Anaerobic Adhesive And Sealant
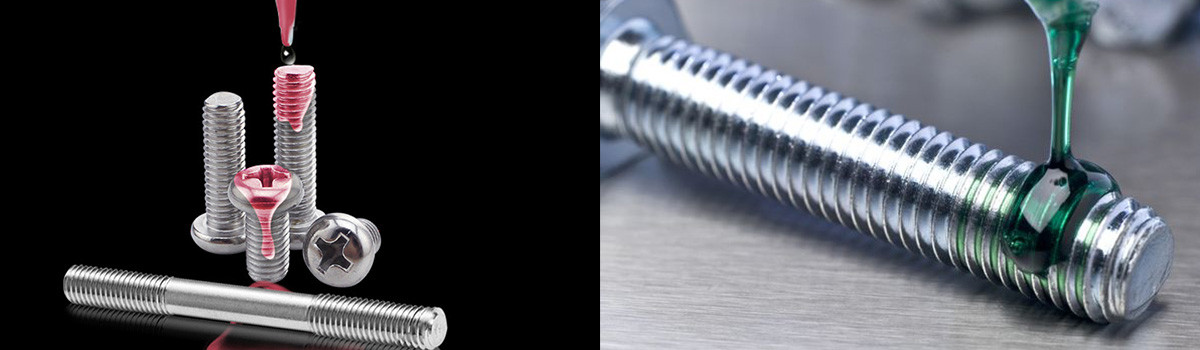
In the realm of modern manufacturing and industrial applications, the demand for reliable and durable bonding solutions has never been greater. Anaerobic adhesives and sealants have emerged as a remarkable solution, catering specifically to environments devoid of oxygen. These specialized adhesives offer exceptional bonding capabilities and sealing properties, playing a pivotal role in enhancing the performance and longevity of various products and assemblies across industries. This article delves into the world of anaerobic adhesives and sealants, exploring their applications, characteristics, benefits, and considerations.
Understanding Anaerobic Adhesives and Sealants
Due to their unique curing mechanism, anaerobic adhesives and sealants are indispensable bonding solutions that find widespread application across industries. Here are some key points to comprehend about these remarkable materials:
- Curing Process:Anaerobic adhesives and sealants remain liquid when air exposure, but they cure rapidly into a solid when deprived of oxygen. These adhesives and sealants initiate this transformation by responding to the absence of air and the presence of metal ions, often within the threads of fasteners and other assemblies.
- Strong Bonds:The resulting bonds exhibit exceptional strength and resistance to vibrations, impacts, and chemicals. Their ability to fill microscopic gaps ensures a tight seal and reliable adhesion, contributing to the overall structural integrity of assemblies.
- Versatile Applications:Industries apply these adhesives in various sectors, including automotive, manufacturing, construction, and electronics. They enhance performance, safety, and longevity in applications ranging from engine assembly and concrete anchoring to delicate electronic encapsulation.
- Surface Preparation:Successful application requires meticulous surface preparation. Clean and contaminant-free surfaces are vital for optimal bonding. Any grease, oil, or dirt on the surfaces can hinder the curing process and compromise bond strength.
- Substrate Compatibility:Understanding the compatibility between the adhesive and the substrate is crucial. Some substrates might inhibit the curing process, making choosing the appropriate adhesive formulation necessary.
- Curing Conditions: Factors like temperature and humidity play a role in curing. To achieve consistent and reliable results, following the manufacturer’s guidelines is essential.
- Safety Measures: Since these adhesives require the absence of air to cure, they can be sensitive to light and oxygen exposure. Proper storage in opaque containers and minimizing exposure to air during application are essential.
Anaerobic adhesives and sealants provide industries with efficient and robust bonding solutions. Even in challenging conditions, their ability to create strong bonds underscores their significance in modern manufacturing and construction. By grasping the fundamental principles of anaerobic curing and adhering to best practices, industries can harness the full potential of these adhesives, ensuring the longevity, safety, and performance of their products and assemblies.
How Anaerobic Adhesives Work
Anaerobic adhesives operate through a fascinating mechanism that distinguishes them from other bonding agents. Here are key points to understand about their functioning:
- Air Exclusion: Anaerobic adhesives require the absence of oxygen to initiate their curing process. When applied between two close-fitting surfaces, such as threaded fasteners or components of machinery, they remain in a liquid state due to the presence of air.
- Contact with Metals: The presence of metal ions, commonly found on metal surfaces, plays a pivotal role. These ions function as catalysts, promoting the adhesive’s cure when excluding oxygen.
- Gap Filling:One of the distinctive features of anaerobic adhesives is their ability to fill microscopic gaps between mating surfaces. As they cure, they flow into these gaps, resulting in a tight, secure bond that protects against leakage.
- Polymerization Process: Upon exclusion of air and in the presence of metal ions, anaerobic adhesives rapidly undergo polymerization. The linking of molecules forms a robust, cross-linked polymer structure.
- Curing Speed:The curing speed of anaerobic adhesives depends on temperature, humidity, and the specific formulation used. Higher temperatures generally accelerate the curing process.
- Bond Strength:The resulting bond is solid and durable, capable of withstanding mechanical stress, vibrations, and chemical exposure. Their robust bonding solutions make them perfect for use in applications that demand durability.
- Versatility:Anaerobic adhesives find applications in various industries, including automotive, manufacturing, and construction. Industries utilize them for thread locking, pipe sealing, and retaining bearings.
- Proper Application:To ensure optimal results, adequate surface preparation is crucial. Surfaces should be clean, dry, and free from contaminants like oils or greases. Following the manufacturer’s application and cure time guidelines is essential for achieving reliable bonding.
The mechanism behind anaerobic adhesives is a unique interplay of air exclusion, metal ions, and polymerization. Their ability to fill gaps and create strong bonds underlines their significance in various sectors. Understanding their working principles empowers industries to leverage these adhesives for enhanced product performance and reliability.
Advantages of Anaerobic Bonding
Anaerobic bonding offers a range of compelling advantages that make it a preferred choice in various industrial applications. Here are key points highlighting the benefits of this innovative bonding technique:
- Rapid Curing: Anaerobic adhesives are cured quickly without air, allowing for efficient production processes and reduced downtime. This rapid curing helps expedite assembly and enhances overall productivity.
- Strong and Durable Bonds:The resulting bonds are powerful and resistant to mechanical stress, vibrations, and chemicals. This durability ensures the longevity and reliability of assemblies, even in challenging environments.
- Gap Filling:Anaerobic adhesives uniquely fill microscopic gaps between mating surfaces, ensuring a tight seal and consistent bond strength. This feature is particularly advantageous for assemblies with irregular or uneven surfaces.
- Enhanced Performance:In applications such as thread locking, these adhesives prevent the loosening of fasteners due to vibrations or external forces, thereby improving the overall performance and safety of machinery and structures.
- Corrosion Protection:Anaerobic bonding can provide a barrier against moisture and corrosive substances, protecting metal components from degradation and extending their lifespan.
- Versatile Applications:These adhesives find use in diverse industries, from automotive to electronics, due to their adaptability and ability to cater to specific bonding needs.
- Cost-Effective: The rapid curing and strong bonding capabilities of anaerobic adhesives lead to efficient production processes and reduced maintenance requirements, resulting in potential cost savings.
- Reduced Waste: Unlike traditional bonding methods that might involve an excess adhesive application, anaerobic adhesives minimize waste due to their ability to fill gaps precisely.
- Environmental Friendliness: Reducing waste and energy-efficient curing contribute to a more environmentally friendly manufacturing process.
- Easy Application:Anaerobic adhesives are easy to apply and require minimal equipment. This simplicity in application adds to their overall convenience and usability.
Anaerobic bonding presents many advantages, making it a compelling choice for various industrial scenarios. From its quick curing and exceptional bonding strength to its adaptability and cost-effectiveness, anaerobic bonding has proven invaluable for enhancing production processes and ensuring the reliability of assemblies across different sectors.
Applications in Thread locking
Thread locking, a crucial aspect of mechanical assemblies, benefits significantly from the unique properties of anaerobic adhesives. Here are vital points illustrating the applications and advantages of anaerobic thread locking:
- Vibration Resistance:Anaerobic thread lockers prevent the loosening of threaded fasteners due to vibrations, shocks, or dynamic loads. The adhesive fills the gaps between threads, creating a secure bond that resists movement.
- Enhanced Safety:In industries where safety is paramount, such as automotive and aerospace, anaerobic thread lockers play a crucial role in preventing critical fastener failures that have the potential to cause accidents or equipment malfunctions.
- Maintenance Reduction: By keeping fasteners firmly in place, these adhesives reduce the need for frequent maintenance and tightening, leading to cost savings and improved operational efficiency.
- Corrosion Prevention: Anaerobic thread lockers provide a protective barrier that helps shield threaded connections from moisture and corrosive agents, which can extend the lifespan of components.
- Temperature and Chemical Resistance: Threadlockers can withstand various temperatures and resist multiple chemicals, making them suitable for applications in diverse environments.
- Ease of Disassembly:While providing solid and secure bonds, anaerobic thread lockers allow for relatively easy disassembly when required. Heat and hand tools can break the bond without damaging the threads.
- Variety of Strengths: Threadlockers have different strengths, ranging from low to high, catering to specific requirements. This flexibility ensures optimal performance across various applications.
- Automotive Industry: Anaerobic thread lockers play a vital role in automotive manufacturing, securing critical components such as engine mounts, brake calipers, and suspension systems.
- Machinery Assembly: In manufacturing, thread lockers prevent loosening bolts and screws in machinery and equipment, ensuring consistent performance.
- Construction Sector:Threadlockers find use in construction applications, such as securing bolts and nuts in infrastructure projects where structural integrity is essential.
Anaerobic thread lockers offer indispensable benefits in preventing the loosening of threaded fasteners. Their ability to resist vibrations, enhance safety, reduce maintenance, and protect against corrosion makes them a go-to choice for industries that rely on secure and durable mechanical assemblies. In automotive, manufacturing, or construction, anaerobic thread lockers contribute to the overall reliability and longevity of various structures and systems.
Thread Sealing with Anaerobic Sealants
Anaerobic sealants offer an effective solution for thread-sealing applications, providing a reliable and durable bond in various industries. Here are key points outlining the significance and advantages of using anaerobic sealants for thread sealing:
- Leak Prevention:Specifically formulated anaerobic sealants create a secure seal between threaded components, effectively preventing leaks in fluid-carrying systems like pipes, fittings, and hydraulic connections.
- Gap Filling:These sealants possess excellent gap-filling capabilities, ensuring a tight and uniform seal even in threads with minor imperfections or irregularities.
- Chemical Resistance: Anaerobic sealants resist a wide range of chemicals, making them suitable for applications where exposure to aggressive fluids or chemicals is daily.
- Temperature Resistance:Threaded connections with anaerobic sealants can withstand a broad temperature range, maintaining their sealing properties even under extreme conditions.
- Vibration Damping:Anaerobic sealants not only seal against leaks but also provide a level of vibration dampening, enhancing the stability of assemblies in dynamic environments.
- Easy Disassembly: While creating a strong seal, anaerobic sealants allow for disassembly when needed. Applying moderate force and using standard tools can break the seal without damaging components.
- Variety of Formulations:Anaerobic sealants come in different formulations, catering to specific needs such as low-strength, medium-strength, and high-strength sealants, providing flexibility in choosing the right solution for each application.
- Automotive and Plumbing Applications:Anaerobic sealants find extensive use in the automotive industry for sealing threaded connections in engines and fluid systems. Similarly, plumbing ensures leak-free connections in water and gas pipelines.
- Industrial Machinery:These sealants contribute to the reliability of industrial machinery by sealing threaded joints in hydraulic systems, pneumatic systems, and various mechanical assemblies.
- Maintenance and Repair:Anaerobic sealants are valuable in maintenance and repair tasks, offering quick and effective sealing of threaded connections without requiring specialized equipment.
Anaerobic sealants are a versatile and effective solution for thread-sealing applications across industries. Their leak-prevention capabilities, resistance to chemicals and temperature fluctuations, and ability to dampen vibrations make them a trusted choice for ensuring the integrity and functionality of threaded connections in various environments.
Gasketing and Flange Sealing
Gasketing and Flange Sealing are critical processes in various industries to ensure leak-proof connections between components, particularly in applications involving fluids, gases, or chemicals under pressure. These processes are pivotal in preventing leaks, minimizing environmental hazards, and maintaining operational efficiency. Key points in gasketing and flange sealing include:
- Gasket Materials:Manufacturers choose gasket materials, such as rubber, silicone, metal, graphite, and PTFE, from a wide range of options based on their compatibility with the fluids or gases being sealed, as well as the temperature and pressure conditions.
- Flange Design:Flanges are the connecting points where two components meet. Designers create them to distribute the sealing force evenly across the gasket, ensuring a secure and tight seal. Flange designs, including raised faces, flat faces, and ring joint flanges, can vary.
- Sealing Techniques:Engineers employ various sealing techniques, including compression gaskets, which involve compressing the gasket between two flanges using bolts. New methods like adhesive gasketing and elastomeric seals are also gaining popularity for their efficiency and reliability.
- Preparation and Cleaning:Proper surface preparation is crucial, and you must thoroughly clean the flanges to remove contaminants that could compromise the seal. Any irregularities on the flange surfaces can affect the sealing effectiveness.
- Tightening Procedures:Achieving the correct bolt torque is essential. Under-tightening can lead to leaks, while over-tightening can damage the gasket or flanges. Bolt-tightening sequences are often specified to ensure uniform pressure distribution.
- Environmental Factors:When you select gasketing materials, consider the operating environment and take into account factors like temperature fluctuations, chemical exposure, and potential vibration.
- Testing and Inspection:Rigorous testing, such as leak testing and pressure testing, ensures the integrity of the seal before putting the system into operation. Regular inspection and maintenance are essential for long-term reliability.
- Safety and Regulations:Proper gasketing and flange sealing are crucial for workplace safety and environmental protection. Many industries must adhere to regulations and standards to prevent leaks that could lead to accidents or ecological contamination.
Retaining Compounds: Enhancing Assembly Strength
Retaining compounds, known for their exceptional bonding properties, enhance assembly strength across diverse industries. These high-performance adhesives offer several benefits contributing to robust and reliable assemblies, making them an integral part of modern manufacturing processes. Key points regarding the use of retaining compounds for enhancing assembly strength include:
1.Gap Filling:Retaining compounds fill microscopic gaps between mating components, creating a seamless, load-bearing connection. Eliminating the requirement for precise machining or tight tolerances simplifies assembly processes.
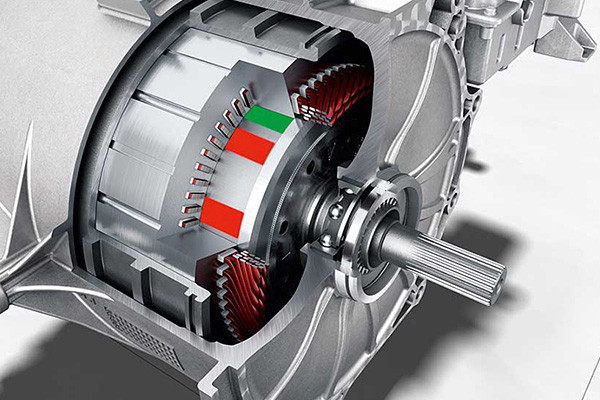
2.Increased Load-Bearing Capacity: By evenly distributing stresses and loads, these compounds significantly enhance the load-bearing capacity of assemblies, reducing the risk of premature failure or loosening over time.
3.Vibration and Impact Resistance:Retaining compounds provide excellent resistance to vibration and impact, making them ideal for applications subject to dynamic forces or constant movement.
4.Corrosion Prevention:These compounds create a protective barrier, preventing metal-to-metal contact and reducing the risk of corrosion, even in harsh environments.
5.Temperature and Chemical Resistance:Formulators design retaining compounds to withstand various temperatures and resist different chemicals, ensuring reliable performance in challenging conditions.
6.Uniform Distribution of Stress:Unlike traditional fastening methods like screws or bolts, retaining compounds ensure a uniform stress distribution, minimizing stress concentrations that could weaken the assembly.
7.Versatility:Retaining compounds can be used with various materials, including metals, plastics, and composites, making them versatile solutions for diverse assembly applications.
8.Cost and Weight Reduction:These compounds can replace traditional fasteners, reducing the number of parts and potentially cutting down on assembly costs and overall weight.
9.Ease of Application:Retaining compounds are applied as liquids and cured into a solid adhesive, ensuring complete coverage and eliminating the risk of loosening due to vibration or thermal expansion.
10.Time Efficiency:The curing process of retaining compounds can be accelerated using heat or activators, enabling faster assembly line production.
Curing Process and Activation
Materials’ curing process and activation hold paramount importance across industries, influencing the performance, durability, and reliability of various products and applications. Key points regarding curing processes and activation methods include:
- Chemical Transformation:Curing involves inducing chemical reactions in materials to achieve desired physical and chemical properties, such as strength, hardness, adhesion, and resistance to environmental factors.
- Heat Curing:Applying controlled heat accelerates the curing process by increasing molecular mobility and reaction rates. Manufacturers commonly use this method for polymers, coatings, adhesives, and composites.
- UV Curing:Ultraviolet (UV) light initiates photopolymerization in UV-curable materials. This fast and energy-efficient process is employed in coatings, inks, and adhesives, as it eliminates the need for extended heat exposure.
- Moisture Curing:Certain materials cure upon exposure to moisture in the air. This method is advantageous for applications with impractical controlled heat or UV light.
- Two-Part Systems:By mixing two components (resin and hardener), you initiate a chemical reaction that leads to curing. This approach controls curing time and finds common usage in epoxy adhesives and resins.
- Catalysts and Activators:Chemical catalysts or activators are added to formulations to initiate or accelerate curing. These can be particularly useful for low-temperature curing or in applications requiring faster production rates.
- Induction Heating:Induction heating induces electrical currents within conductive materials, rapidly generating heat for localized curing in metals and other conductive materials.
- Plasma Activation:Plasma treatment modifies material surfaces, enhancing adhesion and promoting better bonding in applications such as electronics and medical devices.
- Post-Curing:Some materials require post-curing, a secondary process that ensures complete cross-linking and optimization of material properties after the initial curing phase.
- Adhesion and Bonding:Proper activation methods significantly impact the adhesion strength between materials, ensuring reliable bonds in adhesive applications.
- Quality Control:Monitoring and controlling curing processes are essential for maintaining product quality and performance consistency.
Compatibility with Different Substrates
Achieving compatibility between materials and substrates is critical in numerous industries, ensuring optimal performance, adhesion, and functionality of various products. Key points regarding compatibility with different substrates include:
- Surface Properties:Understanding the surface properties of substrates, such as roughness, porosity, and energy, is essential to select appropriate materials and adhesion methods.
- Adhesion Promoters:Sometimes, substrates require adhesion promoters or primers to enhance bonding with materials that might not naturally adhere well to them.
- Material Selection:Choosing materials with compatible chemical and physical properties is crucial to prevent delamination, peeling, or reduced performance over time.
- Coefficient of Thermal Expansion:Materials and substrates should have similar coefficients of thermal expansion to avoid stress-induced failures due to temperature changes.
- Flexibility and Rigidity:Matching the flexibility or rigidity of materials and substrates is vital to prevent cracking or breaking under stress.
- Thermal Conductivity:In applications where heat transfer is essential, selecting materials and substrates with compatible thermal conductivities ensures efficient performance.
- Chemical Compatibility:For applications involving exposure to chemicals or corrosive environments, compatibility between materials and substrates prevents degradation and ensures longevity.
- Electrical Properties:Proper functioning of electronics and electrical applications relies heavily on the compatibility of materials and substrates with the desired electrical properties.
- Coating and Treatment Compatibility:Substrates with coatings or treatments need compatible materials to prevent layer degradation or treatment degradation.
- Mechanical Properties:Matching mechanical properties such as hardness, tensile strength, and elasticity helps maintain structural integrity and prevent premature failure.
- Environmental Conditions:Considering the environmental conditions the product will face, such as temperature variations, humidity, and exposure to UV light, is crucial for compatibility.
- Testing and Validation:Conducting compatibility tests, such as adhesion tests, shear tests, or exposure to simulated operational conditions, ensures the chosen materials and substrates will perform as expected.
Ensuring compatibility between materials and substrates is paramount for the successful performance and longevity of products in various industries. Manufacturers can achieve strong bonds, reliable functionality, and overall product excellence through careful material selection, surface preparation, and understanding of the application’s functional requirements. The interplay between materials and substrates is a fundamental consideration that directly impacts the quality and success of the end product.
Temperature and Chemical Resistance
Temperature and chemical resistance are pivotal in material selection across industries, ensuring optimal performance and durability in challenging environments. Key points concerning temperature and chemical resistance include:
- Temperature Range:Materials must be chosen based on their ability to withstand specific temperature ranges, whether extremely low or high, without undergoing deformation, degradation, or loss of mechanical properties.
- Thermal Expansion:Understanding how materials expand, and contract with temperature changes is crucial to prevent warping, cracking, or stress-induced failures.
- Heat Insulation:Applications that require maintaining temperature differentials or thermal protection demand materials with high resistance to heat transfer.
- Chemical Compatibility:Resistance to chemicals, acids, bases, solvents, and corrosive substances prevents material deterioration, preserving structural integrity and functionality.
- Corrosion Resistance:Choosing materials with inherent corrosion resistance is vital in environments where exposure to moisture, chemicals, or aggressive substances could lead to degradation over time.
- Chemical Inertness:In applications involving contact with chemicals, selecting chemically inert materials prevents undesirable reactions that could compromise the material’s integrity.
- Hydrophobic/Hydrophilic Properties: Tailoring the material’s hydrophobic (water-repellent) or hydrophilic (water-absorbing) characteristics to the application’s needs prevents water-induced damage or swelling.
- UV Resistance:For outdoor applications, materials must resist UV degradation to maintain their mechanical properties and appearance over time.
- Oxidation Resistance:Materials that resist oxidation or degradation due to exposure to oxygen are vital in applications where air contact is frequent.
- Flame Resistance:Materials with flame-retardant properties enhance safety in applications where fire risk is a concern.
- Testing and Validation:Thorough testing in relevant environments and conditions, such as temperature and chemical exposure, validates a material’s claimed resistance properties.
- Coating and Laminates:Applying specialized coatings or laminates can enhance a material’s resistance to specific chemicals or temperatures.
Selecting materials with adequate temperature and chemical resistance is critical for products’ long-term functionality and reliability. Whether for industrial equipment, electronics, automotive components, or construction materials, understanding the potential challenges posed by temperature fluctuations and chemical exposures ensures that the chosen materials can withstand the demands of the intended environment.
Preventing Vibration Loosening
In engineering and design, especially for applications where components face dynamic forces and vibrations, preventing vibration loosening becomes vital. Key points regarding strategies for preventing vibration loosening include:
- Locking Mechanisms:Implementing locking mechanisms such as nuts with nylon inserts, serrated washers, or prevailing torque nuts creates resistance against loosening caused by vibrations.
- Thread Locking Adhesives:Thread locking adhesives, also known as thread lockers, are applied to fastener threads. They cure to form a bond that prevents loosening due to vibrations while still allowing for disassembly when needed.
- Spring Washers:Spring washers, also called Belleville washers, provide tension and maintain pressure on fasteners, compensating for potential loosening caused by vibrations.
- Nyloc Nuts:Nyloc nuts have a nylon insert that forms a tight interference fit with the bolt threads. Increasing the friction and resistance to vibrations reduces the risk of loosening.
- Double Nuts:Using two nuts tightened against each other creates a locking effect. This method is effective when vibration tends to cause the outer nut to loosen.
- Wedge Locking Washers:Wedge locking washers have serrated surfaces that grip both the bolt and the surface, creating a secure connection that resists vibrational forces.
- Adhesive Tapes and Patches:Applying adhesive tapes or patches on fastener threads provides an extra layer of resistance against loosening caused by vibrations.
- Tightening Procedures:Following recommended torque specifications and tightening sequences ensure that fasteners are adequately secured, reducing the risk of vibration-induced loosening.
- Anti-Vibration Mounts:In equipment and machinery, using anti-vibration mounts or dampers isolates components from vibrations, preventing their transmission to fasteners.
- Regular Inspection:Periodic inspection and maintenance allow for identifying loosening or potential issues early on, preventing further damage.
- Material Selection:Choosing materials with suitable mechanical properties and fatigue resistance helps prevent the deformation and elongation of fasteners under vibrational stress.
Addressing vibration-induced loosening is essential to ensure the integrity and reliability of mechanical systems. Employing a combination of hardware solutions, adhesive applications, proper tightening techniques, and regular maintenance can effectively mitigate the risks associated with vibrational forces. You must carefully select each strategy based on the specific application and operational requirements to ensure optimal performance and safety.
Anaerobic Adhesives vs. Traditional Fastening Methods
When considering adhesive options, the choice between Anaerobic Adhesives and Traditional Fastening Methods is crucial, as it directly impacts assembled components’ strength, efficiency, and reliability. Anaerobic Adhesives offer distinct advantages over traditional fastening methods, presenting an innovative solution that addresses various challenges.
1.Improve Bonding:Develop anaerobic adhesives that can create strong bonds between substrates like metals, plastics, and composites without requiring air, enhancing the overall effectiveness of the bonding process.

2.Gap Filling:Unlike traditional methods, anaerobic adhesives can fill gaps and voids between mating surfaces, compensating for irregularities and ensuring a uniform bond line.
3.Vibration Resistance:Anaerobic adhesives provide excellent resistance to vibration and shock, reducing the likelihood of loosening or disassembly, which is joint with traditional mechanical fasteners.
4.Sealing and Preventing Corrosion:These adhesives bond and seal assemblies, preventing leakage of fluids and protecting against corrosion in a way that traditional fasteners cannot.
5.Reduced Weight and Size:Anaerobic adhesives eliminate the need for bulky mechanical fasteners, reducing assemblies’ weight and size, making them ideal for lightweight designs.
6.Improved Aesthetics:Adhesives offer a cleaner and more aesthetically pleasing appearance than traditional methods, often leaving visible fasteners or holes.
7.Uniform Stress Distribution:Anaerobic adhesives distribute stress uniformly across the bonded area, minimizing stress concentrations that can occur with traditional fasteners.
8.Higher Productivity:These adhesives offer faster curing times than waiting for paint or coatings on traditional fasteners to dry, resulting in improved assembly line efficiency.
9.Design Flexibility:Adhesives allow for creative and flexible design choices, as they can bond dissimilar materials and enable the joining of intricate and complex shapes that may be challenging with traditional methods.
10.Resistance to Environmental Factors:Anaerobic adhesives exhibit excellent resistance to environmental factors such as temperature extremes, chemicals, and moisture, ensuring long-term durability.
11.Reduced Assembly Steps:Using adhesives can reduce assembly steps as there’s no need for drilling, tapping, or welding as traditional fastening methods require.
Storage and Shelf Life Considerations
Storage and Shelf Life Considerations are essential factors that play a significant role in various industries, ensuring the quality and safety of products over time. Proper storage conditions and understanding of shelf life contribute to minimizing waste, maintaining product integrity, and enhancing consumer satisfaction. Several vital aspects underline the importance of these considerations:
- Temperature Control:Storing products at the appropriate temperature is crucial to prevent spoilage, bacterial growth, and chemical reactions that could compromise quality and safety.
- Humidity Management:Controlling humidity levels helps prevent moisture-related issues such as mold growth, clumping, and degradation of products.
- Light Exposure:Protecting products from light exposure, especially ultraviolet (UV) light, is vital to prevent the degradation of sensitive compounds, such as vitamins and pharmaceutical ingredients.
- Air Quality:Maintaining a controlled environment that limits exposure to contaminants, pollutants, and oxygen helps extend shelf life and preserve product quality.
- Packaging Integrity:Adequate packaging, including barrier properties and sealing, prevents air, moisture, and external contaminants from entering the package and affecting product stability.
- First-In-First-Out (FIFO) Method:Adhering to the FIFO method ensures that you first use or sell products with the shortest remaining shelf life, thereby reducing the risk of expired goods and waste.
- Expiration Dates:Clear and accurate labeling of expiration or best-before dates on products helps consumers make informed decisions and reduces the chances of consuming expired goods.
- Rotation Practices:To maintain freshness and quality, regularly rotate stock to ensure the use of older products before newer ones.
- Quality Testing:Periodic quality testing and monitoring of products throughout their shelf life help ensure they meet desired specifications and safety standards.
- Product Segregation:Properly segregating products based on their storage requirements prevents cross-contamination and ensures each product retains its intended characteristics.
- Climate Considerations:Tailoring storage conditions to local climate factors, such as temperature and humidity variations, is essential for maintaining product stability in different regions.
- Specialized Storage: Certain products, such as perishable foods or temperature-sensitive medications, may require technical storage facilities, like refrigeration or controlled atmosphere environments.
- Regulatory Compliance:Following storage and shelf life guidelines mandated by regulatory authorities ensures product safety and prevents legal issues.
- Consumer Confidence:Providing optimal-quality products through proper storage practices enhances consumer trust and loyalty.
Environmental Impact and Sustainability
Environmental Impact and Sustainability are crucial considerations across various sectors as societies strive for responsible and ethical practices. Our actions today have far-reaching consequences on the planet’s health and well-being. Addressing environmental impact and promoting sustainability is a collective responsibility that requires immediate action and long-term commitment. Several vital factors underscore the importance of these considerations:
- Resource Consumption:Unsustainable resource consumption, such as excessive use of fossil fuels, water, and raw materials, depletes finite resources and contributes to ecological imbalance.
- Climate Change:Industrial processes and energy production are significant contributors to greenhouse gas emissions, which drive climate change and result in severe weather events, rising sea levels, and ecosystem disruptions.
- Biodiversity Loss:Unchecked development, deforestation, and pollution lead to habitat destruction, causing biodiversity loss and threatening countless species with extinction.
- Waste Generation:The generation of waste, particularly non-biodegradable plastics and hazardous materials, contributes to pollution and threatens ecosystems, wildlife, and human health.
- Pollution: Pollution from industrial emissions, agricultural runoff, and improper waste disposal contaminates air, water, and soil, causing health issues for humans and wildlife.
- Sustainable Practices: Embracing sustainable practices, such as renewable energy adoption, responsible waste management, and eco-friendly manufacturing, minimizes negative impacts on the environment.
- Circular Economy:Transitioning to a circular economy, where resources are reused, recycled, and repurposed, reduces the need for new resource extraction and minimizes waste.
- Conservation Efforts:Protecting and restoring natural habitats through conservation efforts helps preserve biodiversity and supports the overall health of ecosystems.
- Renewable Energy:Shifting from fossil fuels to renewable energy sources like solar, wind, and hydroelectric power reduces carbon emissions and dependence on finite resources.
- Green Technologies:Advancing technology that promotes clean energy, efficient transportation, and sustainable agriculture contributes to mitigating environmental impact.
- Corporate Responsibility:Industries and businesses adopting environmentally responsible practices demonstrate corporate social responsibility and contribute to positive change.
- Education and Awareness: Educating communities about environmental impact fosters awareness and empowers individuals to make informed choices in their daily lives.
- Policy and Regulation:Government policies and regulations that incentivize sustainable practices and impose consequences for harmful activities play a vital role in curbing environmental degradation.
Safety Measures during Application
Safety Measures during application are paramount when dealing with any process or technology that involves potential risks. Whether in industrial settings, laboratories, or everyday activities, implementing adequate safety measures ensures the well-being of individuals, the protection of the environment, and the integrity of processes. Emphasize several key safety considerations:
- Training and Education: Proper training and education are essential for anyone applying processes or technologies that could pose risks. A comprehensive understanding of procedures, equipment operation, and potential hazards helps individuals make informed decisions and respond appropriately in critical situations.
- Personal Protective Equipment (PPE): Depending on the nature of the application, individuals should wear appropriate personal protective equipment (PPE) such as helmets, gloves, goggles, masks, or full-body suits. PPE is a barrier against potential exposure to harmful substances, physical hazards, or other dangers.
- Risk Assessment:Conducting thorough risk assessments before commencing any application is crucial. Identifying potential hazards, evaluating their severity, and devising strategies to minimize or mitigate these risks are integral to safety planning.
- Emergency Protocols: Establish, communicate, and regularly practice well-defined protocols. These protocols outline steps to take in case of accidents, spills, leaks, or any unforeseen incidents, minimizing panic and ensuring a swift and organized response.
- Ventilation and Containment:Adequate ventilation systems and containment measures are essential when harmful gases, vapors, or particles could be released. Proper ventilation prevents the buildup of hazardous substances in the environment.
- Proper Equipment Use:Thorough understanding of equipment operation is critical. Misusing or not following reasonable procedures can lead to accidents or malfunctions that compromise safety.
- Labeling and Signage:Clear labeling of hazardous areas, materials, and equipment helps individuals identify potential risks and take necessary precautions.
- Waste Disposal:Safe disposal of waste generated during the application process, mainly if it involves hazardous substances, is essential to prevent environmental contamination and health risks.
- Regular Inspections and Maintenance:Frequent inspections and maintenance of equipment, tools, and facilities ensure they work correctly. Implementing this measure reduces the probability of accidents resulting from faulty equipment significantly.
- Communication: Open and effective communication among team members is vital. It ensures everyone knows potential risks, safety protocols, and procedure changes.
- Continuous Monitoring:Ongoing monitoring during the application process helps identify any deviations from expected outcomes or safety concerns that might arise.
Precision Dosing and Dispensing Techniques
Precision Dosing and Dispensing Techniques have revolutionized various fields by enabling accurate and controlled delivery of substances. These techniques are vital in industries ranging from pharmaceuticals to manufacturing, where precise measurements are crucial for optimal outcomes. Employing advanced technologies and methodologies, precision dosing and dispensing offer several key advantages:
1.Accurate Formulation: Precision dosing ensures that substances are mixed in exact quantities, resulting in consistent and precise formulations. Proper dosing is crucial in pharmaceuticals, as it directly impacts the effectiveness of medications in achieving therapeutic results.
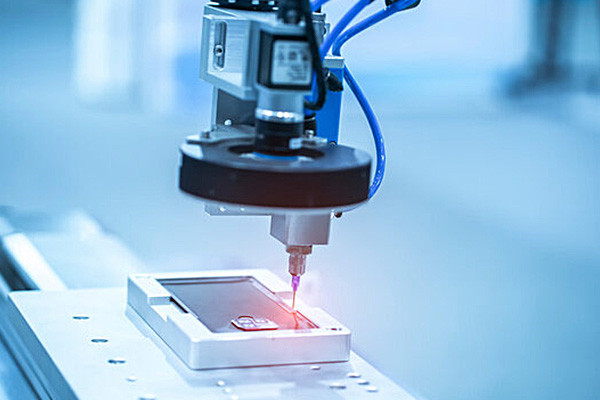
2.Reduced Waste: Precision dispensing techniques reduce waste by minimizing overages and spillage. By adopting this approach, companies can meet sustainability goals and achieve cost savings by reducing the waste of raw materials during manufacturing.
3.Enhanced Quality Control: Precision dosing and dispensing techniques help maintain strict quality control standards. By avoiding variations in ingredient ratios, companies can produce products with consistent quality and performance.
4.Customization: Precision dosing allows for the creation of tailored products and solutions. Industries like cosmetics and personal care greatly benefit from this as it caters to customers’ diverse preferences and requirements.
5.Automation and Efficiency:Automated precision dispensing systems streamline production processes, reducing the requirement for manual intervention and accelerating production cycles. This enhancement in efficiency leads to increased output.
6.Minimized Human Error:Human errors in measurement and dispensing can have serious consequences, especially in industries like healthcare. Precision dosing technologies significantly reduce the risk of dosage errors, enhancing patient safety.
7.Research Advancements:In scientific research, precision dosing and dispensing techniques enable researchers to work with small quantities of substances while maintaining accuracy. Minor variations can lead to significant outcomes in experiments, making paying close attention to even the most minor details essential.
8.Complex Formulations: For industries dealing with complicated formulations, such as the food and beverage sector, precision dosing allows the accurate incorporation of multiple ingredients, ensuring consistent taste and texture.
9.Pharmaceutical Innovation: Precision dosing plays a pivotal role in drug development, enabling the creation of novel drug delivery systems and personalized medicine approaches. Consequently, there is an enhancement in the effectiveness of treatment and better outcomes for patients.
10.Medical Treatments: In healthcare, precision dosing is essential for administering medications, particularly in critical care scenarios where slight variations can have life-threatening implications.
Quality Control and Testing Standards
Quality Control and Testing Standards are pivotal in ensuring products and services’ reliability, safety, and performance across various industries. These standards serve as benchmarks that guide manufacturers, developers, and service providers in maintaining consistent quality and meeting customer expectations. The implementation of rigorous quality control processes and adherence to established testing standards offer several benefits:
- Reliability: Quality control measures enhance the reliability of products by identifying and rectifying defects during production. Customers are more satisfied and loyal by reducing the likelihood of malfunctions or breakdowns.
- Safety: Stringent testing standards contribute to the protection of products, especially those used in critical sectors such as healthcare, automotive, and aerospace. By subjecting products to rigorous testing, companies can identify and address potential safety hazards before these hazards pose any risk to users or the environment.
- Consistency:Quality control processes ensure consistency in product performance and attributes. Industries heavily relying on component interchangeability must pay special attention to avoid even the slightest variations. Such discrepancies could result in compatibility issues that need proper mitigation.
- Compliance: Adhering to established quality control and testing standards helps companies maintain regulatory compliance. Ensuring compliance is imperative to prevent legal troubles and costly fines and solidify a company’s image as a provider of reliable and compliant merchandise.
- Cost Efficiency:While implementing quality control processes and adhering to testing standards may require an upfront investment, it ultimately leads to cost savings. Identifying and rectifying issues early in production reduces the need for costly rework, warranty claims, and recalls.
- Competitive Advantage:Companies that consistently deliver high-quality products gain a competitive edge. Such products tend to have better reviews, leading to positive word-of-mouth marketing and an increased market share.
- Innovation:Quality control and testing standards drive innovation by encouraging companies to improve their products continuously. Companies can develop cutting-edge products that meet evolving customer needs through iterative testing and quality enhancement.
- Risk Mitigation: Implementing quality control measures and following testing standards minimizes the risk of unexpected product failures, which could result in reputational damage and financial losses. For companies working in industries with high liability, this is particularly crucial.
- Customer Satisfaction: High-quality products that meet or exceed customer expectations enhance overall customer satisfaction. By creating an exceptional customer experience, businesses can achieve repeat business, cultivate brand loyalty, and provoke positive reviews that entice new customers.
Innovations in Anaerobic Adhesive Technology
Innovations in Anaerobic Adhesive Technology have led to remarkable advancements in the manufacturing and construction industries. These adhesive solutions, known for their ability to cure in the absence of air, have revolutionized how joints and connections are secured. Some noteworthy developments include:
- Enhanced Bonding Strength: Recent innovations have resulted in anaerobic adhesives with significantly improved bonding strengths. The development has made it possible to form more vital and dependable connections, even under extreme pressure.
- Versatile Applications: The technology’s adaptability has expanded its range of applications. Anaerobic adhesives are now utilized for thread locking and sealing, retaining cylindrical parts, preventing leaks, and even structural bonding.
- Faster Curing Times: One of the critical breakthroughs is reducing curing time. New formulations allow anaerobic adhesives to cure more rapidly, optimizing production timelines and efficiency.
- Temperature and Chemical Resistance: Innovations have addressed the limitations of anaerobic adhesives in extreme environments. Modern formulations exhibit enhanced resistance to a broader range of temperatures and chemicals, making them suitable for diverse operating conditions.
- Reduced Environmental Impact:A significant development in recent years is the introduction of more environmentally friendly anaerobic adhesives. Manufacturers have been able to produce formulations with lower levels of volatile organic compounds (VOCs) and reduced overall environmental impact.
- User-Friendly Application:Innovations have also focused on user experience. Anaerobic adhesives are now available in user-friendly packaging, applicators, and dispensing systems, simplifying their application and minimizing wastage.
- Compatibility with Various Substrates: Advancements in anaerobic adhesive technology have expanded the range of substrates they can effectively bond. Whether metal, plastic, or composite materials, these adhesives offer strong adhesion across diverse material types.
- Quality Control Measures: Innovators have integrated quality control mechanisms into the adhesive formulations. Reducing the risk of bond failure is significantly achieved by ensuring consistent and reliable performance.
These innovations collectively underscore the transformative potential of anaerobic adhesive technology. These advancements have propelled industries forward from increased bonding strength to broader application possibilities and improved environmental consciousness. As research and development in this field continue, it is exciting to anticipate the future options that will further elevate the role of anaerobic adhesives across industries.
Selecting the Right Anaerobic Solution
Selecting the right anaerobic solution is a crucial decision that requires careful consideration of various factors to ensure optimal performance and successful outcomes. Anaerobic adhesives and sealants offer a range of specialized properties, and choosing the appropriate product for a specific application can significantly impact the bonded components’ efficiency, reliability, and longevity. To effectively navigate this decision, you should take the following points into account:
- Application Requirements: Understand the exact requirements of the application. Consider factors such as the types of materials the bonding will involve, the anticipated loads and stresses, operational temperatures, and whether the adhesive needs to offer sealing properties.
- Curing Time:Evaluate the desired curing time for the project. Different anaerobic solutions have varying curing times, ranging from a few minutes to several hours. Select an adhesive that aligns with the production or assembly schedule.
- Bond Strength: The required bond strength can differ depending on the specific application. Determine whether a low, medium, or high-strength adhesive is necessary to ensure the components stay securely bonded under operational conditions.
- Viscosity:The viscosity of the anaerobic adhesive affects its flow and gap-filling capabilities. A lower-viscosity adhesive might be more suitable for applications with tight tolerances or irregular surfaces, while higher-viscosity options are better for more significant gaps.
- Temperature Resistance: Consider the temperature range that will expose the bonded components. Some anaerobic adhesives maintain their performance at high temperatures, while others are better suited for lower-temperature environments.
- Chemical Compatibility: Evaluate the compatibility of the anaerobic adhesive with the materials it bonds and any substances it might encounter throughout its lifecycle. Industries where exposure to chemicals or solvents is daily, must consider this a crucial factor.
- Environmental Considerations:If sustainability is a priority, look for anaerobic solutions that align with eco-friendly practices, such as those with reduced VOC emissions or a lower environmental impact.
- Application Method: Consider the application method that suits your production process. Some anaerobic adhesives are available in convenient packaging, such as cartridges or syringes, making them easier to apply accurately.
- Testing and Validation: Before committing to a specific anaerobic solution, perform thorough testing and validation on representative samples to ensure the adhesive meets the desired performance criteria.
Future Prospects in Anaerobic Bonding
Future prospects in anaerobic bonding hold significant promise for various industries and applications, owing to its unique characteristics and benefits. This innovative bonding technique, which involves creating strong adhesive bonds without oxygen, presents a range of exciting possibilities for advancements in manufacturing, construction, and technology. The potential advantages of anaerobic bonding are multifaceted and can be summarized as follows:
- Enhanced Bond Strength:Anaerobic adhesives, when applied correctly, have shown exceptional bond strength, often surpassing traditional bonding methods. This increased bonding power could enable the development of more durable and reliable products across industries.
- Reduced Environmental Impact:Anaerobic bonding eliminates the need for heat-curing processes. It can significantly reduce energy consumption and emissions, aligning with sustainability goals and contributing to a greener future.
- Improved Production Efficiency: The rapid curing time of anaerobic adhesives can streamline manufacturing processes by reducing assembly line waiting times. This efficiency boost could lead to increased production output and cost savings.
- Versatile Applications:The potential applications of anaerobic bonding are vast. Anaerobic adhesives could revolutionize the assembly of various products, offering a versatile solution for diverse industries, from automotive components to aerospace parts.
- Sealing Capabilities:Anaerobic adhesives bond components together and possess sealing properties. This dual functionality could enhance assembled products’ integrity, preventing leaks and improving overall performance.
- Compatibility with Various Materials:Anaerobic bonding exhibits compatibility with a wide range of materials, including metals, plastics, and composites. This versatility could enable engineers and designers to experiment with innovative material combinations.
- Cost-Effectiveness:With its quick curing time and reduced energy requirements, anaerobic bonding could prove cost-effective in the long run. Lower energy consumption and faster production cycles could lead to significant financial savings.
- Advancements in Electronics:As the electronics industry demands minor and more intricate components, anaerobic bonding’s precise application and strong bonds could find valuable applications in creating reliable connections on microelectronic devices.
Anaerobic adhesives and sealants represent a revolutionary leap in the field of bonding solutions, effectively addressing the challenges posed by oxygen-free environments. Their ability to provide secure, leak-proof, and durable joints has transformed industries ranging from automotive and aerospace to electronics and manufacturing. With an ever-expanding array of applications and continuous advancements in adhesive technology, anaerobic products are poised to remain a cornerstone of modern assembly techniques. As industries strive for enhanced efficiency and performance, these specialized adhesives are set to play a pivotal role in shaping the future of manufacturing and assembly processes.