Glass Bonding Applications: A Comprehensive Guide
Glass Bonding Applications: A Comprehensive Guide
Glass bonding is a specialized process used across various industries. It enables the seamless and durable attachment of glass to diverse materials like metals, plastics, and ceramics. Glass bonding techniques have evolved to meet the demands of modern applications, including electronic displays, automotive windows, medical devices, and architecture. This article covers everything from basic principles to advanced applications and materials used in glass bonding.
Introduction to Glass Bonding
Glass bonding is essential in industries where precision, strength, and aesthetic appeal are critical. Unlike conventional bonding materials, glass requires specific adhesives and bonding processes to ensure a solid and durable bond. Achieving a flawless bond depends on various factors, including the type of glass, the bonded substrate, environmental factors, and the chosen adhesive.
Common Types of Glass Used in Bonding:
- Tempered Glass:Used in automotive, electronics, and architecture due to its strength and safety properties.
- Laminated Glass:Preferred for applications that require shatter resistance, like car windshields.
- Borosilicate Glass:Known for its thermal and chemical resistance, it is often used in lab equipment and cookware.
- Fused Silica Glass:Provides excellent optical clarity, suitable for optics and high-precision instruments.
Importance of Glass Bonding:
Proper bonding ensures that glass remains functional under stress, temperature changes, and other external factors in industries where it is bonded to other materials. For example, in electronics, improper bonding can lead to device failures, while in construction, it can compromise structural integrity.
Critical Applications of Glass Bonding
Glass bonding applications vary across industries, each with unique requirements and challenges. Below are some key areas where glass bonding plays a crucial role.
Electronics and Displays
In electronics, glass bonding is fundamental for creating high-performance displays, touch screens, and optical lenses. This application requires adhesives that maintain optical clarity, resist UV light, and withstand extreme temperatures.
Applications in Electronics:
- Smartphone Screens:Requires ultra-clear bonding to ensure vivid displays.
- LCD and OLED Displays:Adhesives in these screens prevent bubble formation and resist yellowing over time.
- Touch Panels:Adhesives must allow touch functionality while protecting from scratches and impacts.
Essential Adhesives for Electronics:
- Optically Clear Adhesives (OCA):OCAs are preferred for their high transparency and durability in electronic displays.
- UV-Curable Adhesives:These are commonly used due to quick curing times and are ideal for automated production lines.
Automotive Glass Bonding
In the automotive industry, glass bonding is crucial for safety, aerodynamics, and aesthetics. Bonded glass in cars must withstand high speeds, temperature fluctuations, and impact.
Applications in Automotive:
- Windshields and Windows:Strong adhesives maintain the integrity of the windshield and side windows, which are critical in rollover accidents.
- Sunroofs and Moonroofs:Requires adhesives that resist UV light and temperature fluctuations.
- Headlights and Taillights:Adhesives used here must be weather-resistant and maintain clarity over time.
Essential Adhesives for Automotive:
- Polyurethane Adhesives:Known for their high strength, they are used primarily for windshields.
- Silicone Adhesives:Flexible and UV-resistant, commonly used for glass parts exposed to sunlight.
Architectural Glass Bonding
Architectural glass bonding emphasizes durability and aesthetics. In modern construction, large glass panels are often structurally bonded to other materials to create sleek, seamless designs.
Applications in Architecture:
- Curtain Walls:Bonding glass panels to metal frames in high-rise buildings requires adhesives that can withstand wind loads and temperature variations.
- Skylights and Façades:Adhesives here must resist UV exposure, provide waterproofing, and handle structural loads.
- Balustrades and Partitions:Indoor glass partitions require aesthetic bonds, while outdoor balustrades need strong, weather-resistant adhesives.
Essential Adhesives for Architecture:
- Silicone Sealants:Flexible and weather-resistant, ideal for outdoor applications.
- Structural Glazing Adhesives:Specifically designed for glass-to-metal bonding in architectural façades.
Medical Devices and Laboratory Equipment
Glass bonding is essential for creating durable, sterile, and transparent surfaces in medical devices. Applications in this field often require adhesives with specific biocompatibility and chemical resistance standards.
Applications in Medical and Laboratory Fields:
- Microscope Slides and Lenses:Requires high optical clarity and stability.
- Diagnostic Equipment:Glass-to-plastic bonding for devices that come into contact with chemicals.
- Syringes and Vials:Adhesives must be biocompatible and resistant to sterilization processes.
Essential Adhesives for Medical Applications:
- Epoxy Adhesives:Known for their durability, they are often used in lab equipment and optical components.
- UV-Curable Adhesives:Preferred for their fast curing and suitability in sterile environments.
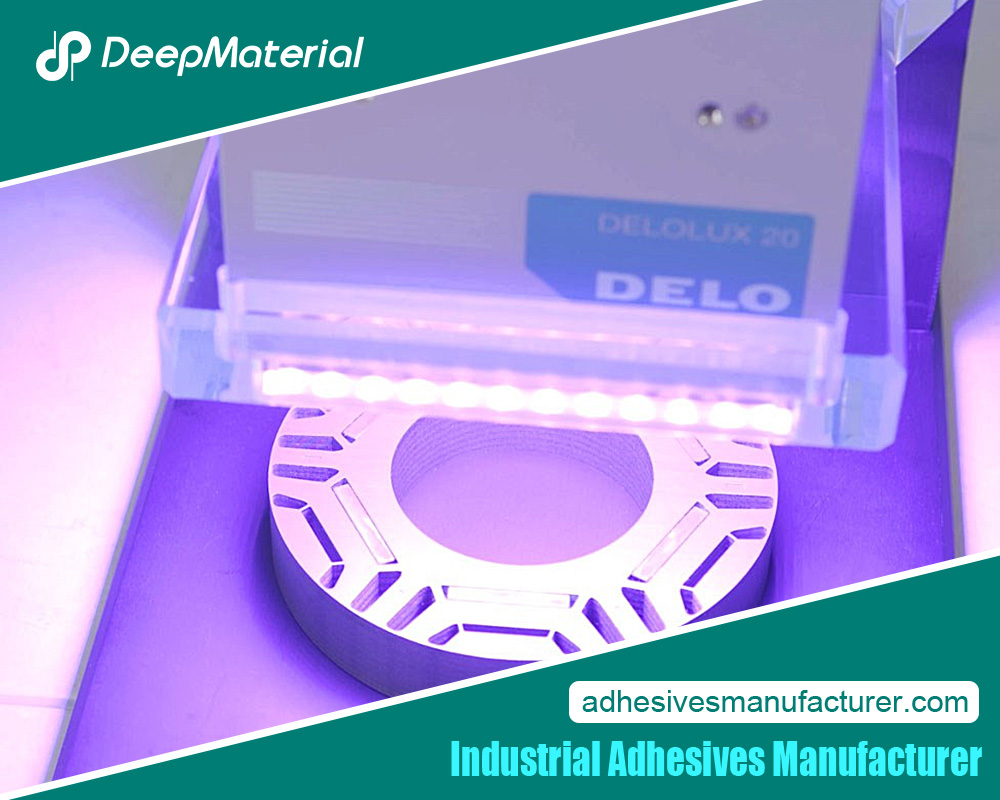
Types of Adhesives Used in Glass Bonding
Choosing the right adhesive for glass bonding depends on the application’s requirements. Each adhesive type offers distinct advantages and is suited for specific types of glass and substrates.
Epoxy Adhesives
Epoxy adhesives are widely used for their strength, durability, and resistance to environmental factors. Epoxies are particularly effective for glass-to-metal and glass-to-plastic bonds.
Benefits:
- High bond strength
- Excellent chemical resistance
- Suitable for applications requiring load-bearing capabilities
Drawbacks:
- Limited flexibility can be a drawback in applications with frequent vibrations or temperature changes.
Polyurethane Adhesives
Polyurethane adhesives are valued for their flexibility and impact resistance, making them ideal for automotive and construction applications.
Benefits:
- Excellent impact resistance
- It has good flexibility, making it suitable for applications with movement or vibrations
- Resistant to weathering, ideal for outdoor use
Drawbacks:
- Generally slower curing time
- It may require moisture for curing, which could impact some applications
Silicone Adhesives
Silicone adhesives are famous for their flexibility, UV resistance, and weatherproof properties, making them ideal for outdoor and architectural applications.
Benefits:
- Excellent UV and weather resistance
- High flexibility, accommodating movements without losing adhesion
- Resistant to temperature variations
Drawbacks:
- Lower bond strength compared to epoxy and polyurethane
- It may not be suitable for applications with high structural load requirements
UV-Curable Adhesives
UV-curable adhesives cure quickly under UV light, making them ideal for applications requiring precision and speed, like electronics.
Benefits:
- Fast curing, ideal for high-throughput manufacturing
- High optical clarity, suitable for displays and optics
- Bonds well with glass, plastics, and some metals
Drawbacks:
- Requires UV light for curing, which can limit the process to transparent substrates
- Limited resistance to high temperatures and chemicals
Factors Influencing Glass Bonding Quality
Successful glass bonding relies on various factors impacting the final bond’s strength, durability, and appearance.
Surface Preparation
Surface cleanliness is critical to achieving a reliable bond. Dust, oil, and other contaminants can significantly weaken the adhesive’s ability to bond to glass.
Methods for Surface Preparation:
- Cleaning:Use isopropyl alcohol or specialized glass cleaners to remove contaminants.
- Etching:Light etching with acid can improve adhesion by increasing surface roughness.
- Priming:Primers enhance bonding strength and ensure adhesive compatibility with specific glass types.
Curing Process
The curing process affects the adhesive’s performance. Different adhesives require different curing methods, including heat, UV light, or chemical catalysts.
Types of Curing Processes:
- UV Curing:Common for fast, precise applications like electronics.
- Heat Curing:Used in applications where high bond strength is needed.
- Moisture Curing:Polyurethanes often rely on ambient moisture for curing.
Environmental Conditions
Temperature, humidity, and exposure to UV light can impact adhesive performance over time.
Considerations for Environmental Conditions:
- UV Exposure:Outdoor applications need UV-resistant adhesives to prevent degradation.
- Temperature Resistance:Bonded glass exposed to extreme temperatures, such as in automotive or aerospace, requires temperature-stable adhesives.
- Moisture and Chemical Resistance:Medical and lab equipment adhesives should withstand moisture, cleaning agents, and sterilization processes.
Advanced Techniques and Future Trends in Glass Bonding
As technology advances, glass bonding methods are evolving to accommodate new applications and materials. Innovations in adhesive chemistry and bonding processes open possibilities in fields like flexible electronics, wearable devices, and smart glass.
Adhesives for Flexible and Wearable Electronics
Flexible and transparent adhesives are critical for the growing market of wearable devices and flexible displays. Research is ongoing to develop flexible and durable adhesives that maintain bond integrity during bending or stretching.
Smart Glass and Electrochromic Applications
Smart glass, used in applications where transparency can be electrically controlled, relies on advanced bonding techniques to integrate electronic components within glass panels. Adhesives in these applications must maintain transparency and allow electrical conductivity.
3D-printed Adhesives and Nanotechnology
3D printing technology enables the development of custom adhesives tailored for specific applications. Nanotechnology also enhances adhesive performance through improved flexibility, durability, and resistance to environmental factors.
Conclusion
Glass bonding is a dynamic field essential to many industries, from electronics and automotive to architecture and medical devices. With advances in adhesive technology and surface preparation methods, glass bonding continues to expand, allowing for innovative applications and enhanced durability. As industries push the boundaries of design and functionality, glass bonding will remain a vital process for high-performance applications.
Choosing the suitable adhesive and bonding technique is crucial, as each application has specific requirements that affect performance, aesthetics, and longevity. With continued research and development, the future of glass bonding looks promising, offering solutions that will support the evolving demands of modern technology and design.
For more about a complete guide to glass bonding applications: a comprehensive guide, you can pay a visit to Deepmaterial at https://www.adhesivesmanufacturer.com/ for more info.