Customized Adhesive Glue
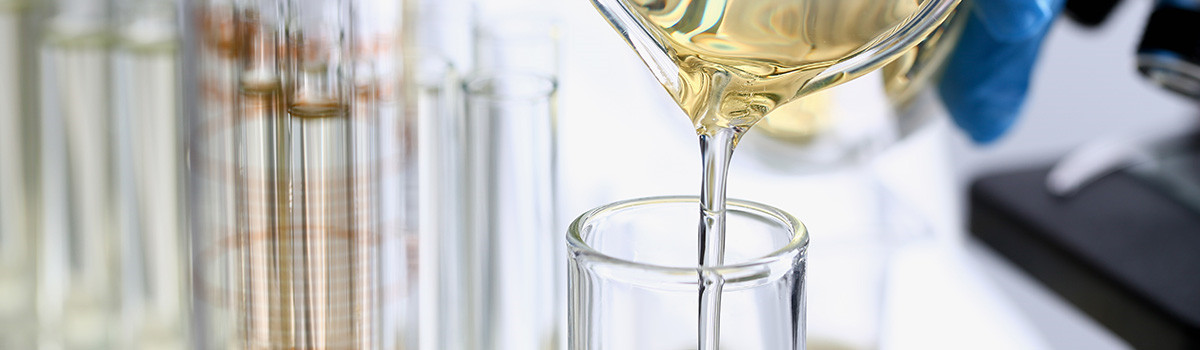
If you need it, we have it. And if we don’t, we’ll create it. Yes, you can custom the adhesives what you want at Deepmaterial.
Driven by a passion to innovate, create, solve and serve, we develop and manufacture nearly any type of adhesive solution imaginable. We also utilize custom-formulated adhesives for specific materials.
In the dynamic landscape of industrial and consumer needs, adhesive solutions have become a linchpin for achieving efficient and durable bonds between materials. The emergence of customized adhesive glue has revolutionized the way industries approach bonding challenges. By offering the flexibility to tailor adhesive properties to specific applications, customized adhesive glue has opened doors to unprecedented innovation and efficiency across various sectors. This comprehensive article delves into the world of customized adhesive glue, exploring its composition, benefits, applications, and the role it plays in shaping contemporary manufacturing and design.
Understanding Customized Adhesive Glue
Understanding Customized Adhesive Glue is essential for industries seeking tailored solutions to bonding challenges in various applications. Unlike off-the-shelf adhesives, customized adhesive glue offers precise formulations that align with specific requirements, ensuring optimal performance and reliability. This approach involves a deep collaboration between manufacturers and end-users, creating unique adhesive products to address particular needs. Several vital points underscore the importance and benefits of customized adhesive glue:
- Application-Specific Formulations:Formulate customized adhesive glue to cater to the specific substrates, environmental conditions, and stresses an application demands. This tailored approach results in a bond optimized for the intended purpose.
- Enhanced Performance: Unlike generic adhesives, customized adhesive glue is fine-tuned to deliver superior performance, whether high tensile strength, flexibility, resistance to temperature extremes, or other attributes.
- Problem-Solving:Customized adhesive glue is an excellent solution for bonding challenges that standard adhesives cannot adequately address. It allows overcoming unique issues such as compatibility concerns or extreme operating conditions.
- Cost Efficiency: While customized adhesive glue might have a higher upfront development cost, it can lead to cost savings in the long run by preventing failures, reducing rework, and enhancing overall efficiency.
- Tailored Curing Methods: Formulate customized adhesive glue to cure through various methods, such as heat, UV light, or moisture. This flexibility ensures the adhesive is compatible with the available equipment and processes.
- Substrate Compatibility: Customized adhesive glue considers the specific properties of the substrates it bonds, ensuring a solid and durable bond that withstands challenges unique to the materials.
- Longevity and Reliability:With a formulation designed to match the exact application, customized adhesive glue offers a longer lifespan and higher reliability than generic adhesives.
- Reduced Environmental Impact:Customized adhesive glue can be formulated with environmentally friendly ingredients, aligning with sustainability goals.
- Collaboration: Developing customized adhesive glue involves close cooperation between manufacturers and end-users. This partnership ensures that the adhesive meets the precise requirements and performance expectations.
- Innovation: Creating customized adhesive glue encourages innovation as manufacturers strive to develop solutions for specific challenges that they haven’t addressed before.
Composition and Formulation Variability
Composition and Formulation Variability plays a significant role in various industries, influencing product quality, performance, and reliability. Whether in pharmaceuticals, manufacturing, or consumer goods, understanding and managing the intricacies of composition and formulation is essential for achieving consistent results. Several key points highlight the importance and implications of composition and formulation variability:
- Raw Materials Influence:The composition and quality of raw materials used in formulations directly impact the final product’s attributes. Variability in these materials can lead to consistency in product performance and quality.
- Product Consistency:Maintaining consistent composition and formulation is crucial for ensuring that products meet predetermined specifications and perform as intended.
- Regulatory Compliance:Many industries are subject to strict product composition and formulation regulations. Deviations from established standards can lead to regulatory issues and potential legal consequences.
- Quality Control Challenges:Variability in composition and formulation can pose challenges in quality control processes, as it requires vigilant monitoring and testing to ensure products meet the desired standards.
- Consumer Perception:In industries such as cosmetics and food, even slight variations in composition and formulation can lead to changes in color, taste, texture, or effectiveness, affecting consumer perception and trust.
- Process Stability:Fluctuations in composition and formulation can impact manufacturing processes, leading to increased downtime, reduced yield, and inefficiencies.
- Customization and Innovation:Controlled variability allows tailored products to meet specific customer preferences or accommodate different market segments.
- Risk Mitigation:Understanding composition and formulation variability is crucial for identifying potential risks and developing mitigation strategies. Ensuring product safety is necessary in industries where it holds the utmost significance.
- Supply Chain Considerations:Variability in raw materials across different suppliers can lead to inconsistencies in the final product, highlighting the importance of establishing reliable supply chains.
- Testing and Validation:Rigorous testing and validation processes are necessary to ensure that products remain consistent in their attributes, performance, and safety, despite any allowable formulation variability.
Benefits of Tailored Adhesive Solutions
The Benefits of Tailored Adhesive Solutions are profound across various industries, offering a strategic advantage for achieving optimal performance, cost-effectiveness, and efficiency in bonding applications. Tailoring adhesives to specific needs provides solutions that cater to unique challenges and requirements, resulting in superior outcomes. Several vital points underscore the importance and advantages of tailored adhesive solutions:
- Optimized Performance:Precisely formulate tailored adhesive solutions to match the characteristics of the substrates they bond, ensuring optimal adhesion, strength, and durability.
- Customized Adhesive Formulation:Achieve superior adhesive performance in challenging environments, such as high-stress situations, chemical exposure, and extreme temperatures, by tailoring adhesives through personalized formulations.
- Enhanced Efficiency:Tailored adhesives streamline processes by eliminating the need for adjustments, reducing assembly time, and minimizing rework.
- Cost Efficiency:While tailored adhesive solutions might have upfront development costs, they lead to cost savings in the long run by preventing failures, reducing wastage, and enhancing overall efficiency.
- Reduced Material Consumption:Precise formulations lessen the amount of adhesive required for each application, minimizing material consumption and waste.
- Improved Aesthetics:Create personalized adhesives that seamlessly blend in after curing, enhancing a polished and visually appealing finish.
- Bonding Dissimilar Materials:Tailored adhesive solutions enable adequate bonding between dissimilar substrates, allowing for innovative designs and joining of diverse materials.
- Longevity and Reliability:Customized adhesives ensure bonds that stand the test of time, contributing to longer-lasting products and reduced maintenance requirements.
- Environmental Considerations:Tailored adhesive solutions can be formulated with environmentally friendly ingredients, aligning with sustainability goals and reducing the environmental impact.
- Problem-Solving:Tailored adhesive solutions address specific bonding challenges more effectively than generic adhesives might.
- Flexibility in Curing Methods:Create customized adhesives capable of curing through different techniques, providing versatility to align with the available machinery and procedures.
- Collaboration:Developing tailored adhesive solutions involves close cooperation between manufacturers and end-users, ensuring that the adhesive meets the precise requirements and performance expectations.
Adhesion to Diverse Substrates
“Adhesion to Diverse Substrates” is a critical aspect of various industries and applications, ranging from manufacturing and construction to biomedical research. This phenomenon refers to the ability of a material or substance to cling onto and maintain a bond with different types of surfaces. Achieving adequate adhesion to diverse substrates presents many challenges and opportunities for innovation. Key factors such as surface chemistry, physical forces, and material properties play pivotal roles in determining the strength and longevity of adhesion. Several techniques and strategies have emerged to enhance adhesion to diverse substrates, including:
- Surface Modification:Altering the surface characteristics of substrates through techniques like plasma treatment, chemical functionalization, or physical abrasion can create a more conducive environment for adhesion. These modifications can introduce new functional groups or roughen the surface, providing better contact points for adhesive materials.
- Selection of Adhesive Materials:Choosing the appropriate adhesive material is crucial for achieving optimal adhesion. Different materials exhibit varying affinities for various substrates. Polymer-based adhesives, epoxy resins, and pressure-sensitive adhesives are materials designed to adhere effectively to diverse surfaces.
- Interfacial Compatibility:Ensuring compatibility between the adhesive material and the substrate is essential. Mismatches in coefficients of thermal expansion or differences in material rigidity can lead to premature detachment. Engineers and researchers must carefully assess the mechanical properties of the adhesive and substrate to ensure long-lasting adhesion.
- Molecular Adhesion:In cases requiring strong adhesion at the molecular level, you can employ covalent or hydrogen bonding approaches. These interactions form a strong chemical bond between the adhesive and the substrate, enhancing the overall adhesion performance.
- Geometric and Microstructural Designs:Incorporating microstructures or surface patterns can significantly enhance adhesion. The gecko’s ability to cling to surfaces is a prime example of biomimicry inspiring innovative adhesive designs. Microscopic pillars, hooks, or ridges can create mechanical interlocking, improving adhesion on a tiny scale.
- Environmental Factors:Environmental conditions like temperature, humidity, and chemical exposure can influence adhesion performance. Developing adhesives that maintain their bonding properties under various conditions is crucial for real-world applications.
Temperature and Environmental Resistance
“Temperature and Environmental Resistance” are pivotal considerations in developing and deploying materials across various industries. The ability of a material to withstand fluctuating temperatures and harsh environmental conditions can determine its longevity, reliability, and overall performance. This dual challenge of ensuring thermal stability and ecological resilience requires strategic design, material selection, and testing. Key factors and strategies include:
- Material Selection:Choosing materials that possess inherent resistance to extreme temperatures and environmental factors is a fundamental starting point. Polymers like PTFE (polytetrafluoroethylene) and metals such as stainless steel are known for their excellent resistance to temperature variations and corrosion, respectively.
- Thermal Expansion Management: Mismatched coefficients of thermal expansion between different materials can lead to mechanical stress and material failure. Selecting materials with similar expansion properties or incorporating design features to accommodate growth can mitigate these challenges.
- Coatings and Sealants:Protective coatings and sealants enhance temperature and environmental resistance. These layers provide a barrier against moisture, chemicals, and temperature-induced degradation, extending the material’s lifespan.
- High-Performance Alloys:Industries such as aerospace and automotive rely on high-performance alloys that can maintain structural integrity under extreme conditions. Alloys like Inconel and Titanium offer exceptional temperature resistance, making them valuable choices for components subjected to elevated heat.
- Testing and Simulation:Rigorous testing and simulation are essential to assess a material’s behavior under various temperature and environmental conditions. Accelerated aging tests, thermal cycling tests, and exposure to corrosive agents help identify weaknesses and inform improvements.
- Thermal Barrier Coatings:In industries like gas turbines, thermal barrier coatings are applied to components to reduce heat transfer and enhance temperature resistance. These coatings help components withstand high operating temperatures, improving overall efficiency and durability.
- Environmental Protection:Designing materials resistant to environmental stressors like UV radiation, humidity, and chemical exposure can extend their useful life in outdoor or aggressive environments.
- Engineering Design:Incorporating thoughtful engineering design can minimize the impact of temperature fluctuations. Proper ventilation, heat sinks, and thermal insulation can all contribute to maintaining stable operating conditions.
Flexible and Rigid Bonding
“Flexible and Rigid Bonding” techniques play a pivotal role in various industries, offering distinct advantages for different applications. The choice between flexible and rigid bonding depends on material properties, intended use, and desired performance outcomes. These bonding methods encompass a range of techniques that enable materials to adhere to each other, creating connections that can either withstand deformation and movement or maintain structural integrity. Key considerations and applications include:
Flexible Bonding
Flexible bonding involves joining materials to allow movement, expansion, and contraction without compromising the bond’s integrity. This feature is especially beneficial for applications where materials encounter dynamic forces or changing conditions.
- Applications:Flexible bonding finds use in wearable technology, electronic devices, and automotive interiors, where components experience constant movement and vibration. It’s also valuable in medical devices and textiles, where comfort and conformity to body contours are essential.
Rigid Bonding
Rigid bonding creates a strong and immovable connection between materials. Designed to provide structural stability and maintain the original shape of the bonded components, it often finds use in load-bearing scenarios.
- Applications:Rigid bonding is crucial in the construction, aerospace, and automotive industries, where structural integrity is paramount. It’s also essential in manufacturing, where precision and accuracy are required, such as assembling electronic components.
Adhesive Selection
The choice of adhesive plays a significant role in determining whether the bond will be flexible or rigid. Flexible adhesives typically have some elasticity, while tough adhesives provide a robust and inflexible bond.
- Adhesive Formulation:Formulate adhesives to achieve varying degrees of flexibility or rigidity, allowing for customization based on the application’s specific requirements.
Substrate Compatibility
The bonded materials influence whether a flexible or rigid approach is more suitable. Matching the bonding method’s flexibility with the materials’ joined characteristics is essential for achieving a successful bond.
- Compatibility Considerations:For instance, bonding a flexible polymer to a rigid metal might require an adhesive with some flexibility to accommodate the material differences.
Dynamic vs. Static Loads
Consideration of the type of load the bonded components will experience is essential. Dynamic shipments, like vibrations, require flexible bonds, while static loads, like weight, are better suited for rigid bonds.
Engineering Analysis: Engineers analyze the stress and strain patterns in the bonded components to determine the appropriate bonding approach.
Role in Product Design and Innovation
The concept of “Role in Product Design and Innovation” is a multifaceted and pivotal aspect that significantly influences the success and trajectory of any company or industry. In the dynamic landscape of today’s market, the role of product design and innovation extends far beyond aesthetics and technical functionalities; it serves as a driving force behind a company’s competitive edge and market positioning. This role encompasses many functions and responsibilities, each vital in shaping the outcome of a product’s journey from conception to market launch. Several essential points underline the significance of this role:
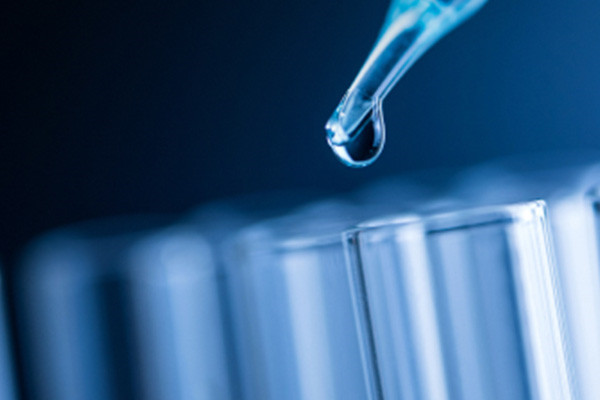
- User-Centered Approach:Product design and innovation place the user at the heart of the process. Companies can create products that genuinely resonate with their target audience by empathizing with user needs, preferences, and pain points.
- Market Adaptation:A successful product doesn’t exist in isolation; it’s a response to the demands and trends of the market. An acute understanding of market dynamics enables companies to tailor their products to meet current and future consumer demands.
- Cross-Disciplinary Collaboration:The role of product design and innovation thrives on collaboration. Engineers, designers, marketers, and other stakeholders must work together to synthesize diverse perspectives and insights, resulting in holistic and well-rounded products.
- Iterative Prototyping:Innovation is rarely a linear process. Iterative prototyping allows continuous refinement, incorporating feedback and insights to enhance a product’s features, functionality, and user experience.
- Risk Management and Creativity:This role’s core is balancing creativity with risk management. While innovation encourages thinking outside the box, it also requires a calculated approach to ensure feasibility, scalability, and resource optimization.
- Ethics and Sustainability:Modern product design and innovation must consider ethical implications and environmental sustainability. The role extends to ensuring that products align with ethical standards and contribute positively to society and the planet.
- Differentiation and Branding:Product design can be a crucial differentiator in an increasingly crowded market. Innovative features and a distinct design philosophy can establish a brand identity that resonates with consumers.
- Disruption and Industry Leadership:Companies prioritizing product innovation can drive industry-wide disruption. Groundbreaking products capture market share and position their creators as thought leaders and pioneers.
- Adaptation to Technology:Rapid technological advancements continually reshape the product design and innovation landscape. Embracing emerging technologies allows companies to push boundaries and explore new possibilities.
- Global Competitiveness:Geographical boundaries do not limit the role of product design and innovation. Companies that excel in this area can compete worldwide, reaching diverse markets and demographics.
Medical Applications and Biocompatibility
The intersection of “Medical Applications and Biocompatibility” has revolutionized the healthcare field by merging technological advancements with the imperative of patient safety. Within this realm, medical applications have harnessed cutting-edge technologies to enhance diagnostics, treatments, and patient outcomes. These innovations are underpinned by biocompatibility, ensuring that medical devices and materials are well-tolerated by the human body without causing adverse reactions. This synergy has led to a new era of medical possibilities characterized by improved precision, reduced invasiveness, and enhanced patient experiences. Several key points highlight the significance of this convergence:
- Diagnostic Precision:Medical applications have paved the way for highly accurate diagnostic tools, such as advanced imaging techniques and wearable monitoring devices, enabling early disease detection and personalized treatment approaches.
- Minimally Invasive Interventions:Biocompatible materials and technologies have facilitated minimally invasive procedures, reducing patient trauma, recovery times, and the risk of complications.
- Implantable Innovations:Biocompatibility ensures that implantable medical devices, such as pacemakers, stents, and joint replacements, seamlessly integrate with the body, minimizing the risk of rejection or discomfort.
- Drug Delivery Advancements:Medical applications have led to novel drug delivery systems that can precisely target affected areas, optimizing therapeutic efficacy while minimizing side effects.
- Regenerative Medicine:Biocompatible materials and techniques are pivotal in regenerative medicine, enabling the development of tissue engineering, organ transplantation, and wound healing solutions.
- Remote Healthcare:Medical applications allow for remote monitoring and telemedicine, enhancing access to healthcare and enabling real-time patient data analysis.
- Ethical and Regulatory Considerations:Integrating medical applications and biocompatibility raises ethical and regulatory questions, necessitating robust oversight to ensure patient safety and data privacy.
- Collaboration Across Disciplines:The convergence of medical applications and biocompatibility demands collaboration between medical professionals, engineers, material scientists, and regulatory experts.
- Long-term Safety:Biocompatibility assessments ensure the long-term safety of medical devices and materials, mitigating risks associated with chronic exposure within the body.
- Global Health Impact:The fusion of medical applications and biocompatibility has a global impact, as we can leverage advancements in healthcare technology to address healthcare disparities and enhance medical access in underserved regions.
Automotive Bonding Solutions
In the realm of automotive engineering, the quest for enhanced performance, safety, and aesthetics has driven the evolution of “Automotive Bonding Solutions.” These solutions are pivotal in assembling modern vehicles, encompassing various techniques and materials that ensure structural integrity, durability, and innovation. From traditional welding and fastening methods to cutting-edge adhesive technologies, automotive bonding solutions have revolutionized the industry by enabling the creation of complex, lightweight, and energy-efficient vehicles. Several vital aspects underscore the significance of these solutions:
- Strength and Structural Integrity:Automotive bonding solutions offer a high-strength alternative to traditional welding and mechanical fastening methods, enhancing the structural integrity of vehicle components and assemblies.
- Weight Reduction:By replacing heavy metal components with bonded structures, vehicles can significantly reduce weight, improving fuel efficiency and reducing emissions.
- Vibration Damping:Bonding materials possess inherent vibration-damping properties, which enhance ride comfort and reduce noise within the vehicle cabin.
- Design Flexibility:Adhesive bonding solutions enable the creation of intricate and innovative designs that might be challenging to achieve using traditional methods.
- Corrosion Resistance:Adhesive bonding eliminates the need for drilling holes and welding, reducing the potential entry points for corrosion and contributing to the vehicle’s longevity.
- Enhanced Safety:Bonded components distribute stress and impact forces more evenly, improving the vehicle’s and its occupants’ overall safety.
- Aesthetic Appeal:Bonding solutions enable flush surfaces, eliminating visible weld seams or fasteners, thus enhancing the vehicle’s visual appeal.
- Reduced Production Time:Adhesive bonding can streamline manufacturing by eliminating the need for time-consuming welding processes and facilitating automation.
- Joining Dissimilar Materials:Automotive bonding solutions allow for the joining of dissimilar materials, such as composites, plastics, and metals, expanding design possibilities and material choices.
- Environmental Considerations:Some bonding solutions are more environmentally friendly than traditional methods, as they generate less heat and consume less energy during assembly.
Advancing “Automotive Bonding Solutions” signifies a paradigm shift in how we design, manufacture, and experience vehicles. By offering a harmonious blend of strength, design flexibility, weight reduction, and environmental considerations, these solutions contribute to the ongoing evolution of the automotive industry. As manufacturers continue to seek ways to create vehicles that meet evolving market demands and regulatory requirements, automotive bonding solutions will undoubtedly remain at the forefront of innovation, shaping future cars.
Electronics and Micro Component Assembly
In the fast-paced electronics landscape, “Electronics and Micro Component Assembly” are the cornerstones of innovation, enabling increasingly compact, powerful, and interconnected devices. This field encompasses intricate processes and techniques that involve the precise placement and integration of minuscule components onto circuit boards or substrates, resulting in the daily functionality and performance we rely on. From smartphones and wearables to medical devices and automotive systems, electronics and microcomponent assembly play an instrumental role in shaping our technologically-driven world. Several vital points underscore the significance of this domain:
- Miniaturization: Electronics and microcomponent assembly drive the miniaturization of devices, allowing for powerful functionality in increasingly compact form factors.
- Precision Placement:The assembly process involves placing components with sub-micron accuracy, necessitating advanced robotics, machinery, and optical systems.
- Interconnectivity:Micro assembly techniques facilitate the creation of intricate circuitry, enabling seamless communication and cooperation between components.
- Advanced Materials:The field demands specialized materials, such as conductive adhesives and solder pastes, to ensure reliable connections and electrical conductivity.
- Packaging Solutions:Effective microcomponent assembly often involves innovative packaging solutions, which safeguard delicate components and optimize space utilization.
- Quality Control:Stringent quality control measures are vital to detect defects and ensure the functionality and reliability of assembled microelectronics.
- Medical Advancements:Micro-component assembly contributes to medical breakthroughs, powering devices like pacemakers, implantable sensors, and diagnostic equipment.
- Consumer Electronics:From smartphones to smartwatches, micro-assembly drives the production of devices that seamlessly integrate into daily life.
- Automotive Innovation:Electronics assembly is crucial in modern vehicles, enabling features like advanced driver assistance systems (ADAS) and infotainment systems.
- Internet of Things (IoT): Micro assembly supports the IoT by enabling the creation of interconnected devices that communicate and share data.
- Energy Efficiency:Micro component assembly contributes to energy-efficient electronics, optimizing power consumption and extending battery life.
Aerospace and High-Stress Environments
In aerospace engineering, the challenges posed by “Aerospace and High-Stress Environments” are pivotal in shaping aircraft and spacecraft design, manufacturing, and performance. The aerospace industry operates within an environment characterized by extreme conditions, including high speeds, rapid temperature fluctuations, intense vibrations, and radiation exposure. The intersection of aerospace and high-stress environments necessitates a meticulous approach to materials, technology, and engineering solutions to ensure the safety, reliability, and efficiency of vehicles that venture beyond the Earth’s atmosphere. Several vital points underscore the significance of this convergence:
- Material Innovation:Aerospace engineering requires the development of advanced materials that can withstand extreme heat, pressure, and forces, ensuring the structural integrity of vehicles in high-stress conditions.
- Temperature Extremes:Aerospace vehicles experience rapid temperature changes, from the intense heat of reentry to the extreme cold of outer space, necessitating materials that can withstand thermal stresses.
- Vibration and Shock:The dynamic nature of aerospace operations introduces intense vibrations and shocks during launch, flight, and landing, demanding robust design and manufacturing methods.
- Aerodynamic Performance:Designing aerospace vehicles involves creating structures that can handle high-speed aerodynamic forces while maintaining stability and control.
- Radiation Protection:Beyond the Earth’s protective atmosphere, spacecraft face exposure to cosmic and solar radiation, requiring shielding to protect onboard equipment and crew.
- Reliability and Redundancy:High-stress environments leave no room for error. Aerospace systems incorporate redundant systems and meticulous testing to ensure reliability in critical situations.
- Space Debris Mitigation:Aerospace engineering considers the presence of space debris, necessitating designs that minimize the risk of collisions.
- Human Factors:For crewed missions, aerospace engineers consider high-stress environments’ physiological and psychological impacts on astronauts.
- Fuel Efficiency:Aerospace engineers strive for fuel-efficient designs that optimize propulsion systems while overcoming the challenges of operating in high-stress conditions.
- Innovation and Exploration:The convergence of aerospace and high-stress environments drives innovation, enabling the exploration of new frontiers and pushing the boundaries of human understanding.
The symbiotic relationship between aerospace engineering and high-stress environments exemplifies human ingenuity and determination. From the first space missions to the future colonization of other planets, aerospace engineering continues to evolve, leveraging cutting-edge technology and engineering solutions to navigate and harness the extreme conditions that define the cosmos.
Construction and Structural Integrity
In the realm of construction, the concept of “Construction and Structural Integrity” forms the bedrock of safe, resilient, and enduring built environments. From towering skyscrapers to intricate bridges, the integrity of a structure underpins its safety, longevity, and functionality. Construction and structural integrity encompass a meticulous process that involves designing, engineering, and assembling components to ensure the final product’s stability and performance. Principles of physics, materials science, and engineering expertise govern this process to create structures capable of withstanding various forces, environmental conditions, and potential hazards. Several key points highlight the significance of this convergence:
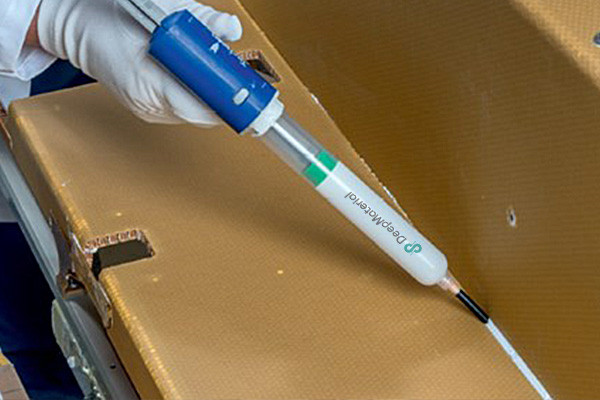
- Material Selection:The choice of materials is crucial in ensuring the structural integrity of a construction project. Different materials possess varying strength, durability, and resistance properties.
- Load Distribution:Structural engineers design buildings and infrastructure to distribute loads, both static and dynamic, evenly throughout the structure, preventing excessive stress on any one component.
- Environmental Factors:Structures must account for environmental stresses such as wind, earthquakes, temperature fluctuations, and corrosion to maintain their integrity over time.
- Foundations:A solid foundation is essential to the stability of any structure, as it transfers loads from the building to the ground and prevents settling or tilting.
- Quality Control:Rigorous quality control measures ensure that construction materials, techniques, and processes meet safety and integrity standards.
- Innovative Design:Advances in technology and engineering allow for innovative structural designs that maximize efficiency, aesthetics, and safety.
- Maintenance and Inspection:Regular maintenance and inspection are critical to identifying potential weaknesses or structural issues and addressing them before they compromise integrity.
- Resilience and Disaster Preparedness:Focusing on structural integrity contributes to the overall strength of communities in the face of natural disasters and other emergencies.
- Longevity and Sustainability:By ensuring structural integrity, construction projects contribute to sustainability by reducing the need for frequent repairs or replacements.
- Safety:The paramount concern in construction is the safety of occupants and the public, making structural integrity a non-negotiable aspect of the process.
The relationship between “Construction and Structural Integrity” reflects the fusion of science, art, and practicality in creating our physical environment. As societies evolve and urban landscapes change, construction, and structural integrity remain pivotal in shaping the cities, infrastructure, and spaces that facilitate our lives. By adhering to principles of engineering excellence, material science, and innovative design, construction professionals ensure that the buildings and structures they create stand as testaments to human achievement and serve as safe and functional spaces for future generations.
Food-Grade and Packaging Adhesives
In the realm of food industry solutions, Food-Grade and Packaging Adhesives stand out as indispensable components that ensure consumables’ safety and visual appeal. These adhesives have proven themselves as a crucial link in the packaging process, upholding the integrity of various packaging materials while conforming to strict food safety regulations. Key benefits and features of Food-Grade and Packaging Adhesives include:
- Safety Assurance:Prioritizing food safety, we formulate these adhesives with materials approved for direct and indirect contact with food. By preventing the leaching of harmful substances into the packaged products, their purity and quality are maintained.
- Strong Bonding Properties:Food-Grade and Packaging Adhesives exhibit excellent bonding strength on various substrates commonly used in packaging, such as paper, cardboard, plastic, and metals. By implementing this method, we guarantee that the packaging will remain undamaged during transportation and storage, effectively preventing contamination or leakage.
- Temperature Resistance:We design the adhesives to withstand a wide range of temperatures, from cold storage to the heat of transportation and display. This temperature resistance ensures the adhesives maintain integrity and securely bond packaging materials even under challenging conditions.
- Flexibility and Durability:Packaging comes in all shapes and sizes, and these adhesives offer the flexibility required to adhere to different forms of packaging while maintaining durability over time. It is essential to ensure secure packaging for items susceptible to stress or movement during transportation and handling.
- Customizability:Formulate Food-Grade and Packaging Adhesives to meet specific requirements, such as rapid curing for high-speed production lines or addressing specialized adhesion needs for unique packaging designs. This level of customization enhances efficiency and effectiveness in the packaging process.
- FDA and EU Compliance:These adhesives adhere to stringent regulations and comply with both FDA (Food and Drug Administration) regulations in the United States and similar guidelines set by the European Union. This compliance underscores their suitability for use in food packaging applications.
Custom Adhesives for Art and Craft
Custom adhesives have emerged as invaluable tools in art and craft, offering a versatile range of options for artists and enthusiasts to explore their creativity with precision and innovation. This niche has witnessed the development of adhesives tailored to specific artistic needs, characterized by:
- Diverse Substrate Compatibility:Custom adhesives cater to a wide array of materials, from paper and fabric to wood, ceramics, and even unconventional surfaces, providing secure bonds without compromising the integrity of the artistic medium.
- Specialized Formulations:These adhesives come in various formulations, such as repositionable, quick-drying, and acid-free, ensuring that artists can choose the suitable adhesive for their specific project requirements.
- Enhanced Precision:With options like fine-tip applicators and controlled dispensing mechanisms, custom adhesives enable intricate detailing, allowing artists to execute even the most delicate designs accurately.
- 3D and Mixed Media Support:Artists engaged in three-dimensional and mixed media projects benefit from adhesives designed to bond diverse materials seamlessly, facilitating the construction of complex structures and textures.
- Minimal Residue and Clean Application:Engineers customize adhesives to leave minimal residue or marks, preserving the aesthetics of the artwork and reducing the need for extensive cleanup.
- Longevity and Durability:Artists can confidently rely on these adhesives for long-lasting results, ensuring their creations stand the test of time without deteriorating or losing their bond.
- Non-Toxic Options:Many custom adhesives are considered non-toxic and safe for various artistic applications, making them suitable for artists of all ages.
- Variety of Uses:Custom adhesives support a myriad of artistic endeavors, including paper crafting, scrapbooking, collage, mosaic, model-building, and more, providing a versatile solution for various creative pursuits.
Custom adhesives have revolutionized the art and craft landscape, offering artists and crafters an innovative toolkit to push the boundaries of their imagination. As this field continues to evolve, artists can expect to see even more tailored solutions that empower them to explore new techniques and artistic expressions, ultimately enhancing the overall creative experience.
Challenges in Formulation and Testing
Formulating and testing new products is a complex endeavor involving various challenges, requiring careful navigation to ensure successful outcomes. As industries strive to innovate and meet evolving consumer demands, several vital challenges emerge in the formulation and testing process:
- Ingredient Compatibility:A persistent challenge is to select the right combination of ingredients that work harmoniously. Compatibility issues can lead to undesirable reactions, affecting product stability and performance.
- Optimal Formulation:Achieving the desired product attributes, such as texture, color, scent, and efficacy, while maintaining stability and safety demands meticulous formulation adjustments and iterations.
- Preservation and Shelf Life:Developing effective and safe products over time requires addressing preservation challenges. Ensuring microbial stability without compromising product quality is a delicate balance.
- Sensory Appeal:Balancing sensory attributes with product functionality is essential. Products must not only deliver results but also offer a pleasant user experience through appearance, smell, and texture.
- Regulatory Compliance:Navigating the intricate landscape of regulations and standards is a critical challenge. Formulations must adhere to various guidelines, ensuring consumer safety and product legality.
- Resource Limitations:Limited resources, budget, or raw materials, can restrict the formulation process. Finding cost-effective alternatives without compromising quality is a constant concern.
- Scale-Up Complexities:Transitioning from small-scale lab formulations to large-scale production introduces unforeseen challenges. To ensure consistent quality, reevaluate factors like mixing dynamics and heat transfer.
- Testing Accuracy:Developing effective testing methods to assess product performance and safety is crucial. Ensuring that these tests accurately reflect real-world usage scenarios is a continual challenge.
- Environmental Impact:Designing formulations with reduced ecological footprint requires careful ingredient selection and sustainable sourcing, adding an extra layer of complexity.
- Consumer Variability:Accounting for diverse consumer preferences, skin types, and sensitivities can be challenging. Products must cater to a broad audience while minimizing adverse reactions.
Collaborative Design Process with Manufacturers
The collaborative design process with manufacturers is a dynamic and essential approach that fosters innovation and efficiency throughout product development. This multifaceted process involves close interaction between design teams and manufacturers, ensuring seamless integration of creative ideas and practical production considerations. Key aspects of this process include:
1.Early Engagement:Manufacturers are brought into the design process early on, allowing their expertise to inform decisions from the outset. Identifying potential manufacturing challenges and solutions in the design phase reduces costly redesigns later.
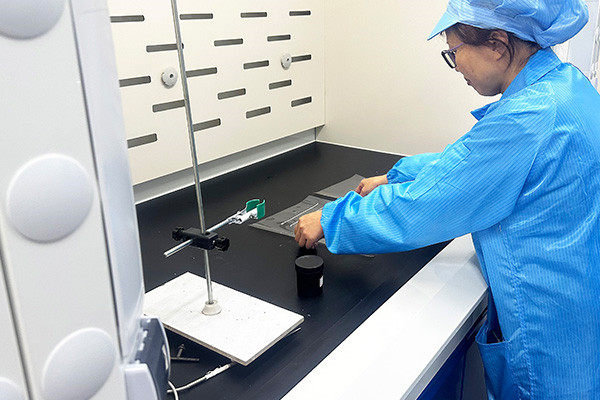
2.Iterative Feedback Loop:Regular feedback exchanges between designers and manufacturers lead to continuous refinements. Manufacturers provide insights on materials, production techniques, and cost-effectiveness, influencing design choices for optimal manufacturability.
3.Material Selection:Manufacturers’ input aids in selecting materials that align with the product’s functional requirements and manufacturing capabilities. By doing this, we guarantee that the result will meet the highest quality standards while being produced efficiently.
4.Design for Manufacturing (DFM): Collaboratively implementing DFM principles guarantees streamlining the invention for production. Designing components simplifies assembly, reduces the number of parts, and eliminates unnecessary complexities.
5.Prototyping and Testing:Close collaboration during prototyping enables manufacturers to identify potential production challenges early. Designers can then adapt the design swiftly, enhancing the product’s manufacturability and functionality.
6.Cost Considerations:Manufacturers provide valuable cost estimates at various design stages. Providing helpful information on design features, materials, and processes enables better decision-making and directly impacts the product’s final price.
7.Risk Mitigation:Manufacturers contribute to identifying and mitigating potential risks associated with production, such as supply chain disruptions or quality control issues. Their insights enable proactive strategies to ensure a smoother production timeline.
8.Continuous Communication:By keeping communication channels open and transparent between design and manufacturing teams, they ensure prompt relay of changes and updates, preventing misunderstandings and minimizing production delays.
9.Collaborative Problem Solving:When unexpected challenges arise during production, collaborative problem-solving approaches involving design and manufacturing experts lead to efficient solutions that maintain the product’s integrity.
Application Techniques and Dispensing
Application techniques and dispensing methods are critical in achieving optimal adhesive performance and efficient manufacturing processes across industries. Key points highlighting the importance of application techniques and dispensing include:
- Precision Dispensing:Modern dispensing equipment enables precise control over adhesive application, ensuring accurate placement and consistent coverage, which is crucial for reliable bonding.
- Uniform Thickness:Proper application techniques ensure a uniform adhesive thickness, preventing weak spots and ensuring even stress distribution across the bond line.
- Automated Systems:Automated dispensing systems enhance efficiency and consistency by reducing human error and facilitating high-volume production with minimal variation.
- Selective Dispensing:Selective dispensing, often used in electronics, allows for precise adhesive placement only in specific areas, minimizing excess and optimizing performance.
- Metering and Mixing:For two-component adhesives, accurate metering and mixing of components are essential to achieve the correct formulation and curing properties.
- Robotic Applications:Robotic dispensing systems offer flexibility in applying adhesives to complex shapes and surfaces, enhancing repeatability and reducing manual labor.
- High-Speed Dispensing:Specialized dispensing systems ensure fast and accurate adhesive application without compromising quality in high-speed production environments.
- Contact and Non-Contact Methods: Both contact and non-contact dispensing methods, such as jetting, offer advantages depending on the adhesive viscosity, substrate, and application requirements.
- Adhesive Delivery:Adhesives can be delivered in various forms, including liquid, paste, tape, film, or spray, allowing flexibility in choosing the most suitable structure for the application.
- Environmental Considerations:The chosen dispensing method should align with ecological considerations, minimizing waste and ensuring efficient material usage.
- Training and Expertise:Proper training of personnel operating dispensing equipment ensures consistent and accurate application, reducing the risk of defects or performance issues.
- Process Validation:Validating the dispensing process through testing and inspection confirms that the adhesive is applied as intended and meets performance requirements.
Quality Control and Adhesive Performance
Quality control ensures consistent adhesive performance and product reliability in various industries. Key points highlighting the significance of quality control and adhesive performance include:
- Material Consistency:Quality control processes monitor the consistency of adhesive formulations, ensuring that each batch meets specified standards and reducing variations in performance.
- Adhesion Strength:Rigorous testing assesses the adhesive’s bonding strength, ensuring it meets or exceeds required levels for different substrates and conditions.
- Durability and Longevity:Quality control measures evaluate the adhesive’s resistance to temperature fluctuations, humidity, chemical exposure, and mechanical stress to ensure long-term durability.
- Curing Uniformity:We monitor adhesive curing processes to ensure uniform curing throughout the bond line, preventing weak spots and ensuring reliable adhesion.
- Viscosity and Dispensing:Monitoring adhesive viscosity and dispensing methods ensures proper application, avoiding issues like incomplete coverage or excess adhesive that can affect performance.
- Adhesive-to-Substrate Compatibility:Quality control ensures that adhesives are compatible with various substrates, preventing delamination or poor adhesion due to material interactions.
- Testing Protocols:Standardized testing protocols, such as shear, peel, and impact tests, verify adhesive performance under specific conditions, ensuring reliability in real-world applications.
- Consistent Production:Quality control measures maintain consistent production processes, reducing the likelihood of defects and variations that could impact performance.
- Traceability:Quality control systems track raw materials, production processes, and test results, quickly identifying issues and facilitating recalls if necessary.
- Real-World Simulation:Testing adhesives in simulated real-world conditions ensures their performance matches expectations and meets the application’s demands.
- Continuous Improvement:We use quality control data and feedback to identify areas for improvement, leading to refined formulations and enhancing adhesive performance over time.
Quality control is indispensable to adhesive development and manufacturing, ensuring that products meet specified standards and consistently deliver optimal performance. By adhering to stringent quality control processes, industries can achieve reliable adhesion, product longevity, and overall customer satisfaction while minimizing the potential for costly failures or recalls.
Environmental Considerations and Sustainability
Environmental considerations and sustainability have become paramount in various industries, prompting a shift towards eco-friendly practices and materials. Key points highlighting the importance of ecological reviews and sustainability include:
- Material Selection:Industries prioritize using biodegradable, recyclable, or derived-from-renewable resources to reduce environmental impact.
- Reducing Carbon Footprint:The push for sustainability involves choosing materials and manufacturing processes that emit fewer greenhouse gases and consume less energy.
- Life Cycle Assessment: Assessing a product’s environmental impact throughout its life cycle helps identify areas for improvement, from raw material extraction to production, usage, and disposal.
- Circular Economy:Embracing circular economy principles involves designing products and materials with recycling and reusability in mind, reducing waste, and conserving resources.
- Green Chemistry:Developing adhesives with reduced toxicity, minimal waste, and lower emissions aligns with green chemistry principles, contributing to safer and more sustainable products.
- Bio-Based Adhesives:Adhesives derived from natural sources like plants or biomass offer reduced environmental impact compared to petroleum-based alternatives.
- Water-Based Formulations:Water-based adhesives emit fewer volatile organic compounds (VOCs) and are less harmful to human health and the environment.
- Waste Reduction:Minimizing excess adhesive application, utilizing precision dispensing techniques, and reducing material waste contribute to sustainability efforts.
- Regulatory Compliance: Adhesive manufacturers and industries are adhering to strict regulations and standards for emissions, waste disposal, and environmental impact.
- Packaging Optimization:Sustainable adhesive solutions extend to packaging, focusing on minimizing packaging materials and using recyclable or compostable options.
- Collaboration for Innovation:Collaborative efforts between industries, researchers, and governments drive innovation in sustainable adhesive development, fostering a holistic approach to environmental responsibility.
The awareness of environmental factors and the pursuit of sustainability compel industries to embrace more conscientious practices and create adhesive solutions that harmonize with a cleaner and greener future. By choosing materials, processes, and products that reduce environmental harm and conserve resources, industries can contribute to the preservation of ecosystems, reduction of pollution, and a more sustainable global economy.
Future Trends in Customized Adhesive Development
Future trends in customized adhesive development are poised to revolutionize bonding solutions across industries, driven by cutting-edge technologies and evolving manufacturing demands. Key points outlining these trends include:
- Smart Adhesives:Adhesives equipped with sensors, self-healing properties, and responsiveness to external stimuli will enable real-time monitoring of bond integrity and adaptive functionality.
- Bio-Inspired Adhesives:Drawing inspiration from nature, adhesive development is undergoing transformative changes that reshape how materials join in various applications.
- Sustainable Formulations:Eco-friendly adhesive formulations derived from renewable sources and featuring biodegradability will gain prominence, aligning with global sustainability initiatives.
- Nanotechnology Integration:Nano-scale additives enhance adhesive properties, enabling better adhesion, durability, and compatibility with advanced materials like carbon composites and lightweight alloys.
- 3D Printing Adhesives:As additive manufacturing grows, specialized adhesives for 3D printing will emerge, ensuring optimal layer adhesion, print accuracy, and compatibility with various printing techniques and materials.
- Electromagnetic Adhesives:Adhesives responsive to electromagnetic fields will facilitate rapid curing, on-demand release, and reversible bonding for applications in electronics and robotics.
- Customization on Demand:Adhesive solutions tailored on demand using modular components will offer versatility and efficiency for specific bonding challenges.
- Multi-Material Bonding:With the rise of hybrid materials, adhesive formulations capable of bonding different materials, such as dissimilar metals and composites, will become essential.
- Digital Twin Integration:Adhesive development will integrate digital twin simulations to optimize formulations, predict performance, and refine adhesive properties before physical production.
- Data-Driven Adhesive Design:Machine learning and data analytics will play a role in predicting adhesive performance based on material characteristics, environmental conditions, and bonding requirements.
- Collaborative Development:Close collaboration between adhesive manufacturers, end-users, and researchers will facilitate the rapid development of customized solutions that address unique challenges.
Innovation, sustainability, and the demand for versatile bonding solutions will shape the future of customized adhesive development. Exciting transformations are on the horizon for the adhesive industry as it moves towards intelligent and responsive adhesives, sustainable formulations, and integration with advanced technologies. These changes will reshape the way various applications join materials.
Customized adhesive glue has redefined the concept of bonding by offering tailor-made solutions for a wide spectrum of industries and applications. Its ability to adapt to specific requirements, whether in extreme environments, medical devices, or artistic endeavors, has propelled industries towards greater innovation and efficiency. As technologies continue to evolve, the collaborative efforts between manufacturers, adhesive engineers, and designers are expected to lead to even more advanced and specialized adhesive solutions. In a world where adaptability and precision are key, customized adhesive glue stands as a testament to human ingenuity, enabling the creation of products that push the boundaries of possibility.