Industrial Appliance Adhesive Manufacturer: Bonding for Reliability
Industrial Appliance Adhesive Manufacturer: Bonding for Reliability
The industrial appliance adhesive manufacturing industry represents a critical link in the supply chain of industrial appliances, ensuring the reliability, longevity, and performance of these essential devices. Behind the sleek and robust exteriors of industrial appliances, a world of intricate components, complex assemblies, and demanding operational conditions calls for a specialized and dependable bonding solution. Industrial appliance adhesive manufacturers rise to meet this challenge, providing the adhesives that hold, seal, and protect these machines.
We’re going on an adventure, taking a deep dive into the manufacturing of adhesives for industrial appliances. Here, performance and precision are absolute musts. We’re learning about what part adhesives play in industrial machines — their production capabilities, the variety of products created just for that purpose, and the stringent quality standards used to guarantee dependability.
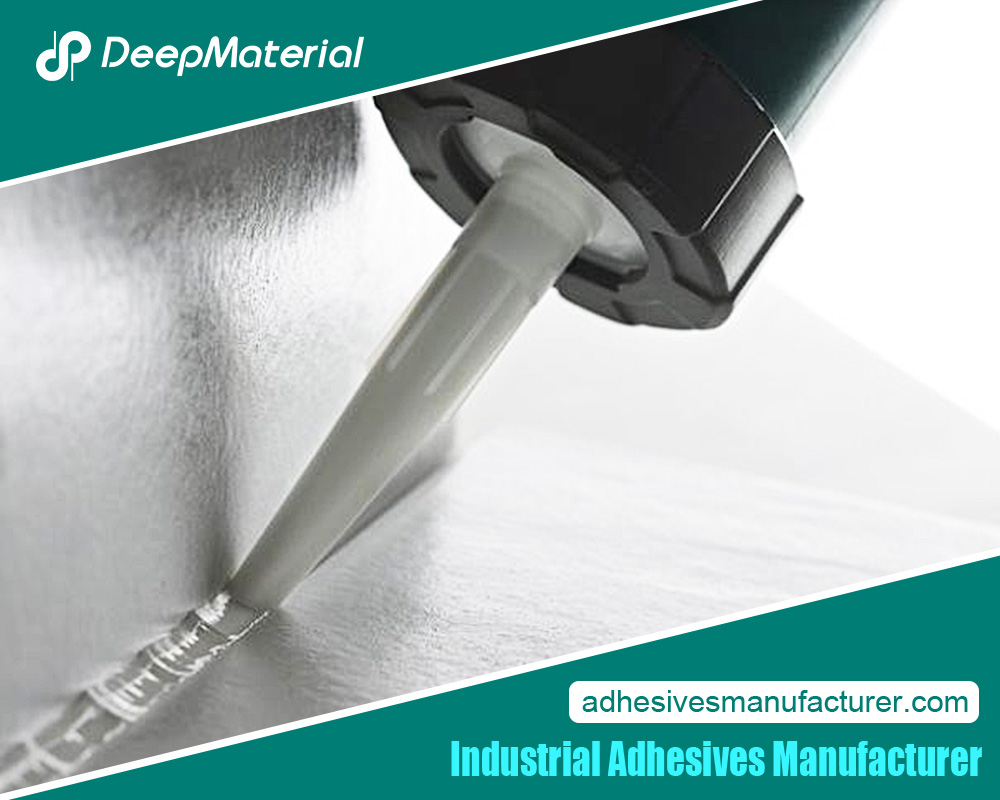
Besides all that, we’ll discover how partnerships promote innovation across the board and examine if it really is possible to be mindful of sustainability in this industry, plus, finally uncovering the real-world impact of reliable adhesive use on industrial gadgets!
The industrial appliance adhesive manufacturing industry is an unsung hero, ensuring the integrity and functionality of devices that underpin a multitude of sectors, from manufacturing and energy to transportation and healthcare. By shedding light on the industry’s core attributes and its vital role in maintaining reliability, we gain a deeper understanding of the intricate world of industrial appliances and the essential role that adhesive bonding plays in their operation.
The Significance of Adhesive Bonding in Industrial Appliances
Adhesive bonding plays an important role in ensuring the reliability, durability, and performance of industrial appliances. The significance of adhesive bonding in this context is multi-faceted and encompasses several key aspects:
- Structural Integrity: Adhesive bonding reinforces the structural integrity of industrial appliances by securely joining various components, such as metals, plastics, and composites. It creates strong bonds that withstand mechanical stress and vibrations, enhancing the appliance’s overall robustness.
- Leak Prevention: Adhesives are instrumental in creating leak-proof seals, which are crucial in applications involving liquids, gases, or chemicals. For instance, in industrial pumps or pipelines, adhesive seals prevent leaks, maintaining safe and efficient operation.
- Thermal Management: In appliances with heating or cooling elements, adhesives are used to attach heat sinks and insulate components. This helps manage temperature fluctuations, ensuring efficient thermal performance and preventing overheating.
- Vibration Dampening: Adhesive bonding can dampen vibrations in industrial appliances, which is vital for the longevity and stability of moving parts. This is particularly significant in devices with rotating or oscillating components.
- Noise Reduction: Adhesive-backed acoustic materials can reduce noise in industrial appliances. This is crucial in environments where noise pollution must be minimized for worker comfort or to comply with regulations.
- Electrical Insulation: Adhesives can be used to insulate electrical components within appliances. Insulating materials and coatings prevent electrical short circuits and ensure the safety of the appliance and its operators.
- Environmental Protection: Industrial appliances often operate in harsh environments. Adhesive seals and coatings protect internal components from exposure to moisture, chemicals, dust, and other ecological factors, prolonging the appliance’s lifespan.
- Weight Reduction: Lightweighting is a critical consideration in many industrial appliances, particularly for applications where portability or energy efficiency is essential. Adhesive bonding allows for the use of lightweight materials without compromising strength.
- Corrosion Resistance: Adhesive coatings and sealants can provide a barrier against corrosion, extending the service life of appliances that may be exposed to corrosive substances.
- Design Flexibility: Adhesives offer design flexibility, enabling manufacturers to create appliances with innovative and streamlined designs. They allow for the bonding of dissimilar materials, facilitating design choices that optimize performance and aesthetics.
- Cost Efficiency: In some cases, adhesive bonding can replace traditional mechanical fasteners, reducing manufacturing costs. This can lead to more cost-effective production without sacrificing performance.
- Adaptability to Complex Shapes: Adhesives can bond irregularly shaped components, which is particularly valuable in appliances with intricate designs or complex geometries.
- Minimized Stress Concentrations: Adhesive joints distribute stresses more evenly across the bonded area, reducing stress concentrations that can lead to component failure.
- Ease of Assembly: Adhesive bonding can simplify the assembly process, as it eliminates the need for drilling holes or creating mechanical fastening points. This streamlines manufacturing and reduces labor costs.
Adhesive bonding is a critical technology that enhances the performance, reliability, and efficiency of industrial appliances. It addresses a wide range of challenges, from structural reinforcement to thermal management, and plays a pivotal role in the functionality and longevity of these essential machines.
The Role of Adhesive Bonding in Ensuring Reliability
Adhesive bonding plays a crucial role in ensuring the reliability of various products and systems across numerous industries. Several key functions and contributions characterize its significance in this regard:
- Structural Integrity: Adhesive bonding reinforces the structural integrity of assemblies by securely joining various materials, such as metals, plastics, composites, and even dissimilar materials. This creates strong and durable bonds that withstand mechanical stress, shock, and vibrations, ensuring the reliability of the overall structure.
- Sealing and Leak Prevention: Adhesive bonding is instrumental in creating reliable seals and preventing leaks. In applications involving liquids, gases, or air, such as automotive and aerospace, adhesives provide leak-proof seals that are crucial for safety, performance, and environmental protection.
- Vibration Dampening: Adhesive bonding can dampen vibrations in mechanical systems, reducing the wear and tear on components and improving reliability. This is especially important in vehicles, industrial machinery, and other equipment where vibration-induced damage can lead to breakdowns.
- Noise Reduction: Adhesives are used to attach acoustic materials that reduce noise levels in products and systems. In industrial and consumer appliances, as well as automotive and construction equipment, noise reduction is essential for improving comfort and safety.
- Electrical Insulation: Adhesive bonding is employed to insulate electrical components and connections, preventing short circuits and ensuring the reliability of electrical systems. This is critical in electronic devices, power distribution, and electrical panels.
- Environmental Protection: Adhesive seals and coatings protect against environmental factors, such as moisture, chemicals, dust, and temperature extremes. By guarding sensitive components and systems from external influences, adhesive bonding contributes to long-term reliability.
- Weight Reduction: Adhesive bonding can replace traditional mechanical fasteners, reducing weight and enhancing fuel efficiency in applications like automotive and aerospace. Lighter components can lead to improved reliability and performance.
- Corrosion Resistance: Adhesive coatings and sealants can offer a barrier against corrosion, extending the service life of components and structures exposed to corrosive environments, such as offshore equipment or infrastructure in coastal regions.
- Design Flexibility: Adhesive bonding provides design flexibility, allowing engineers to create innovative and streamlined products. It enables the bonding of dissimilar materials, which can optimize performance and reliability.
- Cost Efficiency: In some cases, adhesive bonding can reduce manufacturing costs by eliminating the need for mechanical fasteners or drilling holes. This can lead to more cost-effective production without compromising reliability.
- Adaptability to Complex Shapes: Adhesive bonding is particularly advantageous when joining components with complex shapes or irregular geometries. It ensures reliable bonds even in situations where traditional fastening methods may be less effective.
- Minimized Stress Concentrations: Adhesive joints distribute stresses more evenly across the bonded area, reducing stress concentrations that can lead to component failure. This even distribution enhances the reliability of structures and systems.
- Ease of Assembly: Adhesive bonding can simplify the assembly process, reducing labor costs and the risk of assembly errors. This contributes to improved reliability by minimizing human-induced defects.
Final Words
Adhesive bonding is integral to ensuring the reliability of a wide range of products, systems, and structures. Its contributions encompass structural integrity, sealing, insulation, environmental protection, and other critical functions that collectively enhance the durability and dependability of the end product or system.
For more about a complete guide to industrial appliance adhesive manufacturer, you can pay a visit to Deepmaterial at https://www.adhesivesmanufacturer.com/ for more info.