Conformal Coating Material
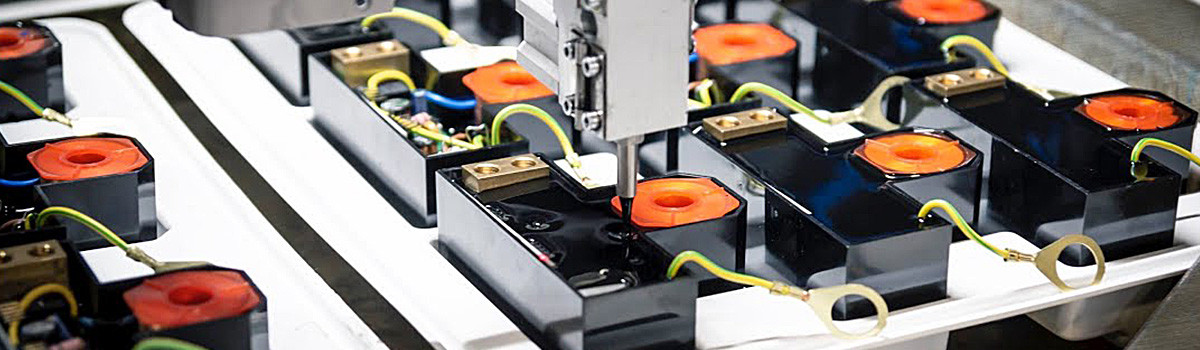
In the world of electronics, where intricate components and delicate circuits are the heart of innovation, safeguarding against environmental threats is crucial. Conformal coating materials have emerged as a transformative solution, redefining the way electronic devices are shielded from moisture, dust, chemicals, and other contaminants. By applying a thin, protective layer over circuitry, conformal coatings ensure reliability, longevity, and performance even in challenging conditions. This comprehensive exploration delves into the realm of conformal coating materials, unveiling their types, mechanisms, applications, benefits, and their pivotal role in enhancing the durability of modern electronics.
Introducing Conformal Coating Materials
Conformal coating materials represent a crucial frontier in electronics protection and reliability. These specialized coatings safeguard printed circuit boards (PCBs) and electronic components from environmental factors such as moisture, dust, chemicals, and temperature variations. By forming a thin, protective layer that adheres to the contours of the PCB, conformal coatings provide an additional shield against potential damage.
These coatings offer several benefits that contribute to electronic devices’ overall longevity and performance. They enhance resistance to harsh environments, preventing short circuits and corrosion that can compromise functionality. Conformal coatings also bolster insulation properties and minimize the risks of electrical leakage.
Manufacturers can choose from various conformal coating materials, including acrylics, silicones, urethanes, and epoxy resins. The selection depends on the specific application, considering flexibility, curing mechanisms, and chemical resistance.
Introducing conformal coating materials underscores the commitment to delivering robust and reliable electronics. By effectively sealing sensitive components, these coatings play a pivotal role in extending the operational life of devices and ensuring their sustained performance in diverse and challenging conditions.
Challenges in Electronics Protection
In electronics protection, conformal coating materials are pivotal in safeguarding sensitive components and printed circuit boards (PCBs) against environmental and mechanical challenges. However, while these coatings offer significant advantages, they pose unique challenges that require careful addressing.
Material Selection: Balancing Properties
Choosing the suitable conformal coating material is a delicate balancing act. Different coatings offer varying levels of protection, flexibility, and chemical resistance. Striking the right balance among these properties is crucial to ensure optimal performance in the intended environment.
Compatibility with Components: Preserving Functionality
Conformal coatings must not hinder the functionality of electronic components. Ensuring compatibility with sensitive components, such as sensors and high-frequency devices, is essential to maintain performance integrity.
Application Consistency: Covering Every Nook and Cranny
Applying conformal coatings uniformly across intricate PCB designs can be challenging. The inconsistent application can lead to coverage gaps or excessive coating thickness, potentially impacting heat dissipation and signal transmission.
Curing Techniques: Achieving Optimal Properties
Different coating materials require specific curing methods, such as thermal or UV. Proper curing is essential to maximize the coating’s protective properties, adhesion, and longevity.
Rework and Repair: A Delicate Undertaking
Removing and reapplying conformal coatings can be intricate in cases where repairs or modifications are necessary. A significant consideration is to ensure that coatings allow for reworking without causing damage to components.
Inspection and Testing: Ensuring Adequate Coverage
Verifying the uniformity and coverage of conformal coatings can be challenging. Effective inspection techniques are essential to identify defects, voids, or areas with insufficient coating.
As the electronic landscape evolves, conformal coating materials must keep pace to meet the demands of ever-changing environments and applications. Manufacturers and engineers must collaboratively address these challenges through careful material selection, precise application techniques, and rigorous quality control measures. By doing so, the industry can continue to harness the protective potential of conformal coatings, ensuring that electronic devices remain resilient, reliable, and practical, even in the face of challenging conditions.
Mechanisms of Conformal Coating Adhesion
In electronics protection, understanding the mechanisms of conformal coating adhesion is crucial. These mechanisms determine how effectively a coating bonds to the surface of printed circuit boards (PCBs) and electronic components, ultimately influencing the coating’s ability to provide reliable and lasting protection.
Chemical Bonding: Establishing Molecular Connections
Chemical adhesion involves the creation of molecular bonds between the conformal coating material and the substrate surface. This bond formation occurs through chemical reactions, forming a strong and durable connection. Chemical bonding is particularly effective when using coatings designed to chemically react with the substrate, enhancing adhesion and resistance to environmental factors.
Mechanical Interlocking: Getting a Grip
Mechanical interlocking relies on the physical structure of the substrate to create a secure grip for the coating material. Coatings with high viscosity or the ability to flow into surface irregularities create a tight fit, enhancing the mechanical interlocking effect. This mechanism is crucial for ensuring adhesion to surfaces with complex topographies.
Electrostatic Adhesion: Charged Connections
Electrostatic adhesion occurs when the coating and the substrate have opposite electrical charges, leading to attraction and bonding. This mechanism can provide strong adhesion but requires careful consideration of the electrical properties of the materials involved.
Wetting and Capillary Action: Filling in the Gaps
Wetting involves spreading the coating material over the substrate’s surface, aided by reducing surface tension. Capillary action then draws the coating into gaps and crevices, ensuring comprehensive coverage and adhesion. This mechanism is essential for achieving uniform protection, especially in intricate designs.
Surface Preparation: A Foundation for Adhesion
Adequate adhesion starts with proper surface preparation. Cleaning and degreasing surfaces, and in some cases, treating them to enhance their receptivity to the coating material, is necessary. A well-prepared surface provides a solid foundation for the adhesion mechanisms to take hold.
Understanding these mechanisms is crucial for optimizing conformal coating adhesion and, consequently, the overall protection of electronic devices. By tailoring coating formulations and application techniques to leverage these mechanisms, manufacturers can ensure that coatings adhere reliably to PCBs and components, offering robust defense against environmental stressors and contributing to the longevity and reliability of electronic products.
Types of Conformal Coating Materials
Conformal coatings protect electronic components from environmental factors such as moisture, dust, chemicals, and physical abrasion. To create these coatings, people use various materials, and each material offers distinct properties and advantages. Here are some of the primary types of conformal coating materials:
Acrylic Resin Coatings
- Their versatility and ease of application make them widely used.
- Good moisture resistance and dielectric properties.
- Transparent nature allows easy inspection.
- Limited chemical resistance and moderate temperature tolerance.
Silicone Resin Coatings
- This material offers exceptional flexibility and elongation, making it suitable for components prone to vibrations.
- High-temperature resistance, making them suitable for harsh environments.
- While it provides good moisture protection, there is a potential for outgassing under high temperatures.
Urethane Resin Coatings
- Excellent chemical and solvent resistance.
- Superior abrasion resistance, suitable for components facing mechanical stress.
- Generally, thicker coatings may impact fine-pitch components.
Parylene Coatings
- It was deposited as a vapor, conforming even to intricate shapes.
- Ultra-thin, optically clear, and biocompatible.
- It offers superior chemical resistance, which makes it ideal for medical and aerospace applications.
- Application of this requires specialized equipment.
Epoxy Resin Coatings
- Exceptional adhesion to various substrates.
- High mechanical strength and durability.
- Good protection against chemicals and moisture.
- The curing process involves heat, which might affect temperature-sensitive components.
Fluoropolymer Coatings
- It exhibits exceptional chemical resistance against corrosive agents.
- Wide temperature tolerance range.
- It has a low friction coefficient, making it ideal for components with moving parts.
- Complex application process requiring heat for curing.
Nano Coatings
- Utilizes nanotechnology to create ultrathin and highly protective layers.
- It offers excellent barrier properties against moisture and contaminants.
- Precision application is required, often applied as a secondary process.
Selecting the suitable conformal coating material depends on the application’s requirements, including operating environment, component sensitivity, and desired protective qualities. Each type of material has its trade-offs, making it crucial to evaluate and match the coating material to the intended application for optimal performance and longevity of electronic devices.
Acrylic Conformal Coatings
Acrylic conformal coatings represent a popular choice in protective coatings for electronic components. These coatings offer a range of benefits that make them suitable for various applications. Here are some key points about acrylic conformal coatings:
- Versatility:Acrylic coatings are known for their adaptability and ease of application. You can brush, spray, or dip these coatings onto the components, enabling efficient coverage.
- Moisture Resistance:Acrylic coatings provide reasonable protection against moisture and humidity. This property becomes valuable when electronic components face exposure to varying moisture levels.
- Dielectric Properties:These coatings exhibit reliable dielectric properties, ensuring that they do not interfere with the electrical performance of the coated components.
- Transparency:Acrylic coatings are transparent when applied in thin layers, allowing for easy visual inspection of the components after coating. This transparency aids in detecting potential issues or defects.
- UV Tracing:Manufacturers formulate certain acrylic coatings with UV traceability, allowing them to utilize UV light for quality control and verification of coating coverage.
- Ease of Repair and Rework:Acrylic coatings can be easily repaired or reworked. Their solvent-based nature makes removing and reapplying the coating possible without significant challenges.
- Cost-Effectiveness:Acrylic coatings are generally cost-effective compared to other conformal coatings, making them a practical choice for high-volume production.
However, it’s essential to consider the limitations of acrylic conformal coatings:
- Chemical Resistance:Acrylic coatings may not offer the same level of chemical resistance as other coatings, which could be a concern in chemically harsh environments.
- Temperature Limits:Acrylic coatings have moderate temperature resistance. Extreme temperature variations affect their performance, making them less suitable for specific harsh environments.
Acrylic conformal coatings balance ease of use, moisture resistance, and cost-effectiveness. Their versatility and straightforward application process make them a favored choice in many electronic applications. However, careful consideration of the operating environment and specific requirements of the components is necessary to ensure the optimal performance and longevity of the coated electronic devices.
Silicone Conformal Coatings
People recognize silicone conformal coatings for their unique properties and versatility in safeguarding electronic components. Here are some critical points about silicone conformal coatings:
- Flexibility and Elongation:One of the standout features of silicone coatings is their exceptional flexibility and elongation, making them an excellent choice for components subjected to vibrations and mechanical stress.
- High-Temperature Resistance:Silicone coatings can withstand various temperatures, making them well-suited for applications in high-temperature environments.
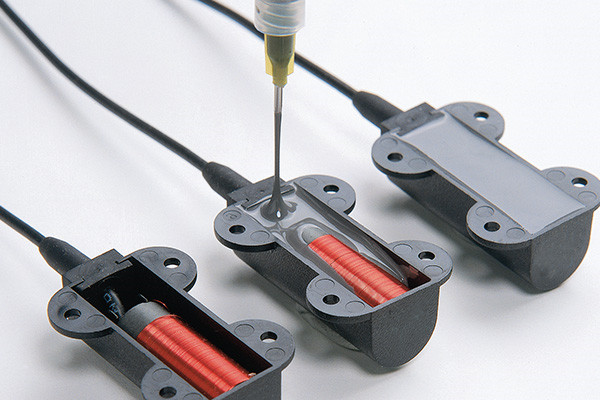
- Moisture Protection:Silicone coatings offer good moisture resistance, preventing water and humidity from infiltrating and damaging electronic components.
- Dielectric Properties:These coatings possess dielectric solid properties, ensuring that they do not compromise the electrical performance of coated components.
- Transparency:In thin layers, silicone coatings are transparent, allowing for easy visual inspection of coated components.
- Outgassing:However, it’s important to note that some silicone formulations may exhibit outgassing when exposed to high temperatures, potentially affecting sensitive components or surrounding materials.
- UV Tracing:Similar to acrylic coatings, certain silicone coatings can also be formulated with UV traceability, facilitating quality control and inspection processes.
- Harsh Environments:People commonly choose silicone coatings for applications in harsh environments, where their resistance to chemicals and moisture offers distinct advantages.
- Complex Application:The application process for silicone coatings might be more complicated than other types, requiring specialized equipment.
- Component Compatibility:While silicone coatings are compatible with various substrates, testing compatibility with specific materials and components is essential to prevent any adverse reactions.
Silicone conformal coatings offer robust flexibility, high-temperature resistance, and moisture protection. Their suitability for challenging environments and ability to withstand mechanical stress makes them a preferred choice for applications where these properties are essential. However, when selecting silicone coatings for electronic components, you should carefully consider the potential for outgassing and the specialized application process.
Polyurethane Protective Coatings
Polyurethane protective coatings are a versatile and durable choice for conformal coating applications. Their remarkable resistance to chemicals, abrasion, and moisture, and the ability to customize formulations for different temperature ranges, positions them as a reliable solution for safeguarding electronic components across various industries and environments.
Versatility and Durability
Polyurethane protective coatings have become a robust and versatile choice for conformal coating applications. Their unique properties make them a preferred material for safeguarding electronic components in various environments.
Chemical and Solvent Resistance
Polyurethane coatings excel in providing exceptional chemical and solvent resistance. This attribute suits them well for applications where components face exposure to harsh chemicals, solvents, or corrosive substances.
High Abrasion Resistance
One of the standout features of polyurethane coatings is their high abrasion resistance. This quality is precious for components subjected to mechanical stress or friction, ensuring longevity and reliability.
Moisture and Humidity Protection
Polyurethane coatings protect moisture and humidity, preventing water ingress and potentially damaging sensitive electronics. This property is crucial in environments with varying levels of humidity.
Temperature Tolerance
While polyurethane coatings generally exhibit moderate temperature resistance, you can tailor formulations to withstand extreme temperature fluctuations. This adaptability allows them to perform effectively in various operating conditions.
Application Flexibility
You can apply polyurethane coatings through various methods, including spraying, brushing, or dipping, which offers flexibility in the coating process. However, their thicker nature might impact fine-pitch components.
Considerations and Trade-offs
Despite their many advantages, it’s essential to acknowledge specific considerations when using polyurethane coatings. Their relatively thicker nature might lead to challenges with intricate or delicate components. Additionally, curing processes often involve heat, which could affect temperature-sensitive elements.
Parylene Coatings for Delicate Electronics
In the ever-evolving landscape of electronics, the demand for durable and reliable components has led to the development of advanced protection measures. Conformal coatings, specialized materials applied to electronic components, play a pivotal role in safeguarding them against environmental factors such as moisture, chemicals, and physical stress. Selecting an appropriate conformal coating material is crucial to ensure optimal electronic device performance, longevity, and functionality across various industries. This exploration delves into the diverse conformal coating materials, examining their unique properties, advantages, and considerations. From the versatile acrylic coatings to the intricate perylene options, this journey sheds light on the options available to engineers and manufacturers seeking to fortify their delicate electronic innovations.
Unique Vapor Deposition Process
Parylene coatings have gained significant attention as a specialized conformal coating material, particularly for delicate electronics. What sets them apart is their unique deposition process. Parylene is applied as a vapor, which allows it to conform precisely to intricate shapes and small components, ensuring complete coverage without compromising functionality.
Ultra-Thin and Transparent
Parylene coatings are fragile, often measuring only a few microns in thickness. This ultra-thin layer adds minimal weight and volume to the coated components, preserving the delicate nature of sensitive electronics. The transparency of parylene coatings enables easy visual inspection after application.
Superior Chemical Resistance
One of the most remarkable attributes of parylene coatings is their superior chemical resistance. They can withstand various chemicals, making them ideal for applications in chemically aggressive environments, such as medical devices and aerospace components.
Biocompatibility and Medical Applications
Parylene coatings are biocompatible and FDA-approved, making them suitable for medical devices and implants. Their non-toxic nature and ability to adhere uniformly even to complex medical components make them invaluable for ensuring safety and longevity.
Challenges and Precision Application
While parylene coatings offer exceptional benefits, their intricate application process requires specialized equipment. The deposition process involves vapor-phase polymerization in a vacuum chamber, demanding precision and expertise to achieve consistent and reliable coatings.
Protection Against Moisture and Contaminants
In electronics, the battle against the elements is a constant one. Moisture, chemicals, dust, and contaminants pose significant threats to the functionality and longevity of electronic components. To counter these challenges, engineers and manufacturers turn to conformal coating materials – specialized protective layers that serve as a shield against environmental hazards. This exploration delves into the crucial role of conformal coating materials in providing robust protection against moisture and contaminants, examining the types of coatings available, their unique attributes, and their benefits to various industries.
Guarding Against Moisture: A Multifaceted Challenge
Moisture infiltration is a pervasive concern for electronic devices, as it can lead to corrosion, short circuits, and performance degradation. Conformal coatings are a barrier against moisture, preventing intrusion into sensitive components. Silicone and acrylic coatings create an impenetrable barrier when exposed to humid or wet conditions.
Resisting Chemical Assault: Defense Mechanisms in Coating
Chemical exposure is another formidable adversary that electronics face. Specific industries, such as manufacturing and automotive, are rife with corrosive agents that can compromise components over time. Conformal coatings like polyurethane and perylene resist various chemicals, protecting against deterioration caused by aggressive substances.
Fortifying Against Contaminants: Dust and Particles
Beyond moisture and chemicals, electronic devices are susceptible to the accumulation of dust, dirt, and particles that can impede functionality. Conformal coatings create a barrier, preventing the intrusion of these contaminants and ensuring devices perform optimally in settings where cleanliness is paramount, such as medical equipment and aerospace applications.
Utilizing conformal coating materials to safeguard electronics against moisture, chemicals, and contaminants is a pivotal strategy in ensuring the reliability and longevity of electronic components. By understanding the diverse attributes of different coating materials and tailoring their selection to the specific demands of each application, engineers can confidently navigate the challenges posed by the elements and create electronic innovations that thrive in even the harshest environments.
Chemical and Solvent Resistance
Conformal coating materials play a pivotal role in fortifying electronic components against the corrosive effects of chemicals and solvents. This layer of protection is particularly critical in industries where exposure to aggressive substances is common, such as manufacturing, automotive, and chemical processing.
Polyurethane Coatings: A Shield Against Chemical Assault
- Polyurethane coatings provide exceptional chemical resistance, making them preferred in environments where corrosive agents expose components.
- These coatings act as a barrier, preventing chemicals from infiltrating and compromising the integrity of sensitive electronics.
- The ability of polyurethane coatings to withstand a wide range of chemical substances enhances the longevity and reliability of electronic devices in challenging settings.
Parylene Coatings: Unyielding in Harsh Environments
- Parylene coatings showcase remarkable resistance to chemicals and solvents, rendering them suitable for applications in aerospace and medical devices.
- These coatings maintain their integrity even when subjected to aggressive substances, safeguarding delicate electronic components from deterioration.
- Parylene’s unique vapor deposition process ensures that it forms a consistent and uniform protective layer that withstands chemical challenges.
Trade-offs and Considerations
While chemical and solvent resistance is a crucial advantage of these conformal coatings, it’s essential to consider the application’s specific requirements. To ensure optimal performance, one must carefully evaluate factors such as temperature fluctuations, substrate compatibility, and application methods.
Strengthening Resistance for Long-Term Reliability
Conformal coating materials with robust chemical resistance properties provide protection in electronics, where exposure to corrosive chemicals and solvents is a constant threat. Whether through the robust capabilities of polyurethane coatings or the precision of perylene, these coatings enhance the longevity and reliability of electronic components, ensuring that they can thrive even in the harshest chemical environments.
Thermal and Electrical Insulation
Thermal and electrical insulation are crucial in various industries, ensuring optimal performance and safeguarding against potential hazards. Effective insulation materials mitigate heat transfer and electrical conduction, preventing energy loss and possible short circuits. Thermal and electrical insulation synergy is pivotal in the electronics, aerospace, construction, and automotive sectors. Key points to consider include:
- Material Selection:Choosing a suitable insulation material is paramount. Options like fiberglass, ceramic fiber, foam, and mineral wool offer varying degrees of thermal resistance and electrical non-conductivity.
- Energy Efficiency:Thermal insulation reduces heat flow between hot and cold areas, enhancing energy efficiency in appliances, buildings, and industrial processes.
- Electrical Safety:Electrical insulation materials prevent unintended current flow, reducing risks of shocks, fires, and equipment damage. Dielectric materials, such as rubber and plastic, are commonly used for cable and wire insulation.
- High-Temperature Applications:In high-temperature environments, specialized materials like ceramic fibers excel due to their ability to withstand extreme temperatures while maintaining insulation efficiency.
- Thermal Conductivity:Low thermal conductivity materials like aerogels are increasingly popular for providing effective insulation while minimizing bulk and weight.
Conformal Coating Material: Enhancing Protection and Longevity
Conformal coating materials protect sensitive electronic components from environmental factors such as moisture, dust, chemicals, and physical damage. These coatings form a protective layer that conforms to the contours of the components, providing comprehensive coverage and extending their operational lifespan. Consider these essential aspects:
- Coating Types:Various coating materials, such as silicone, acrylic, epoxy, and polyurethane, offer distinct attributes, including flexibility, chemical resistance, and temperature stability.
- Environmental Protection:Conformal coatings shield circuit boards and electronic assemblies from harsh environments, preventing corrosion and electrical interference.
- Application Techniques:Different application methods like spraying, dipping, and brushing offer flexibility to suit various component shapes and sizes, ensuring even and consistent coverage.
- Dielectric Properties:Conformal coatings must possess adequate dielectric properties to prevent electrical short circuits while providing insulation.
- Adhesion and Durability:A robust coating should adhere firmly to the substrate and withstand mechanical stresses, temperature fluctuations, and chemical exposure.
- Optical clarity:When visual inspection is crucial, maintaining optical clarity after coating is vital for quality control and troubleshooting.
Thermal and electrical insulation and conformal coating materials are fundamental to achieving optimal performance, safety, and longevity in diverse industries. Selecting the appropriate materials and application methods is critical to ensure that components and systems function reliably under challenging conditions, contributing to enhanced operational efficiency and reduced maintenance costs.
Conformal Coating Techniques
Conformal coatings are essential for safeguarding electronic components against environmental stressors, but selecting the proper application technique is equally crucial. Various methods offer distinct advantages based on component complexity, production volume, and coating material characteristics. Consider the following techniques:
- Spray Coating:Utilizing an airbrush or automated spray equipment, this method offers quick and even coverage for large batches of components. It’s suitable for complex geometries and allows adjustment of coating thickness. Careful masking is required to prevent overspray.
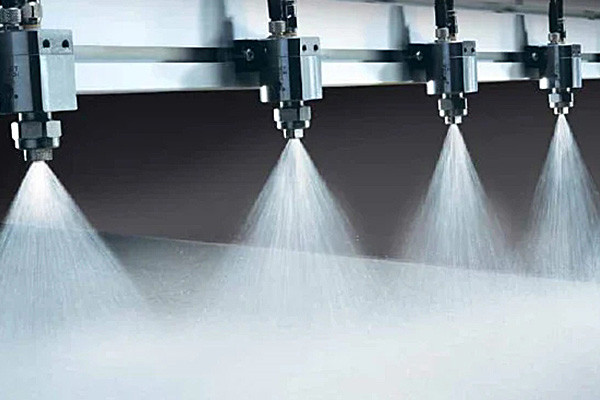
- Dip Coating:Components are immersed into a liquid coating material and then withdrawn at controlled speeds. This technique provides consistent coverage even on intricate shapes, with the option to control the thickness by adjusting the withdrawal speed. Drainage and proper curing are critical for uniformity.
- Brush Coating:Hand or automated brushing ensures precise coatings application to specific areas, making it suitable for selective coating or touch-ups. It’s cost-effective but might require skilled labor to ensure uniformity.
- Selective Coating:Robotic dispensing systems or controlled nozzles target specific areas, offering accuracy for intricate assemblies. This technique minimizes waste and reduces the need for masking.
- Vapor Deposition:Vacuum-based methods like chemical vapor deposition (CVD) and physical vapor deposition (PVD) allow thin, uniform coatings on complex shapes. These techniques are suitable for specialized applications but can be capital-intensive.
- Curing and Drying:After application, curing or drying the coating material is essential to ensure proper adhesion and functionality. Heat, UV light, or chemical reactions may be employed based on the coating material’s characteristics.
- Inspection and Quality Control:Regular inspection is crucial to identify defects like voids, pinholes, or uneven thickness. Automated inspection systems and manual checks aid in maintaining coating quality.
Selecting the appropriate conformal coating technique depends on factors like the component’s design, production volume, coating material properties, and the desired level of protection. Balancing efficiency, precision, and cost-effectiveness ensures that components are shielded from environmental stressors while maintaining optimal performance and longevity.
Electronics in Harsh Environments
In today’s interconnected world, extreme conditions often expose electronics to risks that can compromise their functionality and longevity. Adequate protection is paramount to ensure electronic components’ resilience and reliability in harsh environments. Key considerations include:
- Temperature Extremes:Electronics can face high and low temperatures, which may cause performance degradation or failure. Thermal management solutions such as heat sinks, phase change materials, and thermoelectric modules are crucial.
- Moisture and Humidity:Moisture can lead to corrosion, short circuits, and electrical interference. Conformal coatings act as a barrier, preventing moisture infiltration and safeguarding components.
- Chemical Exposure:Industries like automotive, aerospace, and manufacturing involve exposure to chemicals that can corrode or degrade electronics—conformal coatings with chemical resistance shield components from these hazards.
- Vibration and Shock:Vibrations and mechanical shocks can dislodge components or damage solder joints. Secure mounting, shock-absorbing materials, and conformal coatings with flexibility are essential.
- Dust and Particles:Dust and particles can accumulate on components, leading to overheating and malfunction. Proper enclosures, gaskets, and conformal coatings prevent particle ingress.
- UV Radiation:Outdoor electronics face UV radiation, which can degrade materials and affect performance. UV-resistant conformal coatings provide an extra layer of protection.
Conformal Coating Material: A Shield Against Harsh Conditions
Conformal coatings play a pivotal role in protecting electronic components from the challenges posed by harsh environments. They provide a barrier against moisture, chemicals, and physical stressors, extending the operational life of the electronics. Consider these factors when selecting conformal coating materials:
- Material Compatibility:Choose coatings compatible with the substrate and components to ensure proper adhesion and performance.
- Environmental Conditions:Select coatings based on the specific ecological stressors the electronics will face, such as moisture, chemicals, or UV radiation.
- Application Method:Different coating techniques, such as spray, dip, or selective coating, offer varying precision and coverage, catering to the component’s complexity and volume.
- Curing Process:Understand the curing requirements of the coating material to ensure proper adhesion and protection.
- Thickness and Coverage:Coating thickness and coverage should be optimized to protect without interfering with component functionality or heat dissipation.
- Inspection and Testing:Regularly inspect and test coated components to identify defects and ensure consistent quality.
Incorporating suitable conformal coating material and techniques into the design and production process of electronics destined for harsh environments is vital to guarantee their reliability, functionality, and longevity in challenging conditions.
Aerospace and Defense Applications
Conformal coating materials have emerged as a critical technology in the aerospace and defense sectors due to their ability to enhance the durability, reliability, and performance of electronic components and systems in challenging environments. These specialized coatings offer a range of benefits, making them indispensable in various applications within the industry.
- Protection Against Harsh Environments:Conformal coatings protect against extreme conditions such as moisture, saltwater, chemicals, and temperature variations, safeguarding sensitive electronics in aerospace and defense equipment. This resilience ensures consistent functionality and prevents costly maintenance or replacements.
- Vibration and Shock Resistance:Aerospace and defense systems often experience intense vibrations and shocks during operation, which can lead to the deterioration of electronics. Conformal coatings with flexible and shock-absorbing properties help mitigate these effects by preventing physical stress from directly impacting components.
- Electromagnetic Interference (EMI) Shielding:In an increasingly connected world, EMI shielding has become paramount. Conformal coatings containing conductive materials can effectively reduce electromagnetic interference, enhancing the performance of critical communication and navigation systems in aircraft and military vehicles.
- Extended Lifespan:Conformal coatings significantly extend the lifespan of electronics by minimizing the effects of corrosion and oxidation. Aerospace applications, particularly those with limited maintenance access, such as satellites, underscore the significance of this level of value, where ensuring longevity becomes imperative for mission success.
- Miniaturization and Weight Reduction:As aerospace and defense systems become more compact and lightweight, the challenges of maintaining reliability while reducing size increase. Conformal coatings protect densely packed components without adding significant weight, contributing to overall weight reduction efforts.
- Customization for Diverse Surfaces:Aerospace and defense applications encompass various materials and shapes. One can tailor conformal coatings to adhere to multiple surfaces, including irregular ones, ensuring complete coverage and protection without compromising performance.
Conformal coating materials play an indispensable role in aerospace and defense applications, enhancing the resilience and longevity of electronic systems in the face of demanding operational environments. From protecting against harsh conditions to offering EMI shielding and enabling miniaturization, these coatings contribute to the advancement and reliability of critical technologies that power modern aerospace and defense capabilities.
Medical Device Coatings
Conformal coatings are a specialized category of materials used in medical devices to provide a protective and functional layer that conforms to the device’s shape, ensuring coverage even on intricate surfaces. These coatings are vital for enhancing device reliability, biocompatibility, and performance in various medical applications.
Advantages of Conformal Coatings
- Uniform Protection:Conformal coatings provide consistent coverage, protecting sensitive components from environmental factors like moisture, chemicals, and mechanical stress.
- Enhanced Durability:These coatings improve the device’s resistance to wear, abrasion, and corrosion, which is crucial for long-term reliability in medical equipment.
- Biocompatibility:Formulators can create conformal coatings to be biocompatible, thereby reducing the risk of adverse reactions when the device comes into contact with bodily tissues or fluids.
- Insulation:They act as electrical insulators, safeguarding against short circuits and ensuring patient safety in devices with electronic components.
- Temperature and Chemical Resistance:Conformal coatings can withstand various temperatures and chemicals, making them suitable for devices used in diverse medical procedures.
Common Conformal Coating Materials
- Silicone Coatings:Due to their flexibility and resistance to moisture, silicone coatings are often used in implantable medical devices and electronics, appreciated for their biocompatibility.
- Parylene Coatings:Parylene offers excellent barrier properties, conforming well to complex shapes. Neurostimulation devices and implants widely utilize it.
- Acrylic Coatings:Acrylic coatings provide reasonable protection against moisture and environmental factors, making them suitable for various medical equipment.
- Urethane Coatings:Urethane coatings offer mechanical strength and durability, making them ideal for devices subject to constant movement or mechanical stress.
- Epoxy Coatings:Epoxy coatings are known for their strong adhesion and chemical resistance, making them suitable for devices exposed to harsh environments.
- Challenges and Considerations
- Thickness and Uniformity:Ensuring consistent coating thickness across complex device geometries is crucial for maintaining functionality and performance.
- Biocompatibility and Safety:Careful selection and testing of coating materials are essential to prevent adverse reactions or toxic effects when the device interacts with the body.
- Compatibility with Manufacturing Processes:Coating processes must align with device manufacturing methods, ensuring efficient and reliable application.
- Quality Control and Testing:Rigorous testing is necessary to verify coating uniformity, adhesion, and overall performance.
In the rapidly evolving landscape of medical device coatings, conformal coatings continue to play a vital role in ensuring the reliability and functionality of medical equipment, contributing to safer and more effective healthcare practices.
Consumer Electronics Protection
Consumer electronics have become integral to daily life, from smartphones and wearables to home appliances and entertainment devices. Conformal coating materials are employed as protective layers to ensure the longevity and reliability of these electronics in diverse environments. These materials offer a vital shield against various external factors, enhancing device performance and durability.
Significance of Conformal Coating in Consumer Electronics
- Environmental Protection:Conformal coatings safeguard electronics from moisture, dust, humidity, and other ecological elements, preventing damage and improving overall device resilience.
- Corrosion Resistance:Electronics used in outdoor or harsh conditions are prone to corrosion; conformal coatings act as barriers against corrosive agents, extending the device’s lifespan.
- Vibration and Mechanical Stress:Mechanical stress and beatings often subject consumer electronics to wear and tear; conformal coatings provide a cushioning layer that minimizes the impact of such pressures on internal components.
- Electrical Insulation:Conformal coatings insulate sensitive electronic components, preventing short circuits and maintaining device functionality.
- Thermal Management:Some coatings offer heat dissipation properties, managing device temperatures and preventing overheating, which is crucial for high-performance electronics.
Types of Conformal Coating Materials for Consumer Electronics
- Acrylic Coatings:Widely used due to their versatility and ease of application, they offer good moisture and environmental protection.
- Silicone Coatings:Silicone coatings, recognized for their flexibility and resistance to moisture, are suitable for wearable devices and electronics exposed to varying conditions.
- Urethane Coatings:Urethane coatings provide durability and mechanical strength, making them ideal for electronics in constant use or movement.
- Parylene Coatings:Parylene, which offers excellent barrier properties and conformability, is used in intricate electronics where a thin, uniform layer is required.
- Nano Coatings:Nanotechnology has introduced ultra-thin coatings with superior protection against moisture, UV radiation, and even bacterial growth, ideal for sensitive electronics.
Considerations and Challenges
- Coating Thickness:Achieving consistent coating thickness across intricate electronics designs can be challenging to maintain optimal protection.
- Compatibility with Electronics:The chosen coating material must not interfere with electronic functionality or impede signals.
- Manufacturing Integration:Coating processes should seamlessly integrate into the electronics manufacturing workflow for efficient application.
- Adhesion and Durability:Ensuring strong adhesion and durability of coatings, especially in devices with moving parts, is crucial.
Conformal coating materials are pivotal in safeguarding devices from environmental and operational challenges in consumer electronics. By enhancing durability, performance, and overall user experience, these coatings contribute to the continued advancement of electronic technology.
Testing and Quality Control
In the realm of electronics manufacturing, ensuring the reliability and performance of products is paramount. Conformal coating materials protect sensitive electronic components from environmental stresses, including moisture, dust, chemicals, and temperature fluctuations. To guarantee that these materials effectively serve their protective purpose, rigorous testing, and stringent quality control measures are imperative. This article delves into the significance of testing and quality control concerning conformal coating materials, shedding light on the multifaceted approaches utilized to ensure the durability and functionality of electronic devices.
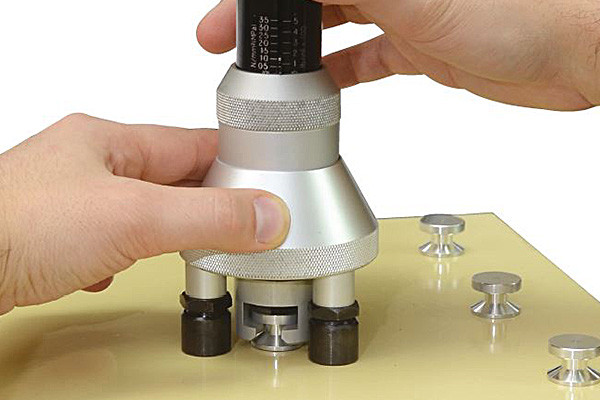
Analyzing Conformal Coating Material Properties
The first step in the testing and quality control process involves an in-depth analysis of the inherent properties of the chosen conformal coating material. These properties, including adhesion strength, flexibility, chemical resistance, and electrical insulation, are meticulously examined to ensure they align with the intended application requirements. Different testing techniques, such as peel tests, bend tests, and thermal cycling, assess the material’s ability to withstand mechanical stresses and environmental challenges over time.
Environmental Simulations for Real-World Scenarios
In electronics, various environmental conditions frequently subject devices to challenges. Conducting environmental simulation tests on conformal coating materials allows for the mimicry of real-world scenarios. These tests expose the coated electronic components to varying humidity levels, temperature extremes, and corrosive agents, allowing manufacturers to gauge how well the materials withstand these stressors. Simulations assist in predicting how long a coating will last and maintain its protective integrity.
Verification of Application Techniques
Quality control encompasses not only the coating material’s properties but also its application’s precision. Manufacturers employ different application techniques, such as spraying, dipping, or brushing, to ensure an even and uniform coating layer. Quality control involves validating that the chosen application method meets predetermined specifications, guaranteeing that each electronic component receives consistent and reliable protection.
Ensuring Compliance and Consistency
Beyond performance, regulatory compliance is another critical aspect of quality control for conformal coating materials. Various industries, including aerospace, medical devices, and automotive electronics, often establish specific standards that require fulfillment to ensure safety and reliability. We conduct rigorous testing to ensure that the materials adhere to these industry-specific regulations, instilling in end-users the confidence that the coated electronics meet the highest manufacturing standards.
Advancements in Coating Technology
Coating technology continues to evolve, driven by the demand for enhanced protection, performance, and functionality across various industries. One remarkable aspect of this evolution is the continuous development of conformal coating materials. These coatings, designed to provide a protective and functional layer that conforms to the shape of the substrate, have seen significant advancements, revolutionizing industries such as electronics, automotive, aerospace, and medical devices.
Innovations in Conformal Coating Materials
- Nanotechnology Integration:The integration of nanotechnology has led to the development of nano coatings, which offer ultra-thin yet highly effective protective layers. These coatings provide exceptional barrier properties against moisture, chemicals, and biological agents while maintaining minimal impact on the coated surface’s original properties.
- Hybrid Coatings:Advancements in material science have enabled the creation of hybrid conformal coatings that combine multiple functionalities. These coatings can incorporate properties such as corrosion resistance, thermal management, and electrical insulation, all within a single layer, optimizing the performance of coated components.
- Biocompatible and Bioactive Coatings:In medicine, conformal coatings have progressed to include biocompatible and bioactive materials. These coatings facilitate better integration of medical implants and devices with the body, promoting faster healing, reduced rejection rates, and personalized therapeutic effects.
- Self-Healing Coatings:Self-healing conformal coatings utilize innovative materials that can repair minor damage to the coating itself. This advancement is relevant in applications where the coated surface faces wear, mechanical stress, or external factors that could compromise the coating’s integrity.
- Smart Coatings:The concept of smart coatings has emerged, incorporating features such as responsiveness to environmental changes, color shifts, or even controlled drug release. These coatings are finding applications in areas like sensors, displays, and biomedical devices, expanding the possibilities of coated surfaces.
Challenges and Future Directions
As coating technology advances, several challenges persist. Ensuring the scalability of advanced coating processes, maintaining coating uniformity across complex geometries, and conducting thorough testing to verify functionality and longevity remain crucial. The future of conformal coatings holds promise in terms of personalized coatings, integration with Internet of Things (IoT) devices, and more sustainable and environmentally friendly coating materials.
The rapid evolution of conformal coating materials exemplifies the relentless pursuit of improved protection and performance across industries. These advancements continue redefining coated surfaces’ capabilities, ushering in a new era of innovation and application possibilities.
Environmental Considerations and Sustainability
As industries continue to prioritize environmental responsibility, the field of conformal coating materials is undergoing a significant shift toward sustainability. With growing concerns about the ecological impact of industrial processes, there is a pressing need to develop and implement environmentally friendly solutions that maintain the protective benefits of conformal coatings while minimizing adverse effects on the planet.
Biodegradable and Eco-Friendly Coatings
- Biodegradable Formulations:Researchers are exploring biodegradable conformal coating materials that break down naturally over time. These coatings reduce the accumulation of persistent pollutants in the environment and alleviate the long-term impact of discarded electronics and coated devices.
- Renewable Resources:Utilizing raw materials derived from renewable sources, such as plant-based polymers, helps reduce the reliance on fossil fuels and mitigates the environmental footprint of coating production.
- Water-Based Coatings:Water-based conformal coatings have gained traction due to their reduced volatile organic compound (VOC) emissions. These coatings offer lower environmental impact during application and contribute to improved air quality.
Reduced Energy Consumption and Waste
- Energy-Efficient Application Processes:Developing energy-efficient coating application methods minimizes the carbon footprint associated with the coating process. Techniques like spray-coating and dip-coating optimization reduce energy consumption while maintaining coating quality.
- Minimal Waste Generation:Designers create innovative coating processes to minimize waste generation by applying precision, reducing the necessity for excess coating material and subsequent disposal.
Lifecycle Considerations
- End-of-Life Management:Designing coatings with easy removability allows for efficient device recycling or disposal, preventing coatings from becoming pollutants during the disposal phase.
- Longevity and Durability:Coatings that enhance device durability and longevity contribute to the reduction of electronic waste by extending the useful life of coated products.
Regulatory Compliance and Eco Labels
- Compliance with Environmental Regulations:Sustainable conformal coatings aim to adhere to strict environmental regulations, ensuring that their production and use do not harm ecosystems or human health.
- Eco Labels and Certifications:Eco labels and certifications can help consumers identify products with reduced environmental impact, encouraging the adoption of sustainable conformal coatings.
Collaboration and Future Outlook
Sustainability in conformal coating materials necessitates collaboration among researchers, manufacturers, and regulatory bodies. The future of these coatings lies in developing innovative solutions that prioritize both protection and sustainability, aligning with the global movement towards greener practices across industries. As the demand for environmentally conscious options grows, the coating industry’s response will shape how we protect and preserve our world.
Conformal coating materials serve as a crucial line of defense in the world of electronics, protecting devices from the array of challenges posed by external elements. Their role in preserving the functionality, reliability, and longevity of electronic systems is indispensable. As technology advances and industries seek innovative ways to ensure device durability, conformal coating materials will remain instrumental in shaping the future of electronics protection. With ongoing research and improvements, these materials are poised to contribute to the development of smarter, more resilient electronic devices across a range of industries.