Electronics Adhesive Glue
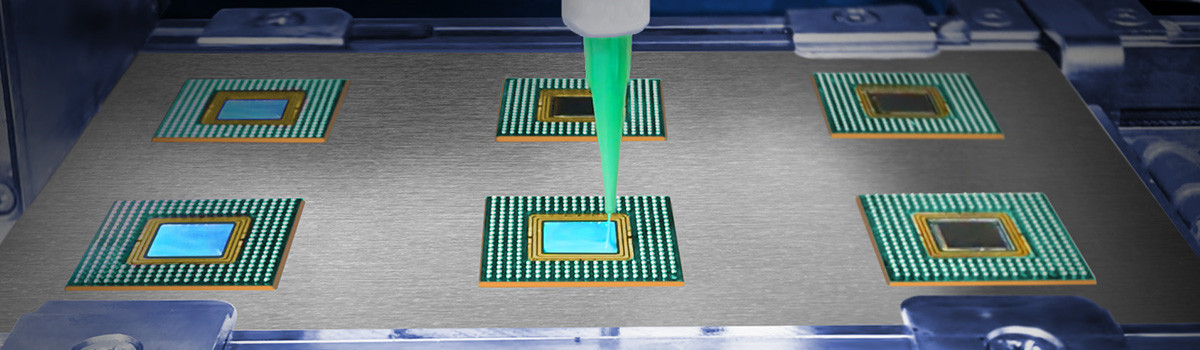
Advanced electronics adhesive glue is revolutionizing electronics manufacturing by enabling the seamless integration of components. This cutting-edge adhesive solution offers unparalleled versatility and robustness, making it an indispensable tool for modern electronics assembly processes. Unlike traditional methods that often involve clunky mechanical fasteners or soldering techniques, this adhesive glue provides a clean, efficient, and highly reliable bonding mechanism. Its ability to securely attach various materials, such as metals, plastics, and ceramics, fosters the creation of intricate electronic devices with enhanced durability.
The empowerment brought by advanced electronics adhesive glue extends beyond just physical integration. Its exceptional thermal and electrical conductivity properties ensure that heat generated by electronic components can be efficiently dissipated, maintaining optimal operational conditions. Moreover, this adhesive promotes miniaturization, allowing for designing and producing smaller, more lightweight devices that conserve space and energy. As industries demand increasingly sophisticated electronics, this adhesive glue is a pivotal enabler, facilitating the development of intelligent gadgets, wearables, and advanced sensor systems that have become integral to modern life.
The impact of advanced adhesive glue is remarkable in consumer electronics, medical devices, automotive technologies, and beyond. It has spurred innovation by enabling the production of flexible and bendable electronics, breaking free from the constraints of rigid designs. This enhances product aesthetics and opens doors to new applications and form factors. As technology continues to evolve, the role of adhesive glue in electronics manufacturing is set to expand, fostering a future where seamless integration is the norm and electronics become more integrated, efficient, and seamlessly woven into the fabric of everyday existence.
What is Advanced Electronics Adhesive Glue, and How Does It Differ from Conventional Adhesives?
Advanced Electronics Adhesive Glue, or electronic adhesive, is a specialized adhesive designed for bonding and securing components in electronic devices and circuits. These adhesives are formulated to meet the unique requirements of electronic applications, which include properties such as electrical conductivity, thermal management, chemical resistance, and mechanical stability.
Here are some key ways in which Advanced Electronics Adhesive Glue differs from conventional adhesives:
- Electrical Conductivity:Many electronic components require electrical connectivity. Advanced electronics adhesives are formulated to maintain conductivity between bonded components, ensuring that electrical signals can flow through the adhesive without significant resistance. Conventional adhesives, on the other hand, are often insulators and can disrupt the functioning of electronic devices.
- Thermal Management:Electronics often generate heat during operation, affecting performance and reliability. Advanced electronics adhesives are engineered to have good thermal conductivity, allowing them to transfer heat away from sensitive components. Conventional adhesives may have different levels of thermal management properties.
- Chemical Resistance:Electronic devices can be exposed to various chemicals, including cleaning solvents, oils, and other substances. Advanced electronics adhesives are designed to resist degradation and maintain integrity when exposed to these chemicals. Conventional adhesives might offer a different level of resistance.
- Mechanical Stability:Electronic components and circuits can experience mechanical stress from vibration, thermal expansion, and shock. Advanced electronics adhesives are formulated to provide strong bonds that can withstand these stresses without compromising the device’s performance. Conventional adhesives might not have the necessary strength and flexibility for these applications.
- Low Outgassing:Some electronic applications, particularly those used in aerospace and vacuum environments, require adhesives with common outgassing characteristics. Advanced electronics adhesives are often formulated to release minimal volatile compounds when exposed to heat or vacuum conditions. This prevents contamination of sensitive components and optics.
- Dielectric Properties:For applications involving insulating or isolating components, advanced electronics adhesives are designed to have specific dielectric properties to prevent unintended electrical coupling between components. Conventional adhesives may not meet these stringent requirements.
- UV Resistance:Some electronics may be exposed to UV radiation, such as outdoors. Advanced electronics adhesives can be formulated to resist UV degradation and maintain their adhesive properties over time.
- Compatibility:Advanced electronics adhesives are prepared to be compatible with various substrate materials commonly used in electronics, such as metals, ceramics, and plastics. Conventional adhesives may provide a different level of compatibility.
How Does Advanced Electronics Adhesive Glue Facilitate Component Bonding?
Advanced electronics adhesive glue facilitates component bonding in electronics manufacturing and assembly. It is a versatile and effective solution for attaching components to printed circuit boards (PCBs) and other substrates. Here’s how advanced electronics adhesive glue facilitates component bonding:
- Strong Adhesion: Advanced electronics adhesive glues are formulated to provide robust and reliable adhesion. They can bond various materials, including metals, plastics, ceramics, and glass, commonly found in electronic components and substrates.
- Surface Compatibility: These adhesives are designed to adhere well to different surface finishes widely found on PCBs and electronic components. They are formulated to work with traditional materials and modern surface treatments, ensuring compatibility and long-lasting bonds.
- Thermal Management: Electronics can generate heat during operation. Advanced adhesive glues often have excellent thermal conductivity, which helps dissipate heat away from sensitive components and prevents overheating, ensuring optimal performance and longevity.
- Electrical Insulation: Adhesive glues used in electronics are typically electrically insulating. This property contains unwanted electrical conductivity between components, possibly leading to short circuits or interference.
- Vibration Dampening: Electronics can be exposed to mechanical vibrations and shocks. Advanced adhesives have the ability to absorb and dampen these vibrations, reducing the risk of damage to delicate components.
- Chemical Resistance: Electronic devices can encounter various chemicals, such as cleaning agents and environmental contaminants. Adhesive glues with chemical resistance help protect members from these potential threats, maintaining their functionality and reliability.
- Flexibility and Stress Absorption: Some electronic components, especially those in portable devices, can experience mechanical stress due to bending or flexing. Flexible adhesive glues can accommodate these movements without compromising the bond, preventing cracks or detachment.
- Precision Application: Electronics adhesive glues are available in various forms, including liquids, gels, and films. This allows for precise application, even in intricate or densely packed electronic assemblies, ensuring proper placement and minimizing waste.
- Low Outgassing: Outgassing refers to releasing volatile compounds from adhesives, which could potentially harm sensitive components or degrade optical surfaces. Advanced electronics adhesive glues are designed to have low outgassing, minimizing the risk of contamination.
- Ease of Processing: Many advanced adhesive glues are designed to be compatible with automated manufacturing processes, such as dispensing systems and pick-and-place machines. This streamlines the assembly process and enhances efficiency.
- Environmental and Regulatory Compliance: Adhesive manufacturers consider environmental and regulatory standards when formulating their products. This ensures that the adhesive glues used in electronics adhere to relevant regulations and minimize the environmental impact.
When is the Ideal Time to Apply Advanced Electronics Adhesive Glue in the Manufacturing Process?
The ideal time to apply advanced electronics adhesive glue in manufacturing can vary depending on the specific requirements of the manufactured electronics, the type of adhesive being used, and the overall assembly process. However, here are some general guidelines to consider:
- Pre-Assembly Preparation: Ensure that all surfaces to be bonded are clean, free from dust, grease, and other contaminants. Proper surface preparation is crucial for achieving solid and reliable bonds.
- Component Placement: In many electronics manufacturing processes, chips, connectors, and other parts are placed onto a substrate or circuit board. Applying adhesive at this stage can help secure these components before proceeding with further assembly steps.
- Selective Coating: Some electronics require conformal coating or cement encapsulation to protect against environmental factors like moisture, dust, and chemicals. This is typically done after the components are placed and soldered onto the board before final testing and sealing.
- Soldering: If the manufacturing process involves soldering, applying adhesive after soldering is essential to prevent interference with the solder joints’ formation and quality. Soldering typically involves high temperatures that could affect the adhesive’s properties.
- Curing Time: Many advanced electronic adhesive glues require a curing or drying process after application. Follow the manufacturer’s curing time and temperature recommendations to achieve the desired bond strength.
- Final Assembly: In some cases, components are attached to a substrate or board using adhesive before the final assembly steps. This can be especially relevant if specific details need to be in a precise position before other parts are added.
- Testing and Inspection: Before applying adhesive, ensure all members are correctly placed and soldered, as any rework after the adhesive application might be challenging.
- Avoiding Contamination: If the electronics involve sensitive components like sensors or optical elements, ensure the tacky application process does not introduce contamination or interfere with their functionality.
- Automation Considerations: An adhesive application might be automated or manual, depending on the manufacturing setup. Consider the compatibility of the adhesive with the chosen application method.
- Process Optimization: It’s advisable to conduct tests and trials to determine the optimal point in the manufacturing process to apply the adhesive. This could involve evaluating bond strength, reliability, and potential impacts on downstream processes.
Ultimately, it’s essential to consult with adhesive manufacturers, process engineers, and other experts in the field to tailor the application process to your specific electronics manufacturing requirements. Adhesive selection, application technique, and timing are critical factors in ensuring the overall quality and reliability of the final electronic product.
Where are the Key Application Areas for Advanced Electronics Adhesive Glue?
Advanced electronics adhesive glues are crucial in applications requiring robust and reliable electronic components and device bonding. Some key application areas for advanced electronics adhesive glue include:
- Printed Circuit Boards (PCBs):Adhesive glues bond components to PCBs, ensuring reliable connections between various parts and the board. They provide electrical insulation, mechanical support, and thermal management.
- Semiconductor Packaging:Adhesive glues are used for die attach and encapsulation in semiconductor packaging processes. They ensure proper heat dissipation and protect delicate semiconductor components from environmental factors.
- Display Technologies:Advanced electronics adhesive glues are used in the assembly of various types of displays, including LCDs, OLEDs, and flexible displays. They enable precise bonding of layers, resulting in improved performance and durability.
- Mobile Devices:These adhesive glues secure components within smartphones and tablets, such as camera modules, batteries, touchscreens, and microchips.
- Automotive Electronics:In the automotive industry, adhesive glues are employed in various electronic components, such as sensors, control modules, and infotainment systems, ensuring vibration resistance and protection from temperature fluctuations.
- Medical Devices:Adhesive glues are used in medical electronics to attach sensors, electrodes, and microfluidic devices to patients or medical equipment.
- Wearable Electronics:With the rise of wearable technology, adhesive glues play a vital role in bonding components to wearable devices like smartwatches, fitness trackers, and medical monitoring devices.
- Aerospace and Defense Electronics:Advanced adhesive glues are used in aerospace and defense applications to ensure reliable bonding of electronic components in harsh and demanding environments.
- Renewable Energy Systems:In solar panels and wind turbines, adhesive glues bond and seal various electronic components, enhancing durability and protection against weather conditions.
- IoT (Internet of Things) Devices:As IoT devices become more prevalent, adhesive glues assemble and secure components within these interconnected devices, ensuring efficient operation and durability.
- Flexible and Stretchable Electronics:Advanced adhesive glues are crucial for bonding components in flexible and stretchable electronics, allowing devices to conform to irregular shapes or stretch without compromising performance.
- Optoelectronics:Adhesive glues assemble optoelectronic devices such as laser diodes, photodetectors, and optical fibers.
- Consumer Electronics:Adhesive glues are used in various consumer electronics, from laptops to gaming consoles, providing structural support and improving device longevity.
- Industrial Electronics:In industrial automation and control systems, adhesive glue bond components in electronic equipment are used in manufacturing and industrial processes.
These are just some key application areas for advanced electronics adhesive glues. As technology evolves, new applications may emerge, highlighting the importance of reliable and versatile adhesive solutions in the electronics industry.
What Are the Benefits of Using Advanced Electronics Adhesive Glue for Seamless Integration?
Using advanced electronics adhesive glue for seamless integration offers several benefits that contribute to electronic devices and systems’ overall performance, reliability, and durability. These adhesives are specifically formulated to meet the unique requirements of the electronics industry. Here are some of the key benefits:
- Bond Strength and Durability:Advanced electronics adhesive glues provide exceptional bond strength, ensuring that components remain securely attached despite various stressors such as temperature fluctuations, vibrations, and mechanical impact. This durability contributes to the overall longevity and reliability of the electronics.
- Seamless Integration:The adhesive’s ability to create strong, precise, and uniform bonds facilitates seamless integration of various components. This is crucial for miniaturized devices where space is limited, as well as for complex assemblies with intricate designs.
- Thermal and Electrical Conductivity:Some advanced electronics adhesives are designed to have excellent thermal and electrical conductivity. This property ensures efficient heat dissipation and electrical connectivity, which prevents overheating and maintains optimal performance.
- Protection from Environmental Factors:Electronics adhesive glues often protect against moisture, chemicals, dust, and other environmental contaminants. This protection helps prevent corrosion, short circuits, and other potential issues from exposure to external elements.
- Reduced Weight and Size:Compared to traditional mechanical fasteners, adhesives are often lighter and take up less space. This is particularly advantageous for lightweight and compact electronic devices, where reducing weight and size is a priority.
- Enhanced Aesthetics:Adhesive bonding can eliminate the need for visible screws or other fasteners on the surface of electronic devices, leading to a cleaner and more aesthetically pleasing appearance.
- Improved Design Flexibility:Adhesive bonding allows for more creative and flexible design options. Using traditional fastening methods, designers can experiment with unconventional shapes, materials, and layouts that might be difficult to achieve.
- Vibration Damping:Electronics adhesive glues can help absorb and dampen vibrations generated by moving parts or external factors. This is particularly beneficial in applications where vibration affects performance or leads to premature failure.
- Ease of Manufacturing:Adhesive bonding can simplify manufacturing processes by reducing the number of components, steps, and tooling required for assembly. This can lead to more efficient production and lower manufacturing costs.
- Reduced Stress Concentrations:Adhesive bonds distribute stress more evenly across the bonded area than traditional fasteners, reducing the risk of stress concentrations that could lead to component failure.
- Compatibility with Various Substrates:Advanced electronics adhesives are formulated to adhere to a wide range of substrates, including metals, plastics, ceramics, and even some flexible materials. This versatility allows for the bonding of different components with varying material properties.
Overall, using advanced electronics adhesive glue for seamless integration offers a holistic approach to designing and manufacturing electronic devices that prioritize performance, reliability, and aesthetics. However, it’s essential to select the correct adhesive formulation based on each application’s specific requirements and environmental conditions.
How Does Advanced Electronics Adhesive Glue Contribute to Miniaturization in Electronics Adhesive Glue?
Advanced electronics adhesive glue plays a crucial role in the miniaturization of electronic devices. Miniaturization refers to making electronic components and devices smaller while maintaining or improving their performance. Adhesive sealants designed explicitly for electronics offer several ways through which they contribute to this miniaturization process:
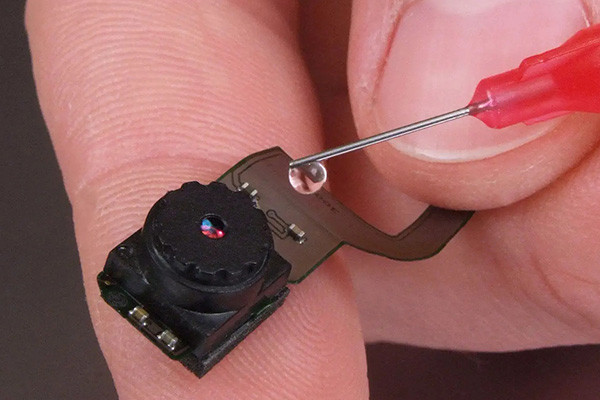
- Reduced Component Size:Traditional methods of connecting electronic components often involve soldering, which requires a certain amount of space for the solder joints. Adhesive glues allow for much smaller and finer connections between members, enabling designers to reduce the device’s overall size.
- Flexibility in Design:Adhesive glues offer more flexibility in designing the layout of electronic components. They can be applied in various shapes and patterns, allowing engineers to optimize the structure for maximum space efficiency and improved performance.
- Weight Reduction:As devices become smaller, their weight is also reduced. This is particularly important in applications such as portable electronics and wearables, where lightweight design is crucial for user comfort and convenience.
- Improved Thermal Management:Miniaturized electronic devices often face challenges with heat dissipation due to the high power density within a small space. Advanced adhesive glues can have thermal conductive properties, helping to efficiently transfer heat away from sensitive components and reducing the risk of overheating.
- Vibration Dampening:In applications where vibrations or mechanical shocks are a concern, adhesive glues can act as dampening materials, reducing the impact of external forces on delicate components. This allows for the design of more reliable and durable devices.
- Integration of Different Materials:Miniaturization often involves integrating various materials, such as semiconductors, metals, and polymers. Advanced adhesive glues can bond different materials, creating complex, multifunctional devices.
- Cost Savings:In some cases, adhesive bonding can simplify manufacturing processes. Soldering, for example, requires careful control of temperature and soldering equipment. Adhesive glues can be applied using automated dispensing systems, potentially reducing manufacturing costs.
- Space Optimization:Adhesive glues can be applied precisely only where needed, eliminating excess material and further contributing to space optimization.
- Protection and Encapsulation:Advanced adhesive glues can protect against environmental factors such as moisture, dust, and chemicals. This encapsulation capability is precious for ensuring the reliability and longevity of miniaturized electronic devices.
- Exemplary Pitch Connections:As electronic components get smaller, the spacing between their connecting pads becomes narrower. Adhesive glues can create reliable connections even in fine-pitch applications, enabling the integration of more features in a limited space.
What Types of Electronic Components Can Be Bonded Using Advanced Electronics Adhesive Glue?
Advanced electronic adhesive glues are designed to provide solid and reliable bonds in various electronic applications. These glues are formulated to withstand the challenges of electronic components, such as temperature fluctuations, vibrations, and exposure to chemicals. Here are some types of electronic components that can be bonded using advanced electronics adhesive glue:
- Surface Mount Components (SMDs):These are small electronic components, such as resistors, capacitors, and integrated circuits, that are mounted directly onto the surface of a printed circuit board (PCB). Adhesive glues hold these components in place before they are sold onto the PCB.
- Connectors and Cables:Adhesive glues can secure connectors, wires, and cables to prevent strain on the solder joints and ensure a reliable electrical connection. This is especially important in applications where lines might experience movement or vibration.
- Heat Sinks:Heat sinks are used to dissipate heat from electronic components that generate a lot of heat, like power transistors and CPUs. Adhesive glues can help attach heat sinks to the components or the PCB, ensuring efficient heat transfer.
- Displays:Advanced adhesive glues can bond display panels, touchscreens, and other displays to the device housing or the main PCB. These glues provide mechanical stability while allowing for the proper functioning of the show.
- LEDs:Light-emitting diodes (LEDs) are often bonded to PCBs using adhesive glues. These glues can help secure LEDs in place and provide electrical insulation.
- Sensors:Various sensors used in electronic devices, such as temperature sensors, motion sensors, and proximity sensors, can be bonded using adhesive glue. The adhesive provides a secure attachment while maintaining the sensor’s accuracy.
- Batteries:Adhesive glues can bond batteries to the device housing or PCB in applications such as smartphones, laptops, and wearables. This ensures the battery stays securely in place.
- Microcontrollers and ICs:In specific applications where shock and vibration resistance are crucial, adhesive glues can attach microcontrollers and integrated circuits to the PCB.
- MEMS Devices:Micro-Electro-Mechanical Systems (MEMS) devices, such as accelerometers and gyroscopes, can be bonded using advanced adhesive glues. These glues allow for precise positioning and secure attachment.
- Flexible Circuits:Adhesive glues can bond flexible circuits (flex PCBs) to rigid or substrates. This is common in applications where the course needs to bend or conform to a particular shape.
It’s important to note that the choice of adhesive glue depends on factors such as the type of components, the materials being bonded, the environmental conditions, and the required bond strength. Different adhesive formulations are available, including epoxy, acrylic, silicone, and polyurethane-based adhesives, each with specific properties that make them suitable for various applications in the electronics industry.
How Does Advanced Electronics Adhesive Glue Ensure Reliability in Harsh Environmental Conditions?
Advanced electronics adhesive glues play a crucial role in ensuring the reliability of electronic devices in harsh environmental conditions. These conditions might include exposure to high or low temperatures, moisture, chemicals, vibrations, and mechanical stress. Electronic reliability in such environments is essential to prevent malfunctions, improve performance, and extend the lifespan of the devices. Here’s how advanced adhesive glues help ensure reliability:
- Chemical Resistance: Harsh environments often involve exposure to various chemicals, including solvents and corrosive substances. Advanced adhesive glues are designed to resist chemical degradation, ensuring that the bond between components remains intact and unaffected by chemical exposure.
- Thermal Stability: Electronic devices can experience extreme temperature fluctuations. Adhesive glues formulated for advanced electronics are engineered to withstand a wide temperature range without losing their adhesive properties. This prevents delamination or weakening of the bond due to thermal expansion and contraction.
- Moisture and Waterproofing: Humidity and moisture can corrode electronic components, leading to malfunctions or failure. Advanced adhesive glues provide water and waterproofing, creating a barrier preventing moisture from reaching sensitive parts.
- Vibration and Shock Absorption: Electronic devices in industrial or automotive settings often face vibrations and mechanical shocks. Adhesive glues with vibration and shock-absorbing properties help distribute mechanical stress throughout the bonded area, reducing the risk of component detachment or damage.
- Flexibility and Durability: Advanced adhesive glues balance flexibility and durability. This enables them to accommodate the expansion and contraction of components under different conditions, such as temperature variations, without causing bond failure.
- Electrical Insulation: Adhesive glues used in electronics need good electrical insulation properties. This prevents short circuits and leakage currents from direct contact between conductive components.
- Long-Term Stability: Electronics often need to perform reliably over an extended period. The adhesive glues are formulated to maintain their strength and other properties over time, preventing the bond from deteriorating with age.
- Adhesion to Diverse Substrates: Advanced adhesive glues are formulated to adhere well to various substrates commonly found in electronic devices, such as metals, plastics, ceramics, and glass. This ensures a strong and consistent bond between different materials.
- Testing and Certification: Manufacturers of advanced adhesive glues often subject their products to rigorous testing in simulated harsh conditions. These tests include thermal cycling, humidity exposure, and chemical resistance tests. Adhesive sealants that meet industry standards and pass these tests are more likely to ensure reliability in real-world applications.
- Customized Formulations: Different electronic applications have unique requirements. Some adhesive manufacturers offer customized formulations tailored to specific environments and applications, further enhancing reliability.
When Should One Opt for Thermally Conductive Electronics Adhesive Glue?
Thermally conductive electronics adhesive glue is specifically designed to address electronic assemblies’ heat dissipation and bonding requirements. It is used when there is a need to efficiently transfer heat away from sensitive electronic components to ensure proper functioning and longevity. Here are some scenarios when opting for thermally conductive adhesive glue would be beneficial:
- Heat Management in Electronic Assemblies:Electronic components generate heat during operation. If this heat is not adequately dissipated, it can lead to performance degradation, reduced lifespan, or even failure of the details. Thermally conductive adhesive glue helps establish a solid thermal path between components and heat sinks or other dissipative surfaces, allowing the heat to be efficiently conducted away.
- Bonding and Heat Transfer:Thermally conductive adhesive glue provides effective heat transfer and a bonding solution. It securely attaches electronic components to heat sinks, chassis, or other surfaces, ensuring mechanical stability and heat dissipation.
- Compact Designs:Space is at a premium in many modern electronic devices. Due to size constraints, traditional methods of attaching heat sinks, such as screws or clips, might not be feasible. Thermally conductive adhesive glue can provide a more compact and versatile solution, effectively managing heat in confined spaces.
- Avoiding Mechanical Stress:Screwed or clipped-on heat sinks can sometimes exert mechanical stress on delicate electronic components or lead to uneven pressure distribution. Adhesive glue offers a more uniform and gentle attachment method, reducing the risk of damage.
- Enhanced Thermal Performance:Unlike traditional thermal interface materials like pads or greases, thermally conductive adhesive glue can offer improved thermal conductivity. This is particularly useful in high-performance applications where superior heat dissipation is essential.
- Vibration and Shock Resistance:Devices exposed to vibrations or shocks can experience loosening of traditional attachment methods over time. Thermally conductive adhesive glue provides a secure, vibration-resistant bond that can withstand various environmental conditions.
- Sealing and Insulation:Some adhesive glues also offer sealing and insulation properties, protecting electronic components from moisture, dust, and contaminants while facilitating efficient heat transfer.
It’s important to note that while thermally conductive adhesive glue can offer numerous advantages, choosing the right type of adhesive for your specific application is essential. Factors to consider include the thermal conductivity of the cement, its viscosity for proper application, compatibility with the materials being bonded, curing time, and operating temperature range.
Where Does Flexible Electronics Adhesive Glue Adhesive Find its Applications?
Flexible electronics adhesive glue finds a wide range of applications due to its ability to bond flexible and bendable electronic components to various surfaces. Some of the standard applications include:
- Flexible Displays:Adhesive glue attaches flexible OLED, LED, or LCDs to substrates, such as plastic or adjustable glass. These displays are utilized in smartphones, wearable devices, curved TVs, and more.
- Wearable Devices:Adhesive glue is crucial in assembling components like sensors, batteries, and circuitry in wearable devices such as smartwatches, fitness trackers, and electronic textiles.
- Medical Devices:Flexible adhesive glue is employed in medical devices like skin patches, smart bandages, and medical wearables. These devices can monitor vital signs, drug delivery, and patient data.
- Automotive Electronics:Flexible adhesive glue helps secure flexible touch panels, curved displays, and other flexible electronics in automotive dashboards, infotainment systems, and instrument clusters.
- Innovative Packaging:Adhesive glue can attach electronic components to packaging materials, allowing for interactive packaging that displays information or interacts with consumers.
- Flexible Sensors:Various types of sensors, like pressure sensors, temperature sensors, and strain sensors, can be integrated into flexible structures using adhesive glue. These sensors are used in robotics, health monitoring, and environmental sensing applications.
- Flexible Solar Panels:Adhesive glue is used to bond flexible solar cells onto different surfaces, enabling the integration of solar panels into unconventional forms and structures.
- Foldable Devices:For devices with foldable or bendable designs, such as foldable smartphones and tablets, adhesive glue is essential in maintaining structural integrity during repeated folding and unfolding.
- Electronic Skins (E-skins):These are thin, flexible electronic devices that can be applied directly to the skin or other surfaces. Adhesive glue is used to secure sensors, microcontrollers, and other components.
- Consumer Electronics:Adhesive glue is used in various consumer electronics, including e-readers, flexible keyboards, and speakers.
- Aerospace and Defense:Flexible electronics are increasingly used in aerospace applications due to their lightweight and space-saving properties. Adhesive glue attaches components in satellites, UAVs (drones), and other aerospace systems.
- Textiles and Fashion:Adhesive glue can be utilized in electronic materials (e-textiles) to attach LEDs, conductive threads, and other electronic components onto fabrics, enabling wearable technology integration into clothing.
- Energy Storage Devices:Flexible adhesive glue can attach components to flexible batteries and energy storage devices.
- Human-Machine Interfaces:Flexible adhesive glue helps integrate touch sensors and haptic feedback devices into various surfaces, creating interactive and tactile user interfaces.
These are just a few examples of the diverse applications of flexible electronic adhesive glue. As technology advances, the range of applications will expand even further.
What Role Does Surface Preparation Play in Achieving Optimal Adhesion with Advanced Electronics Adhesive Glue?
Surface preparation is critical in achieving optimal adhesion when using advanced electronics adhesive glue. The effectiveness of an adhesive bond is highly dependent on the quality of the substrate’s surface and its interaction with the adhesive material. Surface preparation involves a series of steps designed to clean, activate, and enhance the substrate’s surface properties, ensuring strong and durable adhesion. Here’s how surface preparation impacts adhesion:
- Contaminant Removal:Surfaces need to be free from any contaminants such as dust, dirt, oils, grease, moisture, and oxidation. These contaminants can create barriers that prevent the adhesive from directly contacting the substrate. Cleaning the surface thoroughly ensures the sealant can bond directly to the substrate without interference.
- Surface Activation:Many advanced adhesive glues require proper surface activation to enhance the chemical interactions between the adhesive and the substrate. Activation methods may include plasma treatment, corona treatment, or chemical primers. Activation helps to improve wetting, increase surface energy, and create reactive sites on the substrate, which promotes better adhesion.
- Surface Roughening:In some cases, achieving a slightly roughened surface can improve adhesive bonding. This can be accomplished through sanding, abrasive blasting, or chemical etching. A roughened surface provides more contact points for the adhesive, increasing the overall adhesive strength.
- Surface Compatibility:The surface preparation method chosen should be compatible with the adhesive and the substrate material. Some materials may be sensitive to specific cleaning agents or activation methods, potentially leading to material damage or poor adhesion.
- Uniformity:Consistency in surface preparation is crucial to achieving uniform adhesion across the bonded area. Uneven surface preparation can lead to localized weak spots, reducing the overall strength of the bond.
- Adhesive Spreading:Proper surface preparation can also facilitate the uniform spreading and wetting of the adhesive across the substrate. This is important for preventing air pockets, voids, and inconsistencies in the adhesive layer, which could weaken the bond.
- Durability:A well-prepared surface contributes to the durability and longevity of the adhesive bond. In electronic applications, where thermal cycling, vibration, and other stressors are expected, a strong initial bond is essential for maintaining the integrity of the electronics assembly.
- Adhesive Selection:The adhesive chosen for a specific application can influence the required surface preparation. Some adhesives are more forgiving regarding surface quality, while others demand meticulous preparation for optimal performance.
How Does Advanced Electronics Adhesive Glue Enable High-Speed Electronic Circuitry?
Advanced electronics adhesive glue plays a crucial role in enabling high-speed electronic circuitry by providing key benefits that enhance the performance and reliability of electronic devices operating at high frequencies. Here are some ways in which advanced adhesive glues contribute to high-speed electronic circuitry:
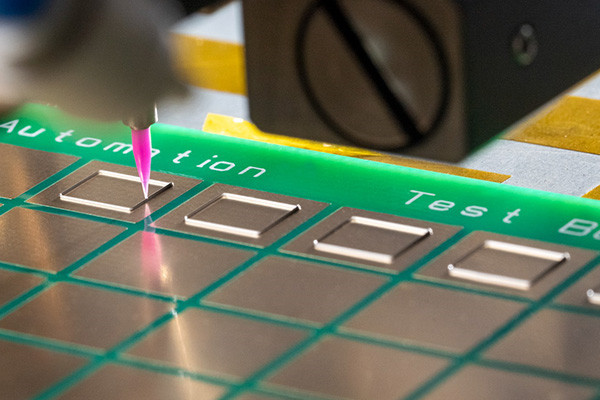
- Signal Integrity and Transmission:High-speed electronic circuitry often involves the transmission of signals at very high frequencies. The adhesive used to bond components must have minimal impact on signal integrity. Advanced adhesive glues are formulated to have low dielectric constants and low loss tangent values, which help to reduce signal distortion, attenuation, and phase shift. This ensures that high-frequency signals can be transmitted with minimal degradation.
- Reduced Parasitic Effects:As electronic components become smaller and closer together in high-speed circuits, parasitic effects such as capacitance, inductance, and crosstalk become more significant. Advanced adhesive glues with controlled electrical properties help minimize these effects by providing consistent insulation and spacing between components.
- Thermal Management:High-speed electronic components generate heat, and effective thermal management is crucial to prevent overheating and maintain optimal performance. Advanced adhesive glues can have excellent thermal conductivity properties, enabling efficient heat transfer from the components to heat sinks or other cooling mechanisms. This helps to prevent thermal throttling and ensures consistent performance.
- Miniaturization and Packaging:High-speed electronic circuits often require compact and densely packed designs. Advanced adhesive glues can be applied in thin, uniform layers that accommodate the miniaturization of components and the proximity of traces, vias, and pads. This precision in adhesive application helps maintain proper electrical isolation and reduces the risk of short circuits.
- Reliability Under Stress:Advanced adhesive glues are engineered to withstand the mechanical stresses and temperature fluctuations that high-speed electronic circuits can experience. They provide strong and durable bonds that resist delamination, cracking, and fatigue, ensuring the reliability of the circuitry even during thermal cycling and mechanical vibrations.
- Compatibility with Substrates:High-speed electronic circuits often use advanced substrates such as flexible materials, ceramics, and composite structures. Advanced adhesive glues are designed to adhere to a wide range of substrate materials, ensuring compatibility and proper adhesion regardless of the substrate’s properties.
- Ease of Application:Advanced adhesive glues are available in various forms, including liquid dispersions, films, pastes, and preforms. This versatility allows precise and controlled application methods, such as dispensing, screen printing, or lamination, to achieve the desired adhesive thickness and coverage.
- RF and Microwave Applications:Advanced adhesive glues with specific electrical and electromagnetic properties are used for applications involving radio frequency (RF) and microwave frequencies. These adhesives minimize signal loss and interference, making them suitable for antennas, RF filters, and other high-frequency components.
What Innovations are on the Horizon for Next-Generation Electronics Adhesive Glue?
Here are some possible innovations:
- Nanotechnology-Enhanced Adhesives:Researchers are exploring the integration of nanomaterials into adhesive formulations to enhance properties like thermal conductivity, electrical conductivity, and mechanical strength. Carbon nanotubes, graphene, and other nanomaterials could create adhesives with improved heat dissipation and conductivity for high-performance electronic devices.
- Flexible and Stretchable Adhesives:The trend towards flexible and wearable electronics has led to a need for adhesives that can maintain strong bonds even in flexible and stretchable substrates. Next-generation adhesives might have improved elasticity and adhesion to accommodate these unique requirements.
- Self-Healing Adhesives:Researchers are working on self-healing adhesives, meaning they can repair small cracks or damage on their own. This could significantly extend the lifespan and reliability of electronic devices by preventing damage propagation.
- Advanced Thermal Management:With the increasing power density of electronic components, thermal management is becoming more critical. Next-generation adhesives might offer better thermal conductivity and insulation properties to dissipate heat and prevent overheating effectively.
- Enhanced Dielectric Properties:Adhesives with improved dielectric properties, such as lower dielectric constants and reduced loss tangents, could further enhance signal integrity in high-frequency and high-speed electronic circuits.
- Printable Adhesives:Printing technologies are advancing rapidly. Printable adhesive formulations could enable precise deposition of adhesive materials on complex circuit patterns, allowing for efficient and cost-effective manufacturing processes.
- Bio-Based and Environmentally Friendly Adhesives:There’s a growing demand for eco-friendly solutions in electronics manufacturing. Next-gen adhesives might incorporate more sustainable and biodegradable materials while maintaining performance standards.
- Adhesives for Advanced Substrates:As electronic devices evolve with new materials and designs, adhesives must adapt. Innovations might include bonds tailored to flexible, transparent, or composite substrates.
- Innovative Adhesives:Adhesives that provide additional functionality, such as sensors, conductive pathways, or even data storage capabilities, could open up new possibilities for electronics design and functionality.
- AI-Optimized Adhesive Formulations:Artificial intelligence could analyze complex data on adhesive performance, substrate properties, and environmental conditions to optimize adhesive formulations for specific applications.
- In-Situ Curing and Activation:Adhesives that can be activated or cured in response to specific environmental conditions (e.g., heat, light, humidity) could simplify manufacturing processes and enhance adhesive performance.
Remember that these are speculative possibilities based on trends and ongoing research. To get the most accurate and up-to-date information, it’s recommended to consult recent research papers, industry news, and experts in the field of electronics adhesives.
When and Why is Underfill Electronics Adhesive Glue Adhesive Used in Chip Packaging?
Underfill electronics adhesive glue is used in chip packaging to enhance semiconductor devices’ mechanical integrity, reliability, and thermal performance, particularly in applications where the chips are subject to mechanical stresses, temperature cycling, and other harsh conditions. Underfill adhesive is typically applied to fill the gap between the chip and the substrate (such as a printed circuit board or another package), encapsulating the chip’s connections and providing reinforcement. Here’s when and why underfill adhesive is used:
When is Underfill Adhesive Used:
- Flip-Chip Packaging:The semiconductor chip is attached to the substrate in flip-chip packaging. This arrangement allows for more direct electrical connections but creates a small gap between the chip and the substrate due to solder or micro bumps. Underfill adhesive is used to fill this gap and provide mechanical support.
- BGA (Ball Grid Array) Packages:BGA packages have an array of solder balls on the bottom of the chip that connects to corresponding pads on the substrate. Underfill adhesive is often applied to improve the structural integrity of these connections and reduce the risk of mechanical and thermal stress-related failures.
- High-Temperature Applications:Semiconductor devices operating in high-temperature environments can experience significant thermal expansion and contraction, leading to potential reliability issues. Underfill adhesive helps to counteract these stresses and prevent solder joint fatigue.
- Harsh Environments:Underfill adhesive benefits applications exposed to extreme conditions such as vibration, shock, humidity, and temperature cycling. It helps prevent the development of cracks and voids in the solder joints that could lead to premature failure.
Why is Underfill Adhesive Used:
- Stress Relief:The difference in coefficients of thermal expansion (CTE) between the chip and the substrate can cause mechanical stress on solder joints during temperature changes. Underfill adhesive reduces this stress by distributing the mechanical load more evenly.
- Enhanced Reliability:Underfill adhesive encapsulates the solder connections, providing a protective barrier against moisture, contaminants, and physical damage. This improves the overall reliability and lifespan of the semiconductor device.
- Improved Thermal Performance:Underfill adhesive with good thermal conductivity can help dissipate heat from the chip, improving the device’s thermal performance and reducing the risk of overheating.
- Vibration and Shock Resistance:Underfill adhesive reinforces the solder joints and prevents movement within the package due to vibrations or mechanical shocks, reducing the likelihood of solder joint fractures.
- Thermal Cycling Resistance:As devices experience temperature cycling from operational and idle states, solder joints can weaken over time. Underfill adhesive mitigates the impact of thermal cycling, reducing the risk of fatigue-related failures.
- Minimized Warpage:Underfill adhesive can help minimize package warpage caused by CTE mismatches, ensuring consistent electrical connections and preventing stress on other components.
Where Does UV-Curing Electronics Adhesive Glue Excel in Electronics Adhesive Glue Manufacturing?
UV-curing electronics adhesive glue excels in electronics adhesive glue manufacturing primarily due to its fast and efficient curing process. Here are some specific areas where UV-curing adhesive glue stands out:
- Rapid Curing:UV-curing adhesive glue cures almost instantly when exposed to ultraviolet (UV) light. This drastically reduces the curing time compared to traditional adhesive curing methods that might require heat or extended periods for drying.
- Precision Bonding:The quick curing process allows for precise and controlled bonding of electronic components. This is crucial in electronics manufacturing, where small and delicate parts must be accurately placed and bonded.
- Reduced Heat Exposure:Unlike heat-curing adhesives that may subject sensitive electronic components to high temperatures, UV-curing adhesive glue does not generate excessive heat during curing. This helps prevent damage to heat-sensitive components.
- Improved Throughput:The rapid curing of UV-curing adhesive glue increases production throughput. Manufacturers can process more units in a shorter time, leading to higher efficiency and reduced manufacturing lead times.
- Lower Energy Consumption:UV-curing adhesive glue does not require prolonged heating, which can consume significant energy. This makes it a more energy-efficient option in electronics manufacturing.
- Minimal Volatile Organic Compounds (VOCs):UV-curing adhesive glues are often formulated with lower VOC content than solvent-based adhesives, contributing to a healthier work environment and reduced emissions.
- Strong Bonds:UV-curing adhesive glues can strengthen bonds with various substrates commonly found in electronics manufacturing, including plastics, metals, ceramics, and glass.
- Less Need for Clamps or Fixtures:The fast curing time reduces the need for clamps or fixtures to hold components in place during the curing process. This simplifies the assembly process and can lead to cost savings.
- Enhanced Aesthetics:UV-curing adhesive glues often produce clean, clear bonds without visible residues or discoloration. This can be important for applications where the appearance of the final product matters.
- Adaptable Formulations:UV-curing adhesive glues can be formulated to meet specific requirements, such as flexibility, conductivity, thermal conductivity, or resistance to environmental factors like moisture, heat, and chemicals.
However, it’s important to note that UV-curing adhesive glues may not be suitable for all types of electronics manufacturing. For instance, components that are not transparent to UV light may not cure properly, and intricate designs with shadowed areas might not receive adequate UV exposure. Manufacturers need to consider the specific requirements of their products and processes before adopting UV-curing adhesive glues in their manufacturing workflows.
How Can Advanced Electronics Adhesive Glue Enhance Vibration and Shock Resistance?
Advanced electronics adhesive glues can enhance vibration and shock resistance in electronic devices by providing a robust and flexible bond between components, dampening vibrations, and absorbing shocks. Here’s how they achieve this:
- Strong Bonding:Advanced adhesive glues are formulated to create strong bonds between different materials, such as metals, plastics, ceramics, and glass commonly found in electronic devices. A strong bond ensures that components remain securely attached, reducing the risk of detachment due to vibrations or shocks.
- Flexibility:These adhesives often have a certain degree of flexibility and elasticity. When components experience vibrations or shocks, the bond can absorb some energy and distribute it across the adhesive joint. This flexibility prevents the direct transfer of excessive forces to the components, reducing the risk of damage.
- Damping Properties:Some advanced adhesive glues have inherent damping properties, which can absorb and dissipate vibrations and shocks. This helps reduce the intensity and duration of vibrations that could potentially harm sensitive electronic components.
- Vibration Isolation:Adhesive glues with vibration isolation properties help decouple different parts of an electronic device from each other. By forming a barrier between components, these adhesives prevent the propagation of vibrations from one piece to another, protecting them from damage and ensuring optimal performance.
- Stress Distribution:Electronics adhesive glues with optimized rheological properties ensure even stress distribution across the bonded surfaces. This prevents concentrated stress points that could result in cracking or detachment during vibrations or shocks.
- Temperature Resistance:Many advanced adhesive glues are engineered to withstand a wide range of temperatures, ensuring that the adhesive’s properties remain consistent even when the device experiences temperature fluctuations due to operational or environmental conditions.
- Chemical Resistance:Electronic devices often encounter various chemicals and environmental factors. Advanced adhesive glues can resist chemicals, moisture, and other environmental factors that might compromise the adhesive’s integrity under vibration or shock conditions.
- Custom Formulations:Manufacturers can tailor the adhesive formulations to match the specific requirements of the electronic device. This includes considerations such as the materials being bonded, the expected level of vibrations and shocks, and the device’s operating conditions.
- Application Techniques:Proper application techniques, including controlled curing processes, enhance the adhesive’s performance further. Manufacturers may utilize specific curing methods to achieve the desired level of flexibility and strength in the adhesive joint.
- Testing and Certification:Adhesive glues used in electronic devices often undergo rigorous testing and certification processes to ensure their effectiveness in enhancing vibration and shock resistance. These tests simulate real-world scenarios and ensure that the adhesive meets industry standards for durability and reliability.
Incorporating advanced electronics adhesive glues with these properties into the design and manufacturing processes can significantly enhance electronic devices’ vibration and shock resistance, ultimately extending their lifespan and improving their reliability.
What Factors Impact the Shelf Life of Advanced Electronics Adhesive Glue?
Several factors, intrinsic to the adhesive and external environmental conditions, can influence the shelf life of advanced electronics adhesive glue. Here are some key factors that impact the shelf life of electronic adhesive glue:
1.Chemical Composition:The adhesive formulation plays a significant role in determining its shelf life. Adhesives with complex chemical compositions or those containing reactive components may have a shorter shelf life due to the potential for chemical reactions to occur over time.
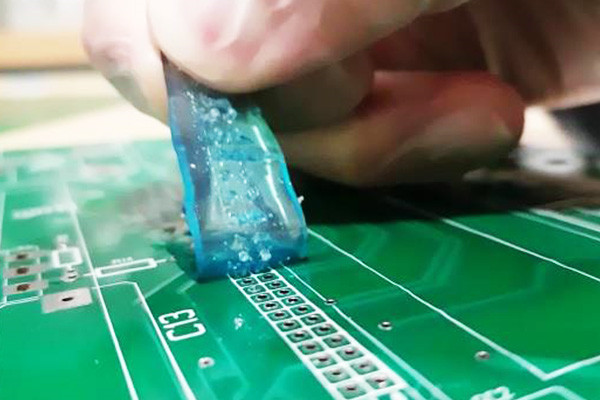
2.Moisture Sensitivity:Many advanced electronic adhesive glues are sensitive to moisture. Exposure to high humidity levels can cause the adhesive to absorb water, leading to reduced performance and shorter shelf life. Proper moisture barrier packaging is essential to protect the bond.
3.Temperature:Temperature is a critical factor affecting adhesive glue’s shelf life. High and low temperatures can cause the adhesive to degrade, cure prematurely, or change viscosity. Adhesive manufacturers usually provide recommended storage temperature ranges.
4.Light Exposure:Some adhesives are sensitive to ultraviolet (UV) light exposure, which can lead to chemical degradation and reduced performance. Adhesives should be stored in opaque containers to protect them from light.
5.Air Exposure:Oxygen and other gases in the air can react with the adhesive’s components, leading to changes in the adhesive’s properties. Proper sealing and storage in air-tight containers are essential to minimize such reactions.
6.Packaging:The quality of the packaging materials used for storing the adhesive can impact its shelf life. Packaging should provide an effective barrier against moisture, light, and air to ensure the adhesive remains stable.
7.Curing Agents and Catalysts:Some adhesives require curing agents or catalysts to achieve their intended properties. These components can have their own shelf lives and impact the adhesive’s overall shelf life when mixed.
8.Storage Conditions:Adhesive manufacturers often provide recommended storage conditions such as temperature and humidity ranges. Deviating from these recommended conditions can accelerate the degradation of the adhesive and reduce its shelf life.
9.Contamination:Contaminants such as dust, dirt, or foreign particles can degrade the quality of the adhesive and affect its performance over time. Proper handling and storage can help prevent contamination.
10.Chemical Stability:Adhesives that are more chemically stable tend to have longer shelf lives. Factors like stabilizers, inhibitors, and antioxidants in the formulation can contribute to improved chemical stability.
11.Batch-to-Batch Variability:Some adhesive formulations might have batch-to-batch variability, influencing their shelf life. Manufacturers typically conduct stability testing on representative batches to determine the expected shelf life.
It’s important to note that the specific shelf life of a given electronics adhesive glue can vary depending on the manufacturer, formulation, and intended use. Always refer to the manufacturer’s guidelines and recommendations for proper storage and usage to maximize the adhesive’s effectiveness and shelf life.
When is Conductive Electronics Adhesive Glue Adhesive Preferred for EMI/RFI Shielding?
Conductive electronic adhesive glue is preferred for EMI/RFI shielding when electrical conductivity, adhesive properties, and shielding effectiveness are required in electronic devices or applications. EMI (Electromagnetic Interference) and RFI (Radio Frequency Interference) are electromagnetic emissions that can negatively impact the performance of electronic devices or systems. EMI/RFI shielding helps prevent these emissions from interfering with the normal functioning of electronics.
Conductive adhesive glues are often preferred for EMI/RFI shielding under the following circumstances:
- Complex Geometries:Conductive adhesive glues can be more practical than traditional metal shielding methods in electronic devices with intricate or irregular shapes. The sticky nature of these glues allows them to conform to various conditions and adhere to surfaces that might be difficult to cover using other methods.
- Lightweight and Space-Saving:Conductive adhesive glues are generally light and have a lower profile than metal shielding solutions like enclosures or metal plates. This is particularly useful in applications where weight and space are critical, such as mobile devices, aerospace electronics, and wearable technology.
- Flexibility and Durability:Electronic components or devices that undergo frequent movements or vibrations can benefit from conductive adhesive glues, as they offer flexibility and durability. These glues can maintain conductivity even when subjected to mechanical stresses, making them suitable for applications like flexible circuits or connectors.
- Electrical Insulation:Conductive adhesive glues can provide both electrical conductivity and insulation, essential when shielding certain parts of a device or circuit from electromagnetic interference while allowing other parts to remain isolated. This can be crucial for preventing cross-talk between components.
- Easy Application:Conductive adhesive glues can be applied using various methods such as screen printing, dispensing, or even manual application. This ease of application makes them suitable for high-volume manufacturing processes and prototype development.
- Cost-Effectiveness:In many cases, conductive adhesive glue can be more cost-effective than traditional metal shielding methods. They eliminate the need for additional metal parts or complex manufacturing processes, reducing production costs.
- Compatibility with Various Substrates:Conductive adhesive glues can often be used on various substrates, including plastics, ceramics, metals, and glass, making them versatile for various electronic applications.
- RF Transparency:Some conductive adhesive glues are designed to be RF-transparent, allowing specific radio frequencies to pass through while shielding against others. This can be advantageous in applications where wireless communication or signal transmission is essential.
It’s important to note that the choice of EMI/RFI shielding method depends on the application’s specific requirements, including the desired level of shielding effectiveness, the operating environment, and the materials involved. Conductive adhesive glues might be preferred in situations where their unique combination of properties aligns well with the needs of the electronic device or system.
Where Does Advanced Electronics Adhesive Glue Fit in the Evolution of Wearable Technology?
Advanced electronics adhesive glue plays a significant role in the evolution of wearable technology by enabling the development of more functional, comfortable, and durable wearable devices. As wearable technology continues to evolve, adhesive glues with specialized properties are essential for addressing wearable devices’ unique challenges and requirements. Here’s how advanced electronics adhesive glue fits into the evolution of wearable technology:
- Miniaturization and Flexibility:Wearable technology has seen a trend toward miniaturization and flexibility. Advanced adhesive glues allow tiny components and sensors to bond onto flexible substrates like textiles or elastomers. These glues provide a secure attachment while maintaining the device’s flexibility, which is crucial for comfort and usability.
- Integration of Components:Wearables often incorporate electronic components such as sensors, microcontrollers, batteries, and displays. Advanced adhesive glues facilitate the integration of these components onto different materials, ensuring proper electrical connections and mechanical stability. This integration contributes to the sleek and discreet design of wearable devices.
- Conformal Bonding:To function optimally, wearable devices must adhere closely to the wearer’s body or clothing. Advanced adhesive glues offer conformal bonding, allowing the device to maintain consistent contact with the skin or clothing. This is important for accurate sensor readings, consistent data collection, and user comfort.
- Water and Sweat Resistance:Wearable devices are often exposed to moisture, sweat, and occasional immersion. Advanced adhesive glues designed to be water-resistant or waterproof protect the internal electronics, ensuring the device’s reliability and longevity even in challenging environments.
- Skin-Friendly Adhesives:Wearable health and medical devices often require direct skin contact. Skin-friendly adhesive glues are designed to be hypoallergenic, non-irritating, and comfortable for extended wear. These adhesives enable the development of devices worn for continuous health monitoring or therapeutic purposes.
- Flexible Circuits and PCBs:Flexible circuits and printed circuit boards (PCBs) are standard in wearable technology. Advanced adhesive glues ensure reliable connections between components on flexible substrates, maintaining electrical conductivity even with repeated bending and stretching.
- Environmental Resistance:Wearable devices are exposed to various environmental conditions, including temperature fluctuations, humidity, and UV exposure. Adhesive glues with excellent thermal stability and UV resistance help protect internal components from degradation and ensure the device’s reliability over time.
- Aesthetics and Comfort:Wearable devices are not just about functionality; aesthetics and user comfort also play a vital role. Advanced adhesive glues allow for seamless bonding of components, eliminating protrusions or rough edges that could cause discomfort or detract from the device’s appearance.
- Manufacturability:As wearable technology advances, manufacturers seek efficient and scalable production methods. Advanced adhesive glues can be designed for compatibility with automated assembly processes, making mass production of wearable devices more feasible.
What Considerations are Essential for Proper Storage and Handling Advanced Electronics Adhesive Glue?
Proper storage and handling of advanced electronics adhesive glue are crucial to maintaining the adhesive’s quality and effectiveness. Adhesive glues are sensitive to various environmental factors, and their performance can be compromised if not stored and handled correctly. Here are some essential considerations to keep in mind:
- Temperature and Humidity: Adhesive glues often have specific temperature and humidity requirements for storage. Extreme temperatures can cause the adhesive to degrade or become less effective. Always store adhesive glues within the recommended temperature range, and avoid exposing them to excessive humidity.
- Storage Conditions: Store adhesive glues in a cool, dry place, away from direct sunlight, heat sources, and moisture. Use airtight containers or original packaging to prevent exposure to air and humidity.
- Ventilation: Ensure adequate ventilation in the storage area to prevent the buildup of fumes or volatile components from the adhesive. Some adhesive glues can release harmful vapors, so a well-ventilated room is essential.
- Sealing and Capping: Always tightly seal the adhesive containers or tubes after each use to prevent air exposure and drying out of the adhesive. This will help maintain the adhesive’s consistency and bonding properties.
- Shelf Life: Adhesive glues have a limited shelf life, even when stored properly. Be aware of the adhesive’s expiration date and use older stock before newer ones to prevent waste.
- Clean Application Tools: Ensure that the tools used for applying the adhesive, such as brushes, syringes, or dispensing nozzles, are clean and residue-free. Contaminants can affect the adhesive’s bonding performance.
- Surface Preparation: Properly clean and prepare the characters to be bonded before applying the adhesive. Clean surfaces help the adhesive adhere more effectively and ensure a strong bond.
- Mixing (If Applicable): Follow the manufacturer’s instructions carefully if the adhesive requires mixing before use. Improper mixing can affect the adhesive’s properties and performance.
- Avoid Cross-Contamination: Prevent cross-contamination by using dedicated tools for each adhesive type to avoid mixing different adhesive formulations.
- Safety Precautions: Adhesive glues can contain chemicals that may be harmful if mishandled. Follow safety guidelines provided by the manufacturer, such as wearing gloves and protective eyewear and working in a well-ventilated area.
- Read Manufacturer Instructions: Always follow the manufacturer’s instructions and guidelines for storing, handling, and applying adhesive glue.
- Testing: Before using the adhesive on critical applications, consider conducting preliminary tests on sample materials to ensure that the adhesive meets your specific requirements.
Remember that different adhesive formulations may have varying storage and handling requirements, so it’s essential to refer to the manufacturer’s recommendations for the specific adhesive you are using. These considerations will help you maintain the quality and effectiveness of advanced electronics adhesive glue and ensure successful bonding in your projects.