible with both the components and the PCB materials to prevent delamination or corrosion.
- Thermal Characteristics:SMT epoxy adhesives should have suitable thermal properties to withstand the operating conditions of the electronic device without degrading or losing their adhesive strength.
- Adhesive Dispensing Precision:Precision in the adhesive application is crucial to prevent excess adhesive from interfering with nearby components or obstructing solder joints.
SMT Epoxy Adhesives for Miniaturized Electronics
The relentless drive toward miniaturization in electronics has ushered in a new era of compact and intricate devices. Within this landscape, Surface Mount Technology (SMT) epoxy adhesives have emerged as a critical enabler, providing essential solutions for the challenges posed by miniaturized electronics. These adhesives offer unique benefits that cater to the demands of shrinking form factors and intricate designs.
Benefits of Miniaturized Electronics
- Precision Bonding:SMT epoxy adhesives enable accurate and precise bonding of tiny components onto PCBs, ensuring optimal placement within confined spaces.
- Reduced Footprint:With solder joints becoming smaller and less reliable due to miniaturization, epoxy adhesives offer a larger bonding area, enhancing the overall stability of components.
- Enhanced Reliability: The adhesive’s ability to reinforce solder joints ensures improved mechanical strength, resisting external stressors and temperature fluctuations inherent in miniaturized designs.
Challenges Addressed
- Vibration Mitigation:Miniaturized devices are susceptible to vibrations that can lead to component displacement; epoxy adhesives dampen these vibrations and enhance device resilience.
- Thermal Management:SMT epoxy adhesives possess proper thermal conductivity, which helps channel heat away from densely packed components and prevents overheating.
- Flexibility and Durability:The adhesive’s flexibility reduces mechanical stress on fragile components, preventing cracking or detachment during assembly and use.
Application and Techniques
- Dispensing Techniques:We use advanced methods such as jetting and needle dispensing to ensure precise adhesive application, considering minute component dimensions.
- Underfilling:For Ball Grid Array (BGA) packages, underfilling with epoxy adhesive reinforces solder joints, curbing the impact of thermal expansion and contraction.
- Curing Considerations:SMT epoxy adhesives undergo controlled curing, solidifying the bond without damaging sensitive electronic parts.
Material Innovation and Compatibility
- Low Outgassing Formulations:Epoxy adhesives with common outgassing properties prevent the release of volatile components that could compromise device performance in confined spaces.
- Dielectric Properties:Adhesives with optimal dielectric constants ensure minimal signal interference in high-frequency applications.
- Adhesive-Substrate Compatibility:Compatibility with diverse materials, including different PCBs and substrates, is crucial to ensure long-term reliability.
Compatibility with Different Substrates
Regarding Surface Mount Technology (SMT), epoxy adhesives are crucial in securely bonding components to substrates. The compatibility of these adhesives with various substrates is critical for ensuring reliable and long-lasting electronic assemblies. Different substrates have distinct properties that can influence the adhesive’s performance, making compatibility a key consideration during adhesive selection.
Factors Influencing Compatibility
- Substrate Material:The substrate material used, such as FR-4, ceramic, or metal, dramatically affects the adhesive-substrate interaction. Each material has varying coefficients of thermal expansion (CTE) and surface energies, which can impact adhesion and stress distribution.
- Surface Finish:Substrates often have different surface finishes, including HASL, ENIG, and OSP. The adhesive’s ability to form a strong bond while accommodating these finishes is vital to prevent delamination or weak adhesion.
- Thermal Properties:Compatibility with a substrate’s thermal conductivity and heat dissipation characteristics is essential to avoid excessive heat buildup during component operation.
Benefits of Compatibility
- Reliability:Compatible adhesives ensure a strong bond between the components and the substrate, reducing the risk of solder joint cracking or detachment during thermal cycling and mechanical stress.
- Longevity:Properly selected epoxy adhesives enhance the overall lifespan of electronic assemblies by maintaining bond integrity over time and under varying conditions.
- Improved Performance:Compatible adhesives help maintain signal integrity, power distribution, and thermal management, all of which contribute to optimal electronic performance.
Considerations during Selection
- Thermal Expansion Matching:Choosing an epoxy adhesive with a CTE close to that of the substrate helps alleviate stress-related issues, especially during temperature fluctuations.
- Surface Energy Matching:Adhesives with similar surface energy to the substrate’s surface finish enhance wetting and spreadability, resulting in better adhesion.
- Chemical Compatibility:Compatibility with cleaning agents, flux residues, and other chemicals used in the manufacturing process prevents adverse reactions that could compromise the adhesive bond.
Surface Preparation for SMT Epoxy Adhesion
Surface Mount Technology (SMT) epoxy adhesives are crucial in electronic assembly, providing reliable bonding for components on printed circuit boards (PCBs). Proper surface preparation is essential to ensure strong and durable adhesion, enhancing the overall performance and reliability of electronic devices. Here are the key considerations and steps for adequate surface preparation when using SMT epoxy adhesives:
Substrate Cleaning
- Thoroughly clean the substrate (PCB) surface to remove dust, grease, oils, and other contaminants.
- Use a mild detergent solution, isopropyl alcohol, or specialized cleaning agents designed for electronics.
- Rinse and dry the surface carefully to prevent residue buildup.
Mechanical Abrasion
- Abrading the substrate surface helps create a roughened texture, promoting adhesive bond strength.
- Techniques include sanding, sandblasting, or abrasive pads. Be cautious not to damage delicate components.
Plasma Treatment
- Plasma cleaning or etching increases surface energy and removes organic contaminants.
- You can effectively use low-pressure plasma systems to treat a variety of substrate materials.
Chemical Treatment
- Chemical primers or adhesion promoters improve the substrate’s receptiveness to epoxy adhesives.
- Many commonly use silane coupling agents to enhance adhesion to various surfaces.
Surface Activation
- Plasma activation or corona treatment enhances surface wettability and adhesion properties.
- This process creates temporary functional groups on the substrate surface, facilitating bonding.
Considerations for Specific Substrates
- Different substrates (e.g., FR-4, ceramic, metal) require tailored surface preparation approaches.
- Select methods compatible with the substrate’s material and characteristics.
Temperature and Humidity Control
- Perform surface preparation in controlled environments to minimize contamination risks.
- Adhere to recommended temperature and humidity conditions for optimal adhesive performance.
Adhesive Dispensing and Curing
- Follow manufacturer guidelines for dispensing and applying epoxy adhesive.
- Ensure uniform coverage and appropriate adhesive thickness.
- Properly cure the adhesive using recommended temperature and curing time to achieve maximum bond strength.
Post-Adhesion Inspection
- After bonding, inspect the adhesive joints for any defects or irregularities.
- Check for voids, delamination, or incomplete bonding that might compromise the integrity.
Electronics in Harsh Environments
In today’s rapidly advancing technological landscape, companies deploy electronic devices in increasingly challenging environments, from industrial settings to aerospace applications. Ensuring the reliability and longevity of electronics in such harsh conditions necessitates specialized considerations and solutions. Here are the key factors and strategies to address the challenges of operating electronics in harsh environments, with a focus on the role of SMT epoxy adhesives:
Environmental Factors
- Harsh environments encompass extremes of temperature, humidity, vibration, and exposure to chemicals or contaminants.
- Electronics must withstand these conditions to maintain functionality and performance.
Component Protection
- SMT epoxy adhesives protect against moisture, dust, and chemicals that could degrade components.
- They help prevent corrosion and ensure the longevity of solder joints and circuitry.
Thermal Management
- Extreme temperatures can impact electronic performance and reliability.
- SMT epoxy adhesives with high thermal conductivity properties aid heat dissipation, minimizing temperature-induced stress on components.
Vibration and Shock Resistance
- Mechanical vibrations and shocks cause various stresses on electronics in applications such as automotive or aerospace.
- SMT epoxy adhesives with excellent bonding strength provide structural integrity, preventing component displacement.
Adhesive Flexibility
- Harsh environments often involve varying degrees of thermal expansion and contraction.
- Flexible epoxy adhesives can absorb mechanical stresses, preventing cracks or detachment.
Chemical Resistance
- Exposure to chemicals, solvents, or corrosive substances can degrade electronic components.
- SMT epoxy adhesives with chemical resistance properties act as a barrier, safeguarding components from harm.
Sealing and Encapsulation
- Potting and encapsulation techniques using epoxy adhesives shield sensitive components from external elements for maximum protection.
- It is essential to consider situations such as underwater sensors or control systems for oil rigs.
Application Expertise
- Designing electronics for harsh environments requires a deep understanding of the specific challenges and operational conditions.
- Collaborating with materials science and electronics assembly experts is crucial to ensure optimal solutions.
Testing and Validation
- Rigorous testing under simulated harsh conditions is essential to verify the performance and reliability of electronics.
- Comprehensive validation ensures that the chosen epoxy adhesives and assembly techniques meet the intended specifications.
Automotive SMT Bonding Applications
Integrating advanced electronics and sensors has become essential for safety, performance, and connectivity in the rapidly evolving automotive industry. Surface Mount Technology (SMT) epoxy adhesives are pivotal in securely attaching electronic components to the vehicle’s Printed Circuit Boards (PCBs). Reliable performance, durability, and miniaturization of automotive electronics are made possible.
Benefits of SMT Epoxy Adhesives in Automotive Applications
1.Compact Design:SMT epoxy adhesives facilitate the mounting of electronic components directly onto PCBs, allowing for a more compact and space-efficient design. In modern vehicles where space is limited, this is extremely important.

2.Vibration and Shock Resistance:Constant vibrations and shocks characterize automotive environments. SMT epoxy adhesives provide excellent bonding strength that withstands these conditions, ensuring the longevity and stability of the components.
3.Thermal Management:Electronic components generate heat; efficient thermal dissipation is vital to prevent overheating. SMT epoxy adhesives with high thermal conductivity help dissipate heat effectively, maintaining optimal operating conditions.
4.Chemical and Environmental Resistance:Various chemicals, fluids, and environmental conditions expose automotive electronics to challenges. SMT epoxy adhesives resist these elements, ensuring consistent performance over the vehicle’s lifespan.
5.Automated Manufacturing:The automotive industry demands high-speed and precision manufacturing processes. SMT epoxy adhesives are compatible with mechanical pick-and-place equipment, streamlining the assembly process and reducing production time.
Key Applications in the Automotive Sector
- Advanced Driver Assistance Systems (ADAS): Manufacturers use SMT epoxy adhesives to attach radar sensors, LiDAR modules, and camera components onto PCBs, enabling ADAS functionalities like adaptive cruise control and lane departure warning systems.
- Infotainment Systems:In-vehicle infotainment systems incorporate touchscreens, displays, and audio components. SMT epoxy adhesives secure these components, ensuring responsive interfaces and uninterrupted entertainment experiences.
- Electric Vehicle (EV) Power Electronics:EVs rely heavily on intricate power electronics systems. SMT epoxy adhesives are instrumental in securing power modules, converters, and battery management systems, contributing to the efficiency and reliability of EVs.
- Wireless Connectivity:The automotive industry is embracing wireless communication technologies. SMT epoxy adhesives play a role in mounting Bluetooth, Wi-Fi, and cellular modules, supporting features such as remote keyless entry and vehicle-to-everything (V2X) communication.
Consumer Electronics and Wearables
The consumer electronics and wearables world has undergone a remarkable transformation driven by integrating innovative technologies into everyday gadgets. Surface Mount Technology (SMT) epoxy adhesives have emerged as indispensable tools in this evolution, enabling the secure attachment of miniaturized components that power the latest consumer electronics and wearable devices.
Benefits of SMT Epoxy Adhesives in Consumer Electronics
- Miniaturization:SMT epoxy adhesives allow for the compact placement of components on Printed Circuit Boards (PCBs), enabling the design of sleek and portable devices that fit seamlessly into users’ lifestyles.
- Robust Bonding:Consumer electronics are subject to frequent handling and potential impacts. SMT epoxy adhesives provide strong and durable bonds, ensuring the longevity of devices even in demanding usage scenarios.
- Electrical Performance:Maintaining reliable electrical connections is crucial with the increasing complexity of electronic circuits. SMT epoxy adhesives offer low resistance connections and minimize signal loss, supporting optimal device performance.
- Temperature and Environmental Resistance:People use consumer electronics in various environments and temperature conditions. SMT epoxy adhesives resist heat, cold, moisture, and other environmental factors, preserving device functionality.
- Production Efficiency:Manufacturers often produce consumer electronics in high volumes. SMT epoxy adhesives are compatible with automated assembly processes, enhancing manufacturing efficiency and reducing production costs.
Key Applications in Consumer Electronics and Wearables
- Smartphones and Tablets:SMT epoxy adhesives are vital for securing components like microprocessors, sensors, and connectors within the compact enclosures of smartphones and tablets.
- Wearable Health Monitors:Wearable devices that track health metrics rely on SMT epoxy adhesives to securely hold biosensors, accelerometers, and other medical-grade components against the wearer’s skin.
- Virtual Reality (VR) and Augmented Reality (AR) Devices:SMT epoxy adhesives play a role in mounting the intricate displays and sensors that enable immersive experiences in VR and AR headsets.
- Fitness Trackers and Smartwatches: The sleek designs of fitness trackers and smartwatches are made possible by SMT epoxy adhesives that securely bond components while maintaining the devices’ slim profiles.
- Wireless Earbuds:Tiny components within wireless earbuds, including microphones, batteries, and Bluetooth modules, are securely affixed using SMT epoxy adhesives, ensuring reliable performance and compact designs.
Medical Device Assembly
The intersection of medical technology and electronics has led to remarkable patient care, diagnostics, and treatment advancements. In medical device assembly, Surface Mount Technology (SMT) epoxy adhesives are crucial in ensuring intricate electronic components’ precision, reliability, and performance. This article explores the significance of SMT epoxy adhesives in medical device assembly, examining their applications, benefits, and unique considerations.
Applications in Medical Device Assembly
- Implantable Devices:SMT epoxy adhesives assemble implantable devices such as pacemakers, defibrillators, and neurostimulators. They secure miniature components while offering biocompatibility and hermetic sealing.
- Diagnostic Equipment:Medical imaging equipment and diagnostic devices rely on SMT epoxy adhesives for stable positioning of sensors, connectors, and microprocessors. This precision ensures accurate readings and diagnoses.
- Wearable Health Tech:Wearable devices like fitness trackers and glucose monitors benefit from epoxy adhesives that provide robust bonding, moisture resistance, and durability while being comfortable for long-term wear.
- Surgical Tools:Epoxy adhesives facilitate the assembly of precision surgical tools and devices, ensuring reliable electronics integration and sterilization compatibility.
Benefits of Medical Device Assembly
- Miniaturization:SMT epoxy adhesives allow for compact designs, enabling the creation of smaller and less invasive medical devices.
- Biocompatibility:Tailoring epoxy formulations to meet biocompatibility requirements renders them suitable for devices that come into contact with human tissue or fluids.
- Hermetic Sealing:Epoxy adhesives provide airtight and moisture-resistant seals that protect sensitive electronics in implantable and external medical devices.
- Thermal Management:Advanced epoxy formulations with high thermal conductivity enhance heat dissipation in devices, prolonging their lifespan and performance.
- Reliability:SMT epoxy adhesives ensure stable component attachment, reducing the risk of malfunctions that could compromise patient safety.
Unique Considerations
- Regulatory Compliance:Medical devices are subject to stringent regulatory standards. Epoxy adhesives must meet these requirements for biocompatibility, sterilization, and safety.
- Longevity and Stability:Medical devices often need to function reliably over extended periods. Epoxy adhesives used must withstand the rigors of time, temperature variations, and environmental stress.
- Assembly Precision:The precision demanded in medical device assembly requires highly accurate epoxy dispensing and component placement, achievable through advanced automation and inspection techniques.
SMT epoxy adhesives are a linchpin for creating technologically advanced, reliable, and patient-centric electronic devices in medical device assembly. Their role in ensuring miniaturization, biocompatibility, sealing, and overall device performance makes them indispensable in shaping the future of healthcare technology.
Quality Control and Inspection
Quality control and inspection are pivotal in ensuring the reliability and performance of Surface Mount Technology (SMT) assemblies utilizing epoxy adhesives. With the ever-increasing demand for higher functionality and miniaturization, meticulous quality assurance processes have become paramount. Below are vital aspects highlighting the significance of quality control and inspection in SMT epoxy adhesive applications:
- Adhesive Dispensing Verification:Automated inspection systems verify the accuracy of adhesive deposition, ensuring proper volume and placement. This step minimizes the risk of incomplete or excessive adhesive, which can lead to solder joint issues and reliability concerns.
- Component Alignment and Orientation:Vision systems assess the positioning and orientation of components before epoxy dispensing. Preventing misalignment is essential, as it could lead to shorts, opens, or faulty connections, negatively affecting the circuit’s performance.
- Visual Defect Detection:Inspection cameras identify visible defects such as air bubbles, voids, and cracks within the epoxy adhesive. Detecting these anomalies is crucial for ensuring the long-term structural integrity of the assembly.
- Adhesive Curing Verification:Quality control includes verifying the proper curing of epoxy adhesives. Inadequate curing can lead to weak bonds and poor thermal or mechanical performance.
- Solderability Verification:Inspection techniques assess whether epoxy residues interfere with solder wetting during the subsequent soldering process. Proper solder wetting is essential for reliable electrical connections.
- Automated Optical Inspection (AOI):AOI systems scan the assembly for defects, including misplaced components, solder joint issues, and epoxy-related anomalies. This technology ensures comprehensive inspection on time.
- X-ray Inspection:X-ray techniques can reveal hidden defects beneath components and epoxy layers. Such identification is crucial for detecting voids, cracks, and other potential issues that could compromise the assembly’s performance.
- Statistical Process Control (SPC):SPC methods track and analyze data over time, allowing manufacturers to identify trends and potential deviations in the adhesive application process. This proactive approach ensures consistent quality across production batches.
- Traceability and Documentation:Quality control systems often include traceability features that link each assembly to its specific adhesive application parameters. This documentation assists in troubleshooting and conducting root cause analysis if issues arise after deploying the product.
Quality control and inspection are integral components of SMT epoxy adhesive applications. These processes ensure that adhesive dispensing, component placement, curing, and assembly integrity adhere to stringent standards, resulting in reliable, high-performance electronic products.
Dispensing Techniques and Automation
In the dynamic field of electronics manufacturing, the precise application of epoxy adhesives is paramount for ensuring the integrity, performance, and reliability of Surface Mount Technology (SMT) assemblies. The evolution of dispensing techniques and automation has transformed how SMT epoxy adhesives are applied, streamlining processes and enhancing overall product quality. This article delves into the various dispensing methods and the role of automation in optimizing SMT epoxy adhesive applications.
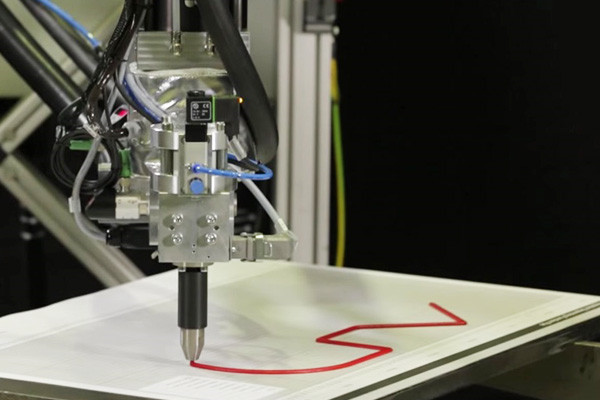
Precision Dispensing Techniques
- Jet Dispensing: High-speed, non-contact method for accurate adhesive deposition.
- Needle Dispensing: Traditional method offering versatility for various adhesive viscosities.
- Micro-Dispensing: Sub-microliter application for intricate, miniature components.
- Auger Valve Dispensing: Ideal for high-viscosity adhesives, ensuring uniformity.
Benefits of Automated Dispensing
- Consistency:Automation eliminates human error, providing uniform adhesive application.
- Speed:High-speed automation accelerates production rates, reducing cycle times.
- Complex Patterns:Automated systems execute intricate adhesive patterns with precision.
- Material Savings:Precise control reduces waste, optimizing adhesive usage.
- Reproducibility:Automation ensures consistent results across batches.
Machine Vision Integration
- Vision-guided dispensing systems use cameras to ensure accurate adhesive placement.
- Real-time adjustments compensate for variations in component positioning.
- This feature facilitates seamless integration into complex production lines.
Inline Quality Control
- Automated inspection systems verify adhesive volume, placement, and quality.
- Rejects defective assemblies, minimizing the risk of faulty products.
- This improvement enhances final product reliability and customer satisfaction.
Customizable Programming
- Automation platforms allow for easy programming of dispensing parameters.
- This technology exhibits adaptability to varying component geometries and adhesive requirements.
- Reduces setup time when transitioning between different products.
Challenges and Future Outlook
- They are overcoming challenges like adhesive curing time and material compatibility.
- Continued advancements in automation technology aim for even higher precision.
- The integration of machine learning enables adaptive and self-optimizing dispensing.
Dispensing techniques and automation have become pivotal in SMT epoxy adhesive applications. Precise dispensing methods and automation bring efficiency, accuracy, and consistency to electronics manufacturing. As technology continues to evolve, the symbiotic relationship between adhesive dispensing techniques and automation promises to drive innovation and elevate the performance of SMT assemblies to unprecedented levels.
Advancements in SMT Epoxy Technology
In recent years, significant strides have been made in Surface Mount Technology (SMT) epoxy technology, revolutionizing the electronics manufacturing industry. These advancements have led to more efficient and reliable electronic assemblies, pushing the boundaries of miniaturization and performance. This article explores the key breakthroughs and benefits of the latest developments in SMT epoxy technology.
Enhanced Thermal Conductivity
- Novel epoxy formulations now offer improved thermal conductivity properties.
- Effective dissipation of heat from high-power components enhances overall device reliability.
- This technology enables the creation of smaller yet high-performing electronic devices. This technology allows for the production of compact but efficient electronic devices.
Nanoscale Packaging Solutions
- Advancements have led to the creation of nanoscale epoxy materials for packaging.
- We have enhanced the protection of sensitive components from moisture, dust, and physical stress.
- This technology assists in creating tiny wearables, IoT devices, and medical implants.
High-Frequency Performance
- New epoxy composites exhibit reduced signal loss at high frequencies.
- Enables the design of high-speed communication devices with minimal distortion.
- This technology paves the way for 5G and beyond.
Reliability and Durability
- Improved epoxy adhesion to various substrates ensures robust solder joint integrity.
- This advancement has improved the ability to withstand temperature and physical strain changes.
- This advancement extends the lifespan of electronics in demanding environments.
Fine Pitch Printing and Placement
- Advanced SMT epoxies allow for finer pitch printing and component placement.
- Enables denser circuitry on PCBs, contributing to space-saving designs.
- Ideal for applications demanding high interconnect density, such as advanced processors and memory modules.
Environmental Sustainability
- Emerging epoxy technologies focus on reducing environmental impact.
- Water-based and solvent-free epoxy options minimize volatile organic compound (VOC) emissions.
- This approach aligns with the industry’s growing emphasis on eco-friendly manufacturing practices.
The continuous evolution of SMT epoxy technology has unlocked a realm of possibilities in electronics manufacturing. Enhanced thermal conductivity, nanoscale packaging solutions, improved high-frequency performance, reliability, refined pitch capabilities, and a focus on environmental sustainability collectively mark a new era in electronics design and production. As these advancements ripple through various sectors, we can anticipate smaller, more powerful, and environmentally responsible electronic devices that shape the future of technology.
Environmental Considerations and Sustainability
Environmental considerations and sustainability are becoming increasingly integral to developing and using SMT epoxy adhesives, reflecting a growing awareness of the need for eco-friendly practices in the electronics industry. The following points highlight the critical aspects of environmental consciousness and sustainability in SMT epoxy adhesives:
- Reduced VOC Emissions:Manufacturers are prioritizing formulations with lower volatile organic compound (VOC) emissions, contributing to improved air quality and minimized environmental impact.
- Biodegradable Components:Incorporating biodegradable materials in adhesive formulations ensures that end-of-life disposal is more environmentally friendly, reducing the adhesive’s long-term footprint.
- Eco-Friendly Packaging: Sustainable packaging options, such as recyclable materials and minimalistic designs, align adhesive production with broader environmental goals.
- Energy-Efficient Processes:Adhesive manufacturers are adopting energy-efficient production processes to lower energy consumption and reduce greenhouse gas emissions.
- Resource Conservation:Sustainable practices involve the responsible use of raw materials and resources, minimizing waste generation, and conserving valuable inputs.
- Lifecycle Analysis:Conducting lifecycle assessments helps identify potential environmental impacts throughout an adhesive’s lifecycle, enabling informed decisions.
- Extended Product Lifespan:Adhesives that contribute to the longevity and reliability of electronic components reduce electronic waste by lowering replacement rates in the long run.
- Recycling Compatibility:Developing adhesive formulations compatible with recycling processes facilitates the recovery of valuable materials from discarded electronics.
- Green Certifications:Adhesives meeting eco-friendly standards and certifications demonstrate a commitment to sustainability and help guide consumers toward environmentally conscious choices.
As the electronics industry embraces sustainable practices, incorporating these environmental considerations in SMT epoxy adhesives reduces the industry’s ecological footprint and aligns with regulatory requirements and consumer expectations. By selecting adhesives that prioritize sustainability, manufacturers contribute to a greener future while ensuring the performance and reliability of their electronic products.
Future Innovations in SMT Epoxy Adhesives
Surface Mount Technology (SMT) epoxy adhesives are at the forefront of electronic assembly, enabling the secure attachment of components to PCBs. As technology evolves, the future holds exciting prospects for innovative advancements in SMT epoxy adhesive formulations. This section delves into the anticipated innovations in SMT epoxy adhesives, exploring how these developments will shape electronic manufacturing processes.
Anticipated Future Innovations:
- Miniaturization Solutions:As electronic components shrink, SMT epoxy adhesives will adapt to accommodate micro-sized features while maintaining robust bonding.
- High Thermal Resistance:Future adhesives will exhibit enhanced thermal resistance, ensuring stability and performance in electronics exposed to elevated temperatures.
- Conductive Adhesives:The rise of wearable electronics and flexible circuits will drive the development of conductive SMT epoxy adhesives, allowing for electrical connections and component attachment in a single step.
- Optical Transparency:Innovations in materials will lead to transparent epoxy adhesives, benefiting applications that require optical clarity or visual inspection.
- Fast-Curing Formulations:Manufacturers will develop rapid-curing adhesives to optimize production processes and reduce assembly times.
- Flexible and Impact-Resistant Adhesives:With the increasing demand for flexible and rugged electronics, epoxy adhesives with flexibility and impact resistance will become essential.
- Biocompatible Adhesives:The medical field will see the emergence of biocompatible SMT epoxy adhesives suitable for implantable medical devices and wearable health tech.
- Innovative Adhesives:Future adhesives might incorporate sensing or self-healing capabilities, enhancing electronics’ performance and longevity.
- Environmentally Friendly Solutions:Sustainability will drive the creation of epoxy adhesives with reduced VOC emissions and biodegradable components.
Impact on Electronic Manufacturing
The upcoming innovations in SMT epoxy adhesives will reshape the landscape of electronic manufacturing:
- Advanced Component Integration:Miniaturization solutions will facilitate the integration of complex components in compact spaces, enabling innovative product designs.
- Enhanced Performance:High thermal resistance and flexible formulations will bolster electronics’ reliability and functionality.
- Streamlined Production:Fast-curing adhesives will accelerate manufacturing processes, optimizing efficiency and reducing time-to-market.
- Diverse Applications:Conductive, transparent, and flexible adhesives will cater to a broader range of applications, from wearables to automotive electronics.
- Technological Synergy:Smart adhesives will synergize with IoT and sensor technologies, creating innovative components with embedded functionalities.
SMT epoxy adhesives play an integral role in the world of electronics manufacturing, ensuring the precision bonding required for Surface Mount Technology. Their ability to provide secure connections, thermal management, and mechanical stability is indispensable for industries seeking high-performance electronic devices. As technology continues to evolve and electronic products become more intricate, SMT epoxy adhesives will remain at the forefront of enabling advanced assembly techniques. With ongoing research and innovation, these adhesives are poised to shape the future of SMT, driving the creation of devices that offer enhanced functionality, reliability, and efficiency across a multitude of applications.