Aerospace Adhesive
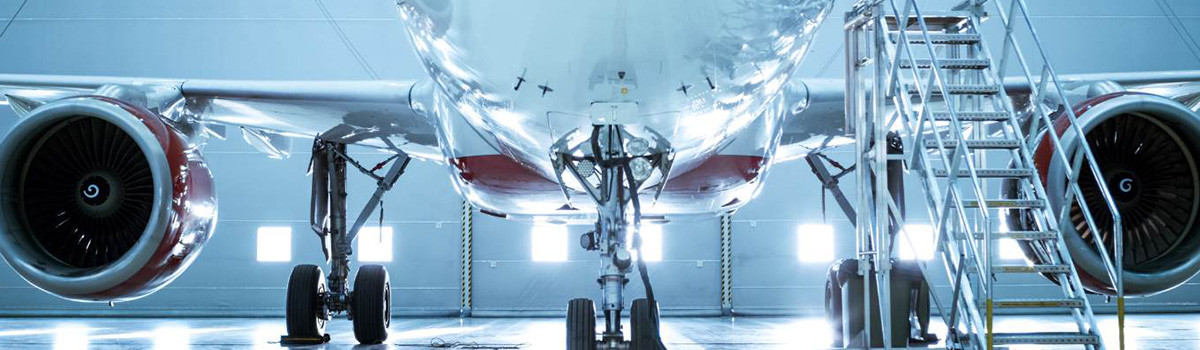
In the realm of aerospace engineering, where safety, durability, and performance are paramount, the role of aerospace adhesive cannot be overstated. These specialized adhesives have revolutionized the way aircraft, spacecraft, and satellites are constructed, offering unmatched bonding capabilities even in the most extreme conditions. Aerospace adhesive solutions have become integral to ensuring structural integrity, thermal management, and weight reduction in aerospace applications. This comprehensive exploration delves into the realm of aerospace adhesive, uncovering its formulations, applications, advantages, and its instrumental role in advancing aviation and space exploration.
Unveiling Aerospace Adhesive
Aerospace adhesives are at the forefront of revolutionizing aircraft manufacturing and maintenance. These advanced materials are reshaping the aviation industry by offering lightweight, durable, and high-performance solutions. Let’s look closer at the world of aerospace adhesives and their significant impact on aviation.
The Evolution of Adhesive Solutions in Aerospace
- Innovative adhesive technologies complement traditional mechanical fastening methods.
- Engineers design aerospace adhesives to withstand extreme temperatures, vibrations, and stressors encountered during flight.
Benefits Driving Adoption
- Weight Reduction:Aerospace adhesives contribute to lighter aircraft, enhancing fuel efficiency and reducing emissions.
- Aerodynamic Flexibility: Adhesives enable seamless and smooth surfaces, optimizing aircraft aerodynamics.
- Corrosion Prevention: Adhesives act as a barrier, protecting aircraft components from corrosive elements.
Bonding Diversity: Applications of Aerospace Adhesives
- Structural Bonding:Adhesives replace or reinforce traditional rivets and bolts in bonding components, reducing weak points.
- Composite Assembly:Adhesives provide robust bonding for lightweight composite materials, enhancing structural integrity.
- Interior and Exterior Panel Bonding:Adhesives offer a secure and aesthetically pleasing finish from cabin interiors to aircraft exteriors.
Challenges and Innovations
- Extreme Conditions:Aerospace adhesives must perform reliably in diverse conditions, from freezing altitudes to scorching runways.
- Research Focus:Researchers continuously innovate to develop adhesives with improved resistance and enhanced flexibility.
Safety and Regulations
- Stringent industry regulations govern the use of adhesives in aerospace applications.
- Adhesives undergo rigorous testing to meet safety standards and maintain structural integrity.
Sustainability and Future Trends
- Eco-Friendly Formulations:The aerospace industry’s push for sustainability has led to the development of adhesives with reduced environmental impact.
- Circular Economy:Research explores recyclable adhesives that align with the aerospace sector’s commitment to circular practices.
Collaboration and Industry Impact
- The development of aerospace adhesives results from collaboration between adhesive manufacturers, aerospace companies, and research institutions.
- Adopting these adhesives contributes to more efficient manufacturing processes and increased aircraft longevity.
The Road Ahead: Innovation and Beyond
- Research continues to refine aerospace adhesive formulations, focusing on durability, versatility, and ease of application.
- Aerospace adhesives are poised to drive the development of next-generation aircraft, shaping the future of aviation.
Challenges in Aerospace Bonding
Aerospace bonding is a critical aspect of aircraft manufacturing and maintenance, ensuring aircraft components’ structural integrity and performance. However, this intricate process has its challenges. Let’s explore the key challenges faced in aerospace bonding and the strategies to overcome them.
Extreme Operating Conditions
- Aerospace vehicles are subjected to various conditions, from high-altitude freezing temperatures to intense vibrations during flight.
- Adhesives must maintain strength and stability under these extreme conditions to ensure long-lasting bonds.
Material Compatibility
- Manufacturers use diverse materials, including metals, composites, and plastics, to make aircraft components.
- Finding adhesives that can securely bond different materials while accounting for their varying expansion coefficients poses a challenge.
Regulatory Compliance
- The aerospace industry is highly regulated to ensure safety and reliability.
- Adhesives must adhere to strict regulations and pass rigorous tests to prove their suitability for aircraft applications.
Longevity and Durability
- Aerospace components need to endure years of operation and thousands of flight hours.
- Adhesives must resist degradation from environmental factors, UV radiation, and chemical exposure over an extended period.
Surface Preparation
- Proper surface preparation is crucial for adhesive bonding success.
- Achieving the appropriate surface cleanliness and roughness for optimal adhesion can be complex and time-consuming.
Complex Geometry
- Aircraft components often have intricate shapes and contours.
- Ensuring uniform adhesive application and proper contact between surfaces can be challenging in complex geometries.
Repair and Maintenance
- Adhesive bonding in aerospace isn’t limited to manufacturing; it extends to repairs and maintenance.
- Developing adhesive solutions that allow for easy repair or replacement while maintaining structural integrity presents a challenge.
Risk Mitigation
- Aerospace bonding failures can have catastrophic consequences.
- Implementing robust quality control measures and risk assessment protocols is essential to prevent bonding issues.
Innovation and Research
- Aerospace technology is evolving rapidly, demanding new adhesive solutions.
- Continuous research is needed to develop adhesives that meet the demands of emerging aircraft designs and materials.
Collaboration and Expertise
- Bonding challenges require multidisciplinary collaboration among adhesive manufacturers, aerospace engineers, and material scientists.
- Leveraging expertise from different fields is essential for finding practical solutions.
Key Characteristics of Aerospace Adhesives
Aerospace adhesives are pivotal in ensuring aircraft and spacecraft components’ structural integrity, safety, and performance. These specialized adhesives possess a distinct set of key characteristics that make them uniquely suitable for the demanding and diverse requirements of aerospace applications:
- High Strength:Designers create aerospace adhesives to provide exceptional bonding strength, enabling them to withstand the extreme forces, vibrations, and stresses experienced during flight and space travel. This high strength contributes to the overall structural integrity of the aircraft or spacecraft.
- Temperature Resistance:Aerospace environments expose components to various temperatures, from cold at high altitudes to intense heat during re-entry. Formulators create aerospace adhesives to maintain the integrity and adhesive properties across this temperature spectrum, ensuring they don’t degrade or lose their bonding capabilities.
- Chemical Resistance:The aerospace industry involves exposure to various chemicals, including fuels, hydraulic fluids, and cleaning agents. Engineers engineer aerospace adhesives to resist chemical interactions, preventing adhesive bond degradation and preserving the joined components’ reliability.
- Weight Considerations:Every ounce matters in aerospace design, as lighter aircraft and spacecraft translate to improved fuel efficiency and greater payload capacity. Formulators formulate lightweight aerospace adhesives, reducing the bonded components’ overall weight compared to traditional mechanical fastening methods.
- Flexibility and Durability:Aerospace adhesives must maintain their performance even under flexing, vibration, and repeated loading conditions. They exhibit high flexibility and durability, allowing them to absorb and distribute stress without compromising the adhesive bond.
- Low Outgassing:In the vacuum of space, volatile compounds released by materials can pose a risk to delicate instruments and optics. Aerospace adhesives are designed with common outgassing characteristics, minimizing the release of flammable substances that could affect nearby surfaces.
- Electrical Insulation:Many aerospace components require electrical insulation to prevent interference and ensure the proper functioning of onboard electronics. Aerospace adhesives possess excellent electrical insulation properties, maintaining a barrier against unwanted conductivity.
High-Temperature Resistance
Various industries and applications require high-temperature resistance as a crucial property for materials and components subjected to elevated temperatures. This characteristic ensures that materials can maintain structural integrity, mechanical properties, and functionality even when exposed to extreme heat. Several vital aspects define the significance and features of high-temperature resistance:
- Material Stability:High-temperature resistance refers to a material’s ability to withstand elevated temperatures without undergoing significant chemical or physical changes. Materials with high-temperature resistance remain stable, avoiding degradation, melting, or decomposition even in extreme heat conditions.
- Industrial Applications:Industries such as aerospace, automotive, manufacturing, energy production, and electronics frequently demand high-temperature-resistant materials. Manufacturers use these materials for components such as engine parts, exhaust systems, furnace linings, turbine blades, and electronic circuitry that operate in environments with elevated temperatures.
- Thermal Expansion Control:High temperatures often induce thermal expansion in materials, potentially leading to dimensional changes and mechanical stress. Engineers engineer high-temperature-resistant materials to have controlled or low thermal expansion coefficients, minimizing the risk of distortion and maintaining the structural integrity of assemblies.
- Ceramics and Metals:Ceramic materials, such as refractory and heat-resistant ceramics, are renowned for their exceptional high-temperature resistance due to their inherent stability and low thermal conductivity. Certain metals and alloys, such as stainless steel and nickel-based superalloys, are also chosen for their ability to withstand extreme heat without compromising their properties.
- Thermal Insulation:High-temperature resistance is closely linked to thermal insulation, as materials designed for this purpose provide a barrier against heat transfer. Companies use insulating materials to protect adjacent components or surfaces from extreme temperatures, contributing to safety and efficiency in various applications.
- Engineering Innovations:The development of high-temperature-resistant materials has spurred engineering innovations, enabling the creation of advanced technologies like supersonic flight, space exploration, and high-efficiency power generation. These materials make it possible to push the boundaries of what is achievable in extreme environments.
Low Outgassing Properties
Low outgassing properties refer to the minimal release of volatile substances from materials in vacuum or high-temperature environments. An essential factor in industries where gas buildup or contamination can harm equipment, performance, and safety.
Importance
- Space Exploration:Materials with low outgassing properties in the aerospace industry are vital for spacecraft and satellite construction. The vacuum of space can cause released gases to condense on sensitive instruments, hindering their functionality.
- Optics and Electronics:Optical and electronic devices, such as sensors and lenses, require materials that do not emit gases that cause fogging, reduced clarity, or decreased signal quality.
- Medical Equipment:Medical facilities utilize outgassing-resistant materials in equipment like particle accelerators and MRI machines to maintain consistent performance and prevent contamination.
Testing and Standards
- ASTM E595: This standard test method evaluates the total mass loss (TML) and collected volatile condensable materials (CVCM) from materials exposed to a vacuum environment. Acceptable levels are determined based on the application.
- ECSS-Q-ST-70-02: The European Cooperation for Space Standardization outlines testing procedures and limits for materials used in space systems. It categorizes materials based on their level of outgassing.
- NASA SP-R-0022A:NASA provides guidelines for selecting materials with low outgassing properties for space missions, offering information on acceptable TML and CVCM values.
Mitigation Strategies
- Material Selection:Choosing materials with inherently low outgassing rates, such as specialized polymers, ceramics, and certain metals, can significantly reduce the risk of contamination.
- Surface Treatments:Applying coatings or finishes to materials can mitigate outgassing by sealing the surface and preventing the release of volatile compounds.
- Preconditioning:Some materials can be baked or exposed to vacuum conditions before use to drive off volatile substances, minimizing subsequent outgassing.
- Barrier Layers:Introducing barrier layers between the material and the vacuum environment can restrict the escape of outgassed substances.
Future Trends
As industries continue to push the boundaries of technology, the demand for materials with even lower outgassing properties will rise. Researchers are exploring nanotechnology and advanced surface treatments to create materials that exhibit superior stability in extreme environments.
Vibration and Impact Resilience
Vibration and impact resilience are crucial engineering concepts that govern the ability of structures and materials to withstand dynamic forces and shocks. These forces can arise from various sources, such as machinery operations, earthquakes, transportation, or human interaction. The study of vibration and impact resilience involves delving into the mechanical behavior of materials and their response to external stimuli.
Key Factors Influencing Resilience
Several factors play a pivotal role in determining the vibration and impact resilience of materials and structures:
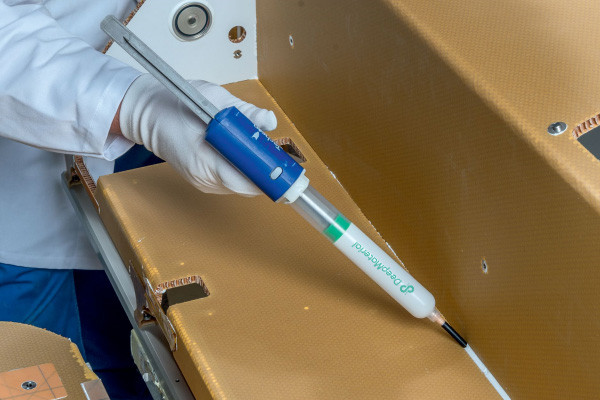
- Material Properties:The intrinsic characteristics of materials, including elasticity, density, and damping, significantly affect their ability to absorb and dissipate energy from vibrations and impacts.
- Frequency Response:Different materials and structures have varying natural frequencies. Resonance can occur when the excitation frequency matches the natural frequency, leading to heightened vibrations or susceptibility to damage.
- Damping Mechanisms: Materials with effective damping mechanisms can dissipate energy more efficiently, reducing the amplitude of vibrations and minimizing the potential for damage.
- Design and Geometry:The creation of a structure can either amplify or dampen vibrations. Geometry, layout, and reinforcement strategies contribute to a structure’s resilience.
Importance in Engineering
Vibration and impact resilience holds immense significance across diverse engineering domains:
- Structural Engineering:Buildings, bridges, and other infrastructure must withstand vibrations and impacts caused by seismic events, heavy machinery, wind, and traffic. Resilient materials and intelligent design ensure longevity and safety.
- Transportation:Vehicles encounter dynamic forces during operation. Vibration and impact resilience in automotive, aerospace, and maritime industries enhance passenger comfort and system durability.
- Electronics:Electronic devices are susceptible to damage from shocks and vibrations. Incorporating resilient materials and shock-absorbing mechanisms safeguards sensitive components.
- Manufacturing:Machinery and equipment vibrate during operation, affecting precision and reliability. Effective vibration control improves manufacturing quality and extends equipment lifespan.
Innovations and Future Trends
As technology advances, the focus on improving vibration and impact resilience continues to grow:
- Innovative Materials:The development of materials with adaptive properties that alter their stiffness or damping characteristics in response to changing conditions is an ongoing area of research.
- Nanotechnology:Researchers are manipulating material properties at the nanoscale to enhance resilience and tailor responses to specific frequencies.
- Predictive Modeling: Using advanced simulations and modeling techniques to predict and optimize a material or structure’s behavior under varying vibrational and impact conditions.
Corrosion Protection
Corrosion protection is a paramount aspect of materials science and engineering that aims to mitigate the destructive effects of corrosion. This natural process deteriorates materials due to chemical reactions in their environment. Corrosion is pervasive across industries, leading to structural damage, financial losses, and safety hazards. Effective corrosion protection strategies are imperative to extend the lifespan of materials and maintain their performance.
Primary Causes and Types of Corrosion
Understanding the underlying causes and types of corrosion is fundamental in devising appropriate protection methods:
- Electrochemical Corrosion:The most common form involves the electrochemical reactions between a metal, an electrolyte (usually moisture), and oxygen. The formation of rust or oxide layers weakens the material.
- Galvanic Corrosion:Occurs when dissimilar metals come into contact with an electrolyte, creating a galvanic cell that accelerates the corrosion of the less noble metal.
- Pitting Corrosion:Localized corrosion characterized by small pits or holes on the surface, often initiated by local chemical inhomogeneities.
Strategies for Corrosion Protection
A range of techniques and materials are employed to prevent or slow down the corrosion process:
- Coatings and Paints:Applying barrier coatings like paints, varnishes, or metal plating creates a protective layer that physically separates the material from its environment.
- Inhibitors:Introducing chemical compounds that react with the metal surface to form a protective layer, inhibiting the corrosive reactions.
- Cathodic Protection:One method involves placing a sacrificial anode, typically a more reactive metal, in contact with the material to be protected. The anode corrodes instead of the target metal.
- Material Selection: Choosing corrosion-resistant materials such as stainless steel, aluminum, or non-metallic composites to avoid or minimize corrosion-related issues.
- Design Modification: Altering the design of structures to improve drainage, reduce crevices, and promote airflow, limiting the accumulation of moisture and corrosive agents.
Industrial Significance
Corrosion protection is integral across a spectrum of industries:
- Infrastructure:Protecting bridges, pipelines, and buildings from corrosion ensures their structural integrity and extends their operational life.
- Transportation:In the automotive, aerospace, and maritime sectors, corrosion protection is crucial to maintain the safety and reliability of vehicles and vessels.
- Oil and Gas: Corrosion in equipment and pipelines can lead to leaks, environmental damage, and production downtime. Adequate protection is essential for maintaining efficiency and safety.
Advancements and Future Directions
Continual research drives innovation in corrosion protection:
- Nanotechnology: Developing nanocoatings with enhanced protective properties due to their ultra-thin and precisely engineered structures.
- Self-Healing Materials:Researchers are exploring creating materials that can autonomously repair corrosion-induced damage through chemical reactions.
- Sustainable Practices:Researchers are exploring eco-friendly corrosion protection methods to minimize environmental impact.
Composite Material Bonding
Various industries widely use composite materials due to their exceptional strength-to-weight ratio and corrosion resistance. Adequate bonding of composite materials is crucial for ensuring structural integrity and performance. Composite material bonding involves joining two or more composite components or materials to create a unified structure. This process requires careful consideration of adhesive selection, surface preparation, and bonding techniques to achieve firm and durable bonds. Here are some key points to consider:
Adhesive Selection
- Choosing a suitable adhesive is essential for a strong bond between composite materials. Sealants can be epoxy-based, polyurethane-based, cyanoacrylate, or other specialized formulations.
- The adhesive should possess compatibility with the composite materials being bonded and provide sufficient strength to withstand the operational loads and environmental conditions.
Surface Preparation
- Proper surface preparation ensures adequate adhesion between composite surfaces and the adhesive.
- You should clean surfaces thoroughly to remove contaminants such as oils, dust, and release agents that can hinder bonding.
- Mechanical methods such as sanding, abrading, or roughening the surface can enhance the adhesive’s grip on the composite material.
Bonding Techniques
Different bonding techniques are employed based on the specific requirements of the application. Some standard methods include:
- Mechanical Fastening: Bolts, rivets, and screws are used to secure composite components mechanically. This method is effective but can introduce stress concentrations.
- Adhesive Bonding: This method distributes loads evenly across the bonded area, minimizing stress concentrations. It also provides improved aesthetics and corrosion resistance.
- Hybrid Bonding:Combining adhesive bonding with mechanical fasteners can provide synergistic benefits, enhancing overall strength and durability.
- Autoclave Bonding:Used in aerospace applications, this involves placing composite components in an autoclave with adhesive and applying heat and pressure to cure and bond the materials.
Quality Control
- Ensuring the quality of composite material bonding is essential for safety and performance.
- Non-destructive testing methods such as ultrasonic testing, X-ray inspection, and visual inspections can be employed to detect defects or irregularities in bonded joints.
- Quality control measures should be implemented throughout the bonding process, from adhesive application to curing, to verify the integrity of the bond.
Metal-to-Metal Bonding
Metal-to-metal bonding is a fundamental process in engineering and manufacturing, essential for creating robust and reliable structures across various industries. This bonding method involves joining two or more metal components to form a unified assembly, imparting strength, durability, and electrical conductivity to the joined parts. Successful metal-to-metal bonding requires attention to specific techniques and considerations. Here’s a breakdown:
Surface Preparation
- Properly preparing metal surfaces before bonding is critical for achieving a solid bond. Characters must be free from contaminants like oils, rust, and oxides to ensure optimal adhesion.
- Professionals use solvent, abrasive, or chemical treatments to clean and activate the metal surfaces, enhancing their bonding capability.
Adhesive Selection
- The choice of adhesive depends on factors such as the types of metals that will undergo bonding, load requirements, and environmental conditions.
- Manufacturers commonly use structural adhesives such as epoxies, acrylics, and polyurethanes for their high strength and versatility.
Bonding Techniques
You can employ various methods for metal-to-metal bonding:
- Adhesive Bonding:Adhesives distribute loads evenly and help prevent corrosion between bonded metals.
- Welding: Processes like arc welding, resistance welding, and laser welding melt and fuse metal surfaces.
- Brazing:You melt a filler metal with a lower melting point than the base metals to join the parts without melting the base metals.
- Mechanical Fasteners: Bolts, nuts, rivets, and screws are used for mechanical joining, providing stability and ease of disassembly.
Compatibility and Galvanic Corrosion
- Different metals can have varying electrochemical potentials, leading to galvanic corrosion in direct contact. Metal-to-metal bonding requires careful consideration.
- Insulating coatings, protective barriers, or selecting metals with similar electrochemical properties can mitigate galvanic corrosion.
Testing and Quality Assurance
- Ensuring the integrity of metal-to-metal bonds requires rigorous testing methods such as tensile, shear, and peel tests to assess adhesive strength and joint performance.
- You should establish quality assurance protocols to monitor the bonding process, from surface preparation to adhesive application.
Panel and Component Assembly
Panel and component assembly is a critical stage in manufacturing, where individual parts seamlessly come together to create a functional and cohesive product. This intricate process involves carefully arranging and integrating various components, each serving a specific purpose, to ensure the final product meets the highest quality and performance standards. Key aspects of panel and component assembly include:
- Precision Placement:Skilled technicians meticulously position components, ensuring they adhere to precise measurements and tolerances. This step demands a keen eye for detail and a steady hand to guarantee accurate alignment, preventing potential malfunctions or defects.
- Interconnectivity:During assembly, skilled technicians must interconnect components electrically and mechanically to facilitate seamless communication and collaboration among different parts. Ensuring solid connections prevents signal disruptions and optimizes the product’s overall performance.
- Adhesive Techniques:Whether traditional or advanced bonding agents, adhesives play a significant role in securing components to the base panel. This technique enhances durability and minimizes the risk of features loosening over time.
- Fastening Methods:Assembly may require various fastening methods, such as screws, bolts, or clips, to securely affix components to the panel. Each process is chosen based on material compatibility, desired stability, and ease of maintenance.
- Quality Control:Rigorous quality checks are integrated throughout the assembly process to identify deviations or inconsistencies. These assessments help catch defects early, ensuring that the final product meets predefined standards and minimizing the need for rework.
- Testing Procedures:Assembled panels undergo thorough testing to assess functionality and performance. This phase may include simulated stress tests, electrical testing, and compatibility evaluations to ensure all components work harmoniously and meet the intended specifications.
- Efficiency and Workflow:Optimizing the assembly workflow is crucial for maintaining productivity. Efficiently organizing workstations, streamlining processes, and utilizing appropriate tools contribute to a smooth and expedited assembly process.
Structural Bonding in Aircraft
Structural bonding in aircraft, also known as aerospace adhesive bonding, is a fundamental technique in modern aerospace manufacturing and design. This method involves using advanced adhesive materials to securely join various structural components of an aircraft, offering numerous advantages over traditional mechanical fastening methods. Key aspects of structural bonding in a plane include:
1.Weight Reduction:Aerospace adhesives are lightweight yet incredibly strong, allowing for the elimination of heavy rivets and fasteners. This weight reduction contributes to increased fuel efficiency and enhanced overall aircraft performance.
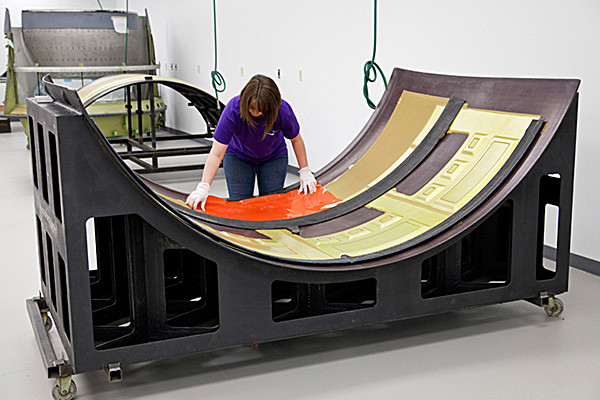
2.Stress Distribution:Adhesive bonding distributes stresses more evenly across the bonded surfaces than traditional fasteners, reducing localized stress concentrations. Improving the aircraft’s structural integrity is beneficial for its overall performance.
3.Improved Aerodynamics:Without the protrusions of rivet heads, bonded surfaces are smoother, leading to improved aerodynamics and reduced drag. This results in better fuel efficiency and overall flight performance.
4.Corrosion Prevention:Rivet holes in traditional fastening methods can create points of vulnerability for corrosion. Aerospace adhesives create a barrier that prevents moisture and environmental factors from reaching critical structural areas, thus enhancing the aircraft’s longevity.
5.Enhanced Design Flexibility:Adhesive bonding allows for more creative and complex designs as it eliminates the need for mechanically accessible joints. This flexibility empowers engineers to optimize the aircraft’s aerodynamic efficiency and overall aesthetics.
6.Vibration Damping:Aerospace adhesives absorb vibrations and dampen noise better than traditional rivets, improving passenger comfort and reducing aircraft structure fatigue.
7.Reduced Fatigue Failure:Adhesive bonding distributes loads more evenly, minimizing the risk of fatigue failure in fastened joints due to cyclic loading.
8.Time and Labor Efficiency:Bonding requires fewer components and less manual labor than traditional fastening methods, resulting in shorter assembly times and reduced production costs.
9.Composite Material Compatibility:Aerospace adhesives are crucial for bonding composite materials in modern aircraft construction. These adhesives offer excellent compatibility with lightweight composite structures, allowing for the creation of strong and durable connections.
Satellite and Spacecraft Applications
Satellite and spacecraft applications demand the utmost precision, reliability, and durability, making aerospace adhesives indispensable in construction and operation. These advanced adhesive solutions are crucial for various aspects of satellite and spacecraft design, ensuring optimal performance and longevity in the harsh conditions of outer space. Key roles of aerospace adhesives in satellite and spacecraft applications include:
- Thermal Protection:Engineers use aerospace adhesives to bond thermal protection materials, which shield satellites and spacecraft from extreme temperature fluctuations. Ensuring these components function correctly and maintain their structural integrity in challenging space environments is essential.
- Component Bonding:Adhesive bonding secures delicate components within satellites and spacecraft, offering exceptional strength while minimizing weight. This method prevents vibration-induced damage and ensures elements remain securely in place during launch and operation.
- Electrical Insulation:We use adhesives with excellent electrical insulation properties to bond and seal electronic components, safeguarding them from the vacuum of space and preserving signal integrity.
- Optical Systems:Aerospace adhesives are essential for assembling and aligning optical systems in satellites, ensuring that telescopes, cameras, and other instruments maintain precise positioning and accuracy.
- Vibration Damping:Adhesive bonding helps dampen vibrations generated during launch and other operational phases, safeguarding delicate equipment and preventing potential malfunctions.
- Sensors and Antennas:Adhesives provide secure attachments for sensors, antennas, and solar panels, allowing for efficient data collection, communication, and power generation.
- Sealing and Pressure Resistance:Engineers use adhesives with high-pressure resistance to seal joints and connections in propulsion systems and fuel tanks. By adopting this approach, we prevent leaks and ensure the components operate safely.
- Reduced Outgassing:Aerospace adhesives with low outgassing properties are crucial to avoid contaminating sensitive equipment and optics, ensuring optimal performance over extended mission durations.
- Microgravity Applications:In the unique microgravity environment of space, adhesive bonding can overcome challenges associated with traditional mechanical fasteners and welds, enabling complex assemblies that are more reliable and efficient.
- Longevity and Reliability:Designers create aerospace adhesives to endure extreme space conditions, including radiation, vacuum, and temperature variations. These adhesives ensure the longevity and reliability of satellite and spacecraft missions.
Thermal Protection Systems
Thermal Protection Systems (TPS) represent a critical aspect of aerospace engineering, safeguarding vehicles and spacecraft from the extreme temperatures experienced during atmospheric reentry and space travel. Aerospace adhesives play a pivotal role in the design, construction, and maintenance of these TPS, ensuring effective heat management and structural integrity in the face of intense thermal challenges.
Adhesive Applications in TPS
Aerospace adhesives find multifaceted applications within TPS, serving as essential components in various thermal management strategies.
Heat Shield Bonding
Adhesive bonding is integral to attaching heat-resistant tiles, panels, or blankets to the vehicle’s exterior. This bonding method ensures secure attachment while effectively dissipating the heat generated during reentry.
Sealing and Insulation
Adhesives with exceptional sealing properties create airtight barriers between TPS components. They prevent heat from infiltrating critical areas and maintain the TPS’s effectiveness.
Flexible Substrates
Aerospace adhesives bind flexible substrates, such as thermal blankets, to the vehicle’s surface. This flexibility ensures a snug fit, accommodating the vehicle’s contours while providing optimal heat resistance.
Challenges in Extreme Environments
The TPS operates in harsh conditions, including high temperatures, rapid heating and cooling cycles, and radiation exposure. Aerospace adhesives used in TPS must withstand these challenges without compromising their adhesive properties or structural integrity.
Material Compatibility
Adhesives are chosen based on compatibility with TPS materials, including ceramics, composites, and refractory metals. Ensuring compatibility prevents material degradation and potential bond failure.
Enhancing Safety and Reliability
Aerospace adhesives contribute to aerospace vehicles’ overall safety and reliability by preventing heat-related damage and maintaining the TPS’s integrity throughout the mission lifecycle.
Research and Innovation
Continuous research and innovation in aerospace adhesives lead to the developing of adhesive solutions that can withstand even higher temperatures and harsher environments, enhancing TPS performance in future missions.
Fuel Tank Sealants
Fuel tank sealants are critical components in aerospace engineering, responsible for maintaining the integrity of fuel systems in aircraft and spacecraft. These specialized aerospace adhesives provide an impenetrable barrier that prevents fuel leakage, corrosion, and contamination while withstanding the unique challenges of the aerospace environment. Essential functions and considerations of fuel tank sealants include:
- Sealing Fuel Systems : Designers create fuel tank sealants to establish a robust and long-lasting seal among various components of fuel systems, including joints, seams, and access panels.
- Chemical Resistance : These sealants must resist the corrosive effects of aviation and space fuels and other chemicals and fluids that may come into contact with the seal.
- Temperature Extremes : Aerospace environments subject sealants to extreme temperatures, ranging from cold at high altitudes to intense heat during reentry orbital operations. Fuel tank sealants must maintain their integrity and effectiveness across this wide temperature range.
- Pressure Variations : Aerospace vehicles experience pressure variations during flight and launch. Fuel tank sealants should be able to accommodate these changes without compromising the seal’s integrity.
- Compatibility with Fuel Types : Formulators design fuel tank sealants to be compatible with various fuel types, including aviation gasoline, jet fuel, and liquid rocket propellants. Compatibility ensures that the adhesive does not react with or degrade the energy.
- Longevity and Reliability : We expect these sealants to retain their sealing properties throughout the entire operational life of the aerospace vehicle, which often spans years or even decades.
- Resistance to Aging : Aerospace sealants must resist aging effects caused by exposure to radiation, oxygen, and other environmental factors that can degrade their performance over time.
- Application Techniques : The application of fuel tank sealants involves precise techniques to ensure complete coverage and adhesion to all relevant surfaces.
- Regulatory Compliance : Aerospace sealants must adhere to stringent industry standards and regulations to ensure the safety and reliability of fuel systems.
- Ongoing Research and Development : Advances in materials science lead to the continuous improvement of fuel tank sealants, enhancing their performance, durability, and resistance to extreme conditions.
Adhesive Inspection and Testing
Inspecting and testing adhesives is critical to ensuring the structural integrity and safety of aerospace components and assemblies that utilize adhesives. These adhesive bonding processes are vital for joining various materials, enhancing load distribution, and minimizing weight. To maintain the highest quality standards, meticulous inspection, and testing protocols are employed:
- Visual Inspection:The initial step involves a comprehensive visual examination of the adhesive application. These measures identify any visible defects, such as uneven bonding, air bubbles, or contamination, that might compromise the adhesive’s effectiveness.
- Ultrasonic Testing:Ultrasonic techniques are employed to assess the quality of adhesive bonds by sending ultrasonic waves through the bond lines. Changes in the wave patterns can reveal irregularities such as voids, delamination, or inadequate adhesive coverage.
- Shear Testing:Shear tests determine the strength of adhesive bonds by subjecting them to controlled force along their bonded surfaces. These actions aid in evaluating the adhesive’s cohesive and adhesive properties, ensuring its ability to withstand anticipated stresses.
- Peel Testing:Peel or bond strength tests measure the force required to separate adhesive-bonded substrates under controlled conditions. This test assesses the adhesive’s resistance to external forces that could lead to detachment.
- Thermal Analysis:Adhesives must endure a range of temperatures in aerospace applications. Thermal analysis techniques like Differential Scanning Calorimetry (DSC) and Thermogravimetric Analysis (TGA) help understand how adhesives react to temperature fluctuations, ensuring they remain stable and effective.
- Chemical Compatibility Testing:Aerospace environments expose adhesives to various chemicals, fuels, and fluids. Chemical compatibility testing ensures adhesives don’t degrade or lose strength when exposed to these substances.
- Microscopic Examination:Microscopy is used to scrutinize adhesive bonds at a microscopic level. This approach facilitates the identification of minute defects, surface irregularities, or inconsistencies that might not be visible to the naked eye.
- Environmental Testing:Aerospace adhesives must withstand diverse ecological conditions, including humidity, moisture, and UV radiation. Accelerated aging tests simulate these conditions to assess the adhesive’s long-term durability.
Application Techniques and Equipment
Application Techniques and Equipment are pivotal in achieving precise and reliable adhesive bonding in aerospace applications. The success of adhesive bonds largely depends on the careful selection of techniques and equipment to ensure optimal performance, structural integrity, and safety:
1.Surface Preparation:Proper surface preparation is essential to ensure adequate bonding. Techniques like cleaning, sanding, and chemical treatments provide that surfaces are free from contaminants, roughened for better adhesion, and optimized for a strong bond.
2.Manual Application:Hand application is suitable for intricate areas where precision matters. It allows for controlled adhesive placement, ensuring even coverage and minimal waste.
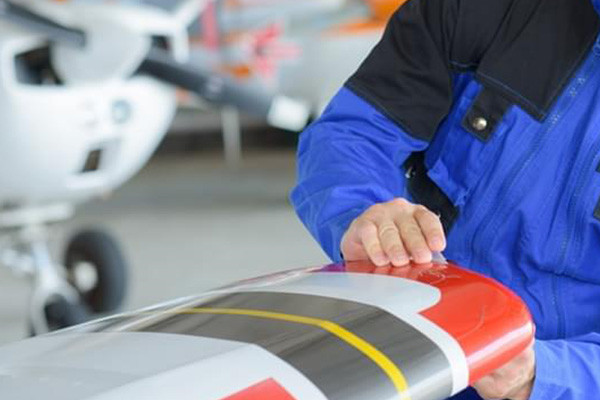
3.Automated Dispensing:Automated dispensing systems provide consistency and accuracy in adhesive application. These systems use robotic arms or automated machinery to apply adhesive with high precision, reducing human error and increasing efficiency.
4.Spray Application:We use spray guns for large surface areas or complex geometries. They evenly distribute adhesive in a fine mist, ensuring uniform coverage and reduced material consumption.
5.Film Adhesive Application:Film adhesives come in pre-cut sheets or rolls and are suitable for large, flat surfaces. They are applied using pressure and heat, ensuring uniform thickness and eliminating the need for mixing.
6.Paste Application:Adhesive pastes are manually or mechanically applied and are suitable for vertical or overhead bonding. They provide flexibility in application, and people often use them to bond uneven or irregular surfaces.
7.Curing Techniques:Adhesives require curing to achieve their full strength. Heat, UV, and chemical curing are standard techniques based on adhesive type and application requirements.
8.Hot Melt Adhesive Application:Hot melt adhesives are heated to a liquid state and then applied. They solidify upon cooling, making them suitable for fast assembly processes.
9.Roller Application:We use rollers to apply pressure and ensure uniform contact between the adhesive and the substrate. Practitioners commonly use this technique in conjunction with film adhesives.
10.Vacuum Bagging:We utilize vacuum bagging for complex structures. We place the adhesive-coated components in a vacuum bag, and the vacuum pressure removes air while applying uniform pressure for bonding.
Safety and Regulatory Compliance
Safety and regulatory compliance are paramount considerations within aerospace adhesives, ensuring the structural integrity of aircraft components and the well-being of passengers and crew. In this context, several key points underscore the significance of adhering to safety standards and regulations:
- Material Selection and Testing:Aerospace adhesives must undergo rigorous testing to meet industry standards. Manufacturers must carefully select adhesive materials that demonstrate exceptional durability, heat resistance, and chemical stability, ensuring optimal performance even in extreme operational conditions.
- Certification and Approval:Regulatory agencies such as the Federal Aviation Administration (FAA) in the United States and the European Union Aviation Safety Agency (EASA) in Europe are pivotal in evaluating and certifying aerospace adhesive products. These certifications indicate that the adhesive has met the necessary safety requirements and that manufacturers can use it in aircraft construction and maintenance.
- Performance under Stress:Aerospace adhesives must maintain their adhesive properties and structural integrity under various stresses, including vibration, pressure changes, and fluctuating temperatures. Compliance with safety regulations ensures that adhesives continue to perform as expected throughout the aircraft’s lifecycle.
- Fire Resistance and Smoke Emission:Fire safety is a critical concern in aviation. Aerospace adhesives must possess fire-resistant properties and low smoke emission levels to prevent the rapid spread of flames and the release of toxic gases in the event of a fire.
- Application Processes and Training:The correct application of aerospace adhesives is essential for their effectiveness and longevity. Safety and regulatory compliance also involve training technicians and mechanics properly, ensuring they apply adhesives according to manufacturer guidelines and industry best practices.
- Environmental Impact:In addition to passenger safety, aerospace adhesive regulations address ecological impact. Adhesive formulations should align with rules to reduce volatile organic compound (VOC) emissions and other harmful substances, contributing to the aviation industry’s commitment to sustainability.
Research and Innovation in Aerospace Adhesives
The aerospace industry continuously searches for lighter, stronger, and more efficient materials to enhance aircraft performance and safety. One significant innovation that has garnered attention is the development of aerospace adhesives. These advanced adhesive solutions transform how aircraft are designed, manufactured, and maintained.
Importance of Aerospace Adhesives in Modern Aviation
- Weight Reduction:Aerospace adhesives play a pivotal role in reducing the weight of aircraft structures compared to traditional mechanical fastening methods. This weight reduction contributes to improved fuel efficiency and reduced emissions, aligning with the industry’s sustainability goals.
- Enhanced Design Flexibility:Adhesives enable the bonding of dissimilar materials, expanding design possibilities and allowing engineers to optimize structures for strength and aerodynamics.
- Stress Distribution:Adhesives distribute stresses more evenly across bonded surfaces, reducing the concentration of stress points and improving overall structural integrity.
Challenges Driving Research and Innovation
- Extreme Conditions:Aircraft operate in various environments, from freezing altitudes to scorching temperatures. Adhesives must withstand these extremes while maintaining their integrity.
- Safety and Reliability:Aerospace adhesives must meet rigorous safety standards. Researchers are constantly developing adhesives that can withstand impact, vibration, and fire without compromising security.
- Longevity and Maintenance:Aircraft have long service lives, necessitating adhesives that can withstand aging, UV exposure, and various chemicals while requiring minimal maintenance.
Recent Technological Advancements
- Nanotechnology Integration:Researchers are developing nano adhesives with enhanced mechanical properties and resistance to temperature variations, pushing the boundaries of adhesive performance.
- Self-Healing Adhesives:Researchers are exploring the incorporation of microcapsules containing adhesive material that can rupture and mend cracks, extending the lifespan of bonded components.
- Innovative Adhesives:Researchers are investigating adhesives with embedded sensors capable of real-time structural health monitoring, offering insights into the integrity of bonded areas.
Sustainability and Environmental Considerations
The aerospace industry’s growing commitment to sustainability has spurred significant advancements in developing environmentally friendly materials. Within this context, the focus on aerospace adhesives has gained prominence due to their widespread application in aircraft manufacturing and maintenance.
Reduced Carbon Footprint
- Water-Based Formulations:Water-based aerospace adhesives have emerged as a more sustainable alternative to traditional solvent-based adhesives. These formulations minimize volatile organic compound (VOC) emissions, reducing both air pollution and health risks to workers. Water-based adhesives also contribute to a healthier work environment due to their lower toxicity.
- Energy-Efficient Curing Processes:Adopting energy-efficient curing processes for aerospace adhesives helps reduce overall energy consumption during manufacturing. Techniques such as UV-curing and electron beam curing accelerate the bonding process and require less energy than traditional heat-curing methods.
Recyclability and End-of-Life Considerations
- Disassembly and Reusability: Aerospace adhesives designed for easy disassembly facilitate component reusability, contributing to a circular economy model. The ability to disassemble bonded parts without compromising their integrity is crucial for efficient maintenance, repair, and potential reconfiguration of aircraft components.
- Compatibility with Composites Recycling:As modern aircraft rely heavily on composite materials, sustainable adhesives must be compatible with hybrid recycling processes. Formulators are developing adhesive formulations that allow for easy separation from composite materials during recycling, ensuring the reclamation of adhesives and substrates without generating additional waste.
Longevity and Performance
- Extended Service Life:Sustainable aerospace adhesives aim to enhance the longevity and durability of aircraft components. By providing excellent resistance to environmental factors such as temperature fluctuations, humidity, and corrosive agents, these adhesives contribute to longer service intervals and reduced material waste.
- Reduced Maintenance Frequency:Adhesives that maintain their integrity over an extended period minimize the need for frequent maintenance and replacements. We can work towards achieving sustainability goals by reducing material inputs and waste generation.
Regulatory Compliance and Future Outlook
- Stringent Regulations:The aerospace industry is subject to strict regulations regarding emissions, waste generation, and overall environmental impact. Sustainable aerospace adhesives must adhere to these regulations while delivering optimal performance and reliability.
- Innovation and Collaboration:Ongoing research and collaboration within the aerospace and adhesive industries continue to drive the development of new sustainable solutions. As technology advances, there is potential for even more eco-friendly adhesive options that balance performance with environmental consciousness.
Future Advancements in Aerospace Bonding
The realm of aerospace bonding is on the brink of groundbreaking advancements poised to revolutionize aircraft and spacecraft design and performance. As engineers and researchers delve deeper into the development of cutting-edge aerospace adhesives, several key trends and breakthroughs are emerging that promise to reshape the industry:
- Nanotechnology Integration:One of the most promising directions in aerospace bonding is the incorporation of nanotechnology into adhesive formulations. Nanomaterials, such as nanoparticles and nanofibers, are harnessed to enhance adhesive strength, durability, and resistance to extreme conditions. These nano-enhanced adhesives offer the potential to improve the structural integrity of aircraft and spacecraft components significantly.
- Self-Healing Adhesives:Researchers are actively exploring the concept of self-healing adhesives that can autonomously repair minor damage. While drawing inspiration from biological processes, researchers have integrated microcapsules of healing agents into these adhesives, which users can activate to release and repair cracks or defects in the adhesive layer. Such self-healing capabilities could extend the lifespan of aerospace structures and reduce maintenance needs.
- Innovative Adhesive Systems: Integrating smart technologies into aerospace adhesive systems is gaining traction. These adhesives can sense temperature, pressure, or stress changes and respond by altering their properties to optimize performance. This adaptability enhances the overall efficiency and safety of aerospace structures and opens the door to predictive maintenance strategies.
- Enhanced Thermal Management:Researchers are developing aerospace bonding solutions focusing on improved thermal management. Adhesives capable of efficiently dissipating heat can mitigate temperature-related stresses on components, ensuring stable performance even during extreme thermal conditions such as reentry or supersonic flight.
- Lightweighting and Fuel Efficiency:Aerospace engineers increasingly prefer adhesive solutions that enable lightweighting without compromising structural integrity. Advanced bonding techniques allow lighter materials, improving fuel efficiency and reducing aviation and space travel emissions.
- Multi-Material Bonding:As aerospace designs become more complex, the ability to bond different materials seamlessly becomes essential. Adhesives that can bond dissimilar materials, such as metals, composites, and ceramics, with high strength and durability enable the creation of innovative structures that optimize material properties for specific applications.
Aerospace adhesive has become a linchpin in the aviation and space industries, fostering unprecedented advancements in engineering and design. Its capacity to withstand extreme temperatures, vibrations, and mechanical stresses has elevated the safety, efficiency, and performance of aircraft and spacecraft. As aerospace technologies continue to evolve, the role of adhesive solutions will remain pivotal in shaping the next generation of air and space vehicles. With ongoing research and innovations, aerospace adhesives are poised to contribute to the realization of ambitious goals in space exploration and redefine the boundaries of aviation performance.