Printed Circuit Board Assembly Adhesive

In the realm of electronics manufacturing, the reliability and performance of printed circuit boards (PCBs) are paramount. Printed Circuit Board Assembly (PCBA) adhesive has emerged as a critical solution, transforming the way electronic components are affixed to PCBs. By providing precise and reliable bonding, PCBA adhesive enhances the durability, electrical connectivity, and thermal management of electronic assemblies. This comprehensive exploration delves into the realm of PCBA adhesive, uncovering its types, mechanisms, applications, benefits, and its integral role in shaping the landscape of contemporary electronics manufacturing.
Exploring PCBA Adhesive
Printed Circuit Board Assembly (PCBA) adhesive plays a pivotal role in the intricate world of electronics manufacturing, where precision and reliability are paramount. As electronic devices become more compact and advanced, the demand for efficient and dependable PCB assembly has skyrocketed. PCBA adhesive is the unsung hero that ensures the stability and durability of components on the board, making it an essential element in modern electronics.
When delving into the realm of PCBA adhesive, one encounters a variety of adhesive types, each tailored to specific requirements and challenges. Epoxy, polyurethane, acrylic, and silicone are just a few examples of unique properties and applications. Epoxy adhesives, known for their exceptional bonding strength, are favored in applications demanding high mechanical resistance. On the other hand, polyurethane adhesives offer flexibility and durability, making them ideal for applications prone to vibrations and thermal cycling.
Selecting a suitable adhesive involves a meticulous consideration of several factors. Engineers and manufacturers must weigh the crucial aspects of temperature resistance, adhesion strength, electrical conductivity, and chemical compatibility. Moreover, the surface preparation preceding adhesive application is equally significant. Proper cleaning and roughening of surfaces ensure optimal adhesion and contribute to the longevity of the bond.
As the PCB manufacturing landscape evolves, so do the challenges in adhesive application. Achieving consistent dispensing accuracy, avoiding voids, and managing curing times present intricate obstacles. The curing process solidifies the adhesive varies based on the adhesive type and manufacturing requirements. Heat, UV, and moisture curing are common mechanisms employed, each with benefits and considerations.
Quality control and testing mechanisms play a pivotal role in ensuring the integrity of the adhesive bonds. Shear testing, thermal cycling, and other methods assess adhesion strength and reliability. Furthermore, with rising environmental consciousness, the industry is increasingly focused on eco-friendly adhesive alternatives that adhere to stringent regulatory standards.
Challenges in Electronics Assembly
The world of electronics assembly is marked by constant innovation, pushing the boundaries of technology. At the heart of this process lies the critical element of Printed Circuit Board Assembly (PCBA) adhesive. While PCBA adhesive plays a crucial role in ensuring the stability and longevity of electronic components, it also brings forth its challenges. Let’s delve into the intricacies of these challenges and how they shape the landscape of electronics assembly.
Compatibility with Diverse Materials
- PCBA adhesive must bond with various materials, including metals, plastics, ceramics, and glass.
- Ensuring compatibility between adhesive and substrate materials is crucial for reliable adhesion and performance.
Temperature and Thermal Cycling
- Electronics are subjected to varying operating temperatures, leading to thermal expansion and contraction.
- Adhesive materials must withstand these temperature fluctuations without compromising bond integrity.
Miniaturization and Component Density
- Shrinking device sizes demand the precise placement of components in confined spaces.
- The adhesive application becomes intricate as miniaturization increases, necessitating accurate dispensing techniques.
Adhesive Curing and Assembly Time
- The balance between adhesive curing time and assembly efficiency is a delicate one.
- Extended curing times can slow production, while inadequate curing compromises bond strength.
Dispensing Accuracy and Void Prevention
- Achieving precise adhesive application is challenging, especially in micro-scale assemblies.
- The void formation caused by improper dispensing can lead to weak connections and reliability issues.
Environmental Considerations
- Environmental factors like humidity, chemicals, and moisture expose electronics to risks.
- Adhesives must exhibit resistance to these conditions to ensure consistent performance over time.
Adhesive Selection for Diverse Applications
- Different electronic devices have unique requirements, from consumer electronics to aerospace applications.
- Selecting the appropriate adhesive type for each application demands a deep understanding of adhesive properties and the device’s operational environment.
Quality Control and Reliability
- Ensuring adhesive bond quality requires robust quality control measures.
- Reliability testing, such as thermal cycling and shear testing, is essential to validate the strength of adhesive bonds.
Removal and Rework
- In component replacement or repairs, removing and reworking adhesive becomes essential.
- Balancing adhesive removability with bond strength is challenging to avoid damage during rework.
The challenges in electronics assembly, specifically about Printed Circuit Board Assembly Adhesive, underscore the intricate dance between innovation and practicality. As technology evolves, so do manufacturers’ complexities in creating reliable, high-performance electronic devices. Addressing the challenges of material compatibility, thermal stresses, miniaturization, and more requires a combination of expertise, cutting-edge technology, and a commitment to delivering products that meet the highest quality and performance standards.
Role of PCBA Adhesive in Electronics
Printed Circuit Board Assembly (PCBA) adhesive is the unsung hero in modern electronics, binding together the intricate components that power our digital world. Beyond its seemingly modest role, PCBA adhesive plays a pivotal part in shaping electronic devices’ reliability, durability, and performance. Let’s explore the multifaceted role of PCBA adhesive and its significance in electronics.
Component Attachment and Stability
- PCBA adhesive secures components to the printed circuit board, preventing mechanical stress and vibrations from compromising their connections.
- Ensures the stable positioning of components, which is crucial for maintaining electrical conductivity and signal integrity.
Thermal Management
- Acts as a thermal conductor or insulator, facilitating heat dissipation generated by electronic components.
- It prevents overheating, which can lead to performance degradation and component failure.
Vibration and Shock Absorption
- Cushions electronic components against external shocks and vibrations, preserving their structural integrity.
- Essential in applications subjected to mechanical stress, such as automotive electronics and industrial machinery.
Environmental Protection
- It creates a barrier against moisture, dust, and contaminants that can cause corrosion and short circuits.
- This practice enhances the longevity of electronic devices, especially those used in harsh environments.
Electrical Insulation
- Isolates conductive components from each other to prevent unintended electrical connections.
- Ensures the reliable functioning of complex circuits by maintaining proper electrical isolation.
Bonding Dissimilar Materials
- Bridges the gap between materials with differing coefficients of thermal expansion, preventing mechanical failure due to material mismatch.
- Enables the use of diverse materials in electronic assemblies, promoting design flexibility.
Structural Support
- Reinforces the mechanical strength of fragile components, particularly in applications where mechanical stress is common.
- This process enhances the overall structural integrity of the device.
Design Flexibility
- This capability enables the creation of innovative designs, including flexible and bendable electronics.
- By providing the freedom to develop novel product forms, this approach allows for maintaining reliable connections.
The unassuming PCBA adhesive goes beyond its role as a mere bonding agent, acting as a silent enabler of the electronic marvels we rely on daily. Its ability to secure, protect, and enhance electronic components is a testament to its significance in electronics. As technology advances, PCBA adhesive evolves, adapting to the demands of ever-smaller devices, complex designs, and rigorous environmental conditions. This essential adhesive truly serves as the glue that holds the future of electronics together.
Surface Preparation for Bonding
Proper surface preparation emerges as a foundational step when it comes to ensuring the reliability and durability of Printed Circuit Board Assembly (PCBA) adhesive bonds. The effectiveness of the adhesive bond relies on the cleanliness and condition of the surfaces being bonded. Let’s explore the significance of surface preparation and the essential steps in achieving optimal adhesion.
Importance of Surface Preparation
Proper surface preparation is the cornerstone of successful bonding in PCBA adhesive applications. It directly influences the strength, longevity, and integrity of the adhesive bond by:
- Removing contaminants and particles that can hinder adhesion.
- Creating a clean and receptive surface for the adhesive to adhere to.
- Minimizing the risk of voids, delamination, and bond failure.
Steps in Surface Preparation
Adequate surface preparation involves a systematic approach to ensure a flawless bond between the adhesive and the substrate. The key steps include:

Cleaning
- Remove dirt, grease, oils, and residues from the surface using appropriate cleaning agents.
- Ensure the surface is free from any contaminants that could hinder adhesion.
Degreasing
- Use specialized solvents to remove any traces of oils, which can interfere with adhesive bonding.
- Thoroughly degrease the surface to promote optimal contact between the adhesive and the substrate.
Abrading
- Gently rub the surface to create micro-roughness, enhancing the mechanical interlocking between the adhesive and substrate.
- Promotes better adhesion by increasing the surface area for contact.
Chemical Treatment
- Apply primers or chemical treatments that improve adhesion by promoting molecular bonding between the adhesive and the substrate.
- This improvement enhances the adhesive’s ability to stick to the surface material.
Drying
- Ensure the surface is completely dry before applying the adhesive to prevent moisture-related issues.
- Moisture can hinder adhesive curing and compromise the integrity of the bond.
Surface preparation is a critical yet often underestimated aspect of successful bonding in Printed Circuit Board Assembly adhesive applications. Meticulously executing cleaning, degreasing, rubbing, and applying appropriate chemical treatment ensures that the adhesive bond forms on a solid foundation. By adhering to these surface preparation principles, manufacturers can create reliable, durable, high-performance adhesive bonds in electronics assembly that stand the test of time.
Types of PCBA Adhesives
Printed Circuit Board Assembly (PCBA) adhesive is a versatile category of materials that plays a crucial role in ensuring the stability and durability of electronic devices. With various types of adhesives available, each tailored to specific needs, selecting the right one is essential for successful bonding. Let’s explore the different kinds of PCBA adhesives and their unique characteristics.
Epoxy Adhesives
- They were known for their exceptional bonding strength and resistance to chemicals and environmental factors.
- Ideal for applications requiring high mechanical stability, such as industrial equipment and automotive electronics.
Polyurethane Adhesives
- It offers flexibility, excellent electrical insulation properties, and good resistance to impact and thermal cycling.
- It is suitable for applications in which components such as consumer electronics and aerospace systems undergo vibrations.
Acrylic Adhesives
- It provides fast curing, good resistance to UV exposure, and a wide range of operating temperatures.
- Often used in applications that demand rapid production cycles and exposure to outdoor conditions.
Silicone Adhesives
- It exhibits excellent flexibility over a wide temperature range, making it ideal for applications with extreme temperature variations.
- It provides reliable electrical insulation and finds common usage in high-temperature environments.
Conductive Adhesives
- It contains conductive particles, allowing them to function as adhesive and electrical connections.
- They find use in applications requiring crucial electrical conductivity, such as bonding electronic components onto flexible circuits.
Thermal Interface Adhesives
- It is optimized for efficient heat transfer between components and heat sinks, preventing overheating.
- This enhancement improves thermal management in computers, LED lighting, and power electronics.
UV-Curing Adhesives
- Cures quickly under ultraviolet light, enabling rapid assembly processes.
- Suitable for applications that require precise placement and immediate bonding, such as microelectronics.
Electrically Insulating Adhesives
- The design intends to offer electrical insulation between components and prevent short circuits.
- Used in scenarios where maintaining proper electrical isolation is critical.
The wide array of PCBA adhesive types caters to diverse needs and applications within the electronics assembly realm. Selecting a suitable adhesive involves carefully considering mechanical properties, thermal conductivity, electrical characteristics, and environmental conditions. By matching the adhesive type to the specific requirements of the assembly, manufacturers can ensure solid and reliable bonds that contribute to the overall performance and longevity of electronic devices.
SMT (Surface Mount Technology) Adhesives
Surface Mount Technology (SMT) has revolutionized the electronics assembly process, enabling the creation of smaller, more efficient devices. At the heart of this innovation lies SMT adhesives, specially formulated to address the unique challenges of component placement and bonding in PCB assembly. Let’s delve into the role and benefits of SMT adhesives in Printed Circuit Board Assembly (PCBA) and how they contribute to precision and reliability.
Key Benefits of SMT Adhesives:
- Precise Component Placement:SMT adhesives facilitate the accurate positioning of miniature components on the PCB, ensuring optimal alignment.
- Vibration Dampening:These adhesives enhance the mechanical stability of components by absorbing vibrations, minimizing the risk of dislodgement.
- Minimized Solder Bridging:SMT adhesives prevent solder bridging by keeping components in place during the soldering process, reducing the chances of short circuits.
- Thermal Management:By creating a thermal interface between components and the PCB, SMT adhesives contribute to efficient heat dissipation, preventing overheating.
- Reduced Assembly Time:SMT adhesives allow temporary component fixation before soldering, streamlining the assembly process and reducing rework needs.
Types of SMT Adhesives:
- Tackifying Adhesives:These adhesives provide temporary tackiness to hold components in place during soldering, enhancing precision.
- Paste Adhesives: SMT paste adhesives are dispensed using stencil printing techniques and offer excellent adhesion and reflow soldering compatibility.
- Dispensable Adhesives:These adhesives are applied in controlled amounts to specific areas, ensuring precise component positioning.
- UV-Curable Adhesives:UV-curing SMT adhesives offer rapid curing under ultraviolet light, increasing efficiency in production cycles.
Applications:
- Manufacturers extensively utilize SMT adhesives in consumer electronics, automotive electronics, telecommunications equipment, and medical devices.
- They find applications in devices with small form factors, such as smartphones, wearables, IoT devices, and miniaturized sensors.
SMT adhesives play a pivotal role in PCB assembly, contributing to electronic devices’ precision, reliability, and efficiency. By providing accurate component placement, minimizing soldering issues, and enhancing thermal management, SMT adhesives enable the creation of compact, high-performance devices that define our modern technological landscape. As electronic designs evolve, SMT adhesives remain an indispensable tool for manufacturers striving to achieve excellence in their PCBA processes.
Thermal Conductive Adhesives for Heat Dissipation
Thermal Conductive Adhesives (TCAs) have emerged as a crucial innovation in Printed Circuit Board Assembly (PCBA) adhesives, revolutionizing the efficiency of heat dissipation in electronic devices. These adhesives combine the benefits of traditional adhesion with the ability to efficiently transfer heat away from sensitive components, ensuring optimal performance and extending the lifespan of electronics. Here’s a concise overview of their significance:
- Enhanced Heat Dissipation:TCAs address the escalating heat challenges of densely packed electronic components. By offering high thermal conductivity, they facilitate the rapid transfer of heat from heat-generating parts to heat sinks or other dissipating elements.
- Improved Reliability:Efficient heat dissipation translates to enhanced reliability and stability of electronic devices. TCAs prevent overheating, leading to premature component failure, data loss, or even catastrophic breakdowns.
- Space-Saving Solution:Unlike traditional heat sinks or thermal pads, TCAs are ultra-thin, ideal for space-constrained PCBAs. They enable compact designs without compromising thermal management.
- Enhanced Design Flexibility:TCAs can be applied in various patterns and configurations, allowing engineers to optimize heat flow within complex PCB layouts. This adaptability contributes to the overall thermal efficiency of the system.
- Reduced Weight:Traditional heat sink solutions can add considerable weight to devices, which might need to be more practical in applications where importance is critical. TCAs provide an efficient and lightweight alternative.
- Uniform Stress Distribution:TCAs ensure efficient heat transfer and offer good adhesive strength. This feature aids in distributing mechanical stress evenly across components, minimizing the risk of solder joint failure due to thermal expansion mismatches.
- Ease of Application:TCAs can be dispensed or applied as pastes, ensuring compatibility with modern assembly processes, including automated dispensing equipment. This ease of application streamlines manufacturing workflows.
Conductive Adhesives for Electrical Connections
Conductive adhesives have emerged as a transformative solution within the realm of Printed Circuit Board Assembly (PCBA) adhesives, reshaping the landscape of electrical connections in electronic devices. These adhesives combine the benefits of adhesive bonding with the capability to establish reliable electrical pathways, offering a versatile and efficient alternative to traditional soldering. Here’s a brief overview of their significance:
- Seamless Electrical Bonding:Conductive adhesives enable seamless electrical connections between components, eliminating the need for soldering. This method can achieve improved signal integrity and reduced risk of joint failure.
- Gentle on Components:Unlike soldering, which involves high temperatures that can damage sensitive components, conductive adhesives are applied at lower temperatures, preserving the integrity of delicate electronic parts.
- Diverse Substrate Compatibility:Conductive adhesives exhibit remarkable compatibility with various substrates, including flexible and rigid PCBs, enabling their use in different electronic designs.
- Miniaturization:As electronic devices become smaller and more complex, conductive adhesives offer a space-efficient solution. Their ability to form fine traces and connections accommodates the trend of miniaturization.
- Reduced Manufacturing Costs:The absence of soldering processes simplifies manufacturing workflows, leading to cost savings. Additionally, the ability to automate adhesive applications contributes to higher production efficiency.
- Enhanced Design Flexibility:Conductive adhesives can be applied in intricate patterns, allowing designers to create custom connections tailored to specific applications. This flexibility promotes innovation in PCB layouts.
- Environmental Benefits:Unlike traditional soldering processes that involve lead-based materials, many conductive adhesives are environmentally friendly, reducing hazardous waste and supporting eco-friendly practices.
- Reliability:Conductive adhesives have undergone rigorous testing to ensure durability and reliability in various operating conditions, increasing confidence in their long-term performance.
Conductive adhesives have revolutionized the establishment of electrical connections in Printed Circuit Board Assemblies. Their unique ability to combine adhesive bonding with electrical conductivity opens new possibilities in electronics design and manufacturing. As the electronics industry continues to evolve, conductive adhesives are a testament to innovation and adaptability, ensuring reliable connections in the era of intricate and compact electronic devices.
PCBA in Consumer Electronics
Printed Circuit Board Assembly (PCBA) plays a pivotal role in shaping the consumer electronics landscape, seamlessly integrating advanced technologies into everyday devices. The convergence of innovation and user-centric design has led to incorporating PCBAs in various products, enhancing functionality, user experience, and connectivity. Here’s a concise overview of PCBA’s significance in the realm of consumer electronics:
1.Compact Design:PCBAs enable the creation of compact and sleek consumer devices, accommodating the growing demand for portable and space-efficient gadgets that seamlessly integrate into modern lifestyles.
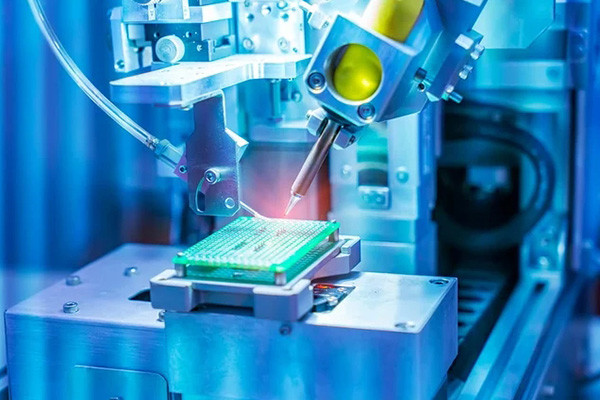
2.Functionality Expansion:The integration of PCBAs empowers consumer electronics with various functionalities, from complex processing capabilities and wireless connectivity to advanced sensors and user interfaces.
3.Connected Ecosystem:PCBAs enable the development of related ecosystems, facilitating seamless communication between devices and promoting features like IoT (Internet of Things) connectivity, enhancing convenience and automation in daily life.
4.User Experience Enhancement:Consumer electronics with PCBAs offer enhanced user experiences through intuitive interfaces, responsive touchscreens, voice recognition, and gesture controls.
5.Energy Efficiency:PCBAs contribute to energy-efficient design by optimizing power consumption, extending battery life, and enabling sleep modes and power management features.
6.Customization:PCBAs allow for tailored designs that cater to specific consumer needs. From wearable fitness trackers to smart home controllers, customization enhances usability and appeal.
7.Rapid Technological Advancements:The fast-paced nature of the consumer electronics industry is facilitated by PCBAs, enabling manufacturers to integrate the latest technologies and stay ahead of evolving trends.
8.Manufacturing Efficiency:Automated processes can assemble PCBAs, streamlining production and reducing costs. This efficiency translates to affordable and accessible consumer electronics.
9.Environmental Considerations:As the industry embraces sustainability, PCBAs can be designed with eco-friendly materials and processes, contributing to reduced electronic waste and a smaller ecological footprint.
Automotive Electronics Bonding
Automotive Electronics Bonding holds a pivotal role within the realm of Printed Circuit Board Assembly (PCBA), driving the innovation and reliability of today’s vehicles. As the automotive industry rapidly embraces advanced technologies, including autonomous driving and electric propulsion, we cannot overstate the significance of secure and efficient bonding in PCBA. Here’s a concise overview, including key bullet points:
- Reliable Connections:Automotive electronics bonding establishes secure connections between components on the PCB, ensuring the continuous operation of critical systems, including safety features, engine management, infotainment, and more.
- Challenging Environments:Vehicles operate in diverse conditions, from extreme temperatures to vibrations and moisture exposure. Effective bonding materials must withstand these challenges while maintaining consistent electrical and mechanical performance.
- Safety and Performance:Secure bonding contributes to vehicles’ safety and overall performance. Components like airbags, anti-lock braking systems, and electronic stability control rely on precise connections enabled by reliable bonding.
- Hybrid and Electric Vehicles:As the automotive landscape shifts toward electrification, bonding plays a role in optimizing battery management, energy distribution, and thermal management, ensuring the efficiency and longevity of electric and hybrid vehicles.
- Sustainability and Efficiency:Efficient bonding solutions contribute to energy efficiency by enabling proper power distribution and minimizing losses, aligning with the automotive industry’s drive toward sustainability.
- Adherence to Standards:Automotive electronics must adhere to stringent safety and quality standards. Bonding materials and techniques must meet these standards to ensure vehicle electronics’ reliability and regulatory compliance.
- Innovative Materials:Advancements in adhesive technologies and conductive materials have led to innovative bonding solutions. These materials offer enhanced thermal conductivity, mechanical stability, and long-term performance in the demanding automotive environment.
- Design Flexibility:Efficient bonding allows for flexible PCB design, enabling compact layouts, optimal signal routing, and effective heat dissipation, which is crucial in space-constrained vehicle electronics.
- Rapid Technological Evolution:The evolution of automotive electronics is rapid. Bonding solutions must keep pace with the integration of new sensors, communication protocols, and advanced driver assistance systems.
Medical Devices and Wearables
In healthcare, Printed Circuit Board Assembly (PCBA) technology has ushered in a new era of innovation with the development of medical devices and wearables. These compact, intelligent devices are reshaping patient care, diagnostics, and monitoring, enhancing patient experience and medical outcomes. Below, we delve into the significance of PCBA in the context of medical devices and wearables, featuring key bullet points under relevant subheadings:
Enhanced Diagnostics and Monitoring
- Compact Design:PCBA enables the integration of robust sensing and diagnostic capabilities into small, wearable devices.
- Real-time Data:Wearables equipped with PCBA can collect, process, and transmit real-time patient data, enabling continuous monitoring and timely intervention.
- Remote Healthcare:Medical wearables extend medical care beyond hospitals, allowing doctors to monitor patients and make informed decisions remotely.
Personalized Treatment
- Data Analytics:PCBA-enabled wearables provide healthcare professionals with rich data insights, facilitating personalized treatment plans.
- Adaptive Feedback:Wearable devices can offer real-time feedback to users, encouraging healthier behaviors and treatment adherence.
- Tailored Medication:Some wearables can deliver precise medication dosages based on real-time patient data.
IoT Integration and Connectivity
- Seamless Integration:PCBA technology enables wearables to seamlessly connect with other devices and platforms, forming a comprehensive Internet of Things (IoT) ecosystem.
- Cloud Connectivity:Patient data collected by wearables can be securely stored and analyzed in the cloud, supporting efficient diagnosis and treatment decisions.
- Health Data Sharing:Wearables facilitate communication between patients, healthcare providers, and caregivers, enhancing collaborative care.
Minimally Invasive Medical Procedures
- Smart Implants:PCBA technology contributes to developing innovative implants that can monitor, regulate, or stimulate bodily functions internally.
- Precision Surgery:Medical devices with PCBA aid surgeons in performing precise procedures by offering real-time imaging and navigation guidance.
Patient Engagement and Empowerment
- User-Friendly Interfaces:Wearable devices with user-centric interfaces enhance patient engagement, allowing individuals to take an active role in their health management.
- Health Insights:Wearables give users meaningful health insights, encouraging them to make informed lifestyle choices.
Printed Circuit Board Assembly has revolutionized healthcare through medical devices and wearables. These devices empower patients, enable personalized treatment, and provide healthcare professionals with valuable data for informed decision-making. As PCBA technology advances, the potential for innovation in medical devices and wearables remains limitless, driving positive transformations in patient care and the healthcare landscape.
Aerospace Electronics Integration
In the aerospace industry, the integration of advanced Printed Circuit Board Assembly (PCBA) technology has revolutionized aircraft design, performance, and safety. Aerospace electronics, comprising a complex web of systems and components, demand cutting-edge PCBA solutions to ensure reliable communication, navigation, and control. Below, we delve into the significance of PCBA in aerospace electronics integration, featuring key bullet points under relevant subheadings:
Critical Flight Systems
- Avionics Systems:PCBA technology powers avionics systems responsible for navigation, communication, flight control, and monitoring.
- Safety Assurance:Reliable PCBA connections in avionics are crucial for ensuring the safety of passengers and crew during all phases of flight.
High Reliability and Durability
- Extreme Conditions:Aerospace electronics operate in harsh environments, from high altitudes to rapid temperature changes. PCBA solutions must withstand these conditions without compromising performance.
- Vibration Resistance:Aircraft encounter significant vibrations during flight. PCBA technology must provide robust bonding and secure connections to prevent malfunctions.
Reduced Weight and Space
- Compact Design:PCBA integration enables aerospace electronics to be lightweight and space-efficient, optimizing fuel efficiency and overall aircraft performance.
- Miniaturization:Advancements in PCBA technology allow miniaturized components and assemblies, essential for maintaining aerodynamic profiles.
Wireless Communication
- Satellite Connectivity:Aerospace electronics integrate with satellite communication networks, requiring sophisticated PCBA solutions to facilitate reliable data exchange.
- Data Transmission:Wireless communication systems in aircraft rely on high-speed PCBA technology to transmit large volumes of data between aircraft and ground stations.
Mission-Specific Electronics
- Uncrewed Aerial Vehicles (UAVs): PCBA technology drives the integration of sensors, cameras, and control systems in UAVs, enabling various applications from surveillance to scientific research.
- Spacecraft Electronics:PCBA plays a pivotal role in spacecraft, supporting vital systems for propulsion, communication, navigation, and data collection.
Redundancy and Safety Measures
- Redundant Systems:Aerospace electronics often incorporate redundant systems to ensure continued operation in case of component failure. PCBA solutions must accommodate these redundancies.
- Fail-Safe Design:PCBA technology contributes to fail-safe designs in critical aerospace systems, preventing single points of failure and enhancing overall safety.
LED Module Assembly
Printed Circuit Board Assembly (PCBA) has transformed electronic device manufacturing by enabling the creation of intricate and compact circuits. Within this domain, the assembly of LED modules holds a prominent place, catering to a diverse range of applications such as lighting, displays, automotive illumination, and more. LED module assembly involves integrating light-emitting diodes (LEDs) and associated components onto a PCB, demanding advanced techniques and careful considerations.
Precise Component Integration
LED module assembly within the realm of Printed Circuit Board Assembly (PCBA) involves the intricate integration of components to ensure optimal performance and durability. This step encompasses the careful placement and soldering of LEDs, resistors, capacitors, and other essential elements onto the PCB.
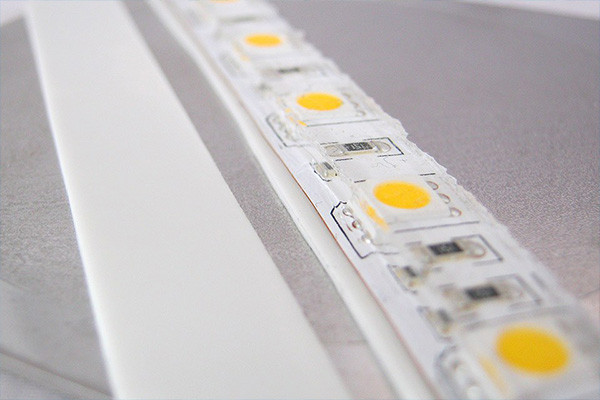
Advanced Soldering Techniques
The assembly process relies heavily on advanced soldering techniques to establish reliable connections between the LED components and the PCB. Surface Mount Technology (SMT) and Through-Hole Technology (THT) soldering methods are pivotal in achieving secure bonds that can withstand thermal stress, mechanical vibrations, and environmental factors.
Thermal Management Considerations
Efficient thermal management is a critical consideration in LED module assembly. The arrangement of LEDs on the PCB should account for heat dissipation to maintain optimal operating temperatures. Heat sinks, thermal pads, and conductive adhesives are employed to enhance thermal conductivity and extend the lifespan of the LEDs.
Automated Assembly for Precision
Automated assembly processes have become indispensable in LED module assembly. These processes ensure precision and consistency in component placement, soldering, and inspection. Mechanical Optical Inspection (AOI) and X-ray techniques are employed to identify potential defects and ensure the quality of the assembled LED modules.
Quality Control and Testing
Throughout the LED module assembly process, we apply stringent quality control measures. We conduct thorough testing procedures, such as functional and burn-in tests, to verify the assembled modules’ performance, electrical characteristics, and overall reliability before integrating them into larger systems or products.
Innovations and Future Trends
LED module assembly continues to see innovations as the LED technology landscape evolves. Miniaturization, improved efficiency, and enhanced integration with smart technologies are shaping the future of LED modules in PCBA.
Underfill Adhesives for Component Protection
In the realm of Printed Circuit Board Assembly (PCBA), the demand for advanced techniques to ensure the reliable performance and durability of electronic components has grown significantly. Underfill adhesives have emerged as a crucial solution to address the challenges posed by the miniaturization of components and the need for enhanced mechanical integrity. These specialized adhesives are pivotal in safeguarding delicate components against mechanical stresses, thermal fluctuations, and environmental factors.
Enhancing Component Reliability
As electronic devices become smaller and more intricate, the risk of mechanical failure increases due to thermal expansion mismatch and mechanical stresses. Underfill adhesives provide a protective barrier by encapsulating the gap between the component and the substrate. This process mitigates stress-induced solder joint fractures and prevents the formation of voids, ensuring consistent electrical connections and prolonging the lifespan of components.
Optimized Thermal Management
Thermal management is a critical consideration in PCBA, as excessive heat can degrade the performance of electronic components. Underfill adhesives with high thermal conductivity facilitate efficient heat dissipation, preventing localized overheating and potential component malfunction. By filling air gaps and promoting direct contact between components and substrates, these adhesives contribute to maintaining optimal operating temperatures.
Coping with Harsh Environments
Environmental conditions like humidity, moisture, and chemical exposure often expose electronic devices to various challenges. Underfill adhesives act as a protective barrier, shielding components from moisture ingress and chemical contaminants. This aspect is particularly significant in automotive, aerospace, and industrial electronics industries, where maintaining reliability under harsh conditions is paramount.
Enabling Miniaturization
By providing mechanical reinforcement and shock absorption, underfill adhesives enable the use of smaller, more delicate components without compromising reliability. This importance is evident in industries where size and weight constraints, such as wearable technology and portable electronics, play a pivotal role.
Underfill adhesives have become indispensable tools in ensuring electronic components’ reliability, longevity, and performance within Printed Circuit Board Assemblies. Their role in enhancing mechanical integrity, thermal management, and environmental protection underscores their significance in modern electronics manufacturing. As technology continues to evolve, the development of advanced underfill adhesive formulations will play a pivotal role in driving the progress of PCBA, meeting the demands of ever-smaller and more powerful electronic devices.
Dispensing Techniques and Automation
In the intricate realm of Printed Circuit Board Assembly (PCBA), the accurate application of adhesives, coatings, and fluids is a critical factor that directly impacts electronic components’ quality, reliability, and overall performance. Dispensing techniques and automation have emerged as indispensable tools in ensuring precision and efficiency throughout the assembly process. This article delves into the pivotal role of dispensing techniques and automation in PCBA, exploring critical aspects under relevant subheadings.
Introduction to Dispensing Techniques
- Diverse Applications:Dispensing techniques encompass a range of processes, including applying adhesives, solder pastes, conformal coatings, underfill materials, and more.
- Precision Focus:The goal of dispensing techniques is to achieve accurate and uniform application, optimizing component adhesion, thermal management, and overall functionality.
Benefits of Automation
- Consistency and Repeatability:Automated dispensing ensures consistent results across production runs, reducing variability and enhancing quality control.
- High Throughput:Automation speeds up the assembly process, increasing production output while maintaining accuracy and reducing human error.
Types of Dispensing Techniques
- Jet Dispensing:Jet dispensing employs rapid bursts of fluid to achieve precise droplet placement, which is ideal for small components and high-density PCBAs.
- Needle Dispensing:Needle dispensing offers controlled application of materials in varying quantities, suitable for adhesive bonding, encapsulation, and coating.
- Screen Printing:A technique for depositing solder paste onto PCBs, vital for surface mount component placement during solder reflow.
Factors Influencing Dispensing Success
- Material Viscosity:Different materials require specific dispensing techniques and equipment due to variations in viscosity and flow characteristics.
- Component Geometry:The shape, size, and orientation of components influence the choice of dispensing method for optimal coverage and precision.
Challenges and Innovations
- Miniaturization:As electronics become smaller and more intricate, dispensing techniques must adapt to accommodate fine pitches and delicate components.
- High-Density PCBAs:Dispensing techniques evolve to address the challenges of densely packed PCB layouts, ensuring accurate placement and coverage.
Dispensing techniques and automation stand as linchpins in the world of Printed Circuit Board Assembly, shaping the final product’s precision, efficiency, and quality. As technology advances and demands for smaller, more intricate PCBAs grow, dispensing techniques and automation become increasingly crucial. By integrating innovative approaches and equipment, the industry continues to elevate the standards of precision and efficiency, ensuring that electronics remain reliable, high-performing, and at the forefront of innovation.
Reliability Testing and Quality Assurance
Reliability Testing and Quality Assurance in Printed Circuit Board Assembly (PCBA) are vital processes that ensure the functionality and durability of electronic devices. These practices play a crucial role in maintaining the performance and longevity of the final product. Here’s a breakdown of the critical points in these processes:
- Environmental Testing:Reliability testing involves subjecting PCBA to various environmental conditions to simulate real-world usage scenarios. Some of the tests involved in this process are temperature cycling, humidity testing, thermal shock, and vibration testing. These tests help identify how the PCBAs perform under different conditions and assess their resilience.
- Functional Testing:Quality assurance entails comprehensive functional testing to verify that the PCBAs meet their design specifications. Ensuring everything works correctly requires separately checking each component, connection, and circuit. Automated testing equipment is often employed to test multiple units efficiently.
- In-Circuit Testing (ICT): ICT involves testing the individual components and connections on the PCB to identify any defects or faults. This process assists in identifying problems such as open circuits, short circuits, and inaccurate component values.
- X-ray Inspection:Manufacturers use X-ray inspection to examine concealed solder joints and connections, especially for surface-mount components that are not easily accessible. Following this process can ensure proper soldering and eliminate the possibility of cold joints or solder bridges.
- Reliability Prediction Models:These models utilize historical data and industry standards to predict the expected reliability of PCBA over its operational lifespan. Identifying potential weak points and making design improvements is aided by this process.
- Accelerated Life Testing:By subjecting PCBAs to accelerated stress conditions, such as higher temperatures and voltage, manufacturers can simulate the aging process and predict their lifespan under normal usage conditions.
- Burn-In Testing:Burn-in testing involves running the PCBAs at elevated temperatures and voltages for an extended period to identify potential defects that might surface over time. Filtering out weak components is crucial to ensure the reliability of the final product.
Reliability Testing and Quality Assurance in PCBA prevent defects from reaching end-users and contribute to product longevity and customer satisfaction. These processes help manufacturers deliver products that perform consistently and are less likely to fail in demanding environments. Manufacturers can ensure that their PCBAs meet the highest quality standards and exhibit superior reliability over time by employing a combination of advanced testing techniques and predictive models.
Environmental Resistance and Durability
Environmental resistance and durability are pivotal to ensuring Printed Circuit Board Assemblies (PCBAs) longevity and functionality. These factors are significant as electronic devices face diverse and often challenging operating conditions. Here are the key points to consider regarding environmental resistance and durability in PCBA:
- Material Selection:Choosing high-quality materials that can withstand temperature variations, humidity, and chemical exposure is fundamental. One must carefully select components such as solder, substrate materials, and conformal coatings to prevent corrosion and degradation.
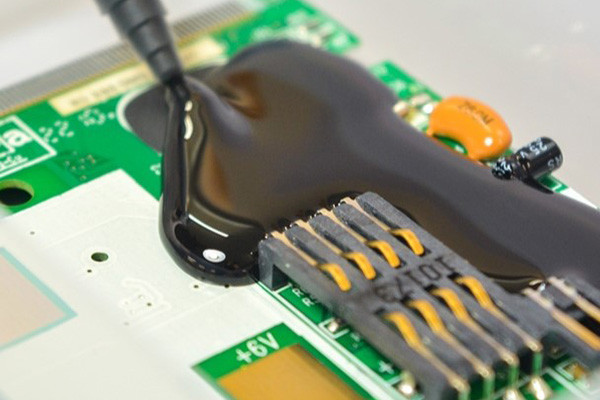
- Conformal Coatings:Applying conformal coatings, which are thin protective layers, safeguards the PCBAs against moisture, dust, and chemical contaminants. These coatings enhance the insulation properties and prevent short circuits, improving overall reliability.
- Encapsulation and Potting:Protecting or encapsulating delicate components in protective compounds protects them from physical stress, moisture, and environmental pollutants. This attribute proves especially useful for devices operating in harsh conditions.
- Sealing and Gasketing:Sealing methods such as gaskets and O-rings offer additional protection against water and dust ingress, making PCBAs suitable for outdoor or rugged environments.
- IP Ratings:Ingress Protection (IP) ratings categorize the level of protection an enclosure provides against solids and liquids. PCBAs designed for outdoor or industrial applications often adhere to specific IP ratings.
- Thermal Management:Efficient heat dissipation mechanisms, such as heat sinks and thermal pads, prevent overheating and extend the operational life of PCBAs.
- Vibration and Shock Resistance:Implementing shock-absorbing mounting techniques and reinforcing solder joints ensure that PCBAs can withstand mechanical stress and vibrations.
Environmental resistance and durability testing involve subjecting PCBAs to rigorous conditions like temperature extremes, humidity, and mechanical shocks. These tests simulate real-world scenarios, enabling manufacturers to identify weak points and design flaws early in development. By ensuring that PCBAs are well-protected against environmental challenges and built to withstand the demands of their intended applications, manufacturers can guarantee the reliability and extended lifespan of electronic devices, ultimately satisfying customer expectations.
Miniaturization and Microelectronics
The fusion of miniaturization and microelectronics has sparked a remarkable transformation in the Printed Circuit Board Assembly (PCBA) field. This synergy has led to the creation of increasingly compact, powerful, and intricate electronic devices. Here are the key points highlighting the impact of miniaturization and microelectronics on PCBA:
- Component Size Reduction:Miniaturization has enabled the production of smaller electronic components without compromising their functionality, allowing for denser PCB layouts.
- High Integration:Microelectronics facilitates integrating multiple functions onto a single microchip, consolidating complex functionalities within a limited space.
- Enhanced Performance:Despite their size, microelectronic components offer improved performance, speed, and energy efficiency, contributing to the overall capabilities of the devices.
- Space-Efficient Designs:Miniaturization allows for creating smaller and sleeker devices, making them more portable and easier to integrate into various applications.
- Challenges and Innovations:The marriage of miniaturization and microelectronics presents challenges in terms of thermal management, signal integrity, and manufacturing precision. Innovations like advanced heat dissipation solutions and high-density interconnects address these challenges.
- Advanced Manufacturing Techniques:Manufacturing PCBAs with miniaturized components demands cutting-edge techniques such as advanced surface mount technology (SMT), fine-pitch assembly, and 3D packaging.
- IoT and Wearables:Miniaturized PCBA components have played a pivotal role in the proliferation of Internet of Things (IoT) devices and wearable technology, enhancing connectivity and data collection.
- Medical Applications:Miniaturization and microelectronics have revolutionized medical devices, enabling implantable monitors, diagnostic tools, and minimally invasive surgical equipment.
The union of miniaturization and microelectronics in PCBA has led to a new era of innovation, ushering in devices once thought to be science fiction. These advancements, from smartphones to medical implants, are reshaping industries and everyday life, exemplifying the remarkable synergy between technology and engineering. As these trends evolve, the possibilities for even more compact, efficient, and sophisticated electronic devices are limitless.
Solder vs. Adhesive in PCBA
In Printed Circuit Board Assembly (PCBA), the choice between solder and adhesive as connection methods holds significant implications for electronic devices’ performance, reliability, and manufacturability. Both techniques serve distinct purposes and offer unique advantages, demanding careful consideration during the design and assembly.
Solder: The Traditional Bonding Agent
Soldering has long been the backbone of PCBA, providing robust and conductive connections between components and PCBs. It involves melting a metal alloy (solder) to create a joint that ensures electrical connectivity and mechanical stability. Soldering offers several benefits:
- Strong Electrical Conductivity:Solder provides low-resistance electrical connections, crucial for maintaining signal integrity and minimizing voltage drops.
- Mechanical Durability:Solder joints are mechanically resilient, capable of withstanding temperature variations, vibrations, and mechanical stress.
- Suitable for Complex Designs:Soldering is ideal for densely populated PCBAs with closely spaced components, allowing for precise connections.
Adhesive: Precision and Flexibility
Adhesive bonding has gained traction as electronics become smaller and more intricate. Adhesives secure components in place without the need for heat, offering distinct advantages:
- Non-Destructive:Adhesives eliminate the potential heat-related damage soldering can cause to sensitive components.
- Flexibility in Component Types:Adhesives can bond a broader range of materials, accommodating components unsuitable for soldering due to heat sensitivity.
- Reduced Weight:Adhesives are lightweight, making them suitable for applications where weight is critical.
Striking the Balance: Considerations for Choosing
The decision between solder and adhesive hinges on various factors, including the application’s requirements, component types, and assembly processes. While soldering offers robust electrical connections, adhesive bonding can be more suitable for delicate components or applications with specific thermal limitations. Ultimately, selecting these two methods underscores the need for a holistic approach considering design, functionality, and reliability.
In the dynamic landscape of PCBA, the choice between solder and adhesive transcends mere technicalities; it shapes the foundation of electronic device manufacturing, influencing their performance, durability, and adaptability to ever-evolving technological demands.
Future Trends in PCBA Adhesive Technology
In the ever-evolving landscape of Printed Circuit Board Assembly (PCBA), adhesive technology is pivotal in ensuring robust connections, efficient thermal management, and overall performance of electronic devices. Industries that demand higher reliability, increased functionality, and enhanced miniaturization are shaping the trajectory of PCBA adhesive technology. This trajectory exhibits several promising trends that set the stage for reshaping how they design and manufacture electronic assemblies.
Advanced Materials for Enhanced Performance
The future of PCBA adhesive technology lies in developing advanced materials with tailored properties. Innovations in nanotechnology and polymer science are giving rise to adhesives that exhibit superior thermal conductivity, electrical insulation, and mechanical strength. These materials will enable more effective heat dissipation, reduce signal interference, and withstand mechanical stresses, further enhancing the longevity and reliability of electronic components.
Miniaturization and High-Density Packaging
As electronic devices continue to shrink, adhesive technology adapts to accommodate the demands of miniaturization and high-density packaging. Future adhesives must balance providing strong bonds and occupying minimal space. This trend drives the exploration of ultra-thin adhesives and innovative bonding techniques, allowing tighter component placement without compromising performance.
Flexibility and Durability for Wearable Technology
The rise of wearable technology presents unique challenges for adhesive technology. Adhesives must demonstrate strong adhesion, flexibility, and durability to withstand the rigors of constant movement and exposure to the elements. Future trends in adhesive technology will likely focus on formulations that maintain reliable bonds even under the dynamic conditions of wearable devices.
Environmentally Friendly Formulations
Sustainability is a growing concern across industries, including electronics. Future adhesive technology will encompass environmentally friendly formulations that minimize the use of harmful chemicals and reduce the overall environmental impact of electronic manufacturing. Biodegradable, low-VOC (volatile organic compound), and solvent-free adhesives will likely become more prevalent in the pursuit of eco-conscious electronics production.
Printed Circuit Board Assembly adhesive stands at the nexus of precision engineering and electronics manufacturing, enabling the creation of compact, efficient, and reliable electronic devices. Its role in ensuring secure component attachment, thermal stability, and electrical connectivity cannot be understated. As technology continues to evolve and consumer demands for more advanced electronics grow, PCBA adhesive will remain instrumental in driving innovation and efficiency. With ongoing research and advancements, the potential for PCBA adhesive to shape the future of electronics manufacturing is undeniable, contributing to the realization of smarter, more interconnected devices that power our modern world.