Acrylic Adhesive
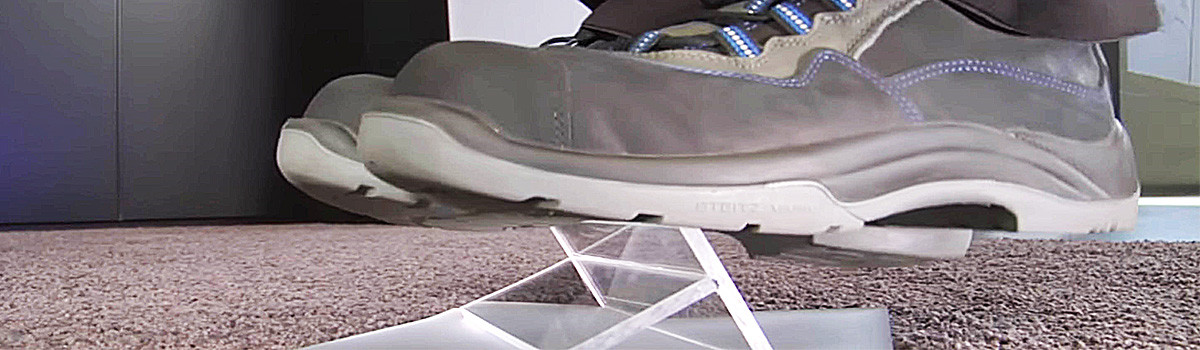
In today’s rapidly evolving landscape of materials science and industrial technology, adhesion has witnessed remarkable advancements, with acrylic bonding solutions emerging as a prominent and versatile player. Acrylic adhesives, renowned for their strong bonding capabilities, have carved a significant niche in various industries, from automotive and electronics to medical devices and architecture. This exploration delves into the innovative world of acrylic bonding, dissecting its mechanisms, applications, and impact.
By peering into the intricacies of acrylic bonding solutions, we gain insights into how these adhesives have revolutionized the way materials are joined, offering a comprehensive understanding of their properties, advantages, and challenges. Join us on a journey to uncover the transformative power of acrylic bonding in technology, design, and manufacturing.
What is acrylic bonding, and why is it significant in various industries?
Acrylic bonding refers to joining or adhering to two or more acrylic surfaces using adhesive methods specifically designed for acrylic materials. Acrylic, known as polymethyl methacrylate (PMMA), is a transparent thermoplastic widely used in various industries due to its optical clarity, weather resistance, and versatility. Acrylic bonding is significant in several industries for several reasons:
- Manufacturing and Fabrication: Acrylic is commonly used in the manufacturing of various products, such as display cases, signage, point-of-sale displays, and lighting fixtures. Proper bonding techniques are crucial to creating seamless and visually appealing structures, ensuring the bond is strong, durable, and optically transparent.
- Automotive Industry: Acrylic is often used for vehicle windows, headlight lenses, and taillight covers. Proper bonding is necessary to maintain structural integrity, prevent leaks, and ensure visibility without distortion.
- Aerospace: In aerospace applications, where weight, strength, and clarity are essential, acrylic bonding is used for cockpit windows, cabin partitions, and other transparent components. The bonding must withstand extreme temperatures, pressure differentials, and vibration.
- Medical Devices: Acrylic is used in medical devices like diagnostic equipment, medical displays, and protective barriers. Secure bonding is essential to meet strict regulatory requirements and ensure the safety and performance of these devices.
- Construction: Acrylic is used in architectural applications such as skylights, canopies, and noise barriers. Strong bonding is essential to withstand environmental factors and ensure the structure’s safety.
- Art and Design: Acrylic is a popular material for artists and designers due to its clarity and versatility. Bonding techniques are used to create complex sculptures, installations, and other artistic projects.
- Electronics: Acrylic is sometimes used for electronic devices’ enclosure panels and protective covers. Proper bonding ensures that the discussions remain securely attached and do not hinder the functionality of the electronics.
- Marine Industry: Acrylic is used for marine windows, hatches, and aquariums due to its transparency and resistance to water. Adequate bonding is crucial to maintain the integrity of these components and prevent leaks.
Various adhesive methods are used to achieve successful acrylic bonding, such as solvent welding, adhesive bonding, UV-curing adhesives, and mechanical fasteners. The choice of method depends on factors such as the type of acrylic, the specific application, and the desired bond strength.
Proper bonding techniques are essential to ensure the functionality, safety, and aesthetics of acrylic components in various industries. A strong and reliable bond helps prevent defects, leaks, and failures, ultimately contributing to the overall quality and longevity of products and structures.
How do acrylic adhesives work on different surfaces?
Acrylic adhesives are versatile and commonly used adhesives that work on various surfaces. They are often chosen for their strong bonding capabilities, quick curing times, and resistance to environmental factors. The way acrylic adhesives work on different surfaces is influenced by their chemical composition and the nature of the substrates involved. Here’s how they generally work:
- Chemical Composition:Acrylic adhesives are typically made from acrylic polymers or copolymers. These polymers can be tailored to have specific properties, such as flexibility, toughness, or resistance to chemicals. The adhesive may also contain additives to enhance its performance.
- Surface Preparation:Proper surface preparation is essential for achieving strong adhesion with acrylic adhesives. Characters must be clean, dry, and free from contaminants like dust, oils, and greases. Some surfaces might benefit from light sanding or cleaning with solvents to ensure optimal bonding.
- Mechanical Interlocking:Acrylic adhesives create bonds through mechanical interlocking and chemical adhesion. When the adhesive is applied to a surface, it flows into microscopic irregularities on the substrate’s surface, creating a mechanical bond. This interlocking helps increase the surface area of contact and enhances adhesion.
- Chemical Bonding:Acrylic adhesives also chemically bond to surfaces through a process known as “wetting out.” The adhesive’s molecules penetrate the microstructure of the substrate’s surface, creating bonds at a molecular level. The adhesive forms intermolecular forces with the surface molecules, which leads to adhesion.
- Curing Process:Acrylic adhesives cure through a process called polymerization. This involves the formation of chemical bonds within the adhesive itself, causing it to harden and solidify. Depending on the specific formulation, acrylic adhesives can cure through various mechanisms, such as heat, UV light, or moisture.
- Substrate Compatibility:Acrylic adhesives are known for compatibility with many substrates, including metals, plastics, glass, ceramics, wood, and some fabrics. However, the compatibility might vary depending on the adhesive formulation and the substrate’s nature. Some adhesives are specially designed for bonding specific materials, such as acrylic-to-acrylic or metal-to-metal.
- Temperature and Environmental Resistance:Acrylic adhesives often exhibit suitable temperature and environmental resistance. They can withstand various temperatures and resist moisture, UV radiation, and chemicals. This makes them ideal for both indoor and outdoor applications.
When were acrylic bonding solutions first introduced, and how have they evolved?
Acrylic bonding solutions, also known as acrylic adhesives or acrylic resins, have been around for several decades and have evolved significantly since their introduction. The development of acrylic bonding solutions can be traced back to the mid-20th century, with notable advancements occurring over the years. Here’s an overview of their evolution:
- 1950s-1960s:Acrylic bonding solutions were initially developed as alternatives to traditional solvent-based adhesives. The earliest formulations were based on polymethyl methacrylate (PMMA) or similar acrylic polymers. These early adhesives offered improved environmental and health safety compared to solvent-based options. However, their initial performance and versatility were limited.
- 1970s-1980s:As research and development in the field of polymers advanced, acrylic bonding solutions underwent significant improvements in terms of adhesive strength, flexibility, and durability. New formulations and additives were introduced to enhance their bonding capabilities across various materials, including plastics, metals, ceramics, and more. These advancements increased adoption in multiple industries, including automotive, aerospace, and electronics.
- The 1990s-2000s:The 1990s saw further developments in acrylic bonding technology, including introduction of two-part acrylic adhesives. These formulations comprised a resin and a curing agent that were mixed before application. Two-part acrylic adhesives offered enhanced performance properties, such as faster cure times, higher bond strengths, and improved resistance to environmental factors like temperature and humidity. These adhesives found applications in demanding industries where structural integrity and long-term durability were critical.
- 2000s-Present:In recent years, acrylic bonding solutions have continued to evolve with a focus on sustainability, ease of use, and improved bonding performance. Manufacturers have introduced innovations such as UV-curable acrylic adhesives, which provide rapid curing through exposure to ultraviolet light, reducing assembly time and energy consumption. Additionally, nanotechnology advancements have enabled nanostructured acrylic adhesives to develop, offering even stronger and more precise bonds.
Overall, the evolution of acrylic bonding solutions has been characterized by improvements in adhesive strength, flexibility, durability, curing methods, and versatility across various substrates. These adhesives have become essential components in modern manufacturing and assembly processes, contributing to developing innovative products and technologies.
What are the critical components of modern acrylic bonding formulations?
Modern acrylic bonding formulations typically comprise several critical components that achieve firm and durable adhesive properties. These components may vary slightly depending on the specific application and desired characteristics of the adhesive, but here are the key elements commonly found in acrylic bonding formulations:
- Acrylic Polymers or Resins:The primary component of acrylic adhesives is the acrylic polymer or resin. Acrylic polymers are typically derived from acrylic monomers like methyl methacrylate (MMA), ethyl methacrylate (EMA), butyl methacrylate (BMA), and others. These polymers provide the adhesive with its main bonding strength, durability, and resistance to environmental factors.
- Initiators and Catalysts:Acrylic adhesives are often formulated as two-part systems, where one part contains initiators or catalysts that initiate the polymerization process. Initiators can be thermal or photochemical and are responsible for kickstarting the chemical reaction that turns liquid acrylic monomers into a solid polymer network.
- Crosslinkers:Crosslinkers help create a three-dimensional network within the polymer structure, enhancing the adhesive’s overall strength and toughness. They are critical in improving the adhesive’s heat, chemicals, and mechanical stress resistance.
- Fillers and Reinforcements:Fillers are added to acrylic adhesive formulations to improve viscosity, flow, and impact resistance properties. Reinforcements like glass fibers or nanoparticles can be included to enhance mechanical properties, making the adhesive suitable for demanding applications.
- Plasticizers:Plasticizers are additives that improve the flexibility and elasticity of the adhesive. They can help maintain adhesive performance over various temperatures and environmental conditions.
- Adhesion Promoters:These are compounds added to enhance the adhesive’s ability to bond to various substrates. They promote surface wetting and improve the adhesive’s contact with the substrate.
- Modifiers:Modifiers can be added to adjust specific adhesive properties, such as viscosity, cure speed, and adhesion strength. They allow formulators to tailor the adhesive to meet the requirements of different applications.
- UV Stabilizers and Antioxidants:Acrylic adhesives can be susceptible to degradation from exposure to UV light and oxidation. UV stabilizers and antioxidants are added to formulations to extend the adhesive’s lifespan and maintain its performance over time.
- Solvents:Solvents control the viscosity of the adhesive formulation, making it easier to apply and ensuring proper substrate wetting. Solvents are sometimes added to create a more manageable application consistency, but they may evaporate during the curing process.
It’s important to note that these components’ exact formulation and proportions can vary based on the specific adhesive application, performance requirements, and manufacturing processes. Formulators often optimize these components to balance adhesive strength, flexibility, durability, and desired properties.
How do environmental factors affect the performance of acrylic-bonded joints?
Acrylic-bonded joints, also known as adhesive joints, are formed using acrylic-based adhesives to bond two surfaces together. Various environmental factors can significantly influence the performance of these joints. Here’s how different environmental conditions can affect the performance of acrylic-bonded joints:
- Temperature: Acrylic adhesives can be sensitive to temperature changes. High temperatures can soften or weaken the glue, potentially leading to bond failure. On the other hand, extremely low temperatures can cause the adhesive to become brittle, reducing its flexibility and impact resistance. It’s essential to consider the intended operating temperature range of the joint when selecting an acrylic adhesive.
- Humidity and Moisture: Moisture can degrade the performance of acrylic adhesives over time. Water absorption can cause swelling of the adhesive layer, leading to reduced bond strength. Acrylic adhesives may also experience reduced adhesion and cohesion properties in humid environments. Moisture exposure can result in long-term deterioration of the joint’s mechanical properties.
- UV Exposure: Ultraviolet (UV) radiation from sunlight can degrade some types of acrylic adhesives. UV exposure can lead to yellowing, embrittlement, and loss of adhesive strength. Suppose the acrylic-bonded joint will be exposed to outdoor or UV-rich environments. In that case, selecting an adhesive resistant to UV degradation or protecting the joint with coatings or barriers is essential.
- Chemical Exposure: Acrylic adhesives can be sensitive to certain chemicals. Exposure to chemicals such as solvents, acids, and bases can cause the adhesive to soften, swell, or chemically react, reducing bond strength. It’s crucial to consider the chemical environment in which the joint will be placed and choose a chemically compatible adhesive.
- Substrate Compatibility: Acrylic adhesives may have different levels of compatibility with various substrates. Some substrates, like plastics or metals, might be more susceptible to chemical interaction with the adhesive, which could weaken the bond. Testing the adhesive on the specific substrates you intend to bond is essential to ensure compatibility and adequate adhesion.
- Aging and Creep: Over time, acrylic adhesives can experience creep, a gradual deformation under constant load. This can lead to a loss of joint integrity and reduced performance. Environmental factors, especially temperature and humidity, can accelerate the aging and creep processes, compromising the joint’s strength.
- Mechanical Stress: Environmental conditions can also affect the mechanical stress the joint experiences. Temperature changes, moisture fluctuations, and exposure to external forces can all impact the joint’s overall performance and longevity.
To ensure the best performance of acrylic-bonded joints under varying environmental conditions, carefully select an appropriate adhesive for the specific application. Manufacturers often provide data sheets that detail the adhesive’s performance characteristics and recommended ecological conditions. Additionally, conducting thorough testing and considering the long-term effects of environmental exposure is crucial for designing reliable acrylic-bonded joints.
What industries benefit the most from acrylic bonding solutions, and why?
Acrylic bonding solutions, often called acrylic adhesives or acrylic-based adhesives, are versatile and widely used in various industries due to their strong bonding capabilities, durability, and resistance to different environmental conditions. The sectors that benefit the most from acrylic bonding solutions include:
1.Automotive Industry: Acrylic bonding solutions are used in automotive manufacturing to bond components like body panels, trim, mirrors, and interior parts. Their high strength and resistance to vibrations, temperature changes, and chemicals make them ideal for ensuring the structural integrity of vehicles.
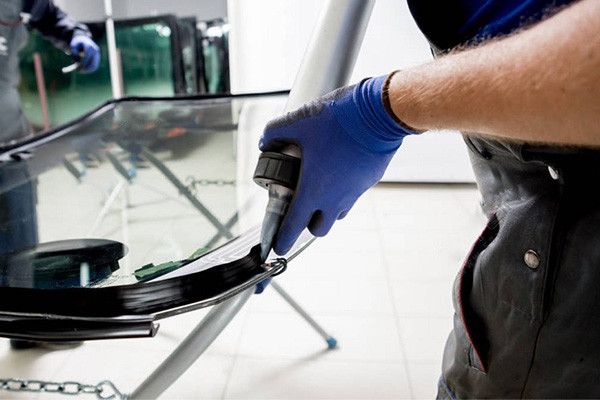
2.Aerospace Industry: Acrylic adhesives are used in the aerospace sector to bond critical components such as composite materials, structural parts, and interior fittings. They offer lightweight bonding solutions with high strength and durability, reducing the aircraft’s overall weight and improving fuel efficiency.
3.Electronics Industry: Acrylic bonding solutions assemble electronic devices, especially in applications where heat resistance and electrical insulation are essential. They provide reliable bonding for displays, touchscreens, and circuit boards.
4.Construction Industry: Acrylic adhesives find applications in the construction industry for bonding building materials like glass, metal, plastic, and stone. Their ability to provide solid, flexible bonds that can withstand weathering and thermal expansion/contraction makes them valuable for architectural projects.
5.Signage and Display Industry: Acrylic bonding solutions are commonly used in the signage and display industry for mounting graphics, signs, and decorative elements onto various substrates. Their transparency and ability to create clean, nearly invisible bonds contribute to the aesthetics of the finished products.
6.Medical and Healthcare Industry: Acrylic bonding solutions are used in medical device manufacturing due to their biocompatibility and ability to bond materials like plastics, metals, and ceramics. They assemble devices like medical instruments, implants, and diagnostic equipment.
7.Marine Industry: In marine applications, where exposure to water and harsh environmental conditions is daily, acrylic bonding solutions offer excellent resistance to moisture and salt water. They bond components in boat construction, underwater equipment, and marine structures.
8.Consumer Goods Industry: Acrylic adhesives are found in various consumer goods, including appliances, furniture, and sporting goods. Their versatility and ability to bond different materials make them valuable for creating durable products.
The key benefits that make acrylic bonding solutions valuable across these industries include the following:
- High Strength: Acrylic adhesives offer strong and durable bonds, ensuring assembled components’ longevity and structural integrity.
- Versatility: Acrylic adhesives can bond with various materials, including metals, plastics, glass, ceramics, and composites, making them suitable for multiple applications.
- Temperature Resistance: They can withstand a wide range of temperatures, making them suitable for applications that experience extreme temperature fluctuations.
- Chemical Resistance: Acrylic adhesives often resist chemicals, solvents, and environmental factors, making them ideal for demanding industrial environments.
- Fast Curing: Acrylic adhesives can have relatively short curing times, allowing for efficient assembly processes.
However, it’s important to note that the specific choice of adhesive depends on the requirements of each industry and application. Different adhesive technologies may also have advantages and limitations, so enterprises often evaluate and select the most appropriate bonding solution based on their unique needs.
How do designers optimize joint designs for adequate acrylic bonding?
Optimizing joint designs for adequate acrylic bonding involves a combination of factors related to the creation of the joint itself and the choice of adhesive or bonding method. Acrylic, commonly known as PMMA (polymethyl methacrylate), is often used in various applications such as signage, displays, automotive parts, and more. Here are some considerations for optimizing joint designs for acrylic bonding:
- Surface Preparation:
- Cleanliness is crucial. Ensure that the surfaces to be bonded are free from dust, oils, and contaminants. Use alcohol-based cleaners to clean the surfaces thoroughly.
- Roughening the surfaces slightly can provide more bonding area and improve adhesive adhesion. This can be done using sandpaper or abrasive methods.
- Joint Design:
- The joint design plays a vital role in the strength and durability of the bond. Standard collaborative techniques include butt, lap, T, and miter joints.
- Consider using a joint design that maximizes the surface area in contact with the adhesive. A larger bonding area generally results in a stronger bond.
- Ensure that the joint design allows for proper adhesive application and minimizes the chances of air pockets or voids in the bond.
- Adhesive Selection:
- Choose an adhesive specifically designed for acrylic bonding. Acrylic adhesives are available in various forms, including liquid adhesives, tapes, and structural adhesives.
- When selecting an adhesive, consider factors like cure time, temperature resistance, and bond strength.
- Adhesive Application:
- Follow the manufacturer’s instructions for adhesive mixing and application. Proper mixing and application are crucial for achieving a solid bond.
- Apply the adhesive evenly to both surfaces to ensure a uniform bond line.
- Curing Conditions:
- Adhesives often require specific curing conditions like temperature and humidity to achieve optimal bond strength. Follow the recommended curing conditions provided by the adhesive manufacturer.
- Clamping and Fixturing:
- Use appropriate clamping or fixturing methods to hold the joint while the adhesive cures. This prevents movement that could compromise the bond.
- Testing and Quality Control:
- Perform testing to validate the strength of the bond following relevant standards or requirements. This can involve tension, shear, or peel tests.
- Implement quality control measures to ensure consistency and reliability in the bonding process.
- Environmental Considerations:
- Consider the operating environment of the bonded acrylic parts. If exposed to extreme temperatures, UV radiation, or other environmental factors, choose an adhesive that can withstand these conditions.
- Prototyping and Iteration:
- It’s recommended to prototype and test different joint designs and adhesive combinations to find the optimal solution for your specific application.
- Safety Precautions:
Follow safety guidelines when working with adhesives, especially if they involve volatile organic compounds (VOCs) or require ventilation.
Remember that the specifics of optimizing acrylic bonding can vary based on the application and the adhesive used. Consult with adhesive manufacturers, conduct tests, and possibly seek advice from professionals experienced in acrylic adhesion for the best results.
What role does surface preparation play in achieving strong acrylic bonds?
Surface preparation plays a crucial role in achieving acrylic solid bonds. Like many other types of adhesives, acrylic adhesives rely on proper surface preparation to ensure adequate bonding between the adhesive and the substrate. Good surface preparation enhances adhesion by improving the wetting and spreading of the adhesive on the substrate surface. Here’s why surface preparation is essential for achieving strong acrylic bonds:
- Cleanliness:The surface needs to be clean and free from dirt, dust, grease, oils, and any contaminants that could hinder the bonding process. Impurities can create barriers between the adhesive and the substrate, leading to poor adhesion.
- Surface Roughness:Acrylic adhesives generally adhere better to surfaces with some roughness. Proper surface roughness provides more surface area for the adhesive to grip onto, increasing the overall bonding strength.
- Surface Activation:Many substrates, especially those with low surface energy (e.g., plastics), may not readily bond with acrylic adhesives. Surface activation techniques like corona treatment, plasma treatment, or chemical priming can increase the substrate’s surface energy, making it more receptive to adhesion.
- Removal of Oxidation:Some substrates can develop an oxide layer over time, hindering bonding. Abrasive techniques like sanding or chemical methods can remove this oxide layer and promote better adhesion.
- Compatibility:Some substrates might have release agents, mold-release residues, or other coatings that must be removed to achieve good adhesion. Surface preparation methods ensure these coatings are removed or altered for proper bonding.
- Decontamination:Substrates used in industrial environments may be exposed to contaminants or residues that must be removed before bonding to achieve consistent and robust adhesive bonds.
- Adhesive Wetting:Like other liquid materials, Acrylic adhesives spread more effectively on clean and properly prepared surfaces. This improved wetting leads to better contact between the adhesive and the substrate, resulting in stronger bonds.
- Uniformity:Proper surface preparation ensures a uniform and consistent surface, essential for uniform adhesive application and bonding.
Standard surface preparation methods for achieving strong acrylic bonds include:
- Mechanical Abrasion:Sanding, grinding, or other abrasive methods roughen the substrate surface, creating microscopic grooves that enhance adhesive bonding.
- Solvent Cleaning:Use solvents to clean the substrate surface and remove contaminants before applying the adhesive.
- Plasma Treatment:An energetic gas plasma activates the substrate surface and improves its bonding characteristics.
- Corona Treatment:Electrical discharge is used to alter the substrate’s surface energy, improving adhesive wetting.
- Chemical Priming:Applying a chemical primer or adhesion promoter to the substrate to enhance its bonding properties.
Proper surface preparation is a critical step in achieving acrylic solid bonds. It ensures the adhesive can adhere to the substrate effectively, improving bond strength, durability, and overall performance.
How do temperature and curing time affect the bond formation process?
The bond formation process can refer to various bonds, such as chemical bonds in reactions, adhesive bonds, or even bonds in materials like polymers and composites. The effects of temperature and curing time on bond formation processes can vary depending on the specific context, but here are some general principles that can help you understand their influence:
- Chemical Reactions:In chemical reactions, temperature and time can significantly influence the rate and extent of bond formation. Higher temperatures generally increase the kinetic energy of molecules, leading to more frequent collisions and higher reaction rates. However, excessively high temperatures can lead to side reactions, decomposition, or other undesired effects. Curing time allows sufficient opportunity for reactants to interact and form new bonds. Longer curing times might lead to more complete conversion of reactants to products, but there can be a point of diminishing returns where reaction equilibrium is reached, or other factors start to dominate.
- Adhesive Bonding:In adhesive bonding processes, such as gluing materials together, temperature and curing time play crucial roles in achieving robust and durable bonds. Many adhesives have an optimal temperature range where they exhibit the best performance. Higher temperatures can enhance the diffusion of adhesive molecules into the substrate, improving wetting and adhesion. Curing time ensures the adhesive has sufficient time to flow, wet the surfaces, and establish strong intermolecular interactions.
- Polymerization and Curing:In polymers and composites, temperature and curing time influence the polymerization and crosslinking processes. These processes determine the mechanical properties and overall performance of the final material. Higher temperatures can accelerate polymerization reactions by providing the necessary activation energy. Longer curing times allow for complete crosslinking, improving strength, stiffness, and other material properties. However, if curing times are shorter, the material might become brittle or prone to degradation.
- Metal Joining:In metal joining processes like welding and soldering, temperature and time control the melting, diffusion, and solidification of metals. Proper temperature and holding time are essential to form a strong metallurgical bond between the joined parts. A sufficient temperature or time can lead to complete bonding and strong joints.
- Biological Systems:In biological systems, temperature and time influence processes like enzyme-catalyzed reactions, protein folding, and DNA hybridization. Enzymatic reactions often have temperature optima that maximize enzyme activity, while folding techniques can be sensitive to temperature changes that disrupt hydrogen bonding and other non-covalent interactions.
The effects of temperature and curing time on bond formation processes are interconnected and context-dependent. The right combination of temperature and time is crucial to achieve the desired level of bond strength, stability, and overall performance in various applications. Considering factors such as reaction kinetics, material properties, and the specific chemistry involved is essential when optimizing temperature and curing time parameters.
What are the potential challenges and limitations of acrylic bonding solutions?
Acrylic bonding solutions, commonly called acrylic adhesives or acrylic-based glues, have several advantages, such as high bond strength, versatility, and resistance to various environmental conditions. However, they also come with specific challenges and limitations:
1.Substrate Compatibility:Acrylic adhesives might not bond well with all substrates. They work better on plastics, metals, glass, and some composites. However, they may adhere less effectively to materials with low surface energy, like polyethylene or polypropylene.
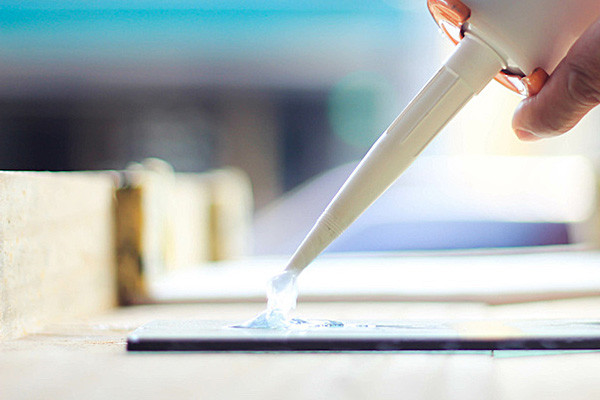
- Cure Time:Acrylic adhesives often require relatively longer curing times than other adhesive types. This can slow down production processes and limit their applicability when fast assembly is required.
- Temperature Sensitivity:While acrylic adhesives generally offer good temperature resistance, extreme temperature variations can affect their performance. High temperatures might lead to adhesive softening or even degradation, while very low temperatures can make them brittle, affecting the bond’s integrity.
- UV Sensitivity:Some acrylic adhesives can degrade when exposed to prolonged UV radiation, which might reduce bond strength over time. This makes them only suitable for outdoor applications if specifically formulated to resist UV exposure.
- Shear Strength:Acrylic adhesives might have lower shear strength than other adhesive types like epoxy adhesives. This makes them less suitable for applications with predominant shear forces, such as structural bonding.
- Chemical Resistance:While acrylic adhesives generally resist many chemicals, they might perform poorly in highly aggressive chemical environments. Certain chemicals can weaken or degrade the adhesive, leading to a loss of bond strength.
- Gap Filling:Acrylic adhesives usually don’t fill gaps as effectively as other adhesive types, like anaerobic adhesives or certain epoxies. This means the bonded surfaces must fit closely together for optimal bonding.
- Aesthetic Concerns:Acrylic adhesives might leave visible bonds on transparent surfaces like glass, which could be aesthetically undesirable in some applications.
- Health and Safety:Acrylic adhesives can emit volatile organic compounds (VOCs) during curing, contributing to indoor air pollution and potentially impacting human health. When working with these adhesives, adequate ventilation and personal protective equipment might be necessary.
- Joint Design and Surface Preparation:Achieving strong bonds with acrylic adhesives requires proper joint design and surface preparation. Contaminants, rough surfaces, or improper standard configurations can all affect the adhesive’s effectiveness.
It’s important to note that not all acrylic adhesives have the same properties and limitations. There are variations in formulation and performance among different brands and types of acrylic adhesives. Choosing the suitable adhesive for a specific application requires considering factors like substrate type, environmental conditions, load-bearing requirements, and production processes.
How do modern testing methods evaluate the quality of acrylic bonds?
Modern testing methods for evaluating the quality of acrylic bonds typically involve a combination of destructive and non-destructive techniques. These methods assess the strength, durability, and integrity of the bonds formed between acrylic materials. Here are some standard methods used for evaluating acrylic adhesives:
- Shear Testing:Shear testing involves applying a force perpendicular to the plane of the bond to determine the bond’s strength and adhesion properties. This test helps measure the maximum force the bond can withstand before failure. It’s commonly used for assessing the quality of adhesive bonds.
- Tensile Testing:Tensile testing involves applying a force parallel to the direction of the bond to assess its strength and adhesive properties under tension. This method helps determine the bond’s tensile strength and elongation properties.
- Peel Testing:Peel testing evaluates the bond’s resistance to delamination or separation. A force is applied to peel apart two bonded materials at a controlled angle, simulating real-world stresses. This test is beneficial for assessing adhesion between layers.
- Microscopy:Optical and electron microscopy can examine the bond interface at a microscopic level. This provides insights into the quality of the bond, such as the presence of voids, defects, or uneven bonding surfaces.
- Ultrasound Testing:Ultrasonic techniques use high-frequency sound waves to detect defects, voids, or inconsistencies within the bonded materials. Changes in acoustic properties can indicate the presence of defects in the bond.
- Thermal Analysis:Differential scanning calorimetry (DSC) and thermogravimetric analysis (TGA) can be used to study the thermal behavior of acrylic bonds. Changes in thermal properties can reveal the presence of contaminants, improper curing, or other issues.
- FTIR Spectroscopy:Fourier-transform infrared (FTIR) spectroscopy can help analyze the chemical composition of the bond interface. Changes in molecular structure can indicate bonding success or potential issues.
- X-ray Imaging:X-ray techniques, such as X-ray computed tomography (CT), can provide insights into the internal structure and quality of the bond. This is particularly useful for assessing bonds in complex systems.
- Acoustic Emission Testing:Acoustic emission monitoring involves detecting and analyzing the sound waves produced during bond testing. Anomalies in the acoustic signals can indicate bond failure or defects.
- Environmental Testing:Exposing acrylic bonds to different ecological conditions, such as temperature, humidity, or chemicals, can help assess their long-term stability and resistance to degradation.
- Pull-Off Testing:This method involves applying a controlled force perpendicular to the bonded surface to determine the bond’s adhesion strength. It’s commonly used for coatings and thin films.
- Dye Penetrant Testing:This method involves applying a colored dye to the bond surface, which is then wiped off. If any cracks or defects exist, the dye will remain in these areas, making them visible under UV light.
It’s important to note that the choice of testing method depends on factors such as the specific application, bond type, and desired level of detail. A combination of these methods can provide a comprehensive assessment of the quality of acrylic bonds.
What future trends are shaping the development of acrylic bonding solutions?
Keep in mind that my knowledge base only includes developments beyond that point. However, these trends might still give you some insights into the potential directions that acrylic bonding solutions could be taking:
- Environmentally Friendly Formulations: The trend towards sustainability and environmental consciousness has influenced the development of acrylic bonding solutions. Researchers and manufacturers have been working on creating more environmentally friendly formulations, including lower volatile organic compounds (VOCs) and reduced toxicity. This aligns with broader industry shifts toward greener products.
- Improved Performance and Durability: There has been a constant drive to improve the performance and durability of acrylic bonding solutions. This includes enhancing adhesion strength, resistance to various environmental factors (such as UV radiation, moisture, and temperature fluctuations), and overall longevity of bonded materials.
- Advancements in Hybrid Formulations: Hybrid acrylic bonding solutions, which combine acrylics with other adhesive technologies, have risen. These hybrids can offer a combination of the benefits of acrylic adhesives (such as fast curing and good bond strength) with properties of other adhesives (like flexibility or chemical resistance).
- Nanotechnology Integration: The integration of nanotechnology into acrylic bonding solutions has been explored to enhance various properties. Nanoparticles can be added to improve adhesion, mechanical strength, and resistance to degradation and provide functionalities like self-healing capabilities.
- Customization and Tailored Solutions: With advancements in manufacturing and formulation technologies, there has been a trend towards developing acrylic bonding solutions that can be customized to meet specific requirements of different industries and applications. This includes adjusting curing times, bond strength, flexibility, and other parameters to suit the needs of a particular use case.
- Adhesive Films and Tapes: Beyond traditional liquid adhesives, there has been growing interest in developing acrylic-based adhesive films and tapes. These formats offer advantages like ease of application, reduced mess, and potential for automation in industrial settings.
- Application in Lightweight Materials and Composites: As industries like aerospace, automotive, and electronics continue to seek lightweight and high-performance materials, acrylic bonding solutions are being explored for their ability to join these materials effectively while maintaining structural integrity.
- Digitalization and Industry 4.0: Integrating digital technologies and data-driven processes into manufacturing (often called Industry 4.0) could impact the development of acrylic bonding solutions. This could include improved process control, quality monitoring, and predictive maintenance in adhesive application processes.
Developments may have occurred after September 2021 that could further shape the trends in acrylic bonding solutions. I recommend checking with industry sources, adhesive manufacturers, and research publications for the most up-to-date information.
How do acrylic bonding solutions contribute to lightweight in the transportation industry?
Acrylic bonding solutions, often called acrylic adhesives or acrylic-based structural adhesives, contribute significantly to lightweight solutions in the transportation industry. These adhesives are a type of adhesive that is based on acrylic polymers and offer several advantages that make them suitable for light applications:
- Low Density:Acrylic adhesives typically have a lower density than traditional joining methods such as welding or mechanical fastening. This means they add minimal weight to the overall structure, which is crucial for achieving lightweight designs in transportation, where every ounce matters.
- High Strength-to-Weight Ratio:Acrylic adhesives can provide high bond strength despite their low density. This high strength-to-weight ratio allows them to replace heavier traditional joining methods while maintaining structural integrity effectively.
- Distribution of Stress:Acrylic adhesives can distribute stress evenly across the bonded area. This can prevent stress concentration points that can occur with mechanical fasteners, leading to more uniform load distribution and reduced chances of fatigue failure.
- Improved Design Flexibility:Acrylic adhesives can bond dissimilar materials, such as metals, composites, plastics, and elastomers. This enables engineers to create hybrid structures that leverage the strengths of each material, optimizing the balance between strength, weight, and other performance characteristics.
- Reduced Corrosion and Galvanic Issues:Traditional joining methods like welding can create areas prone to corrosion, especially when joining dissimilar metals. Acrylic adhesives eliminate the need for direct metal-to-metal contact, reducing the risk of galvanic corrosion and enhancing the structure’s longevity.
- Vibration and Noise Damping:Acrylic adhesives can absorb and dampen vibrations and noise, improving passenger comfort and reducing wear and tear on lightweight structures subjected to dynamic loads in transportation applications.
- Sealing and Bonding in One Step:Acrylic adhesives can act as a sealant and a bond. This dual functionality can create more streamlined and efficient designs by combining sealing and bonding into a single step.
- Improved Aesthetics:Acrylic adhesives can provide nearly invisible joints, which is beneficial for maintaining the aesthetics of transportation components. This is particularly important for industries such as automotive and aerospace, where appearance matters.
- Energy Efficiency:In some cases, acrylic bonding solutions can improve energy efficiency. For example, in automotive applications, reduced weight can lead to improved fuel efficiency and reduced emissions.
Overall, acrylic bonding solutions contribute to lightweight designs in the transportation industry by providing a reliable, strong, and versatile method of joining materials that optimizes structural performance and weight considerations. This is particularly important in sectors where the pursuit of greater efficiency, reduced environmental impact, and enhanced performance are critical.
What safety precautions should be followed when working with acrylic adhesives?
Working with acrylic adhesives requires careful attention to safety precautions to ensure the well-being of the individuals involved and the quality of the work. Here are some essential safety precautions to follow when working with acrylic adhesives:
- Personal Protective Equipment (PPE):
- Wear appropriate PPE, including safety glasses or goggles, to protect your eyes from splashes or fumes.
- Use gloves to prevent skin contact with the adhesive. Nitrile gloves are often recommended for working with adhesives.
- Ventilation:
- Work in a well-ventilated area or use local exhaust ventilation systems to prevent the buildup of potentially harmful fumes or vapors.
- Consider using fans, open windows, or exhaust systems to ensure adequate air circulation if working indoors.
- Skin Protection:
- Avoid direct skin contact with the adhesive. If skin contact occurs, immediately wash the affected area with soap and water.
- Eye Protection:
- Wear safety goggles or a face shield to protect your eyes from potential splashes or contact with adhesive.
- Work Area Preparation:
- Keep your work area clean and organized to prevent accidental spills or exposure.
- Remove any potential ignition sources, such as open flames or sparks, as some acrylic adhesives are flammable.
- Avoid Inhalation:
- Minimize breathing in fumes or vapors by working in a well-ventilated area and wearing appropriate respiratory protection if necessary.
- Read and Follow the Instructions:
- Carefully read and understand the manufacturer’s instructions and safety data sheets (SDS) for your specific adhesive.
- Follow the recommended application methods, curing times, and precautions provided by the manufacturer.
- Proper Storage:
- Store acrylic adhesives in original containers and a cool, dry place away from direct sunlight, heat sources, and incompatible materials.
- Fire Safety:
- Some acrylic adhesives are flammable, so be cautious around potential ignition sources and avoid smoking in the work area.
- Emergency Preparedness:
- Have access to equipment such as eyewash stations, safety showers, fire extinguishers, and first aid supplies.
- Know the proper procedures for handling spills, exposures, or accidents involving the adhesive.
- Training:
- Ensure that individuals working with acrylic adhesives are adequately trained in their safe handling, application, and cleanup.
- Dispose of Waste Properly:
- According to local regulations and guidelines, dispose of waste materials, such as used containers, gloves, and cleaning materials.
Remember that different acrylic adhesives may have specific safety considerations, so always refer to the manufacturer’s guidelines and SDS for accurate and up-to-date information. If you have any concerns or questions about working with a specific adhesive, consider contacting the manufacturer or a qualified safety professional.
How do acrylic bonding solutions contribute to advancements in electronics manufacturing?
Acrylic bonding solutions, also known as acrylic adhesives or acrylic-based adhesives, have played a significant role in advancing electronics manufacturing in several ways:
1.Miniaturization and Precision Bonding:As electronic devices become smaller and more complex, traditional mechanical fastening methods (such as screws or clips) become less practical. Acrylic bonding solutions can securely bond components in tight spaces without adding bulk. Their ability to form thin, precise bonds is crucial for microelectronics and delicate details.
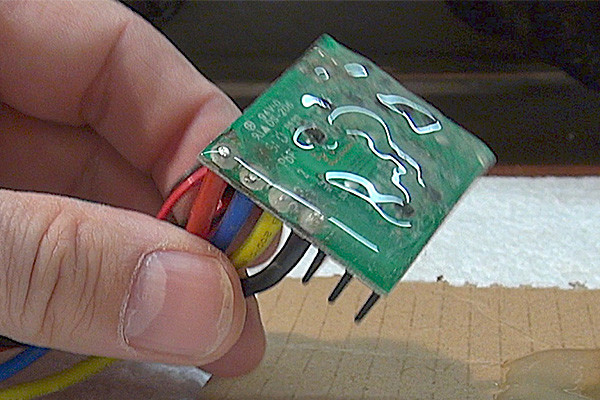
2.Thermal Management:Many electronics generate heat during operation, negatively impacting their performance and lifespan. Acrylic bonding solutions with good thermal conductivity can attach heat sinks and other cooling solutions to electronic components. This helps dissipate heat efficiently, improving overall device reliability and longevity.
3.Vibration and Shock Resistance:In various electronic applications, devices are exposed to vibrations and shocks, leading to component failure if not adequately managed. Acrylic bonding solutions can dampen vibrations and provide shock resistance, reducing the risk of damage to delicate components.
4.Flexibility and Stress Relief:Acrylic adhesives often have some flexibility after curing. This property is advantageous in electronics manufacturing, where components can experience thermal expansion, contraction, and mechanical stress. Acrylic bonding solutions can absorb these stresses, preventing cracks or detachment that might occur with more rigid adhesives.
5.Chemical Resistance and Environmental Protection:Electronics can be exposed to various environmental factors, including moisture, chemicals, and pollutants. Acrylic bonding solutions can provide a protective barrier against these elements, preventing corrosion and degradation of sensitive components.
6.Optical Clarity:Acrylic adhesives can be formulated to have excellent optical clarity, making them suitable for applications where transparent bonding is required. This is important in devices like displays, cameras, and optical sensors, where distortion or haziness would be undesirable.
7.Reduced Manufacturing Steps:Acrylic bonding solutions can often be applied in liquid form and cured through various methods, such as heat, UV light, or chemical reactions. This eliminates the need for additional hardware like screws, reducing the number of manufacturing steps and potentially simplifying the assembly process.
8.Enhanced Design Flexibility:Acrylic adhesives are versatile and can be used on various materials, including metals, plastics, glass, and ceramics. This allows designers more freedom in material selection for their electronic devices without being limited by the constraints of traditional mechanical fasteners.
9.Cost Efficiency:In some cases, acrylic bonding solutions can save costs compared to more complex mechanical attachment methods. They can reduce the need for precision machining or additional components, leading to overall cost reductions in manufacturing.
10.Conformal Coating and Encapsulation:Acrylic adhesives can also be used for conformal coating and encapsulation, providing a protective layer that covers and shields electronic components from moisture, dust, and other contaminants. This is particularly important in harsh environments and outdoor applications.
What impact do acrylic bonding solutions have on sustainable product design?
Acrylic bonding solutions can positively and negatively impact sustainable product design, depending on how they are used and the overall context of the product’s lifecycle. Here are some considerations:
Positive Impacts:
- Durability and Longevity:Acrylic bonding solutions can enhance the durability of products by creating strong bonds between materials. This can extend the lifespan of products, reducing the need for frequent replacements and thus decreasing overall resource consumption.
- Material Efficiency:Acrylic bonding can allow for the bonding of dissimilar materials, leading to designs that use smaller amounts of high-performance materials. This can lead to resource savings and reduce the environmental impact of production.
- Lightweight Design:Acrylic bonding can create lightweight structures, which can benefit transportation, energy consumption, and overall resource efficiency.
- Design Flexibility:Acrylic bonding can facilitate complex and intricate designs that might not be achievable through traditional methods like mechanical fastening. This flexibility can lead to innovative strategies that optimize material usage and energy efficiency.
Negative Impacts:
- Toxicity and Health Concerns:Some acrylic bonding solutions may involve toxic chemicals, solvents, or adhesives that can adversely affect workers and users. Such solutions can counteract sustainability goals by introducing harmful substances into the environment.
- Disassembly and Recycling:Acrylic bonding can create strong and permanent bonds, making it difficult to disassemble products at the end of their lifecycle for recycling or refurbishing. This can lead to increased waste generation and hinder circular economy principles.
- Energy Consumption:Acrylic bonding solutions’ manufacturing and curing processes might require high energy inputs, contributing to a product’s overall carbon footprint if not carefully managed.
- Degradation and End of Life:Some acrylic bonding solutions might degrade over time due to exposure to environmental factors like UV radiation or moisture. This can shorten the lifespan of products and lead to premature disposal.
Sustainable Design Considerations:
- Material Selection:Choose acrylic bonding solutions that are low toxicity and have minimal environmental impact. Consider water-based or solvent-free options that reduce harmful emissions.
- End-of-Life Planning:Design products with the end of life in mind. If acrylic bonding is used, consider methods to make disassembly and recycling more accessible, such as incorporating separable parts.
- Energy Efficiency:Opt for acrylic bonding processes requiring less curing and manufacturing energy. Additionally, consider the energy savings that durable bonding can provide over a product’s lifespan.
- Life Cycle Assessment:Conduct a life cycle assessment to understand the environmental impact of acrylic bonding solutions. Consider factors like resource consumption, energy use, emissions, and potential for reuse or recycling.
In essence, acrylic bonding solutions can contribute to sustainable product design if their benefits are leveraged while carefully managing their potential drawbacks. It’s crucial to approach design decisions holistically, considering both the short-term advantages and long-term environmental implications.
How do acrylic bonding solutions address challenges in medical device manufacturing?
Acrylic bonding solutions play a crucial role in addressing challenges in medical device manufacturing by providing adequate adhesion and bonding for various components used in medical devices. These solutions are typically used in applications requiring robust, reliable bonds between different materials, such as plastics, metals, ceramics, and glass. Here’s how acrylic bonding solutions help address challenges in medical device manufacturing:
- Compatibility and Versatility:Medical devices often have diverse materials with different physical properties. Acrylic bonding solutions are designed to provide strong bonds across a wide range of substrates, making them versatile for bonding dissimilar materials.
- Biocompatibility:Acrylic bonding solutions are often formulated to be biocompatible, meaning they are safe for contact with living tissues and fluids within the human body. This is essential for medical devices implanted or used in direct patient contact.
- Precision and Control:Acrylic bonding solutions can be applied with high precision, allowing manufacturers to control the adhesive used and ensure consistent bond strength. This is important for devices that require delicate assembly or specific performance characteristics.
- Fast Cure Times:Many acrylic bonding solutions offer rapid curing times, accelerating manufacturing. This is especially beneficial for high-volume production where efficiency is paramount.
- Chemical and Environmental Resistance:Medical devices can be exposed to various chemicals, cleaning agents, and environmental conditions. Acrylic bonding solutions often resist common solvents and chemicals, ensuring the longevity and reliability of the bonds even in challenging situations.
- Transparency and Aesthetics:Acrylic adhesives are available in formulations that remain transparent after curing. This is valuable for devices with transparent or translucent components, as it maintains the visual aesthetics of the device.
- Reduced Stress Concentration:Unlike mechanical fastening methods, such as screws or rivets, acrylic bonding provides a more uniform stress distribution across the bonded area. This helps to reduce stress concentration points, which can be important for medical devices subjected to repeated mechanical loads.
- Sealing and Gap Filling:Acrylic bonding solutions can also act as effective sealants and gap fillers, ensuring the medical devices are properly sealed against moisture, contaminants, and other external factors that could compromise their functionality or safety.
- Ease of Automation:Acrylic bonding solutions can be applied through various automated processes, such as dispensing systems or robots. This enables consistent application and bonding quality, particularly in high-throughput manufacturing environments.
- Regulatory Compliance:Many acrylic bonding solutions are designed to meet specific regulatory standards for medical devices, ensuring that the final products adhere to industry requirements for safety, performance, and quality.
What considerations are essential when bonding dissimilar materials using acrylic adhesives?
Bonding dissimilar materials using acrylic adhesives requires careful consideration of several factors to ensure a solid and durable bond. Here are some essential concerns:
- Surface Preparation:Proper surface preparation is crucial for adhesive bonding. Surfaces must be clean, dry, and free from dust, oil, grease, and oxidation contaminants. Depending on the materials, surface treatments such as cleaning, sanding, or chemical priming might be necessary to promote adhesion.
- Material Compatibility:Acrylic adhesives can bond with various materials, but compatibility is still important. Consider the chemical compatibility of the adhesive with both the substrates to be connected. Some substrates may inhibit cure or affect the adhesive’s properties.
- Adhesive Selection:Acrylic adhesives come in various formulations, each with different properties such as flexibility, temperature resistance, and bond strength. Select an adhesive that matches the specific needs of the application and the dissimilar materials being bonded.
- Thermal Expansion:Different materials have varying coefficients of thermal expansion. When exposed to temperature fluctuations, dissimilar materials can expand and contract at different rates, potentially leading to bond failure. Choose an adhesive with good thermal stability and account for potential dimensional changes.
- Joint Design:The collective design plays a significant role in the bond’s strength and durability. Factors like standard geometry, overlap area, and stress distribution should be considered to ensure a balanced load-bearing structure.
- Mechanical Properties:Understand the mechanical properties of both materials, including their rigidity, flexibility, and strength. A strong bond requires an adhesive to handle the stress distribution between the dissimilar substrates.
- Curing Time and Temperature:Acrylic adhesives cure through a chemical reaction. Follow the manufacturer’s recommendations for fixing time and temperature. Higher temperatures can accelerate curing but may also affect the material properties.
- Environmental Exposure:Consider the environmental conditions the bonded materials will be subjected to, such as temperature, humidity, UV radiation, chemicals, and moisture. Choose an acrylic adhesive with suitable resistance to these conditions.
- Testing and Prototyping:Before applying the adhesive on a large scale, conduct testing and prototyping to evaluate the bond’s strength, performance under different conditions, and potential failure modes.
- Application Method:Applying the adhesive can affect the bond’s quality. Whether using manual application, automated dispensing, or other methods, ensure uniform and consistent adhesive coverage.
- Safety and Health:Acrylic adhesives can emit volatile compounds during curing. Ensure proper ventilation in the application area and follow safety guidelines for handling the adhesive.
- Long-Term Performance:Consider the expected lifespan of the bonded assembly. Acrylic adhesives are known for their long-term durability, but selecting the appropriate adhesive formulation can ensure the bond remains strong over time.
- Testing Standards:Depending on the industry and application, specific testing standards and regulations for bonded assemblies might exist. Ensure compliance with these standards to meet safety and quality requirements.
Always refer to the manufacturer’s technical datasheets, guidelines, and recommendations when working with acrylic adhesives, as the specific requirements can vary based on the adhesive formulation and the materials being bonded.
How do acrylic bonding solutions contribute to reducing assembly costs and production time?
Acrylic bonding solutions, such as acrylic adhesives and tapes, can significantly reduce assembly costs and production time in various manufacturing processes. Here’s how:
- Fast Application and Curing Time:Acrylic bonding solutions often have quicker curing times than other adhesive options. They can bond quickly and efficiently, allowing for speedier assembly of components. This reduces the time required for waiting and handling during the production process.
- Eliminating Mechanical Fasteners:Acrylic bonding solutions can replace traditional mechanical fasteners like screws, bolts, and rivets. This eliminates the need for drilling, tapping, or welding, which can be time-consuming. Additionally, the absence of mechanical fasteners reduces the complexity of the assembly, saving time and effort.
- Uniform Stress Distribution:Acrylic adhesives create a strong and consistent bond over the entire bonding area. This distributes stress evenly across the joint, reducing the risk of localized stress concentrations that could lead to material failure. In contrast, mechanical fasteners can create stress concentrations at points of contact, potentially requiring additional design considerations and time-consuming modifications.
- Versatility in Bonding Dissimilar Materials:Acrylic bonding solutions are known for bonding dissimilar materials, such as metals, plastics, composites, and ceramics. This versatility eliminates the need for selecting compatible fasteners for each material combination, simplifying the assembly process and saving time in material sourcing and preparation.
- Enhanced Design Flexibility:Acrylic adhesives offer flexibility in joint design, allowing for innovative and efficient designs that may not be possible with traditional mechanical fasteners. This design flexibility can lead to streamlined production processes and shorter assembly times.
- Reduced Surface Preparation:Acrylic bonding solutions often require less stringent surface preparation than other adhesive types. While proper surface cleaning and treatment are still crucial for optimal bonding, the requirements are generally less demanding, reducing prep time.
- Reduced Labor Costs:Acrylic bonding solutions can be applied using automated dispensing systems, reducing the need for manual labor in the assembly process. This can lead to consistent application and improved production efficiency.
- Lower Material and Tooling Costs:Acrylic bonding solutions can eliminate the need for specific materials like washers, gaskets, and clips commonly used with mechanical fasteners. Additionally, specialized tooling and equipment required for mechanical fastening can be minimized or eliminated when using adhesive bonding.
- Improved Aesthetics:Acrylic adhesives provide a smooth, seamless finish without visible fasteners. This can improve the overall aesthetics of the final product and eliminate the need for additional finishing steps.
- Enhanced Performance:Acrylic bonding solutions often resist environmental factors such as temperature, moisture, and chemicals. This can improve product durability and reduce maintenance requirements, further contributing to long-term cost savings.
It’s important to note that while acrylic bonding solutions offer these benefits, the specific advantages will depend on the application, materials, and production processes in use. Careful consideration of the adhesive’s properties, the assembly design, and the manufacturing environment is essential to capitalize on the potential time and cost savings entirely.
What role do acrylic bonding solutions play in enabling innovative architectural designs?
Acrylic bonding solutions significantly enable innovative architectural designs by providing new possibilities for construction, aesthetics, and sustainability. Here’s how these bonding solutions contribute to pushing the boundaries of architectural creativity:
- Seamless Joints and Aesthetic Freedom:Acrylic adhesives allow for the creation of seamless joints between materials, such as glass, metal, and plastic. This seamless appearance enhances the aesthetics of architectural elements by eliminating the need for visible mechanical fasteners or joints, resulting in a clean and modern design.
- Versatility in Material Combination:Acrylic bonding solutions enable architects to combine materials that might not have been previously compatible. This opens up opportunities for novel combinations of materials, textures, and finishes, allowing architects to create unique and visually striking designs that stand out from traditional structures.
- Complex Geometries and Shapes:Acrylic adhesives provide strong and durable bonds between dissimilar materials, making creating intricate and complex geometric shapes possible. This ability to bond diverse materials together without relying solely on traditional construction methods allows architects to explore new forms, curves, and spatial arrangements that were once challenging to achieve.
- Lightweight Construction:Acrylic bonding solutions allow lightweight construction methods by bonding materials together without needing heavy mechanical fasteners. This is particularly important for large architectural structures, as it can reduce the overall weight of the building and minimize the load on foundations and supports.
- Enhanced Transparency and Light Transmission:Acrylic adhesives are often used in glass bonding applications. By using these adhesives, architects can create large glass façades with minimal visible supports, maximizing transparency and enabling natural light to flood interior spaces. This results in visually striking designs prioritizing openness and environmental connection.
- Improved Energy Efficiency:Acrylic bonding solutions can help enhance the energy efficiency of buildings. For example, they can create solid and well-insulated connections between glass panels in curtain walls or windows. This improves thermal performance, reduces air infiltration, and contributes to sustainable building design.
- Reduced Construction Time:Acrylic bonding solutions can streamline construction processes by simplifying assembly procedures and reducing the need for complex mechanical connections. This can lead to shorter construction timelines and quicker realization of architectural designs.
- Customization and Personalization:Acrylic bonding solutions enable architects to customize and personalize building components more quickly. Whether customized panels, intricate decorative elements, or signage, these bonding solutions offer the flexibility to incorporate unique design features that align with the architect’s vision.
- Durability and Longevity:Acrylic adhesives are engineered for durability and longevity, ensuring that innovative architectural designs maintain their structural integrity and aesthetic appeal over time. This is essential for the sustainability and success of ambitious architectural projects.
- Sustainability Considerations:Many acrylic bonding solutions are formulated to be environmentally friendly and comply with sustainability standards. By choosing these solutions, architects can contribute to creating greener and more sustainable buildings.
Acrylic bonding solutions empower architects to think beyond traditional construction limitations and explore innovative designs that prioritize aesthetics, functionality, sustainability, and structural integrity. The versatility and reliability of these bonding solutions make them valuable tools for translating architectural concepts into real-world structures.